Laser cutters are valuable devices capable of creating intricate cuts and patterns using a powerful laser beam that can heat and melt the material being cut. From wood, metal, and plastic to glass and gemstones, almost any material can be cut with a laser cutter if properly configured, except for materials with high reflectivity.
Proper laser cutter setup depends on five main factors: laser power, cutting speed, pulses per inch (PPI), number of passes, and material thickness or engraving depth. This article will discuss laser cutter setup for different types of materials, the types of machines used for laser cutting, as well as safety precautions to follow during laser cutting operations.
1. What safety precautions should be taken when laser cutting?
When operating a laser cutting machine, it is essential to utilize appropriate safety equipment to safeguard workers from potential burns, vision impairment, and exposure to harmful fumes. Laser beams are concentrated and powerful enough to etch and cut through solid materials, making it imperative to employ adequate laser eye protection to prevent any damage to one's vision. Laser safety goggles effectively block the specific wavelength of the laser beam.
Moreover, ensuring proper ventilation for the laser cutter is crucial. Depending on the material being cut, it may produce harmful fumes referred to as "laser-generated air contaminants" (LGACs). These contaminants can include toxic gases like benzene, hydrochloric acid, and toluene. It is imperative to effectively vent these byproducts out of the laser cutting system and the surrounding room to maintain a safe working environment.
Lastly, it is essential to have a readily accessible fire extinguisher on hand due to the fire hazards associated with laser cutters. To minimize the risk of fires, it is advisable to follow recommended operating settings, never leave a laser system unattended, and maintain a clean workspace around the laser equipment at all times.
Material
|
Power (% of total wattage)
|
Speed (mm/s)
|
Pulses per Inch (PPI)
|
Number of Passes
|
Depth (in)
|
Acrylic (vector cut)
|
100
|
2
|
1000
|
1+
|
0.25
|
Acrylic (vector engraving)
|
2
|
4
|
1000
|
1
|
5
|
Other plastics (raster engraving)
|
15
|
100
|
500
|
1
|
1
|
Other plastics (vector cut)
|
25
|
1.2
|
500
|
1
|
60
|
Glass (raster engraving)
|
100
|
30
|
300
|
1
|
1
|
Glass (vector engraving)
|
10
|
7.9
|
300
|
1
|
1
|
Wood (raster engraving)
|
100
|
596
|
500
|
1
|
20
|
Wood (vector engraving)
|
80
|
10.1
|
500
|
1
|
30
|
Wood (vector cut)
|
50
|
3.1
|
500
|
1
|
125
|
Anodized Aluminum (raster engraving)
|
30
|
100
|
500
|
1
|
1
|
Anodized Aluminum (vector engraving)
|
4
|
4
|
1000
|
1
|
1
|
Aluminum (cutting)
|
100
|
500
|
1000
|
1+
|
0.25
|
Carbon steel (cutting)
|
100
|
33.3
|
1000
|
1+
|
0.25
|
Table of Recommended Laser Cutter Settings for Various Materials
2. What machines are utilized in laser cutting?
Laser cutting encompasses a wide range of machines, spanning from hobbyist models to custom-built industrial behemoths designed for mass production. The technology relies on three primary types of lasers for cutting various materials. The machine configurations and settings are contingent upon the laser type employed. The following are the three main categories of laser cutters:
2.1. CO2 lasers
CO2 lasers function by passing an electric current through a gas mixture-filled tube, generating the laser beam. Typically, this gas mixture comprises carbon dioxide, hydrogen, nitrogen, and helium. The laser tubes incorporate mirrors at both ends, with one mirror being fully reflective and the other partially reflective, allowing a portion of the light to pass through.
After reflecting off these mirrors, the intensified light transmitted through the partially reflective mirror is employed for the cutting and engraving of materials. Machines equipped with CO2 lasers are versatile and capable of cutting a wide array of materials, with a primary focus on wood, paper, paper-based products, and acrylics. These lasers are particularly well-suited for non-metallic materials.
.jpg)
CO2 Lasers
2.2. Fiber lasers
In contrast to CO2 lasers, which rely on electric current, gas mixtures, and mirrors to generate the laser beam, fiber lasers create the beam using specialized glass fibers that derive energy from pump diodes. Fiber lasers represent the costliest option among the three laser types but are distinguished by their minimal maintenance requirements and an impressive operational lifespan of up to 25,000 hours. These lasers excel at metal and thermoplastic engraving, yet they are versatile enough to work with a broad spectrum of materials, whether metallic or non-metallic.
