Ép phun Polypropylene (PP) vẫn là một trong những quy trình sản xuất được sử dụng rộng rãi nhất trong ngành nhựa do tính linh hoạt, hiệu quả về chi phí và hiệu suất. Khi các nhà sản xuất tiếp tục tìm kiếm các phương pháp sản xuất tối ưu, việc hiểu ép phun PP trở nên rất quan trọng để đạt được kết quả chất lượng cao trong khi giảm thiểu các vấn đề sản xuất. Bài viết này sẽ khám phá các khía cạnh quan trọng của ép phun PP mà mọi nhà sản xuất, kỹ sư và kỹ thuật viên nên nhớ để đảm bảo sản xuất thành công.
1. Hiểu về đặc tính của Polypropylene
1.1. Đặc điểm vật liệu
Cấu trúc bán tinh thể của Polypropylene mang lại cho nó những đặc tính độc đáo tác động trực tiếp đến quá trình ép phun. Với điểm nóng chảy tương đối thấp (160-170°C), tỷ lệ co ngót cao (1-2,5%) và đặc tính chảy tuyệt vời, PP đòi hỏi các điều kiện xử lý cụ thể để đạt được kết quả tối ưu. Hành vi kết tinh của vật liệu ảnh hưởng đáng kể đến kích thước bộ phận, độ cong vênh và chất lượng tổng thể trong các ứng dụng ép phun PP.
1.2. Các loại và phụ gia
Mỗi loại PP khác nhau (đồng trùng hợp, đồng trùng hợp ngẫu nhiên, đồng trùng hợp va đập) có quy trình ép phun riêng biệt. PP đồng trùng hợp va đập cung cấp độ dẻo dai được cải thiện nhưng có thể yêu cầu nhiệt độ xử lý cao hơn, trong khi đồng trùng hợp ngẫu nhiên cung cấp độ trong suốt tốt hơn và giảm cong vênh. Việc hiểu cách các chất phụ gia như tác nhân tạo hạt, hợp chất chống tĩnh điện và chất ổn định UV ảnh hưởng đến các thông số xử lý là điều cần thiết để hoạt động đúc phun PP thành công.
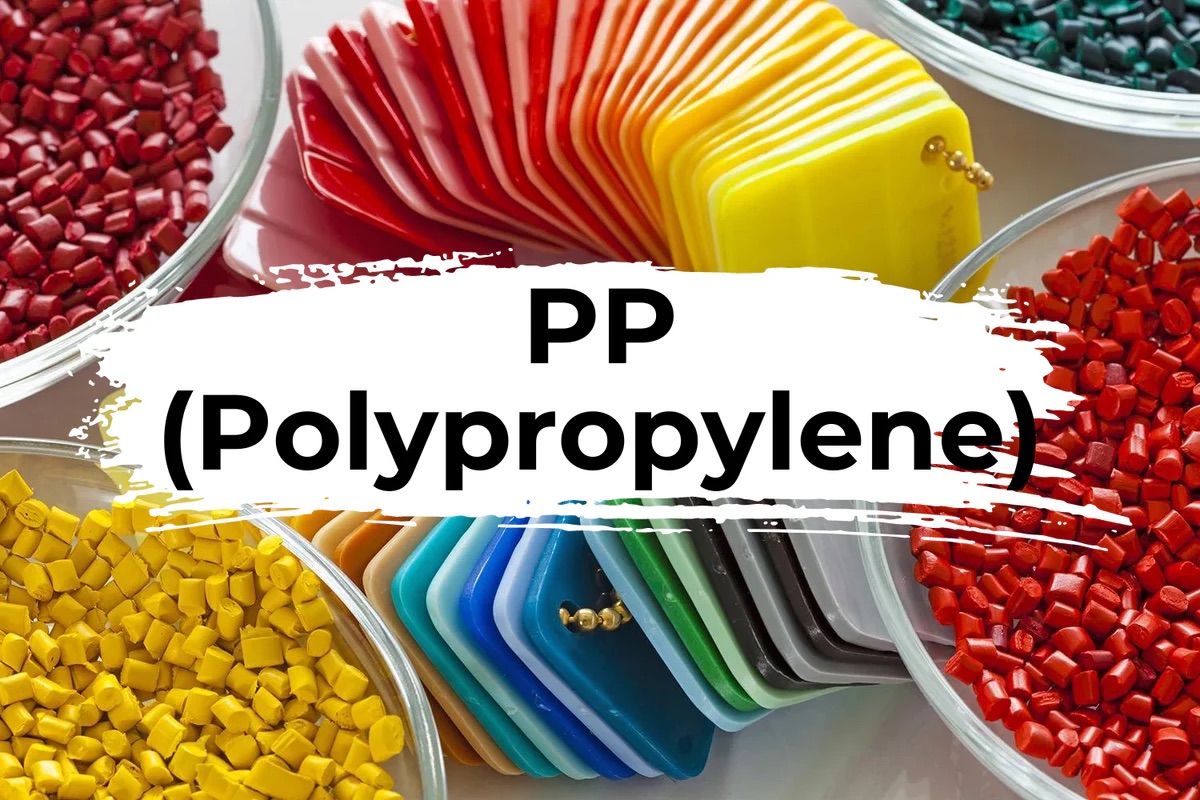
