When it comes to material selection, ABS vs Polycarbonate are two popular choices with distinct characteristics. ABS offers a good balance of strength and affordability, while Polycarbonate excels in impact resistance and optical clarity.
In this article, we will delve into the differences between ABS vs Polycarbonate, exploring their pros and cons, and help you decide which material is better suited for your specific requirements. Whether you're working on automotive parts, consumer goods, or electronics, understanding the differences between ABS vs Polycarbonate (PC) will guide you in making an informed decision. Let's dive into the ABS vs Polycarbonate comparison and find the right choice for your project.
Read more: About PC ABS Plastic: What is it?
1. ABS and PC - What are they?
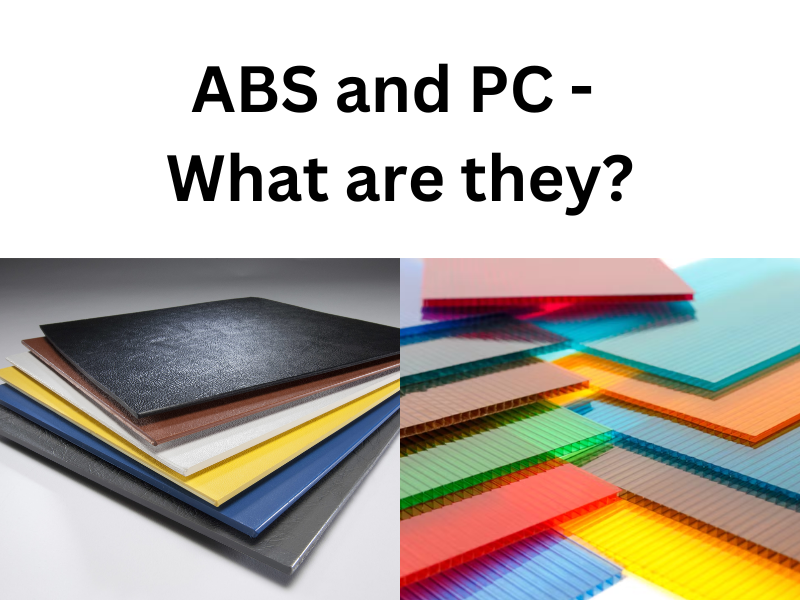
ABS and PC
Before deciding on which between ABS vs Polycarbonate, we need to know what they are exactly first.
ABS is a commonly used engineering thermoplastic known for its excellent balance of strength, impact resistance, and affordability. It is a blend of three monomers: acrylonitrile, butadiene, and styrene. ABS has gained popularity in various industries, including automotives, electronics, and consumer goods, due to its versatile nature and a wide range of desirable properties. The material offers good tensile strength, dimensional stability, and resistance to abrasion, making it suitable for applications that require durability and impact resistance.
Read more: Top ABS Plastic Manufacturers You Need to Know
Polycarbonate, on the other hand, is another widely utilized thermoplastic known for its exceptional toughness, optical clarity, and high heat resistance. It is derived from bisphenol A (BPA) and phosgene and is often referred to by its abbreviation, PC. Polycarbonate exhibits remarkable impact strength, making it ideal for applications where impact resistance is crucial. Its optical clarity and ability to be molded into complex shapes have made it a popular choice in industries such as automotive, electrical, and medical.
Read more: What is polycarbonate plastic? Find out its amazing properties
2. ABS vs Polycarbonate - Main differences
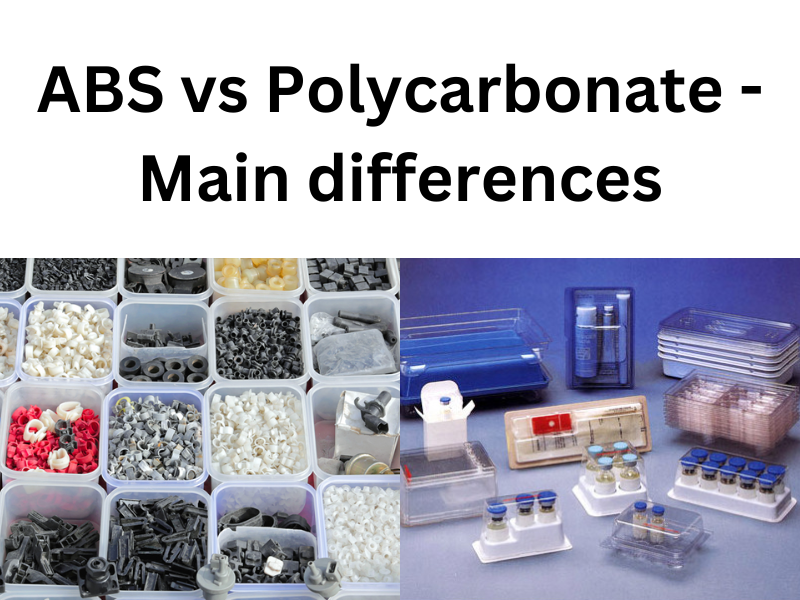
Differences between ABS and PC
In this section, we shall compare and point out the main differences between ABS vs Polycarbonate.