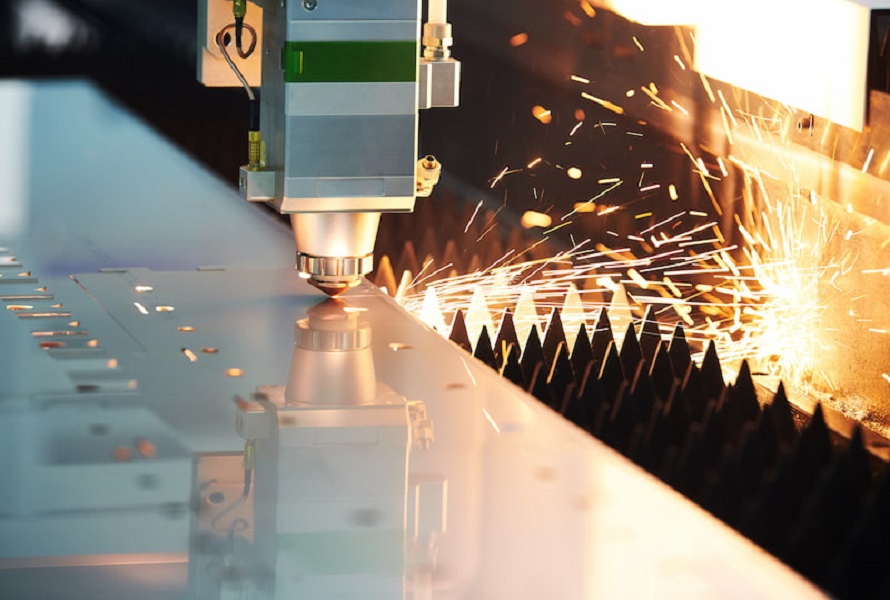
Fiber Lasers
2.3. Nd:YAG/Nd:YVO lasers
The designations Nd:YAG (neodymium-doped yttrium aluminum garnet) and Nd:YVO (neodymium-doped yttrium ortho-vanadate) pertain to the crystals employed in generating the laser beams of these machines. Although Nd:YAG and Nd:YVO laser machines can be relatively expensive, they offer unparalleled cutting prowess and can handle reflective metals with ease. These lasers are suitable for cutting both coated and non-coated metals, as well as non-metallic materials such as plastics and ceramics.
.jpg)
Nd:YAG/Nd:YVO Lasers
Characteristics
|
Laser CO2
|
Fiber Laser
|
Laser Nd:YAG/Nd
|
Laser Source
|
CO2
|
Fiber
|
Nd:YAG/Nd:YVO4
|
Operating Principle
|
Laser beam amplification in a CO2 gas environment
|
Laser emission within a fiber optic medium
|
Laser emission within a crystal medium
|
Advantages
|
Cost-effective, high power, suitable for various materials
|
High precision, high efficiency, long lifespan, suitable for thick metal cutting
|
High precision, high efficiency, suitable for thick materials with smooth surfaces
|
Disadvantages
|
Lower precision compared to fiber laser, lower efficiency compared to Nd:YAG/Nd laser
|
Higher cost
|
Higher cost compared to CO2 laser
|
Applications
|
Cutting wood, plastic, metal, ...
|
Cutting thick metal
|
Cutting thick materials with smooth surfaces
|
Comparison Table of Laser Cutter Types
3. What safety equipment should be used when laser cutting?
Safety equipment should be used to protect workers from burns, eye damage, and smoke when using a laser cutter. A laser is a highly focused beam of light, powerful enough to engrave and even cut through solid materials. Therefore, it is crucial to wear appropriate laser eye protection to prevent eye damage. Laser safety glasses work by blocking the wavelength of the laser beam.
Additionally, it is important to provide proper ventilation for the laser cutter. Depending on the material being cut, harmful smoke known as "laser-generated air contaminants" or LGAC may be produced. Toxic gases such as benzene, hydrochloric acid, and toluene are some byproducts potentially generated during the laser cutting process and need to be expelled from the laser cutting system.
Finally, a fire extinguisher should always be prepared and easily accessible because there is a risk of fire during the laser cutting process. To prevent the possibility of a fire, use recommended settings. Never operate a laser system without supervision and always keep the workspace around the laser machine clean.
.jpg)
What safety equipment should be used when laser cutting?
4. Consequences of not following recommended laser cutter settings
Failure to adhere to the recommended settings for a laser cutter can lead to adverse consequences. This can negatively impact the material being cut, the health and safety of the operators, and even the laser system itself.
Cutting materials with excessive energy levels or cutting too deeply in a single pass can damage the laser cutter's optics, increasing the risk of smoke, vapor, and fire hazards. Furthermore, intentionally cutting materials not designed for the laser system can potentially harm the laser system.
It is imperative never to cut PVC or other vinyl materials because doing so can release chlorine gas, which can damage the optical and laser beam control systems. Other materials like ABS and HDPE should also be avoided due to their tendency to melt and ignite on the machine, leading to cleanliness issues during cleanup and potential damage to the laser beam.
.jpg)
Consequences of Not Following Recommended Laser Cutter Settings
5. Are the settings for laser cutting the same as laser engraving?
The answer is: No, the settings for laser cutting are not the same as laser engraving. Laser cutting involves the laser beam passing through all the layers and creating a clear-cut path. In contrast, laser engraving only performs surface cuts on a part to create logos, illustrations, or text.
As a result, the energy usage, speed, and PPI (Pulses Per Inch) settings will differ significantly between the cutting and engraving processes. It is advisable to consult the laser cutter user manual to determine the precise laser cutter settings when working on cutting and engraving various materials.