Welcome to our comprehensive guide on polystyrene (PS) plastic. From packaging to construction and beyond, PS plastic's adaptability and unique properties have made it a ubiquitous presence in our daily lives. In this blog, we'll delve into the various forms of PS plastic, its applications in different industries, and the ongoing conversation about its environmental impact.
Join us as we uncover the fascinating world of PS plastic, its benefits, and the considerations we need to keep in mind as we navigate its usage in a more sustainable manner. Whether you're a curious consumer or an industry professional, this guide will provide you with everything you need to know about polystyrene.
1. What is PS Plastic?
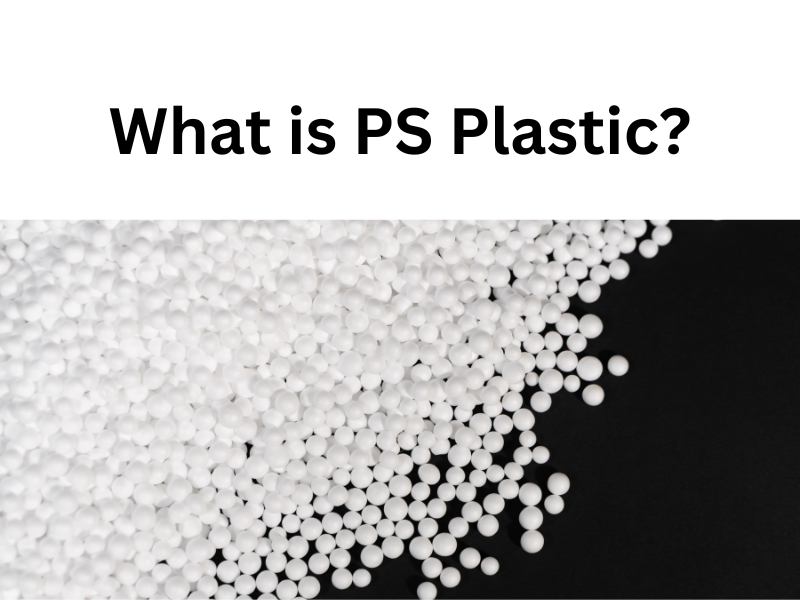
Polystyrene, commonly abbreviated as PS, is a versatile and widely-used plastic polymer known for its unique properties. It falls under the category of thermoplastic polymers, which means it can be melted and reformed multiple times without undergoing significant degradation.
What is the monomer for polystyrene? PS plastic is a synthetic polymer made from styrene monomers through a process called polymerization.
PS plastic can be found in two main types of polystyrene: expandable polystyrene (EPS) and extruded polystyrene (XPS).
- EPS, commonly recognized as Styrofoam, is characterized by its cellular structure, making it an excellent choice for packaging, insulation, and disposable food containers. It provides exceptional thermal insulation and cushioning, making it a staple in the packaging industry.
- XPS, on the other hand, boasts a more uniform, dense structure, lending itself to applications such as thermal insulation in construction, as well as packaging for delicate items. Its water resistance and durability make it an optimal choice for applications requiring prolonged exposure to moisture.
The versatility of PS plastic, coupled with its affordability, has led to its widespread use in various industries. However, concerns have been raised about its environmental impact, particularly its resistance to decomposition. As we delve deeper into the world of polystyrene, we'll explore both its advantages and its potential drawbacks.
2. How is Polystyrene Made
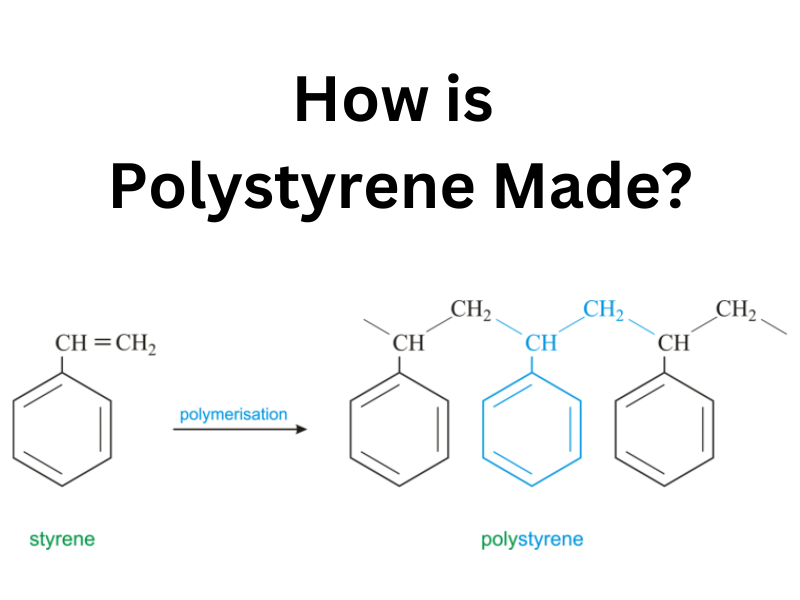
So how is polystyrene made? The production of polystyrene involves a multi-step process known as polymerization. It begins with the extraction of styrene, a petroleum-derived liquid hydrocarbon, which serves as the primary building block for PS plastic.