2.1 ABS vs PC: Mechanical properties
ABS is known for its good tensile strength and impact resistance. It offers durability and the ability to withstand impacts, making it a suitable choice for applications that require robustness. ABS also demonstrates higher resistance to scratching and marring compared to Polycarbonate. These mechanical properties make ABS well-suited for various industries where impact resistance is important, such as automotives, consumer goods, electronics, and toys.
Polycarbonate is renowned for its exceptional toughness and impact strength. It can withstand significant forces without breaking or shattering, making it ideal for applications where impact resistance is crucial. The remarkable mechanical properties of Polycarbonate make it a preferred choice for industries such as automotives, electrical, medical, and safety equipment. Its ability to endure high impacts without compromising structural integrity provides added safety and reliability.
2.2 ABS vs PC: Cost
When considering cost, ABS is generally more affordable compared to Polycarbonate. Its lower cost makes it an attractive option for applications that require a balance between performance and budget considerations. ABS offers a cost-effective solution while maintaining satisfactory mechanical properties. This affordability makes it a popular choice in industries where cost optimization is important.
Polycarbonate, on the other hand, tends to be more expensive than ABS. The higher cost of Polycarbonate is justified by its superior mechanical properties and optical clarity. It provides exceptional impact resistance and can withstand demanding conditions, making it suitable for applications that require high performance. The increased cost of Polycarbonate is often justified for applications where its unique properties are necessary for achieving desired results.
2.3 ABS vs PC: Sustainability
ABS is a recyclable thermoplastic, allowing it to be melted and reprocessed for future use. The recycling process for ABS is relatively straightforward, contributing to its sustainability factor. However, it is important to note that ABS production typically involves the use of petrochemicals, which raises environmental concerns. Balancing the recyclability of ABS with its initial production process is important when considering sustainability.
Polycarbonate is also recyclable, but its recycling process is more involved due to its higher melting point. While Polycarbonate can be recycled, the process may require specialized facilities and techniques. Additionally, the production of Polycarbonate involves the use of bisphenol A (BPA), which has raised some concerns regarding its potential impact on health and the environment. Sustainability-conscious applications may require further evaluation and consideration when choosing Polycarbonate.
2.4 ABS vs PC: Applications
ABS finds extensive applications in automotive parts, consumer goods, electronics, and toys. Its combination of strength, impact resistance, and affordability make it suitable for various components and casings. ABS is commonly used for interior parts in automobiles, electronic enclosures, and structural components in consumer goods. Its versatility and cost-effectiveness make it a popular choice in industries that require durable and impact-resistant materials.
Polycarbonate is widely used in applications that demand exceptional impact resistance and optical clarity. It finds its applications in automotive headlights, safety goggles, electrical enclosures, medical devices, and more. Polycarbonate's transparency and ability to be molded into complex shapes make it ideal for products where both durability and visual clarity are crucial. Its usage in industries that prioritize safety, aesthetics, and precision is highly prominent.
