Có nhiều cách để thực hiện việc in trong khuôn. Trong bài viết này, chúng ta sẽ xem xét ba phương pháp tạo IML hàng đầu. Chúng là ép phun, đúc thổi và hút định hình nhiệt. Cả ba phương pháp này đều hiệu quả. Sự khác biệt duy nhất là cách in nhãn được thực hiện trong từng quy trình.
4.1. Ép phun
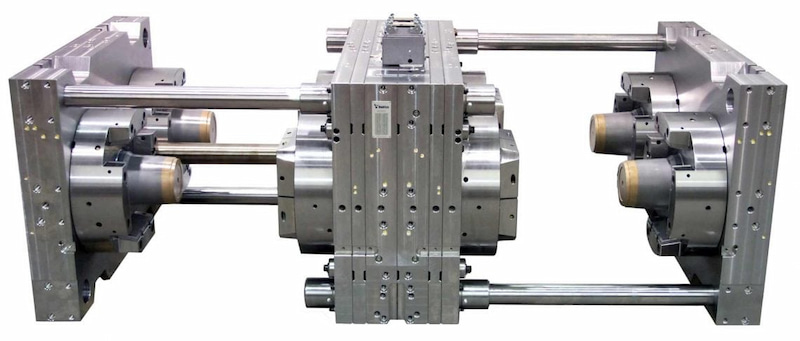
Ép phun là quy trình được sử dụng thường xuyên nhất trong quy trình in trong khuôn. Mặc dù nhìn bề ngoài thì quy trình ép phun có vẻ đơn giản, nhưng có một số yếu tố phải được kiểm soát chặt chẽ để đảm bảo chất lượng tổng thể của các thành phần nhựa được sản xuất. Các nhà sản xuất sẽ dễ dàng hơn trong việc tìm kiếm các nhà cung cấp linh kiện nhựa có thể cung cấp chất lượng và tính nhất quán mà họ muốn nếu họ hiểu rõ về quy trình và các thông số của nó.
Quá trình ép phun như sau:
Bước 1: Chọn nhựa nhiệt dẻo và khuôn thích hợp
Các loại nhựa nhiệt dẻo và khuôn chính xác phải được chọn hoặc chế tạo trước khi quy trình có thể bắt đầu vì đây là những thứ thực sự sản xuất và định hình các thành phần cuối cùng. Thật vậy, các nhà sản xuất phải tính đến cách tương tác giữa nhựa nhiệt dẻo và khuôn để đưa ra lựa chọn tốt nhất, vì một số loại nhựa nhất định có thể không phù hợp với các thiết kế khuôn cụ thể.
Bước 2: Nạp và nấu chảy nhựa nhiệt dẻo
Điện hoặc thủy lực đều có thể được sử dụng để cung cấp năng lượng cho thiết bị ép phun. Các viên nhựa nhiệt dẻo thô được đưa vào phễu của máy ở phía trên để bắt đầu quá trình. Những viên này dần dần được đưa vào thùng của máy trong khi trục vít quay. Nhựa nhiệt dẻo dần dần được làm nóng và tan chảy do quá trình quay trục vít và gia nhiệt thùng cho đến khi nó nóng chảy.
Bước 3: Bơm nhựa vào khuôn
Cánh cửa quản lý việc phun nhựa sẽ đóng lại ngay khi nhựa nóng chảy đến cuối thùng và vít tiến lên. Thao tác này kéo một lượng nhựa định trước đi qua và chuẩn bị vít để bơm bằng cách tạo áp suất bên trong. Hai thành phần của dụng cụ khuôn được giữ chặt với nhau và dưới áp suất cao, hoặc áp suất kẹp, cùng một lúc.
Để đảm bảo bộ phận phát triển đúng cách và không có nhựa thoát ra khỏi dụng cụ trong quá trình bơm, cần phải điều chỉnh áp suất phun và áp suất kẹp. Cửa mở ra, vít tiến lên và nhựa nóng chảy được bơm vào khuôn (lúc này đã được đặt sẵn 1 nhãn in bên trong thành khuôn) sau khi đạt được áp suất thích hợp trong dụng cụ và vít.