- Styrene Production: Styrene is obtained through the distillation of crude oil or natural gas. It is then subjected to various refining processes to ensure its purity.
- Polymerization: The polymerization of styrene is carried out using either a bulk or suspension method. In the bulk process, styrene is heated and treated with a catalyst to initiate polymerization. In suspension polymerization, styrene beads are suspended in water, and a catalyst is added to facilitate the formation of polymer chains.
- Chain Growth: As the styrene molecules link together, they form long chains, resulting in the creation of polystyrene. The length of these chains can be controlled to influence the properties of the final plastic.
- Processing and Forming: Once polymerization is complete, the resulting polystyrene can be processed into various forms. It can be molded into shapes for disposable cutlery, food containers, packaging, and even insulation panels.
The manufacturing process may vary slightly depending on the desired end product, but the fundamental steps remain consistent.
3. Properties of Polystyrene
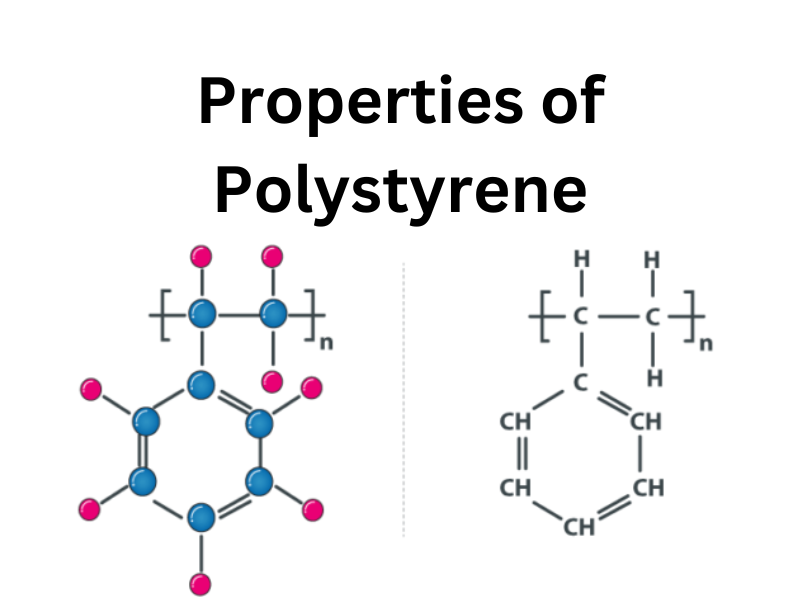
Polystyrene, represented chemically as (C8H8)n, possesses distinct properties that contribute to its widespread use in various industries.
- Molecular Weight/ Molar Mass: With a molar mass of 104.1 g/mol, polystyrene is composed of repeating units of styrene monomers. This molecular weight for polystyrene determines its overall properties.
- Density: Polystyrene exhibits a density of 1.04 g/cm³, which is relatively low compared to other plastics. This low density for polystyrene contributes to its lightweight nature, making it ideal for applications where weight is a concern.
- Solubility in Water: Polystyrene is insoluble in water due to its nonpolar nature. This property ensures its durability and resistance to moisture, which is advantageous for applications such as food packaging.
- Melting Point: The melting point of polystyrene is approximately 240°C. This high melting point allows it to retain its structural integrity at elevated temperatures, making it suitable for various industrial processes and applications.
