EuroPlas and EuP Egypt are leading manufacturers of natural CaCO3 filler masterbatch, an essential material used in the plastic industry. In this article, we will take a closer look at the process and equipment used by EuroPlas to produce high-quality natural CaCO3 filler masterbatch. Additionally, we will discuss the criteria used to evaluate the quality of the final product, ensuring that EuroPlas' natural CaCO3 filler masterbatch meets industry standards. Let's dive in!
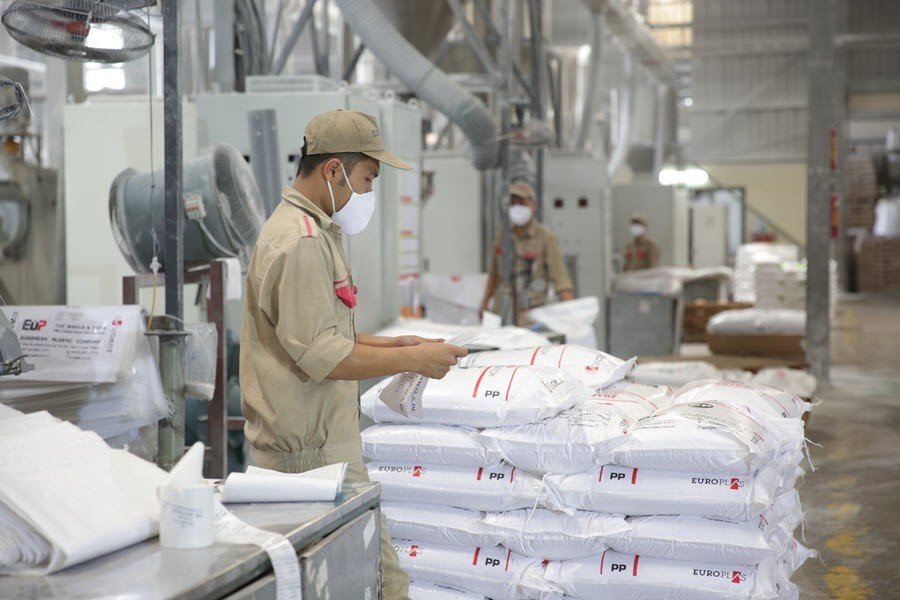
Step 1: CaCO3 filler formula
To produce CaCO3 filler plastic, EuroPlas carefully designs the appropriate CaCO3 filler formula
based on the customer's specific requirements. This involves considering the following factors:
Composition: The composition of the filler is critical in determining the product's final properties. We choose the appropriate type of CaCO3 filler based on the customer's application, such as particle size, surface treatment, and purity.
Color: The desired color of the final product is also a critical factor in the formula design. We can achieve a wide range of colors by adding color pigments to the formula.
Ratio of filler to resin: The ratio of filler to resin plays a crucial role in determining the product's strength, stiffness, and other properties. We work closely with the customer to find the optimal ratio for their specific application.
Additives: Depending on the customer's requirements, we can add various additives to the formula, such as stabilizers, lubricants, and flame retardants. These additives can enhance the product's properties or improve the manufacturing process.
At EuroPlas, we have extensive experience in formula design and can create customized solutions to meet the customer's exact needs. By carefully considering each factor, we can produce high-quality CaCO3 filler plastic that meets or exceeds the customer's expectations.
Step 2: Material selection
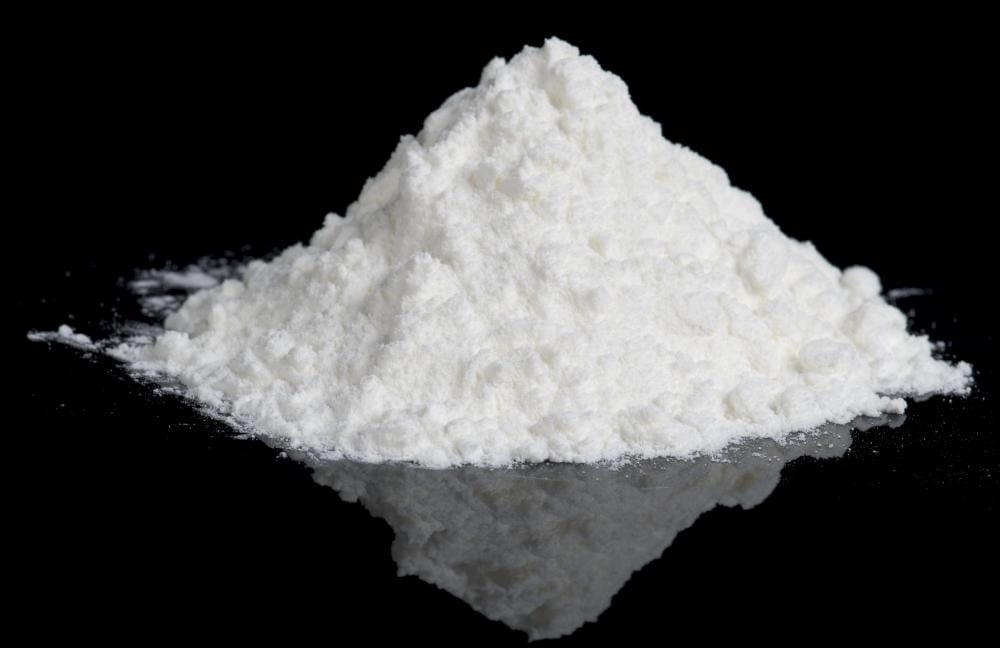
To produce high-quality CaCO3 filler plastic (for example, CaCO3-filled polypropylene), EuroPlas carefully selects the materials used in the production process. The materials chosen can have a significant impact on the final product's quality and properties. Here are the main materials used:
Limestone powder: Limestone powder is the primary material used as the filler in the CaCO3 filler plastic. At EuroPlas, we source our limestone powder from Yen Bai, Vietnam. Yen Bai is well-known for its high-quality limestone deposits, and the limestone powder we use is of the highest purity. YBM is our main supplier of limestone powder for this product.