Bước 4: Giữ và làm mát
Sau khi phần lớn nhựa đã được bơm vào khuôn, áp suất được tạo ra trong một khoảng thời gian nhất định. Điều này được gọi là "thời gian giữ" và tùy thuộc vào loại nhựa nhiệt dẻo và độ phức tạp của thành phần, nó có thể kéo dài từ vài mili giây đến vài phút. Khoảng thời gian giữ này rất quan trọng để đảm bảo rằng nhựa hình thành đúng cách và đóng gói dụng cụ. Sau khi làm mát, nó sẽ có hình dạng tương thích với khuôn và liên kết với nhãn được đặt.
Bước 5: Hoàn thiện quy trình
Chốt hoặc tấm đẩy các chi tiết ra khỏi dụng cụ sau khi hết thời gian giữ và làm mát và chi tiết về cơ bản đã hoàn thành. Những thứ này rơi xuống đáy máy, nơi chúng đáp xuống băng chuyền hoặc trong ngăn. Trong một số trường hợp nhất định, có thể cần các quy trình hoàn thiện như đánh bóng, nhuộm hoặc loại bỏ nhựa thừa; các quy trình này có thể được thực hiện bởi các thiết bị hoặc nhân viên khác. Các thành phần sẽ sẵn sàng để được đóng gói và gửi đến nhà sản xuất sau khi các quy trình này kết thúc.
Bởi vì việc in nhãn của khuôn nhựa được thực hiện trong chu kỳ đúc, nên việc in nhãn sau và các quy trình phụ khác sẽ bị loại bỏ.
Phương pháp in trong khuôn rất linh hoạt và hiệu quả về chi phí. Nó tăng hiệu quả và cung cấp các lựa chọn thay thế cho việc dán nhãn sản phẩm lâu bền. Bởi vì khuôn nhựa được dán nhãn khi nó đang được đúc nên không cần phải dán nhãn sau và các bước tiếp theo khác.
Kỹ thuật ép phun được sử dụng rộng rãi cho hộp nhựa. Hộp đựng kem là một ví dụ về sản phẩm thường sử dụng nhãn ép phun. Bàn phím máy tính, bàn phím điện thoại di động và thùng sơn nhựa nhỏ hơn là những hàng hóa sử dụng nhãn ép phun.
4.2. Đúc thổi
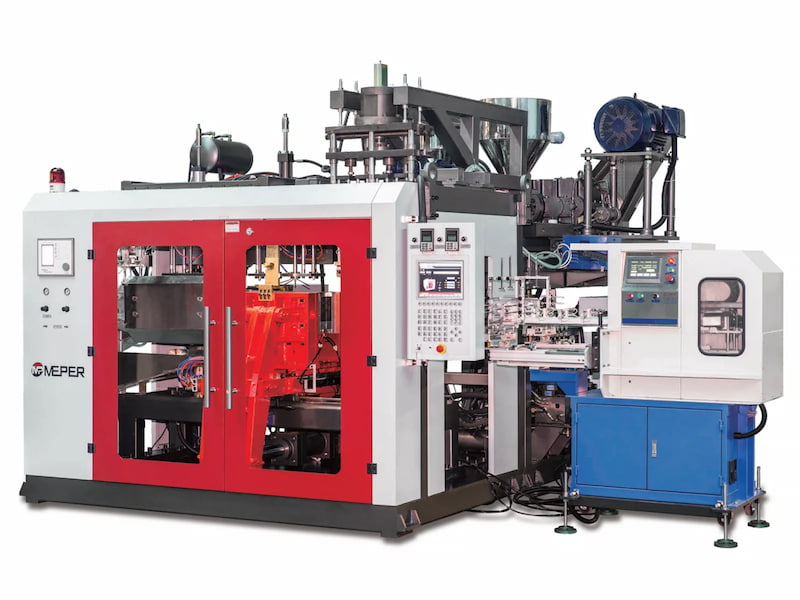
Kỹ thuật được sử dụng rộng rãi thứ hai để in nhãn trong khuôn là đúc thổi. Trong quy trình này, vật liệu nhựa thô được sử dụng trong đúc thổi được tạo thành một ống rỗng, là một ống rỗng có một đầu hở. Cũng giống như in trong khuôn trong ép phun, nhãn để trang trí trước tiên được cố định vào thành khoang của khuôn. Khi nhựa đúc nguội đi, nó sẽ hợp nhất với nhãn bên trong khoang khuôn.