4. Characteristics of Polystyrene: Advantages and Disadvantages
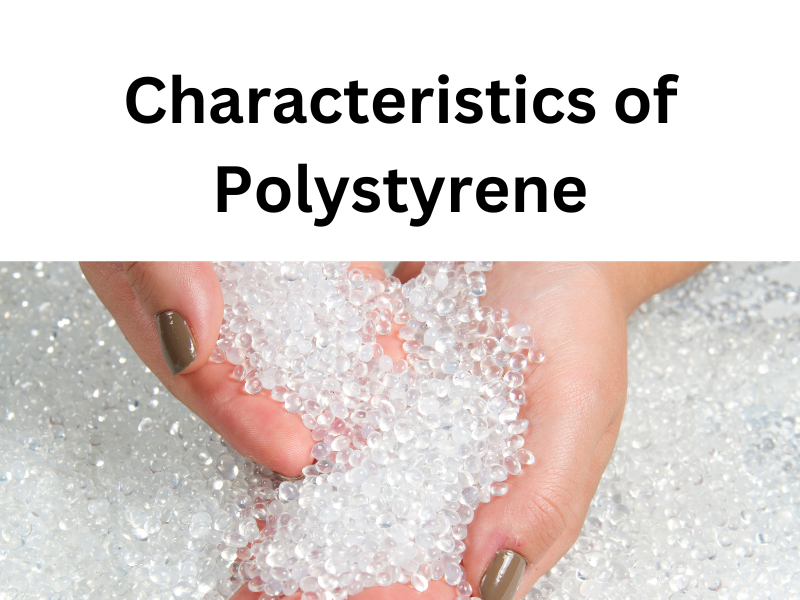
Polystyrene, with its unique properties, offers both advantages and disadvantages that shape its role in various industries.
4.1. Advantages:
- Versatility: Polystyrene's adaptability is a major advantage. It can be molded into intricate shapes or extruded into sheets, catering to diverse applications ranging from packaging to consumer goods.
- Insulation: Expanded polystyrene (EPS) and extruded polystyrene (XPS) excel in thermal insulation. Their closed-cell structure traps air, minimizing heat transfer and making them indispensable for energy-efficient construction and packaging.
- Lightweight: Polystyrene's low density translates to lightweight products, reducing transportation costs and making it suitable for industries where weight is a concern.
- Cost-Effective: The efficiency of the production process makes polystyrene an affordable choice for disposable items and packaging solutions.
- Transparency: Polystyrene can mimic glass when made transparent. Its ease of coloring enhances customization possibilities, driving its use in applications like optical lenses and electronics packaging.
4.2. Disadvantages:
- Environmental Impact: Polystyrene's resistance to decomposition poses environmental challenges. It contributes to plastic pollution, particularly in marine environments, and takes hundreds of years to break down.
- Brittleness: Polystyrene's brittleness limits its use in applications requiring high impact resistance. This drawback can be mitigated by modifying the material or combining it with other substances.
- Health Concerns: When used for food packaging, there are concerns about potential chemical leaching, particularly when in contact with hot or acidic substances.
- Non-Biodegradability: The non-biodegradable nature of polystyrene raises disposal issues, as it clogs landfills and litters landscapes.
- Energy-Intensive Production: The manufacturing process requires significant energy, contributing to its environmental footprint.
In summary, polystyrene's advantages lie in its versatility, insulation properties, lightweight nature, cost-effectiveness, and transparency. However, its disadvantages encompass environmental concerns, brittleness, potential health risks, and energy-intensive production. Striking a balance between its benefits and drawbacks calls for responsible usage, recycling efforts, and exploration of more sustainable alternatives.
At EuroPlas, we take immense pride in our role as a top-tier masterbatch manufacturer based in Vietnam. With a rich history spanning over 15 years, we have been steadfastly exporting innovative plastic solutions to more than 85 countries worldwide. Our journey has been guided by expertise, advanced facilities, and a commitment to sustainability, positioning us as a trusted partner in shaping a brighter and more eco-conscious tomorrow.
Our cutting-edge technology and unique natural resources empower us to customize products across diverse industries, meeting the specific needs of each sector. From cost-effective options to environmentally conscious choices, EuroPlas stands as a beacon of excellence and innovation in the plastic industry.
