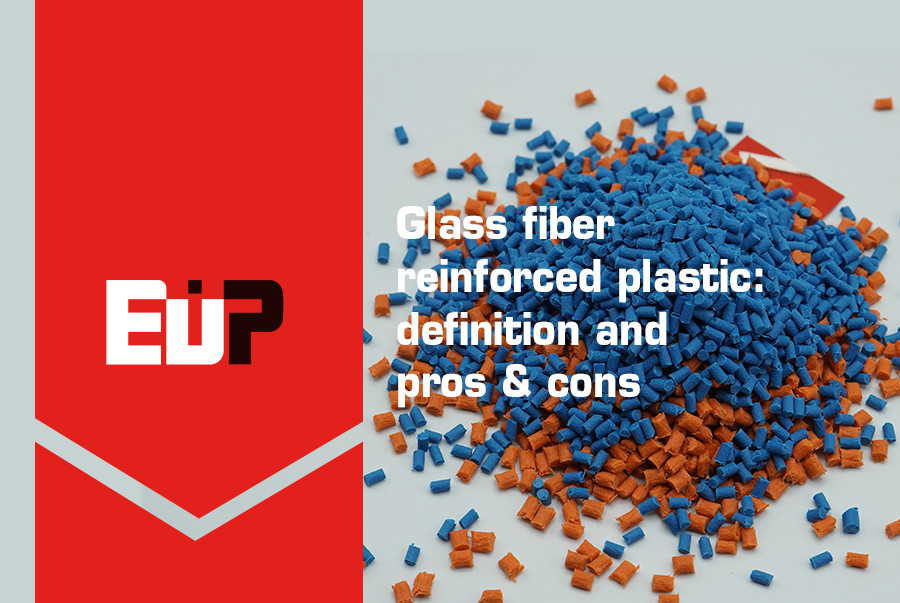
Glass fiber reinforced plastic (GRP), also known as fiberglass, is a composite material made of plastic reinforced with fine glass fibers. It has exceptional mechanical properties such as high strength, stiffness, and resistance to corrosion, making it a popular choice for a wide range of applications.
In this article, we will delve deeper into the definition of glass fiber reinforced plastic and its mechanical properties. We will also explore the pros and cons of using GRP, and help you decide whether it is the right material for your project.
1. What does glass fiber reinforced plastic mean
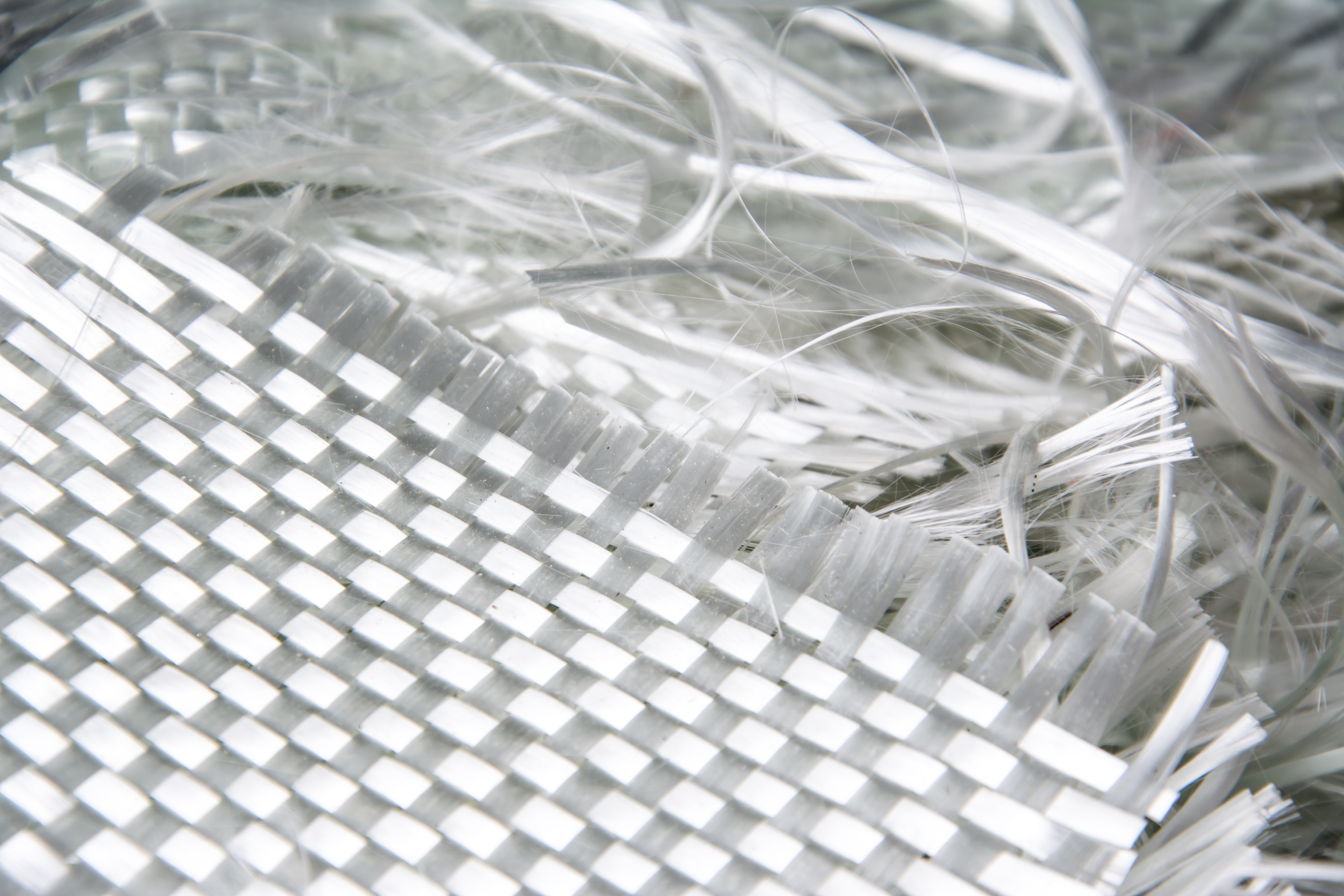
Credit: Plasticon Projects
1.1. What is glass fiber reinforced plastic?
Glass fiber reinforced plastic (GRP), also known as fiberglass, is a composite material made up of a thermosetting plastic matrix reinforced with fine glass fibers. The glass fibers are usually woven into a mat, which is then impregnated with a polymer resin, such as polyester or epoxy.
GRP is manufactured by combining the plastic matrix with the glass fibers in a process called pultrusion. The resulting material is strong, lightweight, and corrosion-resistant.
GRP can be molded into a variety of complex shapes and sizes, including sheets, panels, pipes, and molded components. This versatility, coupled with its high strength-to-weight ratio, has made GRP a popular choice in a wide range of applications, including automotive, aerospace, marine, and construction industries.
1.2. Glass fiber reinforced plastic mechanical properties
Glass fiber reinforced plastic (GRP) has a unique combination of mechanical properties as followings:
- High strength-to-weight ratio: GRP has an excellent strength-to-weight ratio, which means that it is strong and lightweight at the same time. This property makes it ideal for applications where weight is a critical factor, such as in aerospace and automotive industries.
- High stiffness: GRP is a very stiff material, which means that it resists deformation under load. This property makes it ideal for applications where stiffness is essential, such as in structural components.
- Excellent corrosion resistance: the high resistance to corrosion of GRP is applied when the material is exposed to harsh environments, such as in chemical processing and marine industries.
- Good impact resistance: GRP has good impact resistance, it can absorb energy from impacts without fracturing or cracking.
- Low thermal conductivity: GRP has low thermal conductivity, so it does not conduct heat well. This property makes it ideal for applications where insulation is critical, such as in building and construction.
Remember that glass fiber reinforced plastic mechanical properties can vary depending on the type of polymer matrix and the glass fiber reinforcement used. For example, epoxy-based GRP has better mechanical properties than polyester-based GRP. The choice of reinforcement, such as the type of glass fiber and the fiber orientation, can also affect the mechanical properties of GRP. Therefore, it's crucial to select the appropriate type of GRP for the specific application.
1.3. The manufacturing process of glass fiber reinforced plastic
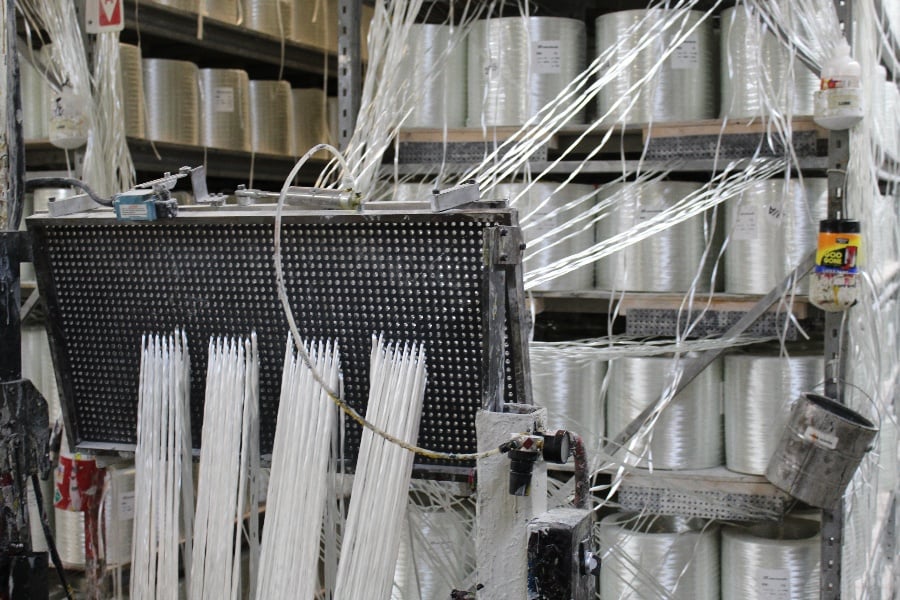
Credit: Tencom
The manufacturing process of glass fiber reinforced plastic (GRP) involves several steps, starting with the preparation of a mold and ending with the curing and demolding of the final product.