Mỗi loại PP khác nhau có một quy trình ép phun riêng biệt
2. Chuẩn bị vật liệu cần thiết
2.1. Yêu cầu sấy khô
Không giống như nhiều loại nhựa nhiệt dẻo kỹ thuật, PP tiêu chuẩn thường không cần sấy khô trước do bản chất không hút ẩm của nó. Tuy nhiên, giả định phổ biến này có thể dẫn đến các vấn đề về chất lượng trong quá trình đúc phun PP khi vật liệu tiếp xúc với độ ẩm cao hoặc chứa các chất phụ gia hút ẩm. Một chu kỳ sấy ngắn (2-4 giờ ở 80°C) có thể có lợi khi xử lý PP được lưu trữ trong điều kiện ẩm ướt hoặc chứa chất độn như bột talc có thể hấp thụ độ ẩm.
2.2. Xử lý và phòng ngừa ô nhiễm
Nhiễm bẩn là một yếu tố rủi ro đáng kể trong quá trình đúc phun PP. Ngay cả một lượng nhỏ vật liệu lạ cũng có thể tạo ra điểm yếu, khiếm khuyết về mặt thị giác hoặc khó khăn trong quá trình xử lý. Việc triển khai các giao thức xử lý vật liệu phù hợp, quy trình thanh lọc thường xuyên và các biện pháp kiểm soát chất lượng hiệu quả giúp duy trì tính toàn vẹn của vật liệu trong suốt quá trình đúc phun PP.
3. Tối ưu hóa các thông số xử lý
3.1. Kiểm soát nhiệt độ
Kiểm soát nhiệt độ nóng chảy thích hợp là rất quan trọng để đúc phun PP thành công. Hồ sơ nhiệt độ thùng được khuyến nghị thường nằm trong khoảng từ 200-230°C đối với hầu hết các loại PP, với mức tăng dần từ vùng nạp đến vòi phun. Nhiệt độ quá cao có thể dẫn đến sự xuống cấp của vật liệu, trong khi gia nhiệt không đủ sẽ gây ra tình trạng đổ đầy không đầy đủ, đường ống dòng chảy và tính toàn vẹn của bộ phận kém. Việc theo dõi cẩn thận nhiệt độ nóng chảy trong suốt quá trình sản xuất đảm bảo chất lượng đồng nhất trong các hoạt động đúc phun PP.