Có ba quy trình đúc thổi khác nhau:
Ép thổi phun (injection blow molding)
Một thanh thổi hoặc thanh lõi được sử dụng trong suốt quá trình đúc thổi phun. Đầu tiên, khoang khuôn chia xung quanh thanh được lấp đầy bằng một parison. Parison thu được có hình dạng giống như ống nghiệm. Máy khuôn thổi nhận parison thông qua thanh lõi, nơi khí nén tạo ra hình thức cuối cùng. Sản phẩm cuối cùng sau đó được chuyển đến thanh, đùn nó ra khỏi máy.
Ép thổi đùn (extrusion blow molding)
Có thể đúc thổi đùn liên tục hoặc lẻ tẻ. Mỗi hình thức trong quá trình đúc thổi đùn liên tục được cắt nhỏ bằng một lưỡi dao khi nó phát triển từ một bộ phận được cung cấp liên tục vào khuôn. Khi nhựa mới được làm nguội và đưa vào khuôn sau khi nhựa trước đó đã được đẩy ra, quá trình đúc thổi đùn gián đoạn sẽ đùn từng loại nhựa mới ra khỏi khuôn kim loại.
Khuôn thổi đùn có thể được tạo ra nhanh hơn đáng kể và với chi phí thấp hơn so với khuôn thổi phun nói chung. Các đường chạy nhỏ hơn thích hợp cho ép đùn thổi. Ưu điểm bao gồm giảm chi phí dụng cụ và thời gian sản xuất nhanh hơn, trong khi nhược điểm thường bao gồm khả năng kiểm soát độ dày thành ít hơn và nhiều vật liệu phế thải hơn.
Ép thổi kéo (injection stretch blow molding)
Các phương pháp ép phun và đúc thổi được kết hợp trong đúc thổi kéo căng. Để tạo ra một nút cổ chai có ren, trước tiên nhựa được tạo thành một hiệu suất vững chắc.
Máy khuôn thổi căng nhận phôi sau khi nó đã nguội. Khí nén sau khi được đẩy sẽ được bơm vào một chai nhựa, và hiệu suất được làm ấm bằng lò sưởi hồng ngoại.
Quá trình này chủ yếu được sử dụng để sản xuất các bộ phận nhựa rỗng. Quá trình này đã được sử dụng để sản xuất chai thủy tinh. Ngày nay, phương pháp này được sử dụng để sản xuất chai nhựa. Quy trình sản xuất này được sử dụng để sản xuất các hộp đựng chất lỏng như hộp đựng dầu gội đầu, nước rửa chén, xà phòng lỏng, nước sốt cà chua, nước sốt, v.v.
4.3. Hút định hình nhiệt
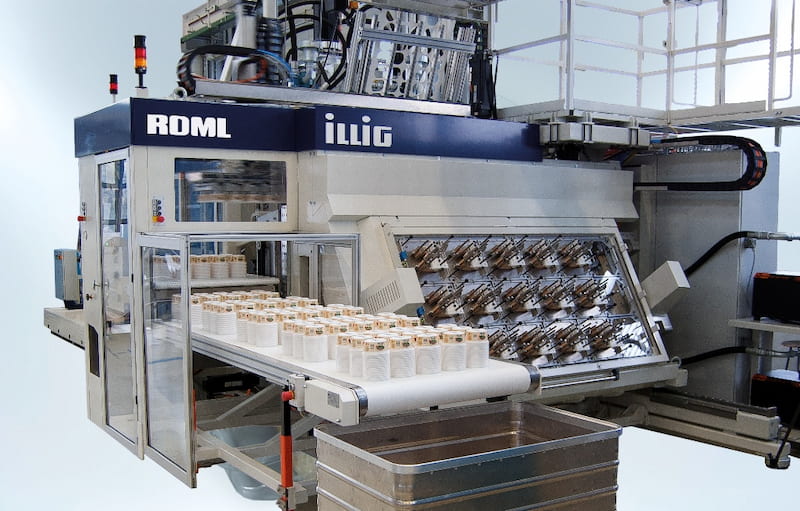
Thermoforming là một quá trình làm nóng một tấm nhựa nhiệt dẻo đến điểm làm mềm của nó. Tấm được căng trên khuôn một mặt và sau đó được chế tác. Sau đó, nó nguội đi thành hình dạng mong muốn. Các phương pháp phổ biến nhất để làm cho tấm phù hợp với hình dạng cuối cùng của nó là tạo hình chân không, tạo hình áp suất và tạo hình cơ học. Thermoforming có vô số ứng dụng và có thể được sử dụng bởi một số ngành công nghiệp khác nhau.
