BOPP plastic film, or Biaxially Oriented Polypropylene film, is a versatile and widely used material in a variety of industries. From food packaging to product labeling, BOPP film is known for its strength, transparency, and durability. In this article, we will examine the concept of BOPP film, its characteristics, and the process of manufacturing.
Related:
- Understanding EVOH plastic food packaging
- 3 layer blown film extrusion process
- What was bubble wrap invented for?
- What are Laminating Pouches Made of?
- BIO filler masterbatch – effective solution for mulching film production
-(1).jpg)
BOPP film is a versatile and widely used material in a variety of industries.
1. What is BOPP film?
1.1. Definition
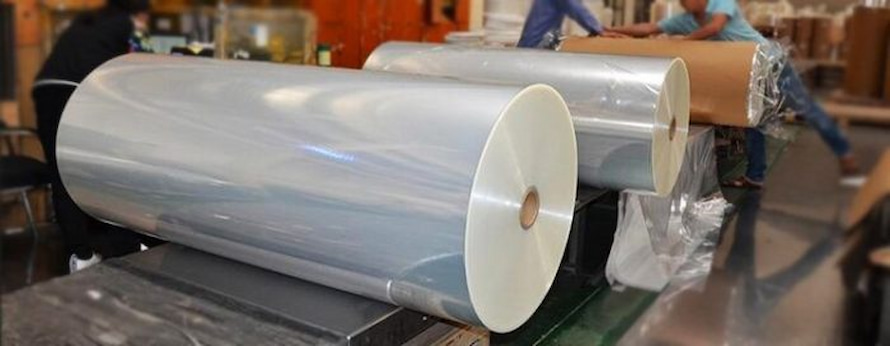
What is BOPP film?
BOPP (Biaxially-Oriented Polypropylene) film is a type of plastic film that has a wide range of applications in the packaging, labeling, and laminating industries. It is produced by extruding polypropylene resin into a thin film and then stretching the film in two perpendicular directions, known as biaxial orientation. This process enhances the strength and durability of the film, making it resistant to tearing, puncturing, and other forms of damage.
BOPP plastic films are the substrate of choice for food packaging all over the world due to the inherent moisture barrier properties, seal ability, high clarity and graphic reproduction, and shelf appeal that they provide, as well as the best possibility of the pack having a monolayer or homogeneous structure.
It is most often used as a co-extruded heat-sealable reverse-printed film for the purpose of food packaging. In the field of labeling, it is favored because of the benefits it offers in terms of yield (the lowest density of 0.55 for the IML orange peel effect), as well as its recyclability with PP containers and other materials. BOPP Films are in high demand all over the world, which is mostly due to the growth of the flexible packaging sector.
1.2. Benefits of using BOPP plastic film
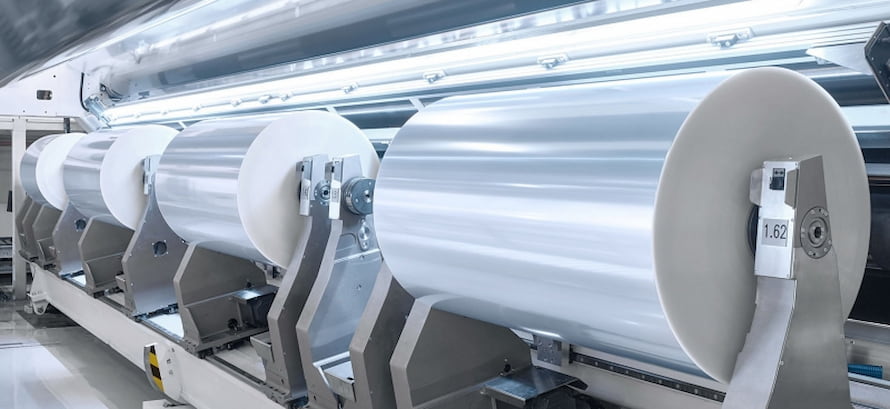
Benefits of using BOPP plastic film
BOPP plastic film become a common type of plastic film used in a wide range of packaging, labeling, and laminating applications due to its numerous benefits. The following are some of the key advantages of using BOPP matt film:
Shelf life extension
The BOPP film offers the best moisture barrier of all the regularly used plastic films, and its metalized version offers the best oxygen barrier to the goods. These two characteristics of BOPP films are crucial for food packaging because they increase product shelf life and decrease food waste.
High clarity
BOPP film has excellent transparency, which makes it an ideal material for packaging applications where the visibility of the product is important. This clarity allows customers to see the product clearly, helping to increase sales and improve the overall aesthetic appeal of the packaging.