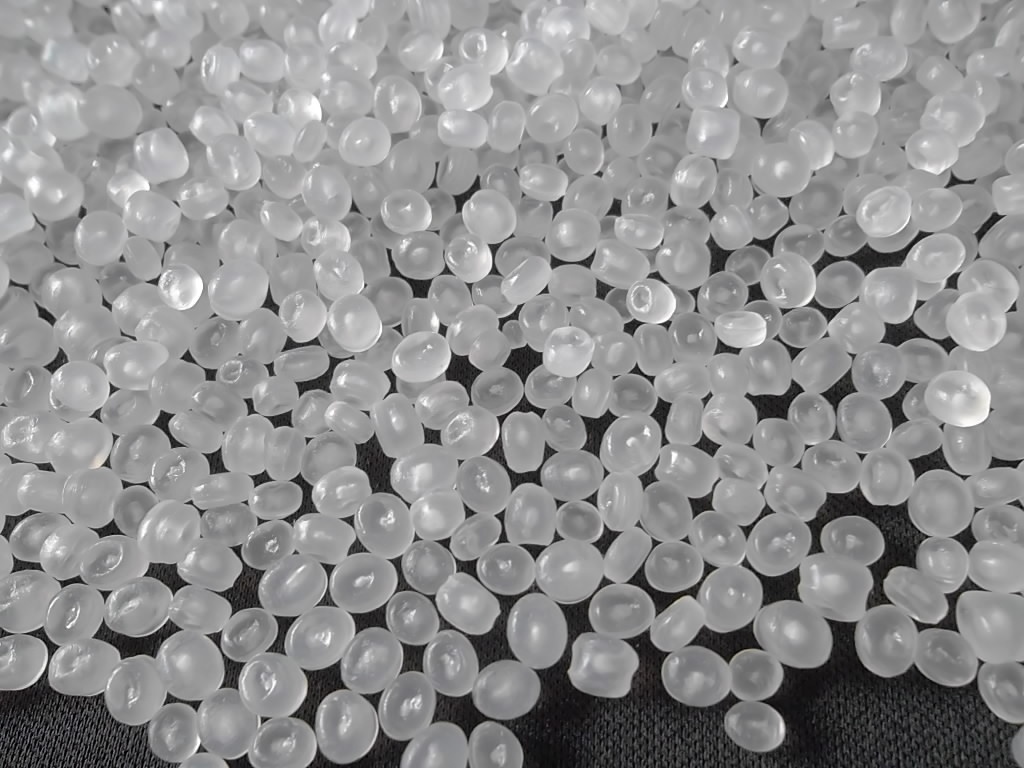
Kiểm soát nhiệt độ nóng chảy thích hợp là rất quan trọng để đúc phun PP thành công.
3.2. Cài đặt áp suất và tốc độ
Áp suất phun, áp suất giữ và tốc độ phun ảnh hưởng đáng kể đến chất lượng chi tiết trong quá trình đúc phun PP. Tốc độ phun cao hơn thường có lợi cho các ứng dụng có thành mỏng nhưng có thể gây ra hiện tượng phun tia hoặc khuyết tật bề mặt ở các phần dày hơn. Áp suất giữ, thường là 50-70% áp suất phun đối với PP, phải được tối ưu hóa để kiểm soát độ co ngót mà không tạo ra ứng suất bên trong quá mức. Việc tìm ra sự cân bằng phù hợp giữa các thông số này là một thách thức chính trong quá trình tối ưu hóa quy trình đúc phun PP.
3.3. Cân nhắc về làm mát
Hành vi kết tinh của PP khiến việc làm mát trở nên đặc biệt quan trọng trong quá trình đúc phun. Nhiệt độ khuôn, thường được duy trì trong khoảng 20-60°C cho các ứng dụng đúc phun PP, ảnh hưởng trực tiếp đến tốc độ kết tinh, độ co ngót của chi tiết và thời gian chu kỳ. Nhiệt độ khuôn cao hơn thúc đẩy quá trình kết tinh tốt hơn và giảm ứng suất bên trong nhưng kéo dài thời gian chu kỳ. Làm mát đồng đều trên toàn bộ khoang khuôn ngăn ngừa sự co ngót khác biệt và cong vênh liên quan trong quá trình sản xuất đúc phun PP.
4. Những thách thức khi ép phun PP và giải pháp
4.1. Hiện tượng co ngót và cong vênh
Tỷ lệ co ngót tương đối cao của PP gây ra những thách thức đáng kể về độ ổn định kích thước. Vị trí cổng phun hiệu quả, thiết kế rãnh dẫn và bố trí hệ thống làm mát giúp quản lý các vấn đề này trong quá trình ép phun PP. Kết hợp các gờ và duy trì độ dày thành đồng đều trong toàn bộ thiết kế bộ phận giúp giảm thiểu sự co ngót khác biệt. Khi xảy ra hiện tượng cong vênh nghiêm trọng trong quá trình đúc phun PP, việc điều chỉnh áp suất giữ, thời gian làm mát và nhiệt độ khuôn thường mang lại các giải pháp hiệu quả.
