1. Introduction
Plastic presents every aspect of life, from electric appliances to children's toys. Plastic resin and filler masterbatch are the two most often used materials when making products from this material. The benefits and drawbacks of each are different. Plastic resin is highly pure, ensuring the quality of the finished product. Filler masterbatch, also known as plastic filler, is a versatile additive that can reduce the cost or improve the properties of plastic.
How are plastic resin and filler masterbatch different from one another? In this article, you'll find all the details you need to know about the two varieties.
2. What Is The Difference Between Plastic Resin And Filler Masterbatch?
2.1. Origin - Characteristics
Plastic resins are derived from fossil fuels such as oil and natural gas. The basic production process includes the following steps:
Step 1. Separate the components of petroleum or natural gas.
Step 2. Polymerize the components to form long molecular chains.
Step 3. Mold the plastic resins to the desired size and form.
Find out more about the production process at: What is Plastic Resin? How is Plastic Resin Made?
Polyethylene (PE), Polypropylene (PP), Polystyrene (PS), Polyvinyl chloride (PVC), and Polytetrafluoroethylene (PTFE) are examples of common plastic resin types.
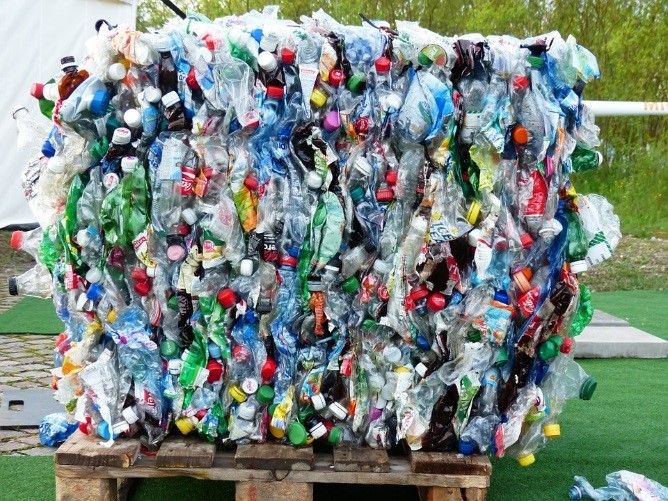
Polyvinyl chloride (PVC) is a top choice for manufacturing a wide range of products.
Filler masterbatch is produced from these natural materials, like clay, limestone, paper pulp, and many others. The following steps are part of the production process:
Step 1. Prepare ingredients.
Step 2. Crush or grind ingredients into powder.
Step 3. Mold particles to the desired size and shape.
Some typical filler masterbatches: inorganic fillers (clay, CaCO3 filler masterbatch, mica), organic fillers (wood pulp, paper pulp, cellulose fiber)
In contrast to fillers, which can vary in color, turbidity, and gloss depending on the production components, plastic resins are clear or white and contain no contaminants. Plastic resin products are often better quality, last longer, and look better than products made from other materials, but they cost more and are harder to recycle. Filler masterbatch products are less expensive and easier to recycle, but at the same time, they are also of inferior quality, less long-lasting, and less aesthetically attractive.
Learn more about filler masterbatch: What is CaCO3 filler? Benefits of CaCO3 filler in plastic production
2.2. Methods to distinguish plastic resin and filler masterbatch?
The easiest way to tell two ingredients apart is to observe them.
Direct observation testing:
Plastic resins are typically bright white and have a smooth, uniform texture. Filler masterbatch, on the other hand, often has smaller particle size than the original plastic and a colorful look, due to its content of different colored fillers.
General-purpose machine testing:
Characteristic |
Plastic Resin
|
Filler Masterbatch
|
Differential scanning calorimetry |
High |
Low |
Shore D hardness |
High |
Low |
Tensile Strength |
High |
Low |
Chemical analysis testing:
Chemical analysis methods can reveal the composition of plastic pellets. Virgin plastic pellets contain only plastic, while filler masterbatch contains plastic and other fillers.
2.3. Applications
Depending on the needs and purposes of use, manufacturers can choose the appropriate type of virgin plastic resins or plastic fillers.
Products made from virgin plastic resins are suitable for the following needs:
- Prioritize quality and do not contain toxic substances: household appliances, children's toys, electronics, medical devices, and food packaging.
- Direct contact with food: food containers, eating utensils, food packaging.
Products made from plastic fillers are suitable for the following needs:
- Need low prices: garbage bags, supermarket bags, and agricultural mulch.
- Improve product properties: plastic pipes, construction materials, and automotive parts.
- Environmentally friendly: bioplastic bottles, biobags, and compostable packaging.