Product quality
Due to its limited gauge spread, BOPP film offers constant and exceptional seal integrity in addition to its barrier capabilities. The food packaging business also benefits from strong heat seal strength, reduced seal initiation temperature, a wide sealing window, and superior machinability.
Aesthetic/Graphics
Clear BOPP films' excellent transparency makes it possible to provide product packaging with a high degree of visual appeal. In this film, half-tone printing tasks with multicolor printing may be easily completed for high-quality graphics. Excellent gloss, great opacity, and exceptional whiteness in the white opaque film type provide product packaging with an appealing appearance.
The superb metallic look of the metalized film variant makes your goods stand out on the shelf. The ability to do post-lamination procedures like foil stamping, UV spot coating, and embossing to improve the visual appeal of product packaging is made possible by the material's high surface tension.
Versatility
BOPP film can be easily converted into bags, pouches, laminates, and other forms of packaging, which makes it a cost-effective and efficient solution for many packaging needs. Its versatility allows manufacturers to tailor the packaging to the specific needs of their product, whether it be for presentation, protection, or both.
Density
In comparison to all other regularly used flexible packaging films, BOPP films have a special quality. Low density promotes the idea of using less plastic per product by increasing yield during conversion. Low density leads to lighter rolls that are easier to handle since they weigh less per roll than other plastic films of the same length.
Sustainability
Is BOPP film recyclable? In comparison to other plastic film substrates like polyester, BOPP film has a comparatively low carbon footprint. Due to its eco-friendliness in flexible food packaging, BOPP Film is the second most favored substrate after cellulose film. Low melting point materials need less energy to change from one form to another. Reprocessed BOPP resin granules are often used to create injection molded components, furniture such as chairs and tables, and other home products like seat mats.
Cost-effectiveness
BOPP film is an economical choice for packaging and labeling, as it is readily available, easy to convert, and has a low cost per square foot compared to other materials. This cost-effectiveness makes it an attractive option for companies that are looking to reduce costs while still providing quality packaging for their products.
2. What is BOPP film used for?
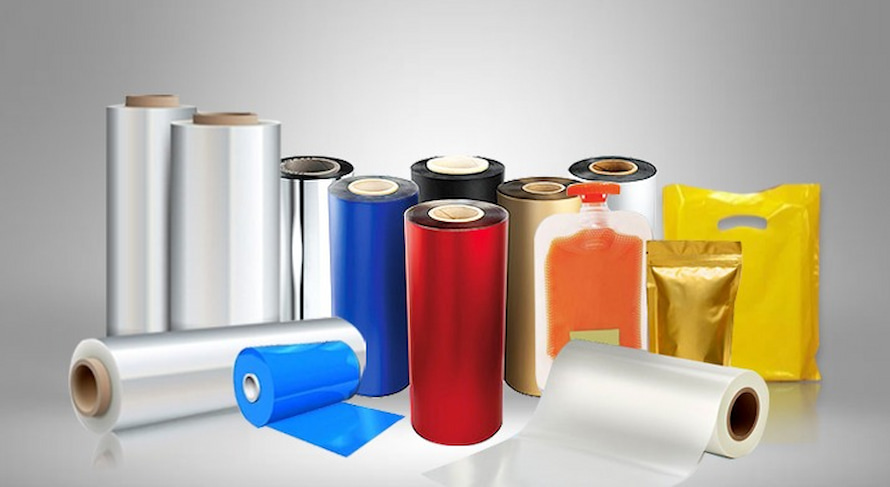
What is BOPP film used for?
BOPP film is a highly versatile material that has a wide range of applications across many different industries. Some of the key applications of BOPP film include:
Food & Beverage Packaging
BOPP film is widely used in the packaging of food and beverage products due to its high strength and durability, as well as its moisture resistance. BOPP film can be used to create a variety of different types of packaging, including stand-up pouches, vacuum pouches, and side gusseted bags. These types of packaging help to protect food and beverage products from damage during transportation and storage.
Labeling and Branding
BOPP film's high transparency and clarity help this kind of film effective for labeling. Its smooth surface also makes it easy to print on, which allows for the creation of eye-catching and informative labels that can help to build brand recognition and customer loyalty.
Laminating
BOPP film can be used to laminate a variety of different materials, including paper, cardboard, aluminum foil, and print materials. BOPP film helps enhance the strength and durability of the materials it is laminated to, hence, becoming one of the most suitable choices for applications such as brochures, posters, and other print materials.
