Plastic materials are widely used in various industries thanks to their versatility and durability. Among the different types of plastics, polyethylene (PE) is one of the most common materials. PE plastic is a thermoplastic polymer that is composed of ethylene monomers. It is known for its excellent combination of properties, making it suitable for various applications. This article will help you thoroughly understand PE plastic properties, types, and applications.
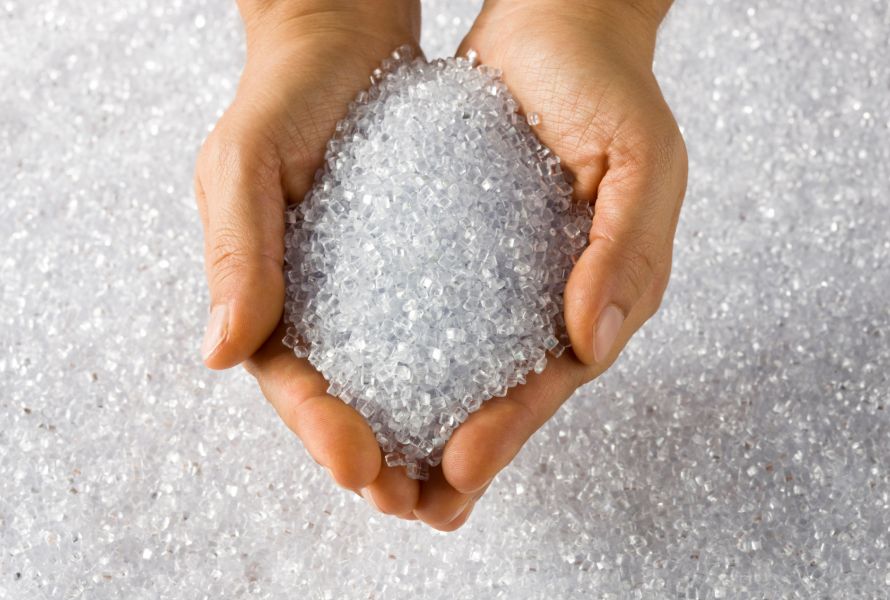
Polyethylene is one of the most common materials in the plastic industry
1. What is PE plastic material?
Polyethylene, or polythene (abbreviated PE), is a synthetic resin derived from ethylene polymerization. This versatile material belongs to the renowned group of polyolefin resins and holds significant importance in the plastic industry.
Ethylene (C2H4) is a gaseous hydrocarbon commonly generated through the cracking process of ethane, a significant component of natural gas. Ethylene molecules consist primarily of two methylene units (CH2) connected by a double bond between the carbon atoms, represented by the chemical formula CH2=CH2.
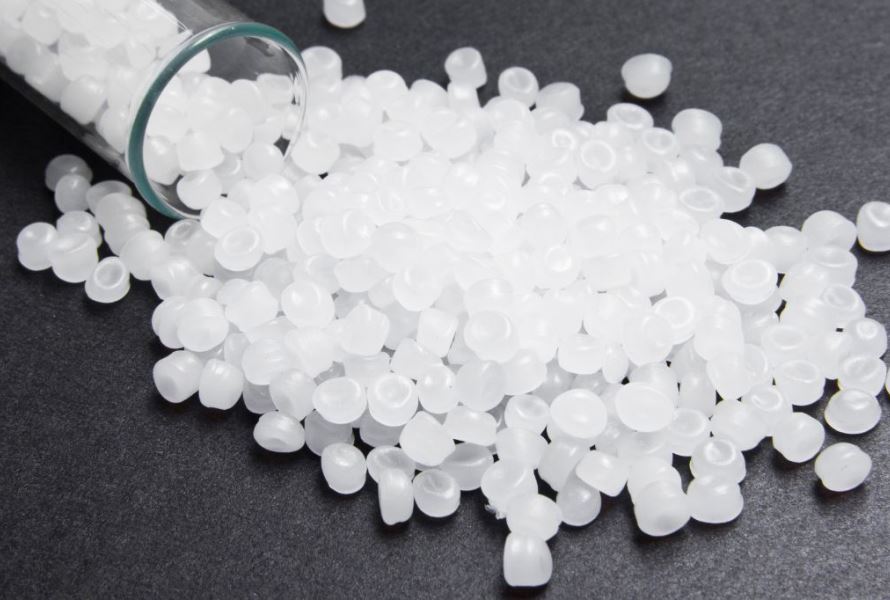
PE plastic is a synthetic resin derived from ethylene polymerization
When exposed to polymerization catalysts, the double bond can be broken, allowing the resulting additional single bond to link with a carbon atom in another ethylene molecule. This process forms the repeating unit of a large polymeric molecule. This uncomplicated structure, replicated numerous times within a single molecule, holds the key to the distinctive properties of polyethylene.