Step 1: Prepare the mold
The mold can be made of various materials, such as metal or composite, depending on the complexity of the part to be produced. Once the mold is ready, a release agent is applied to its surface to prevent the GRP from sticking to the mold.
Step 2: Prepare the polymer matrix
The polymer matrix is usually in the form of a liquid resin. The resin is mixed with a hardener or catalyst to initiate the curing process. The type of resin used depends on the desired properties of the final product. For example, epoxy resin is known for its high strength and stiffness, while polyester resin is more affordable and easier to work with.
Step 3: Impregnation
After the resin is prepared, the glass fibers are applied to the mold surface in the desired orientation. The glass fibers can be bundled into rovings or woven into fabrics, depending on the application. Once the glass fibers are in place, the resin is applied to the fibers to saturate them.
Step 4: Curing
The GRP is then allowed to cure, which can be done at room temperature or by applying heat. During the curing process, the resin hardens and binds the glass fibers together. Once the GRP has healed, it is removed from the mold, and any excess material is trimmed.
Additional steps may be required depending on the application. For example, post-curing may be necessary to achieve the desired mechanical properties, and surface finishes such as painting or coating may be added for aesthetic purposes or to provide additional protection against environmental factors.
2. Advantages and disadvantages of glass fiber reinforced plastic
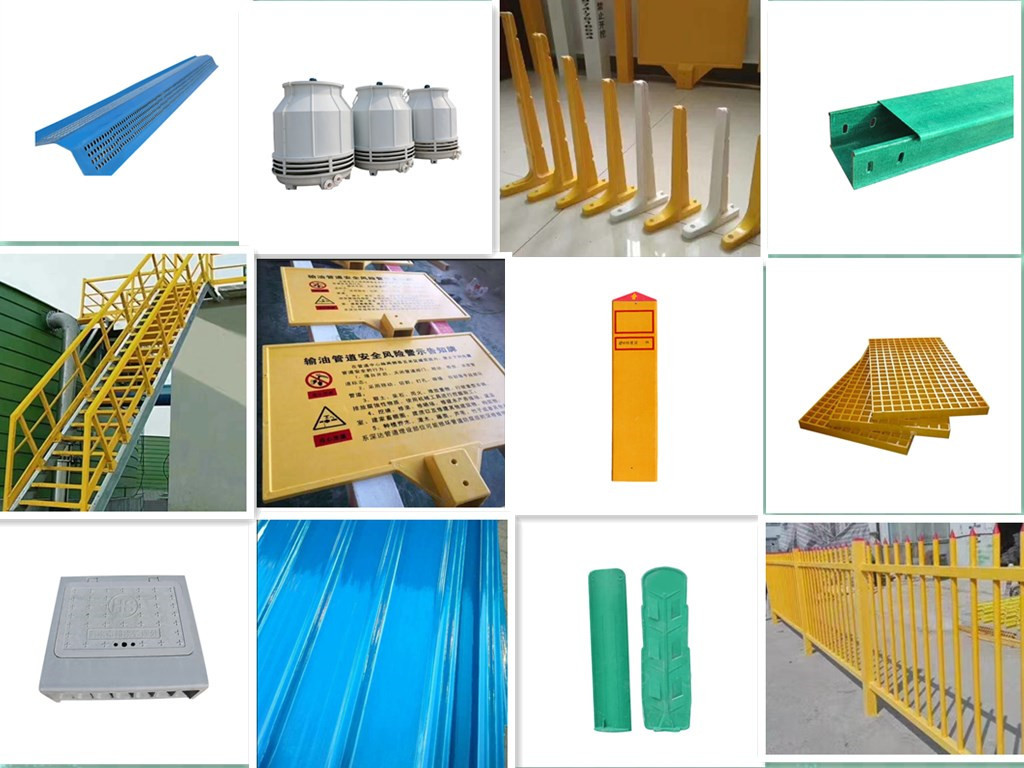
2.1. Advantages of glass fiber reinforced plastic
Glass fiber reinforced plastic (GRP) has gained popularity in various industries due to its numerous advantages over traditional materials like steel, aluminum, and wood. Here are some of the key advantages of GRP:
- Lightweight: GRP is a lightweight material. It can be up to 75% lighter than steel and up to 30% lighter than aluminum.