Tamper Evident Films
BOPP film is used in the production of tamper-evident films, which are used to secure products and prevent unauthorized access. These films are often used in the packaging of products that need to be protected from tampering, such as pharmaceuticals, electronic components, and other similar items. This helps to ensure that the products remain secure and protected, while also providing a measure of consumer protection and confidence.
Personal Care Product Packaging
BOPP film is also used in the packaging of personal care products, such as cosmetics, shampoos, and other similar items. Its high strength, durability, and moisture resistance make it an ideal choice for packaging products that need to be protected from damage and maintain their quality. BOPP film can also be used to create attractive and eye-catching packaging that helps to build brand recognition and customer loyalty.
Medical Packaging
BOPP film is also used in the packaging of medical products and devices due to its strength, durability, and transparency. BOPP film can be used to create a variety of different types of medical packaging, including bags, pouches, and blister packs. These types of packaging help to protect medical products and devices from damage, while also allowing for easy identification of the contents.
Adhesive Tape
BOPP film is often used to make various types of adhesive tape, including packaging tape and Scotch tape. Its strength and resistance to tearing make it an ideal choice for applications where a strong and reliable tape is required.
Agricultural Films
BOPP film is used in the production of agricultural films, such as greenhouse covers and mulch films. Its high transparency allows light to penetrate, while its resistance to weathering helps to protect crops from the elements.
3. How is BOPP plastic film made?
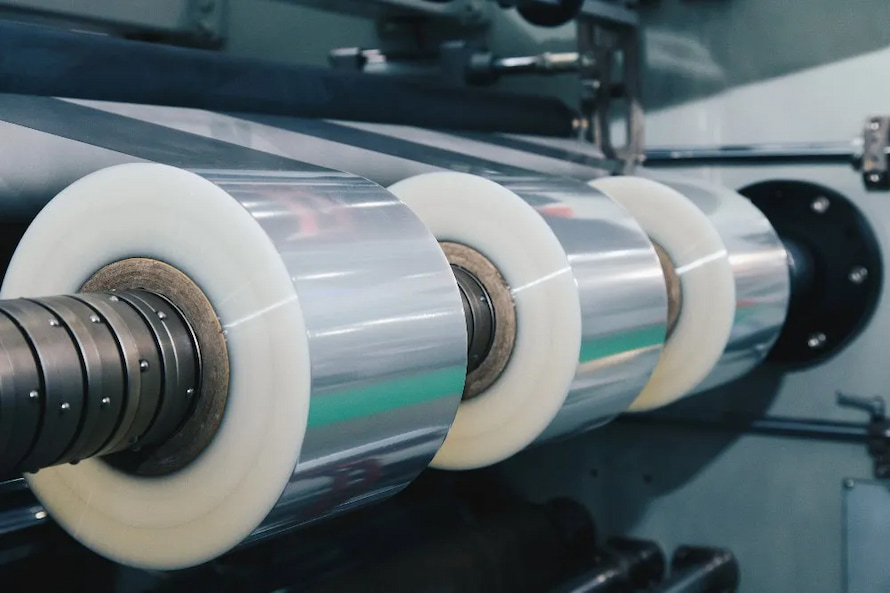
How is BOPP plastic film made?
In the flexible packaging sector, BOPP (Biaxially-Oriented Polypropylene) film has been utilized for many years. It is well regarded for its affordable price, superior optical and mechanical features, and exceptional gas barrier qualities (particularly water vapor).
Below is a detailed demonstration of the BOPP film manufacturing process:
Step 1. Raw material feeding system
Isotactic Polypropylene, a semi-crystalline, thermoplastic polymer, serves as the primary raw material in the center layer. While ethylene-propylene copolymers and/or ethylene-butane-propylene copolymers are used for the outer layers. A hopper system is used to introduce these ingredients into the extruders.
Step 2. Extrusion
The materials are melted and heated to 200–230°C within the extruders before being fed into the extrusion head, where they emerge as a foil.
Step 3. The foil cooling
The foil is then brought into direct contact with a cylinder that has been chilled before being submerged in a water bath to cool the melt.
Step 4. Machine direction orientation (MDO)
The film is subsequently passed over many rollers, which raise the temperature and prepare the film for longitudinal stretching (machine direction). By moving the foil between the rollers that spin at increasing rates, stretching is accomplished. The polymer chains are aligned at this point after the foil has typically been stretched up to five times its original length. The mechanical qualities of the film may be improved at this step, and the thickness can be cut by up to five times.
The film is heated again after stretching to remove the tension created during stretching (annealing phase).