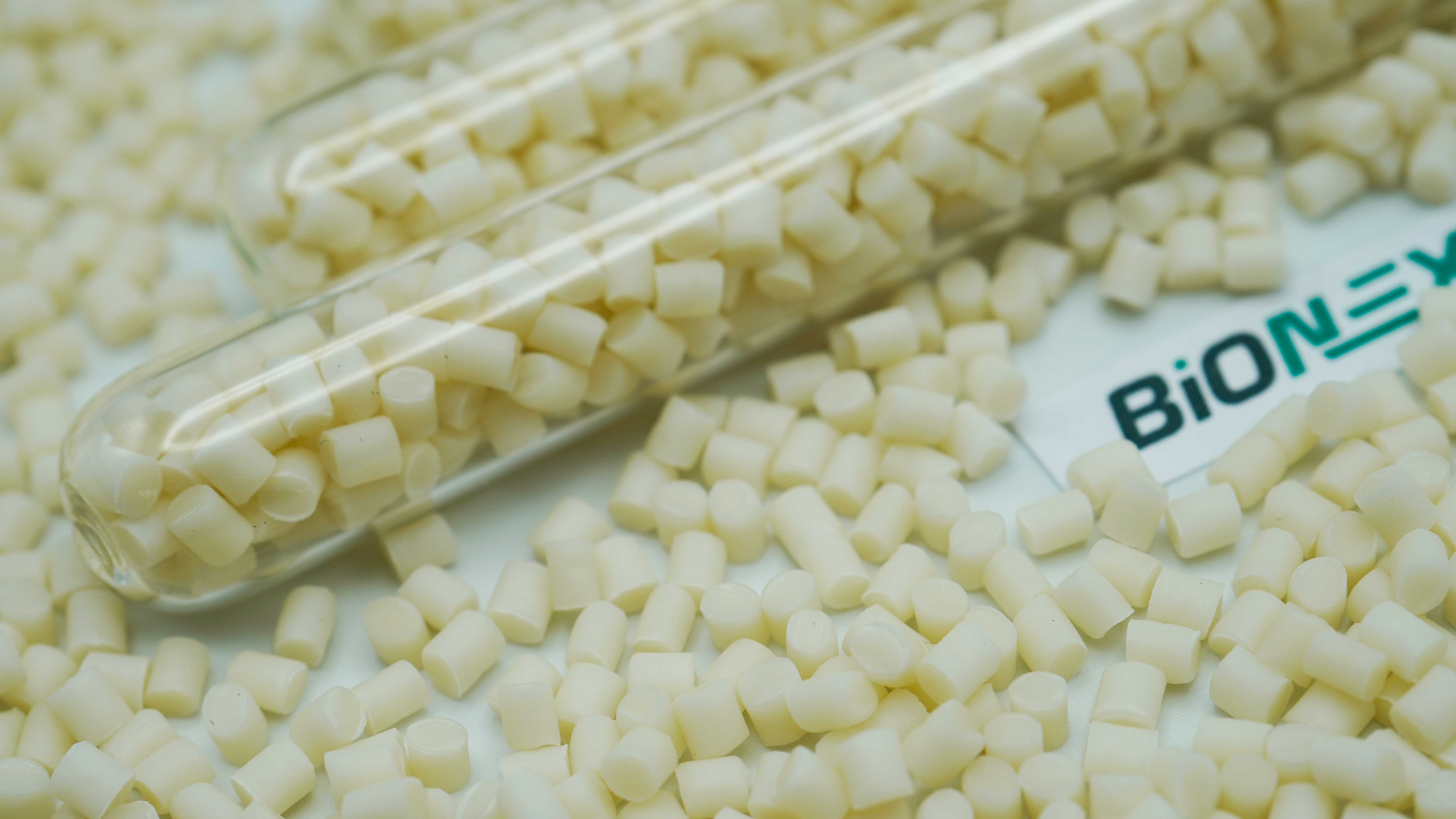
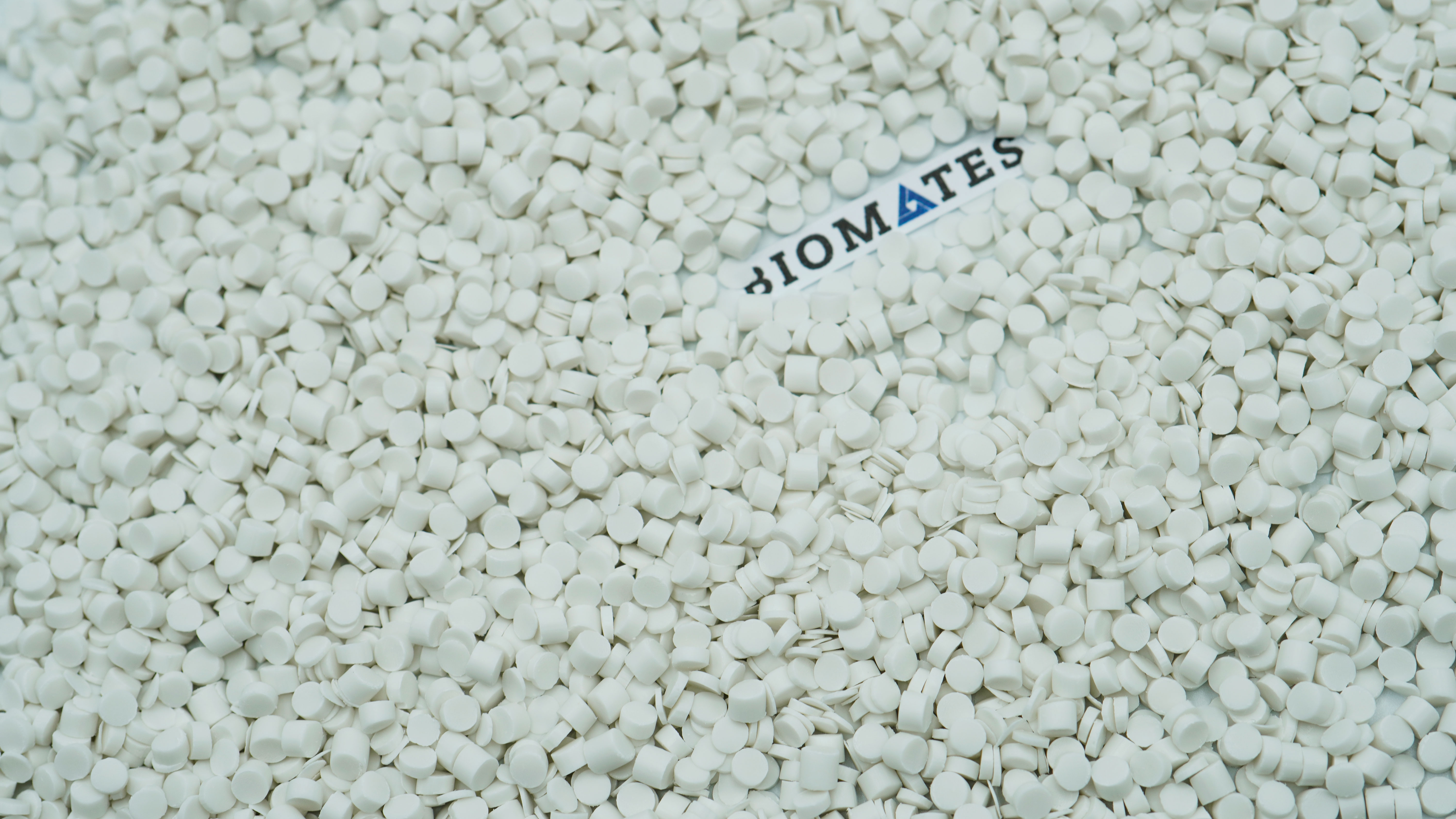
EuroPlas takes a bold step towards a greener future with our bioplastic compound. Crafted from natural starch and biodegradable additives, this unique solution not only enables plastic items to biodegrade within a year but also maintains optimal performance. With applications spanning food packaging, agricultural films, and more, our bioplastic compound is a testament to our dedication to environmental sustainability.
Our commitment to sustainability continues with the bio filler - an eco-friendly alternative that renders plastic items biodegradable within a year. Comprising natural starch and biodegradable additives, this innovative product finds its purpose in food packaging, disposable tableware, and agricultural films, contributing to a greener future without compromising functionality.