- High strength-to-weight ratio: Despite its low weight, GRP has a high strength-to-weight ratio, which means it can support heavy loads while remaining lightweight.
- Corrosion-resistant: GRP is highly resistant to corrosion, making it a durable and long-lasting material that can withstand exposure to harsh environments like saltwater, chemicals, and UV radiation.
- Design flexibility: GRP can be molded into complex shapes and can be customized to fit specific design requirements. This makes it a versatile material that can be used for a wide range of applications.
- Low maintenance: GRP requires very little maintenance and is easy to clean. It does not rust, rot, or corrode, and it is resistant to fading, chalking, and cracking.
- Fire-resistant: GRP is a fire-resistant material that can withstand high temperatures without melting or emitting toxic fumes. This makes it a safe material for use in applications where fire is a concern.
- Cost-effective: While the initial cost of GRP may be higher than traditional materials, its low maintenance requirements and long lifespan make it a cost-effective material in the long run.
- Versatile: GRP can be molded into complex shapes, allowing for the creation of intricate designs and structures. It can also be customized to meet specific design requirements.
2.2. Disadvantages of glass fiber reinforced plastic
While glass fiber reinforced plastic (GRP) has many advantages, there are also some disadvantages to consider when choosing this material for a project. Some of the main disadvantages of GRP include:
- Brittleness: GRP can be brittle and prone to cracking or breaking under sudden impact. This can be a concern in applications where the material is exposed to high stress or impact loads.
- Difficult to repair: GRP can be difficult to repair, especially if damage is in a critical area or if the damage is extensive. Repairs may require specialized knowledge and equipment, which can be costly.
- Limited temperature range: GRP has a limited temperature range in which it can be used, typically between -40°C and 100°C. This can be a concern in applications where the material is exposed to extreme temperatures.
- Environmental impact: The manufacturing process of GRP involves the use of chemicals, some of which can be harmful to the environment. Additionally, GRP products may not be recyclable, which can lead to waste management issues.
- Design limitations: Although GRP can be molded into complex shapes, there may be limitations in terms of size and design. The manufacturing process may also be limited by the size of the mold and the ability to remove the finished product from the mold.
3. Want to customize your glass fiber plastic material?
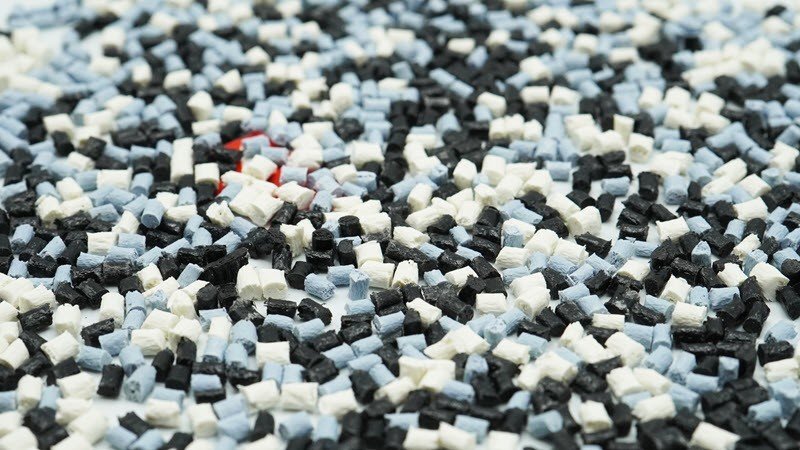
If you are looking to customize your glass fiber reinforced plastic (GRP) material, EuroPlas can help. EuroPlas is a top masterbatch manufacturer in Vietnam with over 15 years of experience, specializing in the production of high-quality glass fiber compound and related products.
Our glass fiber compound can be customized to meet specific design requirements, including properties such as color, strength, and stiffness. EuroPlas' experienced team of engineers and technicians work closely with customers to understand their needs and develop tailored solutions that meet their exact specifications.
In addition to glass fiber compounds, EuroPlas also offers a range of other compounds and masterbatches, including filler masterbatch, plastic additive and bioplastic compounds. These products can be used to enhance the performance of materials in a variety of applications.
EuroPlas uses state-of-the-art equipment and quality control processes to ensure the consistency and reliability of our products. We are committed to providing exceptional customer service and support, with a focus on delivering high-quality products at competitive prices.
If you are interested in customizing your GRP material, contact our team for the earliest support!