High-quality resin: The type of resin used is essential in determining the final product's properties. At EuroPlas, we use a high-quality resin that is appropriate for the specific application. For example, if a customer requires CaCO3 filler plastic for woven polypropylene bags, we would use polypropylene resin as the base.
Colorants and additives: Depending on the customer's requirements, we can add colorants and various additives to the CaCO3 filler plastic. For example, if a customer requires a specific color, we can add color pigments to achieve the desired color. We can also add various additives, such as UV stabilizers, antioxidants, and flame retardants, to improve the product's properties.
By carefully selecting each material used in the production process, EuroPlas can produce high-quality CaCO3 filler plastic that meets or exceeds the customer's expectations.
Step 3: Processing
At EuroPlas, the process of manufacturing CaCO3 filler involves several steps, including material selection, mixing, melting, extruding, and cutting. Each step requires proper CaCO3 masterbatch filler equipment and careful attention to detail to ensure that the final product meets the desired specifications and quality standards.
After the raw materials have been selected and weighed according to the desired composition, the next step is to mix them thoroughly with a CaCO3 plastic filler masterbatch machine. This is done using a high-speed mixer that ensures the particles of CaCO3 filler are evenly distributed throughout the plastic resin.
Once the mixture is well-blended, it is heated to a high temperature until it melts and forms a homogenous liquid. The temperature at which the mixture melts and becomes fluid depends on the type of plastic resin used but typically ranges from 170°C to 220°C.
The liquified mixture is then cooled to a specific temperature and fed into a twin-screw extruder, which uses rotating screws to push the material forward and compress it. The extruder forces the mixture through a die, which shapes the material into the desired form. In the case of CaCO3 filler, this is usually in the form of pellets or granules.
After the mixture has been extruded and shaped, the final step is to cut the material into small pieces. This is done using a pelletizer or cutter, which slices the extruded material into the desired size. The pellets are then ready to be used as a raw material in various applications, such as in the manufacturing of plastic products or as a filler in rubber and paper products.
Step 4: Packaging
After the production process is complete, the next step is packaging the CaCO3 filler product. The packaging process includes determining the appropriate package size and material to ensure the product's quality is maintained during storage and transportation.
Our CaCO3 filler product is usually packaged in bags made of high-quality plastic material. The bags are sealed to protect the product from moisture and other contaminants. The package size can vary depending on the customer's requirements and intended use. Typically, the bags come in sizes ranging from 25kg to 1 ton.
During storage, the bags should be kept in a dry and cool place to prevent moisture and other contaminants from affecting the product's quality. The recommended storage temperature is between 20-30°C, and the relative humidity should be less than 75%.
Overall, the packaging process is a crucial step in ensuring our CaCO3 filler product's quality is maintained until it reaches the customer. Proper packaging and storage procedures can help prevent product degradation, resulting in a satisfied customer and a successful business.
Criteria to evaluate the quality of CaCO3 filler masterbatch
To ensure that the CaCO3 filler masterbatch meets the required specifications and quality standards, EuroPlas uses a variety of testing equipment. This includes devices to measure properties such as melt flow index, ash content, particle size distribution, and moisture content. Additionally, EuroPlas may use various chemical analyses to determine factors such as the presence of impurities or the amount of additives.
One key standard that EuroPlas adheres to is ISO 9001, which provides guidelines for quality management systems. By following this standard, EuroPlas ensures that its production processes are standardized and that the quality of its products is consistently high. In addition, EuroPlas may also obtain other certifications, such as REACH, RoHS, or FDA compliance, depending on the intended use of the CaCO3 filler masterbatch.
By using rigorous testing equipment and adhering to industry standards and certifications, EuroPlas is able to provide high-quality CaCO3 filler masterbatch products to its customers. These measures also demonstrate EuroPlas' commitment to ensuring the quality and reliability of its products, which in turn helps its customers achieve success in their own manufacturing processes.