Plastics are flammable due to their carbon chain molecular structure. However, the degree of ignition and the speed of flame spread in each type of plastic is different. In this article, we’ll learn the fire principle of plastic, common types of fire resistant plastic and how to increase the plastic fire resistance. No more further ado, let’s get started!
Related:
- Flame retardant masterbatch compounds - the ultimate guide
- Common types of halogen-free flame additives
- Flame retardant additives: Essential safety materials
1. What is fire? The burning principle of plastic
Fire is the reaction of a "fuel" substance with oxygen, producing heat and flame. Specifically in this case, plastic is the material for combustion. The burning principle of plastic can be simply understood as follows:
Plastic contains carbon and hydrogen, which is the fuel that sustains the flame. The high-temperature redox reaction between the resin and the oxidant produces vaporous oxidation products, in a mixture called fume. Combustion produces a flame, and produces a temperature sufficient for self-sustaining combustion.
2. 5 common fire resistant plastics
2.1. MC
MC is a form of nylon - a Comonomer mixture, which is made up of molten Lactam Monomer C6H11NO monomers, alkaline compounds as catalysts, activators and other additives. The characteristics of MC plastic are high surface hardness, plasticity, tensile strength, good impact resistance, fatigue resistance, wear resistance, very good folding resistance and especially high fire resistance.
MC plastic is used to make wear-resistant cushions, bearing details, machinery related to transportation, and fireproof MC panels, ...
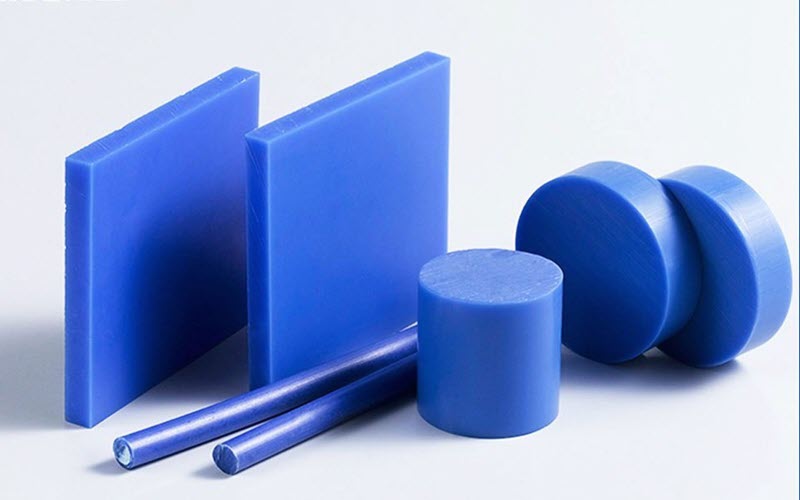
2.2. POM
POM (Polyoxymethylene), also known as acetal, polyacetal and polyformaldehyde, has the chemical formula (CH2O)n , density 1.41–1.42 g/cm3, melting point 175oC. It is milky in color because of its high crystalline composition but can be made in a variety of colors. This was invented by a German chemist named Hermann Staudinger in 1953.
POM resin has high surface hardness, low corrosion, good impact fatigue and impact resistance, low coefficient of friction, and is self-lubricating. Although POM has a high shrinkage rate, the dimensions are still stable. Good dielectric properties, solvent resistance, no stress cracking, and no bubbles are also advantages of POM resin. Due to its torsional strength, it can be kept in its original shape when the external force is removed.
POM plastic has good fire resistance, the flame when burning is clear blue, no coal smoke comes out, and the molten plastic turns black and has a characteristic pungent odor of formaldehyde. As a result, it can irritate the tissues of the nose, throat, and eyes.
The most common application areas of POM plastic are mechanical, electrical, and electronic manufacturing, medical, food processing, and other industries such as toys, windows, water tanks, and sinks.
2.3. PP
PP (Polypropylene) plastic has the chemical formula (C3H6)n. Under normal conditions, PP plastic is transparent white, colorless, odorless, tasteless, and non-toxic. However, due to its wide application in production, PP plastic is often added with color additives.
PP plastic has high mechanical strength, is quite hard and not as flexible as PE plastic, does not stretch, and is therefore made into fibers. PP plastic can tear easily with a small cut or puncture. Besides, this plastic can withstand temperatures higher than 100 degrees Celsius, has better heat resistance than PE, and also has very good electrical and chemical properties.