However, both virgin plastic pellets and plastic fillers can have certain impacts on the environment.
2.4. Sustainable plastic production and consumption: Plastic resins vs. filler masterbatches
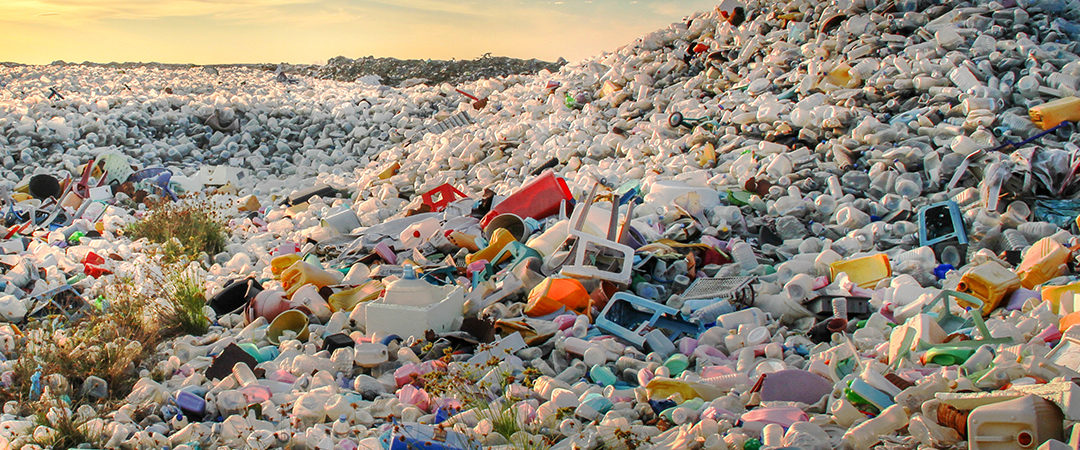
According to the OECD, only 9% of plastic waste was successfully recycled in 2019
Virgin plastic resins are produced from non-renewable resources, such as petroleum and natural gas. The production of virgin plastic resins also consumes a lot of energy and emits greenhouse gases. In addition, they are difficult to recycle and can exist in the environment for
hundreds of years.
Plastic fillers are produced from different raw materials, including clay, limestone, wood pulp, etc. The extraction and transportation of these raw materials can cause environmental pollution. Additionally, plastic fillers can contribute to increased plastic waste when plastic products made from fillers are disposed of.
Despite the environmental challenges posed by virgin plastic pellets and plastic fillers, some positive trends are emerging. Recycled plastic is a new source of raw materials to replace virgin plastic. Using recycled plastic helps reduce the need for virgin plastic, contributing to the conservation of natural resources.
Plastic fillers are also becoming more widely used to improve the properties of plastics, such as strength, stiffness, and heat resistance. New types of plastic fillers with superior properties are being developed, which could further reduce the need for virgin plastic in the future.
3. EuroPlas - The best filler masterbatch solution for businesses
EuroPlas is a leading global filler masterbatch manufacturer with over 16 years of experience working with international businesses. EuroPlas filler masterbatch utilizes calcium carbonate (CaCO3) combined with plastic resin and various additives as per customer requirements.
EuroPlas filler masterbatch offers:
- Reduced production costs: By replacing a portion of plastic resin with calcium carbonate powder, the production cost of finished products is optimized.
- Enhanced product properties: including sturdiness, impact resistance, scratch resistance, heat resistance, etc.
- Increased stability in the processing process: Filler masterbatch increases solidity, minimizes deformation and cracking.
- Improved printing ability and surface quality: Filler masterbatch increases surface smoothness and minimizes shrinkage.
EuroPlas filler masterbatch is widely used in many plastic industries including:
- Packaging: Plastic bags, plastic films, plastic bottles, plastic boxes, etc.
- Electrical equipment: Plastic pipes, plastic cases, etc.
- Construction: Plastic bricks, plastic floors, etc.
- Automation: Plastic cases, plastic components, etc.
Popular EuroPlas filler masterbatch products:
- PP filler masterbatch: used in the production of plastic bags, plastic films, plastic bottles, plastic boxes, etc.
- PE filler masterbatch: used in the production of plastic pipes, plastic cases, etc.
- ABS filler masterbatch: used in the production of electrical equipment, toys, etc.
- PVC filler masterbatch: used in the production of plastic pipes, plastic cases, etc.
4. Conclusion
Distinguishing plastic resin and filler masterbatch is crucial for businesses to ensure product quality and optimize production costs. By understanding the key differences between these two materials, businesses can choose the right type of plastic for their specific needs and applications.
Discover more optimal plastic material solutions for your business at our website.