Step 5. Transverse direction orientation (TDO)
A quick-moving chain of metal jaws grabs the film on both edges once it exits the longitudinal stretching zone (tenter clips). The film is stretched transversely by the diverging rails after being heated up in an oven in the middle (i.e. stretching in the transverse direction up to 9 times its original width).
The macromolecules align at this point, but this time in a transverse orientation, improving the mechanical characteristics of the film and reducing its thickness by up to 9 times. After stretching, the chain and the film converge, allowing the film to balance off the tension that built up during stretching (annealing phase).
Step 6. Thickness measurement and flame treatment
The film enters a new processing step at which point the thickness is automatically measured (along the entire width). After that, one of the faces is given a flame or corona treatment to prepare the film for the subsequent conversion processes, specifically to change the surface that will serve as an anchor for materials like ink (for printing), glue (for laminating), or metal (metallization process).
Step 7. Reel winding
After being wound around a reel, the film is then sliced to the specific measurements.
Step 8. Film measurements
The following are the primary metrics that the final product is subject to:
- Density, grammage, and thickness
- Elastic modulus, elongation at break, and tensile strength
- Haze (opacity) and Gloss (sparkling appearance)
- The friction coefficient between films and between films and metals
- Sealing strength and threshold °C
- Temperature stability (heat shrinkage)
The film has at least three layers and a thickness between 15 and 60 microns; the center layer is the thickest and primarily responsible for the mechanical qualities, while the two outer layers provide the film with different characteristics (i.e. heat-sealing properties).
In order to completely fulfill the application criteria, additives may be added, depending on the ultimate application the film is intended for.
4. BOPP film raw material
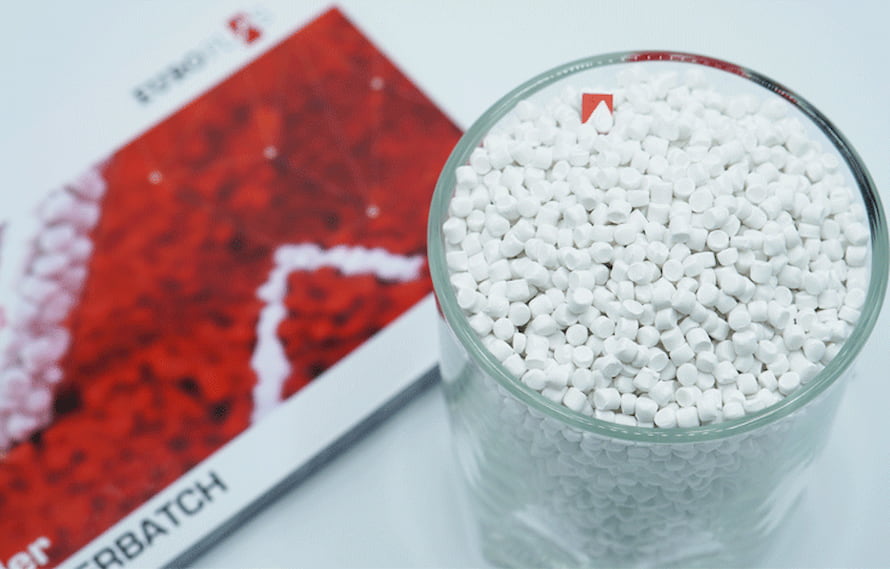
BOPP film is produced from PP (Polypropylene) plastic resins.
BOPP (Biaxially-Oriented Polypropylene) film is produced from PP (Polypropylene) plastic resins. This type of plastic is harder than PE and is considered to have the general characteristics of good tensile strength, and higher transparency than other kinds of plastic. Besides, BOPP film is also known as a thin film, with a thickness of 10 ~ 40 microns. It is due to the low density of PP particles, only 0.90 g/m3.
Currently, EuroPlas is proud to be the world's No. 1 filler masterbatch manufacturer, proudly bringing customers unique plastic raw material solutions to help their factories optimize production costs and improve the competitiveness on the market. PP filler masterbatch brand EuroPlas is a combination of CaCO3 stone powder, PP base resin, and appropriate additives.
EuroPlas's PP filler masterbatch for BOPP plastic film manufacturing is committed to helping customers:
- Optimize production costs
- Improve some surface features of finished products: increasing hardness, reducing shrinkage,...
- Save fuel thanks to the good thermal conductivity of CaCO3
- Reduce mold cooling time, shorten the production cycle
If you are looking for a high-quality PP filler masterbatch for BOPP plastic film manufacturing, do not hesitate to contact us for the earliest advice and support.