3. ABS vs Polycarbonate - Which one is better?
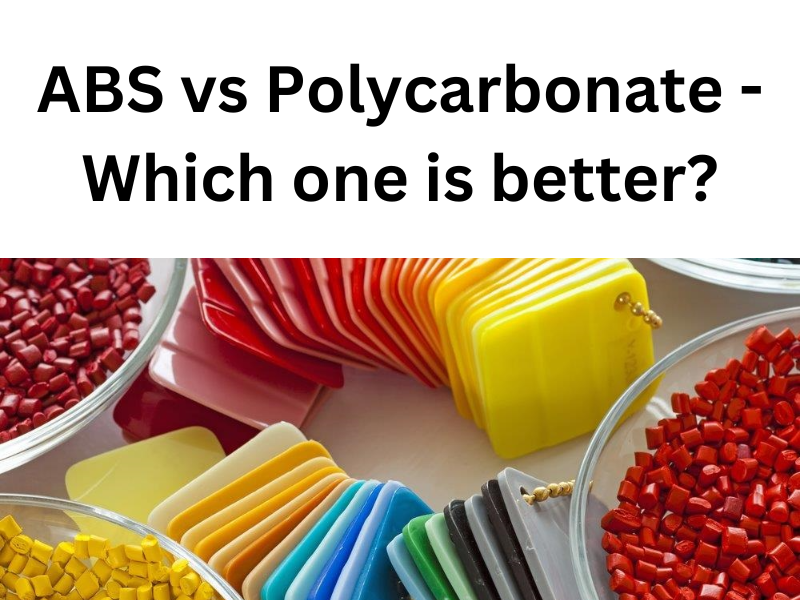
Choosing between ABS and PC
When comparing ABS vs Polycarbonate, it's important to consider their key advantages and disadvantages to determine which material is better suited for your specific needs.
ABS:
- Pros: ABS offers good strength and impact resistance, making it suitable for applications that require durability. It is also more cost-effective compared to Polycarbonate, making it a budget-friendly choice. ABS is widely available and can be easily molded into various shapes.
- Cons: ABS may not be as strong as Polycarbonate and is more prone to degradation from UV radiation. It also has lower heat resistance, limiting its suitability for high-temperature applications.
Polycarbonate:
- Pros: Polycarbonate excels in impact resistance and toughness, providing excellent durability. It offers superior optical clarity and can withstand high temperatures without significant degradation.
- Cons: Polycarbonate is generally more expensive than ABS. Its high melting point makes it more challenging to mold and process compared to ABS.
The choice between ABS vs Polycarbonate depends on your specific requirements. If you prioritize cost-effectiveness, good strength, and ease of molding, ABS may be the better option. On the other hand, if you require exceptional impact resistance, superior optical clarity, and high-temperature resistance, Polycarbonate is a suitable choice. Consider your project's needs and weigh the pros and cons of each material to make an informed decision.
4. ABS & PC products from EuroPlas
At EuroPlas, a leading masterbatch manufacturer in Vietnam, we offer a range of high-quality ABS vs Polycarbonate (PC) products that cater to various industry needs. Our commitment to excellence is reflected in our rigorous testing procedures, advanced manufacturing processes, and the superior quality of our ABS and PC engineering compounds, as well as our color masterbatch solutions.
Our ABS plastic engineering compound is designed to meet the demanding requirements of diverse applications. We prioritize quality in every step of the manufacturing process, starting from the selection of premium-grade raw materials. Our ABS compounds undergo extensive testing to ensure they meet the highest standards for strength, impact resistance, and overall performance. With our ABS compounds, you can expect excellent dimensional stability, good surface finish, and consistent color dispersion. Whether you need ABS for automotive parts, consumer electronics, or other applications, our products deliver the reliability and durability you seek.
When it comes to PC plastic engineering compounds, EuroPlas stands out for its commitment to delivering exceptional quality. Our PC compounds are meticulously formulated to provide superior impact resistance, high optical clarity, and excellent heat resistance. We understand the importance of consistent product quality, and our manufacturing process is backed by stringent quality control measures. We conduct comprehensive testing to ensure our PC compounds meet the highest standards for strength, toughness, and dimensional stability. With EuroPlas' PC compounds, you can rely on the performance and reliability of your end products, whether they are in the automotives, electronics, or other industries.
In addition to our ABS and PC engineering compounds, EuroPlas offers color masterbatch solutions for ABS and PC materials. Our color masterbatches are carefully developed to provide vibrant, consistent, and durable coloration for your ABS and PC products. We understand that aesthetics and brand identity play a crucial role in product success, and our color masterbatches deliver exceptional color consistency and colorfastness. Our team of experts ensures that our color masterbatches are meticulously formulated, thoroughly tested, and optimized for compatibility with ABS and PC materials. With EuroPlas' color masterbatches, you can achieve the desired visual impact for your products while maintaining the mechanical properties and performance characteristics of ABS and PC.
At EuroPlas, we are dedicated to providing superior-quality ABS and PC products that meet your specific requirements. Contact us today to discuss your project needs and discover how our reliable solutions can add value to your applications.