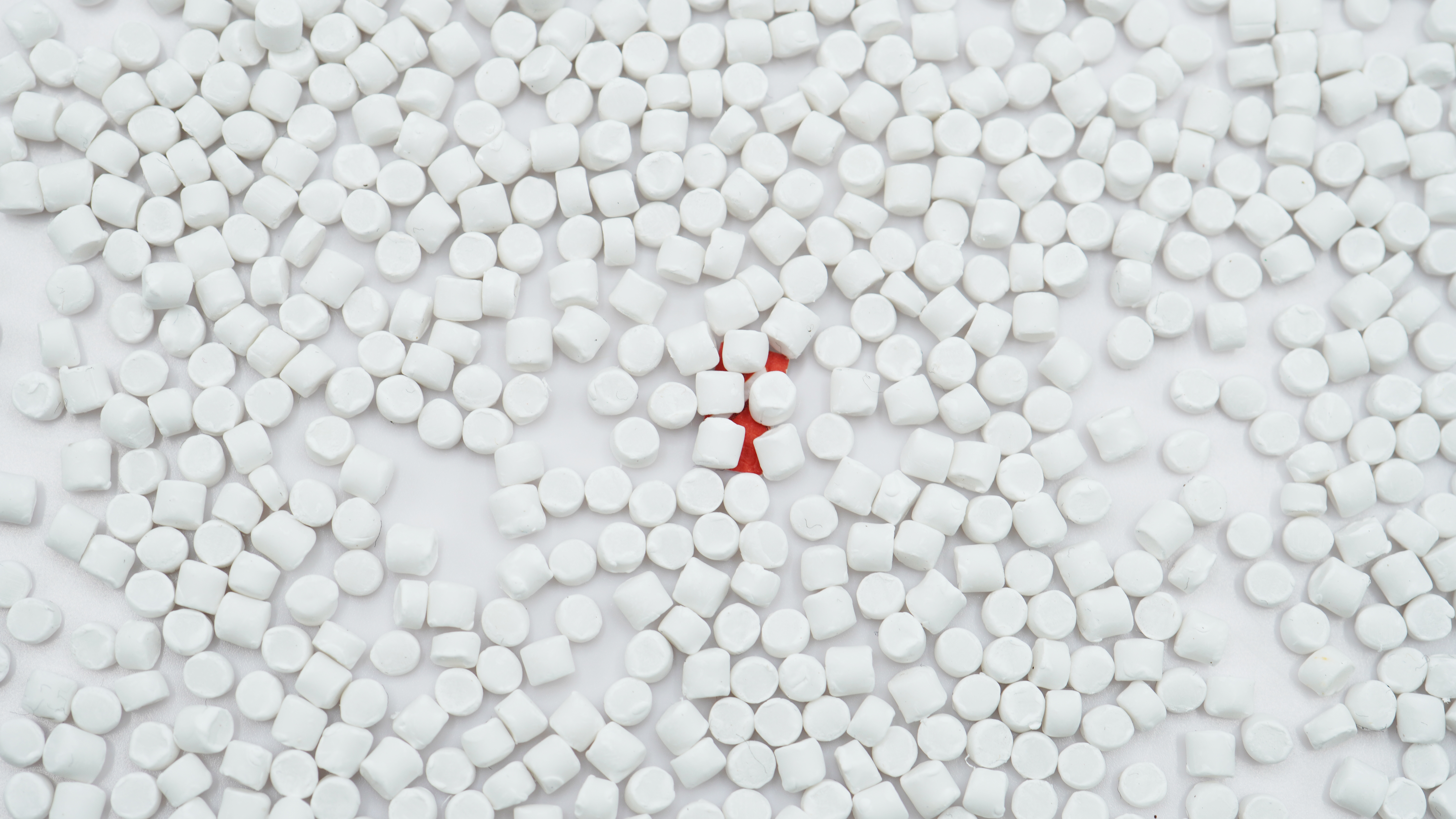
EuroPlas' game-changing filler masterbatch is designed to reduce production costs while enhancing the properties of plastic products. By incorporating filler materials like calcium carbonate or talc, this solution improves stiffness, heat resistance, opacity, and printability. With applications in various industries such as blowing films, injection molding, extrusion, and thermoforming, our filler masterbatch plays a vital role in optimizing plastic production.