PE plastic is one of the most common materials in the world. Polyethylene uses include transparent food wraps, shopping bags, detergent bottles, and automotive fuel tanks. Furthermore, it can be easily transformed into synthetic fibers through slitting or spinning processes. Alternatively, with suitable modifications, polyethylene can acquire elastic characteristics akin to rubber.
2. Main properties of polyethylene (PE) plastic
2.1 Polyethylene density
PE plastic is available in different density variations, including:
- Low-density polyethylene (LDPE): ranging between 0.910 and 0.940 g/cm3
- Linear low-density polyethylene (LLDPE): ranging between 0.910 and 0.920 g/cm3
- Medium-density polyethylene (MDPE): ranging between 0.926 and 0.940 g/cm3
- High-density polyethylene (HDPE): ranging between 0.941 and 0.967 g/cm3
- Ultra-High Molecular Weight Polyethylene (UHMWPE): ranging between 0.931 and 0.949 g/cm3
(Source: Polyolefin Fibres)
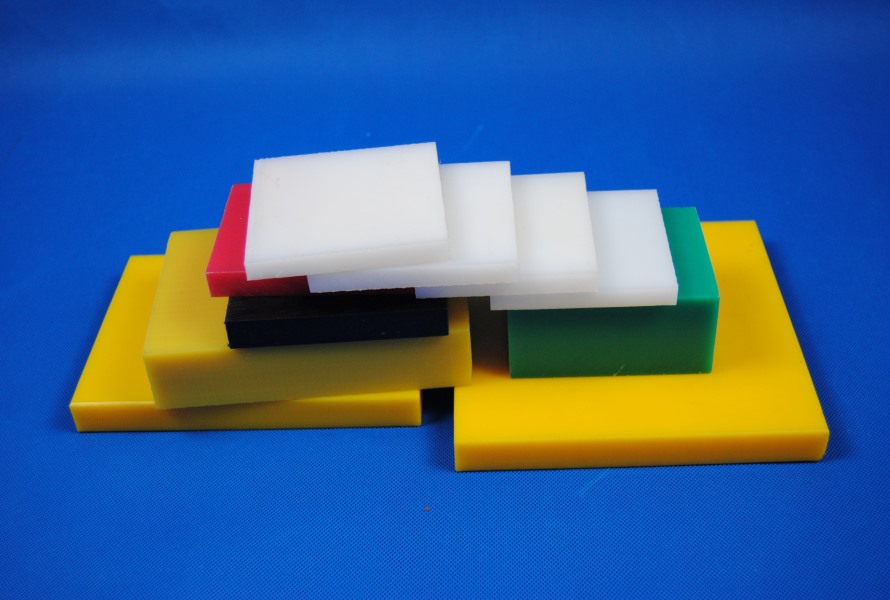
There are many variations of PE plastic density
2.2 Polyethylene molecular weight
Because of the diversity of polymeric structures at the molecular level, the molecular mass of polyethylene also varies depending on which type of PE plastic, such as 300000 - 9.20e+6 g/mol for HDPE and 3.5 and 7.5 million amu for UHMWPE.
The molecular weight of polyethylene material plays a crucial role in determining its physical and mechanical characteristics. PE with higher molecular weight generally exhibits improved strength, toughness, and impact resistance.
2.3 Polyethylene chemical compatibility
Polyethylene exhibits excellent resistance to chemicals, including acids, bases, and solvents. This material is composed of nonpolar, saturated hydrocarbons with high molecular weight. As a result, its chemical behavior closely resembles that of paraffin.
Due to their symmetrical molecular structure, they tend to form crystals, making polyethylene partially crystalline. Increased crystallinity leads to higher density of polyethylene as well as improves polyethylene chemical resistance and properties. Crystalline polyethylene samples do not dissolve at room temperature.
However, polyethylene is prone to be affected by certain chemicals, which can lead to stress cracking, swelling, oxidation, or the penetration of the material. These chemical interactions can potentially diminish the overall physical characteristics of polyethylene.