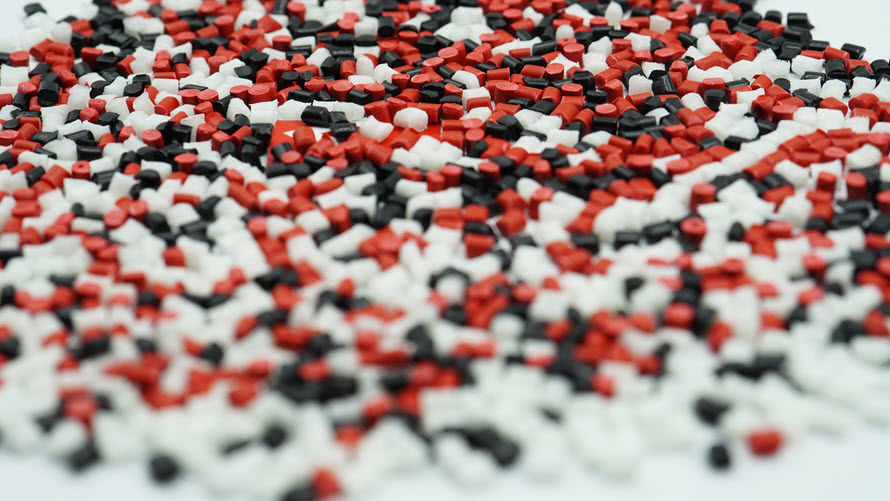
In terms of flammability, PP is more difficult to burn than other plastics due to its good heat resistance. When burned, it produces a light blue flame and releases a burning smell similar to that of rubber.
Popular applications of PP plastic are in the packaging industry, textiles, agricultural coatings, plastic bottles, and some other products requiring heat resistance.
2.4. PA
PA (Polyamide - Polyamide) has a chemical formula of long polymer chains, containing amide units (N-H-C=O). These polymers are obtained by acid polymerization with amides. For example: PA66 is obtained by the reaction of adipic acid with hexamethylenediamine.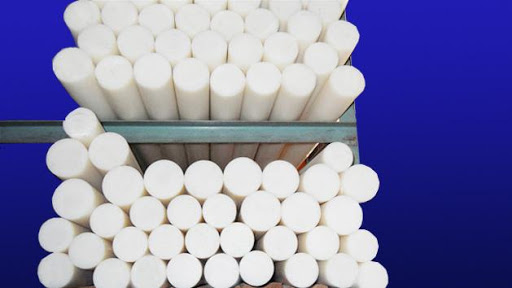
PA has good heat resistance and is self-lubricating, with high mechanical strength, high stiffness, hardness, and toughness. Besides, it also has excellent wear resistance, good chemical resistance, noise absorption, and impact resistance.
PA plastic has good fire resistance, and this advantage is further promoted when it is reinforced with fireproof glass fiber.
PA resin is often used as anti-wear sheets, bearing details, the construction industry, shipbuilding, aircraft, and other utilities.
2.5. ABS
ABS (Acrylonitrile butadiene styrene) has the chemical formula (C8H8)x (C4H6)y (C3H3N)z). Primary ABS plastic is milky white and hard but not brittle.
The characteristics of ABS plastic are good impact resistance, good dimensional stability, dyeable, easy to process and shape. It helps to machine well and has high mechanical strength and stiffness, and low water absorption. Besides, ABS plastic also has good corrosion resistance, simple connection, is non-toxic and odorless.
During the more than 50 years since its invention, ABS has been continuously researched and improved by plastic manufacturers to improve its flame-retardant properties. Currently, ABS has a high resistance to heat, so it is the leading name when it comes to fireproof plastics.
Electronics, home appliances, automobile industry, motorcycle industry, packaging industry, building materials, etc. are common applications of ABS plastic. In addition, because of its flame-retardant properties, ABS is used in the housing of electrical and electronic equipment such as phones and computers.
3. How to enhance plastic fire resistance
As mentioned at the beginning of the article, there is no such thing as non-flammable plastic, just more or less flammable. In order to enhance the fire resistance of plastics, flame retardants are added substances that delay or inhibit the spread of flame.
