Polypropylene (PP) injection molding remains one of the most widely utilized manufacturing processes in the plastics industry due to its versatility, cost-effectiveness, and efficiency. As manufacturers continue to seek optimal production methods, understanding the nuances of PP injection molding becomes crucial for achieving high-quality results while minimizing production issues. This comprehensive guide explores the critical aspects of PP injection molding that every manufacturer, engineer, and technician should remember to ensure successful production runs.
1. Understanding Polypropylene Properties
1.1. Material Characteristics
Polypropylene's semi-crystalline structure gives it unique properties that directly impact the injection molding process. With a relatively low melting point (160-170°C), high shrinkage rate (1-2.5%), and excellent flow characteristics, PP requires specific processing conditions to achieve optimal results. The material's crystallization behavior significantly influences part dimensions, warpage, and overall quality in PP injection molding applications.
1.2. Grades and Additives
Different PP grades (homopolymer, random copolymer, impact copolymer) exhibit varying processing behaviors during PP injection molding. Impact copolymers offer enhanced toughness but may require higher processing temperatures, while random copolymers provide better clarity and reduced warpage. Understanding how additives like nucleating agents, antistatic compounds, and UV stabilizers affect processing parameters is essential for successful PP injection molding operations.
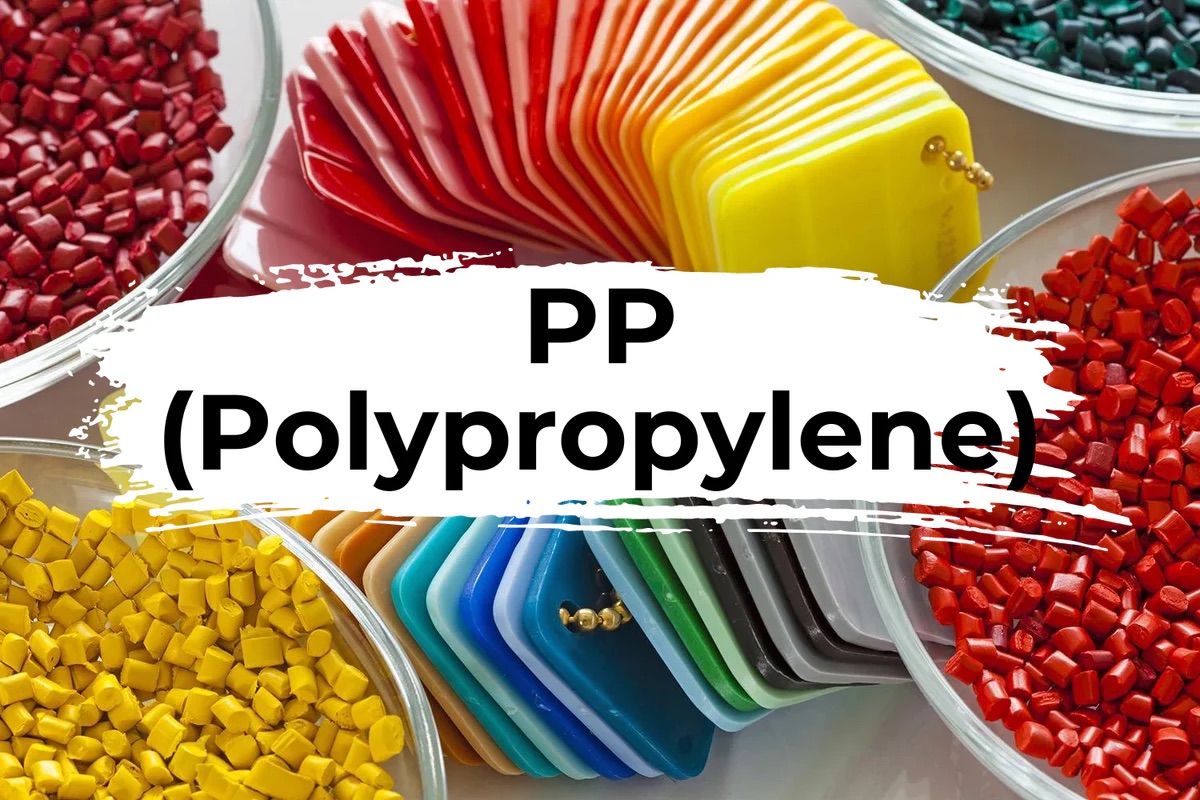
2. Material Preparation Essentials
2.1. Drying Requirements
Unlike many engineering thermoplastics, standard PP typically doesn't require pre-drying due to its non-hygroscopic nature. However, this common assumption can lead to quality issues in PP injection molding when the material has been exposed to high humidity or contains hygroscopic additives. A brief drying cycle (2-4 hours at 80°C) may be beneficial when processing PP that has been stored in humid conditions or contains fillers like talc that may absorb moisture.