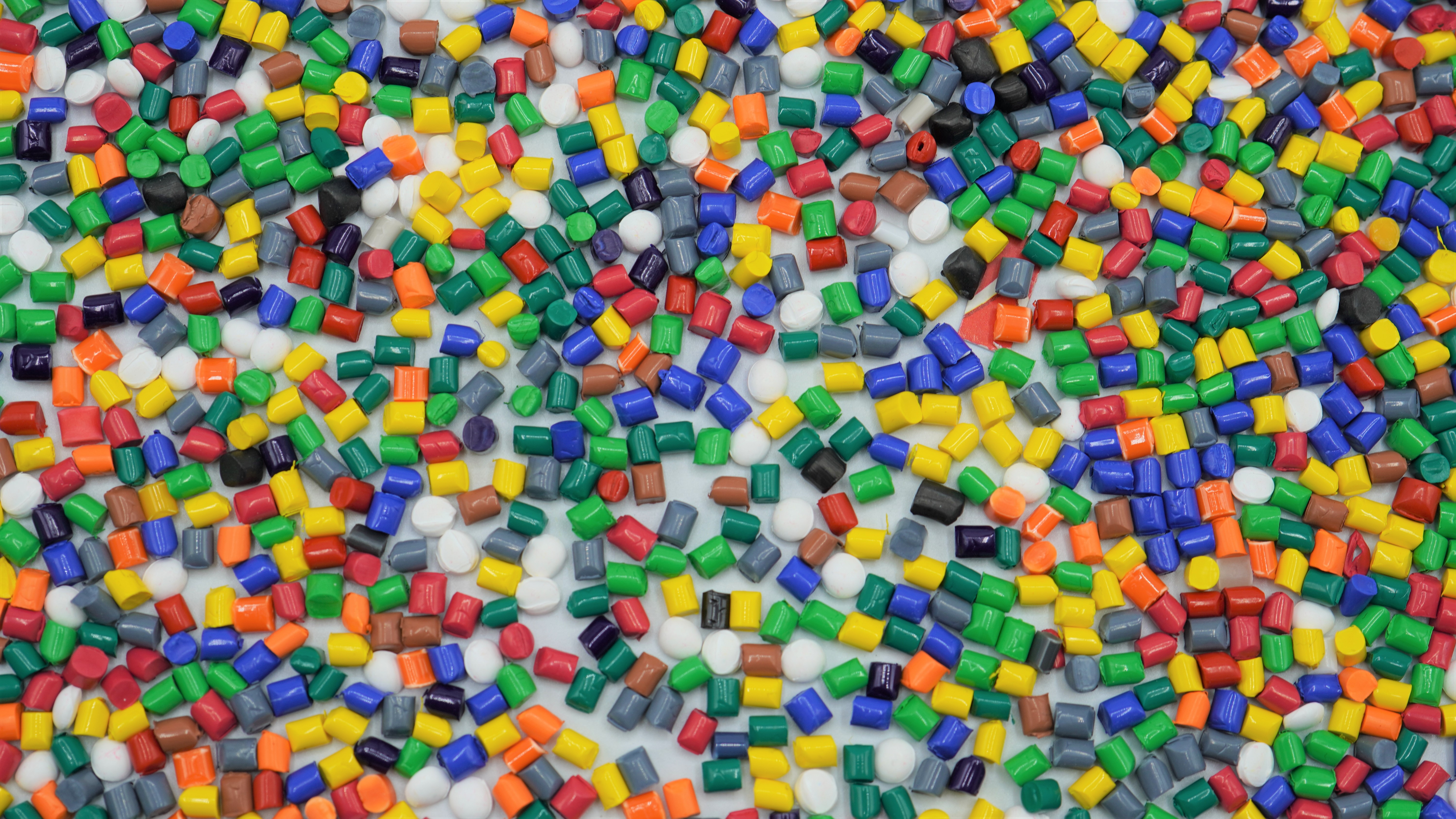
We understand the importance of aesthetics, and EuroPlas' color masterbatch delivers precise and consistent colors for a wide range of products, from toys to household appliances and cosmetics. Blended with high-quality pigments and additives, our color masterbatch ensures vibrant and appealing designs that resonate with market demands.