The duties of fire retardant additives include:
+ Increase the ignition temperature of the material
+ Slow down the fire rate
+ Reduce the amount of heat generated
+ Reduce flame growth
In order to have such properties, flame retardant additives need to be well dispersed with the base resin, without reducing the properties of the base resin or causing corrosion to the machinery.
3.1. Mechanism of flame retardant additives
Mechanism
|
Description
|
Extinguishing gaseous phase free radicals
|
These substances, when decomposed, will create reactive substances with active free radicals (O°, HO°, H°) generated during combustion to form stable, inflammable substances.
|
Creating an insulation layer
|
These substances when burned will create an inert slag layer around the material, helping to prevent contact of oxygen with the burning material.
|
Decreasing the heat of combustion reaction
|
These substances, when decomposed, will produce substances with high heat capacity, often producing water vapor.
|
Diluting gaseous phase
|
These substances, when decomposed, will produce inert gas, pushing oxygen around the environment out of the combustible material.
|
3.2. Types of flame retardants
Halogen flame retardants (Cl, Br)
These substances, when decomposed, will generate free radicals Br°, Cl°, which react with active free radicals (O°, HO°, H°) to form stable, inflammable products.
Someexamples of halogen flame retardants: Decabromodiphenyl oxide (DECA), tetrabromobisphenol A (TBBA), Hexabromocyclododecane (HBCD), TBBA-bis-(2,3-dibromo propyl ether), Chloroparaffins
Phosphorus flame retardant
Phosphorus compounds when burned will produce phosphoric acid, which helps to form a hard, heat-inert slag layer around the burning object, helping to prevent oxygen contact.
Some examples of phosphorus flame retardants: Ammonium Polyphosphate (APP), red phosphorus, Melamine Polyphosphate (MPP), Alkyl phosphate, phosphate ester, bisphenol A diphosphate (BDP)
Nitrogen flame retardants
Involved in the formation of an inert slag layer, which prevents oxygen. When they burn, they also produce an inert gas (N2, NO2) that pushes oxygen away from the burning object.
Some examples of nitrogen flame retardants: Melamine Polyphosphate (MPP), Melamine Cyanuarate (MC)
Inorganic flame retardants
Combustion products are inert solid compounds, thus helping to form an inert slag layer. Some compounds are thermally degradable and produce water, which lowers the temperature of the combustion process.
Some examples of inorganic flame retardants: Aluminum hydroxide, and magnesium hydroxide
4. Flame retardant additives from EuroPlas
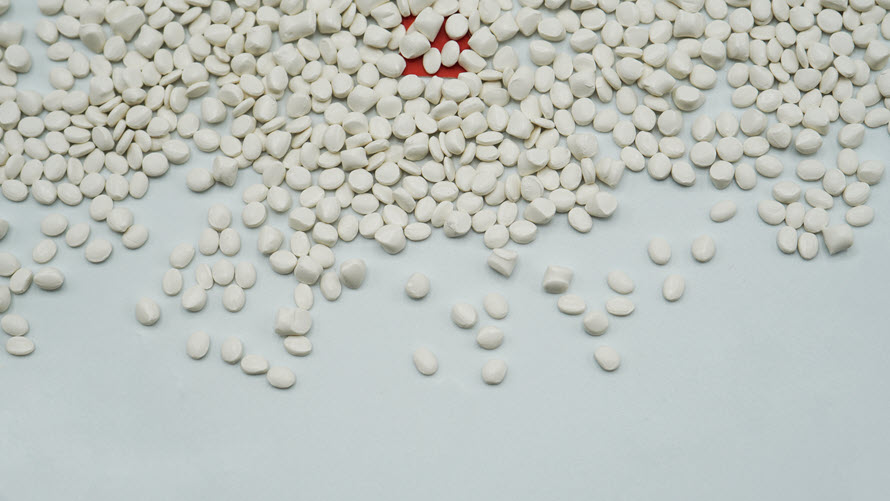
Europlas flame retardants offer high-impact properties, good thermal and dimensional stability, and good scratch resistance. Our product follows the UL 94: V0, V1 và V2 standard that guarantees quality for use and processing. Below are some of its superior features:
- Limit the spread of fire by working on the plastic surface
- Good dispersion with most of the standard resin
- No mechanical degradation caused to end-products
- Reasonable price
- No equipment corrosion
For more detailed information and to receive product samples, please contact our consultant team today, we’ll be more than happy to help!