Polyethylene (excluding cross-linked polyethylene) can be dissolved at higher temperatures using aromatic hydrocarbons like toluene, xylene or chlorinated solvents such as trichloroethane or trichlorobenzene.
2.4 Polyethylene glass transition temperature
PE plastic has a relatively low glass transition temperature compared to other thermoplastics. It remains flexible and durable even at low temperatures. It is important to note that these melting temperatures can vary significantly depending on the specific type of polyethylene.
In the case of medium- and high-density polyethylene commonly used in commercial applications, the melting point typically is about 130.8 °C. Average commercial low-density polyethylene melts from 105 to 115 °C (221 to 239 °F).
However, the uppermost theoretical limit for the melting point of polyethylene is reported to be approximately 144 to 146 °C (291 to 295 °F). Combustion of polyethylene generally occurs at temperatures above 349 °C (660 °F).
2.5 Polyethylene food safe
Numerous types of PE material have obtained approval from the FDA for their suitability in contact with food. These plastics are commonly used in packaging for food, beverages, and medicines; you probably already have them in your household.
HDPE is the most prevalent plastic found in households. It is used to produce beverage bottles, butter containers, liners for cereal boxes, and sturdy food storage buckets.
LDPE shares similarities with HDPE but possesses greater flexibility, making it ideal for applications such as squeeze bottles, plastic films, and six-pack rings. It exhibits resistance to chemicals, repels microorganisms, and does not release harmful toxins when used to store food at various temperatures. However, LDPE is not considered safe for food in its recycled form.
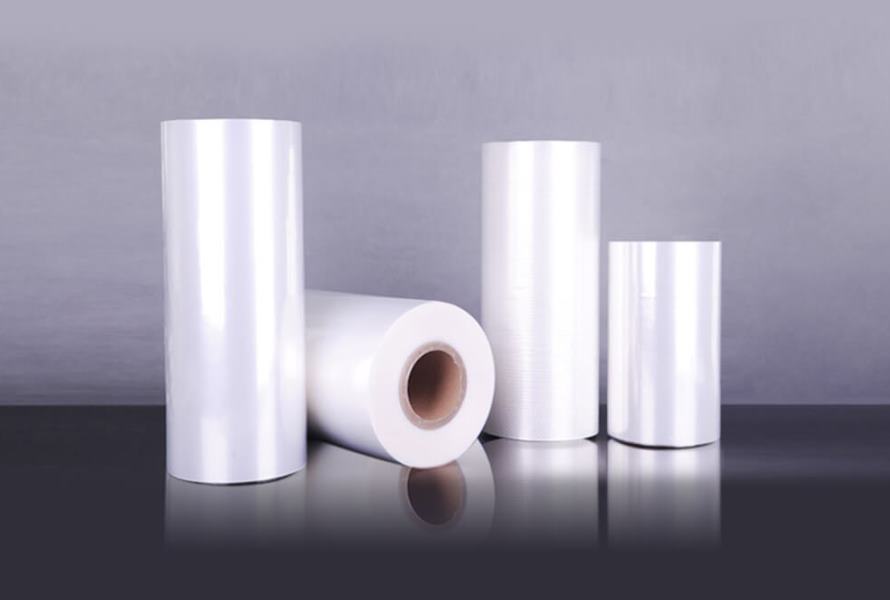
Numerous types of polyethylene have obtained approval from the FDA for food safety
2.6 Polyethylene uv resistance
Is polyethylene UV-resistant? When exposed to sunlight, polyethylene material can become brittle. Carbon black is commonly used as a UV stabilizer to solve this drawback.
However, it's important to note that the extent of UV resistance can vary depending on various factors, such as the specific grade of polyethylene, processing conditions, additives, and environmental factors.