Bước 1: Định hình
Sử dụng một công cụ tạo hình, các tấm nhựa đã được gia nhiệt được tạo hình bằng nhiệt thành một hình dạng nhất định. Trái ngược với ép phun và thổi, các tấm nhựa không được làm nóng hoàn toàn. Xung quanh dụng cụ tạo hình là những tấm nhựa nóng được căng ra. Sau khi làm mát và hóa rắn, các tấm nhựa được nung nóng sẽ có hình dạng của khuôn tạo hình.
Bước 2: Làm nóng
Nhãn đã in được đặt vào khuôn trước khi các tấm nhựa được làm nóng được định vị xung quanh dụng cụ tạo hình. Các tấm nhựa được làm nóng dính vào nhãn đã in khi chúng nguội đi và đông đặc lại trong khuôn. Điều này cuối cùng tạo ra một mặt hàng hoặc sản phẩm bằng nhựa được trang trí hoàn toàn.
Hút định hình nhiệt chủ yếu được sử dụng cho bao bì nhựa cứng. Nó được sử dụng để sản xuất cốc nhựa. Cốc nhựa như cốc cà phê và cốc kem cũng được thực hiện thông qua quá trình này. Quy trình ép nóng cũng được sử dụng để đóng gói kem. Các sản phẩm khác cho ngành công nghiệp thực phẩm, y tế và bán lẻ cũng được thực hiện thông qua hút định hình nhiệt.
5. Khắc phục các vấn đề của in trong khuôn
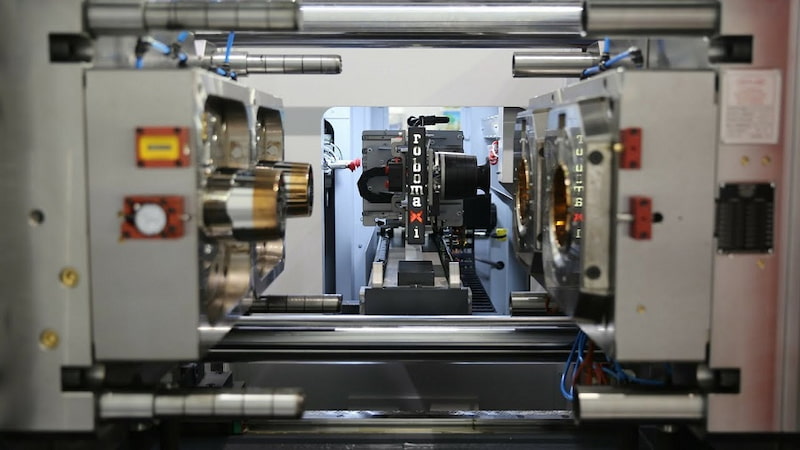
Dưới đây là tổng quan về một số vấn đề phổ biến nhất xuất hiện trong các ứng dụng in trong khuôn:
5.1. Lựa chọn nhựa
Cần xem xét một số loại nhựa phù hợp cho quy trình sản xuất và thành phẩm. Ví dụ, nhựa polycarbonate và nhựa nylon gặp phải những thách thức vì nhiệt độ nóng chảy cao hơn. Mặt khác, các ứng dụng polypropylen và polyetylen dễ xử lý hơn nhiều do điểm nóng chảy giảm. Mặc dù in trong khuôn tương thích với những ứng dụng nhựa này, nhưng việc thử nghiệm trước khi sản xuất là bắt buộc.
Điều quan trọng là người dùng cuối, thợ đúc và nhà cung cấp nhãn in phải đồng nhất về loại nhựa sẽ được sử dụng trước khi bắt đầu quy trình. Trong một số trường hợp và tùy thuộc vào kích thước của bộ phận, bạn nên xây dựng một công cụ nguyên mẫu để kiểm tra khả năng tương thích của nhựa và in trong khuôn.
5.2. Độ bền
Một thách thức rõ ràng khác của IML về mặt trang trí là đạt được mức độ kháng hóa chất hoặc môi trường phù hợp - điều này cũng cần phải thử nghiệm kỹ lưỡng. Ví dụ, nhãn dán trên sàn phải chịu được sự dẫm đạp và các thùng nhiên liệu trong ô tô phải có khả năng chống lại hóa chất.