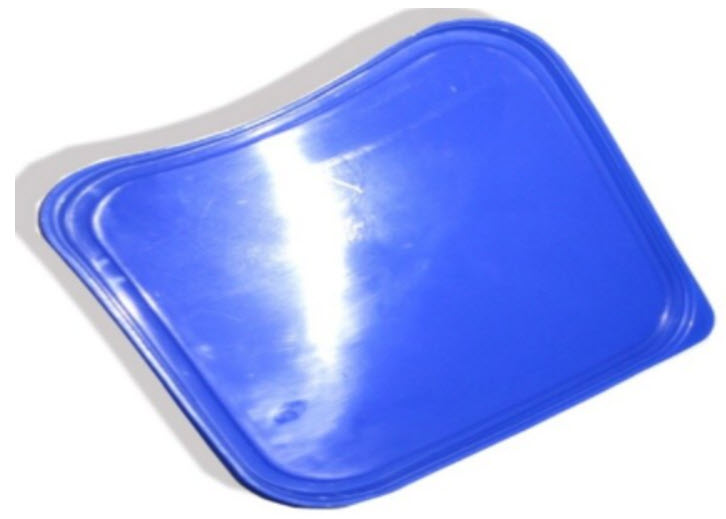
Tỷ lệ co ngót tương đối cao của PP gây ra những thách thức đáng kể về độ ổn định kích thước.
4.2. Xử lý lỗi bề mặt
Việc bị lõm bề mặt là vấn đề phổ biến trong quá trình ép phun PP. Vết lõm thường là do sự co ngót của sản phẩm nhựa, và do chế độ ép chưa phù hợp. Một số cách giải quyết sau có thể giảm tình trạng lỗi bề mặt sản phẩm:
- Áp lực giữ thấp, thời gian ngắn
- Kích thước cổng phun nhỏ
- Giảm nhiệt độ khuôn
- Giảm chiều dày sản phẩm ( thiết kế thêm gân tăng lực, bố trí cổng phun gần vị trí có độ dày cao)
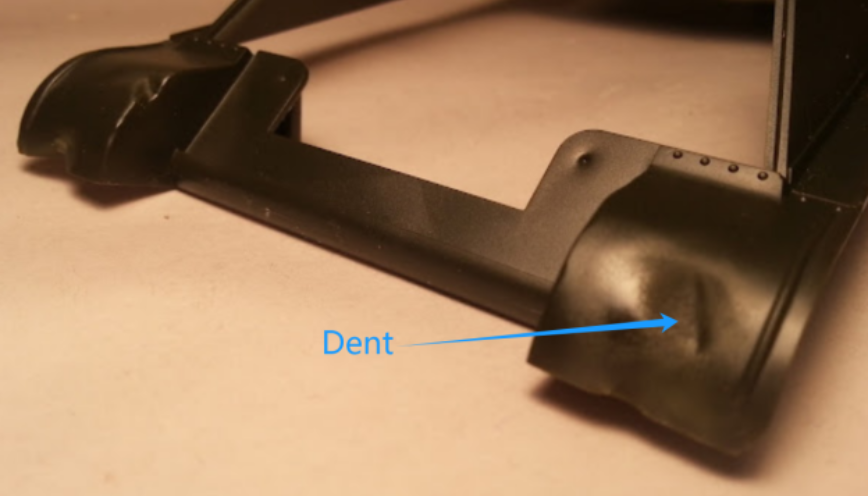
Việc bị lõm bề mặt là vấn đề phổ biến trong quá trình ép phun PP.
5. Kết luận
Để quá trình ép phun PP diễn ra thành công, người thực hiện cần hiểu biết đầy đủ về đặc tính vật liệu, thông số xử lý và nguyên tắc thiết kế khuôn. Bằng cách tập trung vào việc chuẩn bị vật liệu phù hợp, tối ưu hóa các điều kiện xử lý và triển khai các chiến lược khắc phục sự cố hiệu quả, các nhà sản xuất có thể đạt được kết quả chất lượng cao đồng đều trong khi giảm thiểu các vấn đề sản xuất. Khi công nghệ ép phun PP tiếp tục phát triển, việc cập nhật thông tin về các kỹ thuật mới nổi và phát triển thiết bị giúp duy trì lợi thế cạnh tranh trong quy trình sản xuất thiết yếu này.
6. Giới thiệu về EuroPlas
Công ty CP Nhựa Châu Âu hiện là nhà cung cấp filler masterbatch lớn nhất thế giới với công suất 800.000 tấn/năm và đã có mặt trên 95 quốc gia. Trong đó, các sản phẩm nhựa PP của Nhựa Châu Âu là giải pháp tối ưu chi phí và cải thiện tính năng sản phẩm cho các doanh nghiệp sản xuất thành phẩm nhựa. Suốt 18 năm phát triển, chúng tôi luôn tự tin cam kết về chất lượng sản phẩm và dịch vụ của mình.
Để biết thêm thông tin chi tiết, quý khách hàng vui lòng điền vào biểu mẫu hoặc liên hệ trực tiếp qua email/số điện thoại.