2.2. Handling and Contamination Prevention
Contamination represents a significant risk factor in PP injection molding. Even small amounts of foreign materials can create weak points, visual defects, or processing difficulties. Implementing proper material handling protocols, regular purging procedures, and effective quality control measures helps maintain material integrity throughout the PP injection molding process.
3. Optimizing Processing Parameters
3.1. Temperature Control
Proper melt temperature control is crucial for successful PP injection molding. The recommended barrel temperature profile typically ranges from 200-230°C for most PP grades, with a gradual increase from the feed zone to the nozzle. Excessive temperatures can lead to material degradation, while insufficient heating causes incomplete filling, flow lines, and poor part integrity. Careful monitoring of melt temperature throughout production runs ensures consistent quality in PP injection molding operations.
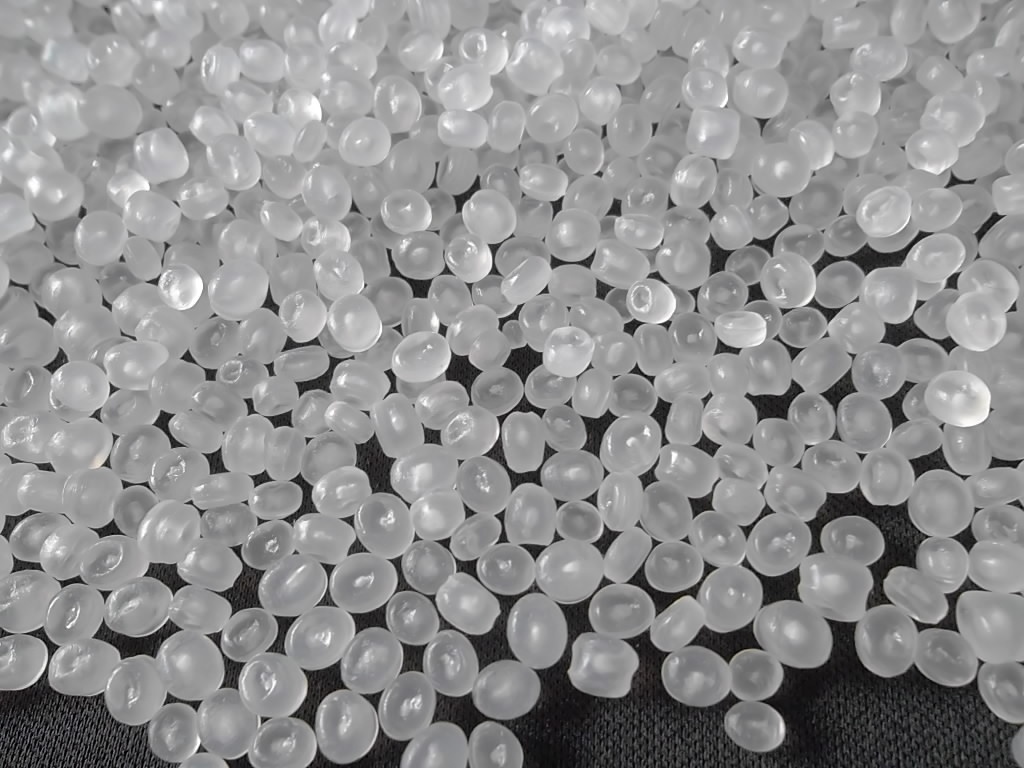
Proper melt temperature control is crucial for successful PP injection molding.
3.2. Pressure and Speed Settings
Injection pressure, holding pressure, and injection speed significantly impact part quality in PP injection molding. Higher injection speeds often benefit thin-walled applications but may cause jetting or surface defects in thicker sections. Holding pressure, typically 50-70% of injection pressure for PP, must be optimized to control shrinkage without creating excessive internal stress. Finding the right balance between these parameters represents a key challenge in PP injection molding process optimization.
3.3. Cooling Considerations
PP's crystallization behavior makes cooling particularly important in the injection molding process. Mold temperature, typically maintained between 20-60°C for PP injection molding applications, directly affects crystallization rate, part shrinkage, and cycle time. Higher mold temperatures promote better crystallization and reduced internal stress but extend cycle times. Uniform cooling across the mold cavity prevents differential shrinkage and associated warpage in PP injection molding production.