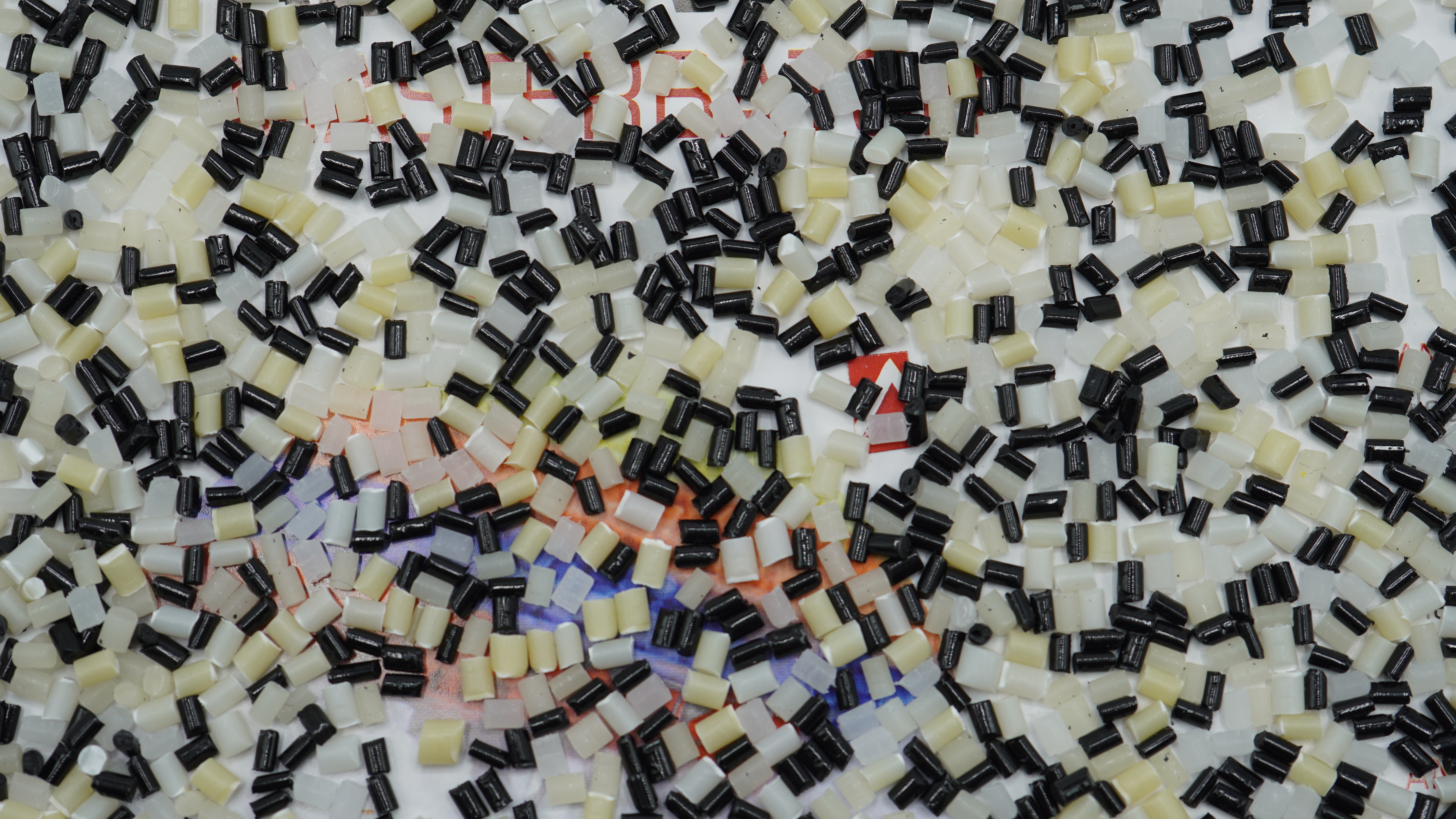
Our comprehensive range of plastic additives serves as a cornerstone in enhancing production efficiency and product functionality across industries. From slip agents to anti-block, anti-static, anti-oxidants, and UV stabilizers, EuroPlas' additives elevate the performance and longevity of plastic products while contributing to waste reduction and sustainability.
.jpg)
For those seeking high-performance solutions, EuroPlas offers engineering plastic compounds that combine engineering resins with various additives. This synergy enhances mechanical, thermal, electrical, optical, and chemical properties, catering to industries like automotive, electronics, and medical devices. Our engineering plastic compounds adhere to stringent industry standards and surpass competitors, exemplifying our dedication to excellence.
At EuroPlas, our diverse product offerings underscore our commitment to creating a more sustainable and innovative future. With a focus on quality, performance, and environmental consciousness, we continue to make a meaningful impact on the global plastic industry.
Thank you for considering EuroPlas as your partner for cutting-edge plastic solutions. Our dedicated team is ready to provide expert guidance and support to meet your unique requirements. Whether you have inquiries about our products, need customized solutions, or want to collaborate on sustainable initiatives, we are here to assist you so contact us now!