4. Common Challenges and Solutions
4.1. Managing Shrinkage and Warpage
PP's relatively high shrinkage rate presents significant challenges in dimensional stability. Effective gate placement, runner design, and cooling system layout help manage these issues in PP injection molding. Incorporating ribs and maintaining uniform wall thickness throughout the part design minimizes differential shrinkage. When severe warpage occurs in PP injection molding, adjusting holding pressure, cooling time, and mold temperature often provides effective solutions.
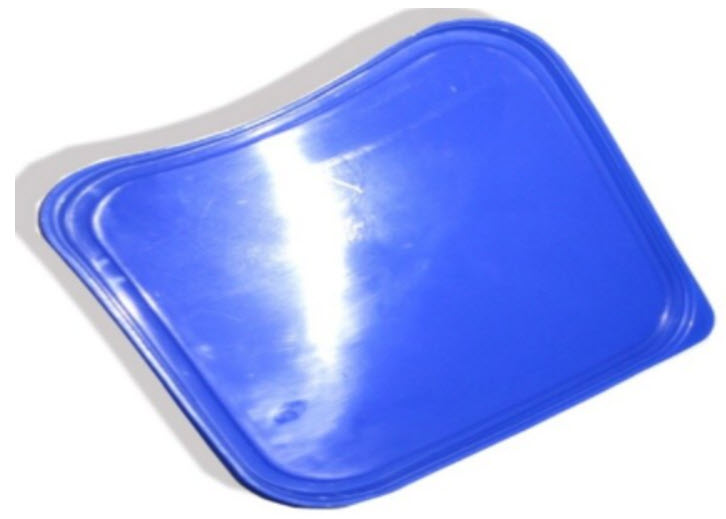
4.2. Surface Defects Troubleshooting
Sink marks, gate blush, and tiger striping represent common surface quality issues in PP injection molding. Sink marks typically result from insufficient cooling time or holding pressure, while tiger striping often stems from excessive shear heating or poor melt homogeneity. Addressing these defects requires systematic adjustment of processing parameters and sometimes tool modifications to achieve consistent high-quality surfaces in PP injection molding production.
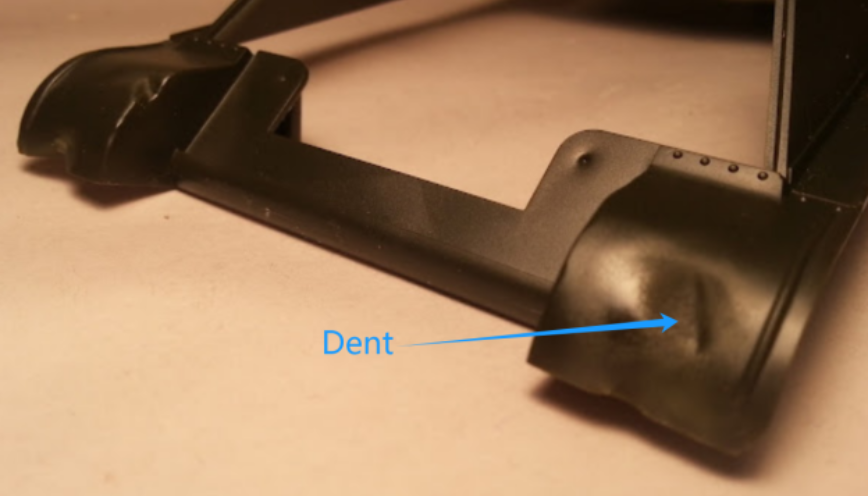
5. Conclusion
Successful PP injection molding requires a comprehensive understanding of material properties, processing parameters, and mold design principles. By focusing on proper material preparation, optimizing processing conditions, and implementing effective troubleshooting strategies, manufacturers can achieve consistent high-quality results while minimizing production issues. As PP injection molding technology continues to advance, staying informed about emerging techniques and equipment developments helps maintain competitive advantages in this essential manufacturing process.
6. About EuroPlas
European Plastic Company is currently the world's largest supplier of filler masterbatch with a capacity of 800,000 tons/year, and has been present in over 95 countries. Especially, PP products of EuroPlas are the solution to optimize costs and improve product features for enterprises producing plastic-finished products. During 18 years of development, we are always confident in our commitment to the quality of our products and services.
For more information, please fill out the form or contact us directly via email/phone number.