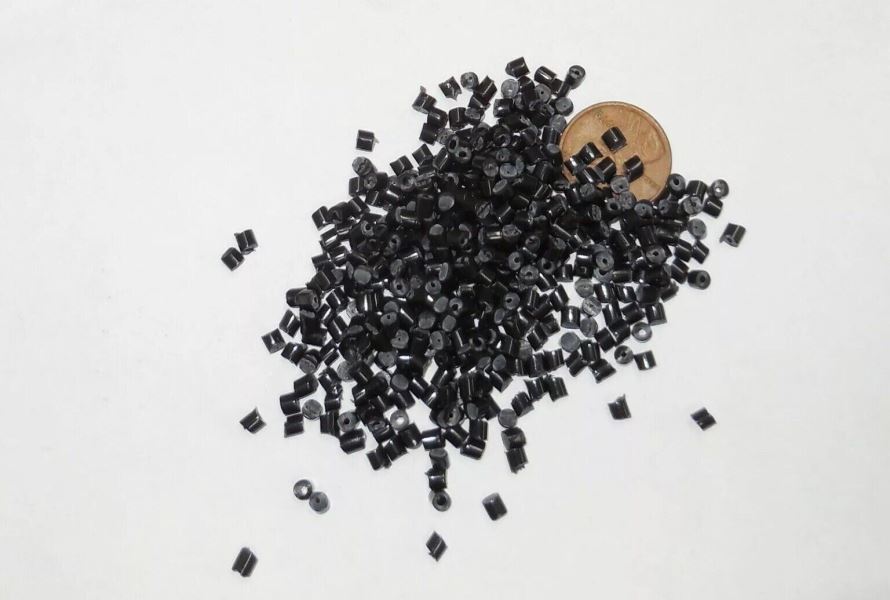
Polyethylene can become brittle when exposed to sunlight
2.7 Polyethylene heat resistance
PE plastic can withstand high temperatures without significant deformation or degradation. It retains its mechanical properties at elevated temperatures, making it suitable for applications requiring heat resistance.
3. How many types of PE plastic?
PE plastic is available in different types based on the molecular weight and density of polyethylene. The most common types include:
3.1 Low-Density Polyethylene (LDPE)
LDPE is a type of PE plastic with a low density and high flexibility. LDPE generally has branches, each with a molecular weight of typically less than 50,000 g/mol.
With a melting point of around 110 °C (230 °F), it finds extensive application in various industries. It predominantly produces packaging films, trash and grocery bags, agricultural mulch, wire and cable insulation, squeeze bottles, toys, and household items. The recycling code assigned to LDPE is #4.
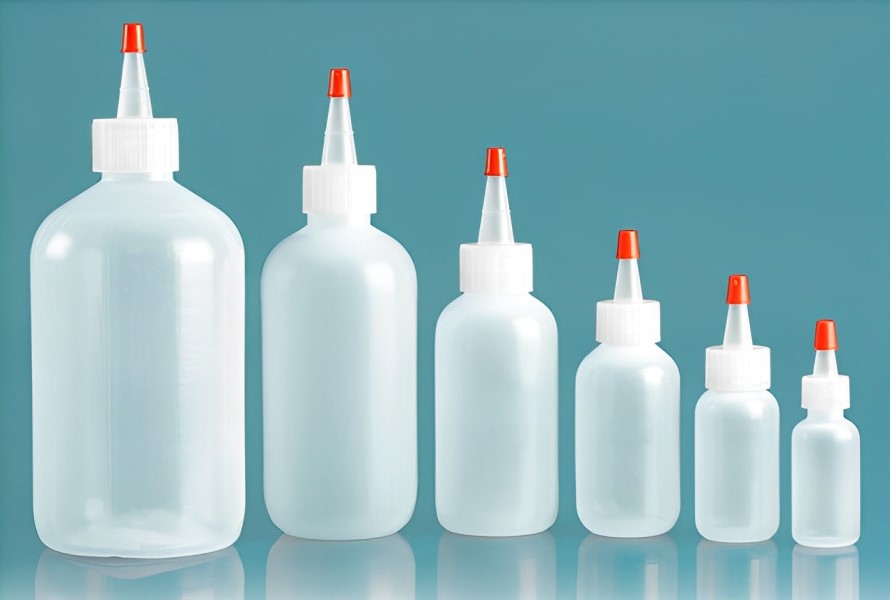
Low-Density Polyethylene bottles
3.2 Linear Low-Density Polyethylene (LLDPE)
LLDPE bears a close resemblance to LDPE in terms of its structure. It is produced through the copolymerization of ethylene with 1-butene and smaller quantities of 1-hexene and 1-octene.
LLDPE shares comparable properties with LDPE. Notably, LLDPE offers several advantages, such as lower energy requirements during the polymerization process and the ability to modify the polymer's characteristics by adjusting the type and quantity of its chemical constituents. The plastic recycling code assigned to LLDPE is #4.
3.3 Medium-Density Polyethylene (MDPE)
MDPE is a type of PE plastic with a medium density between HDPE and LDPE. Its density falls within the range of 0.926 to 0.940 g/cm3. This versatile material can be manufactured through various catalysts such as chromium/silica, Ziegler-Natta, or metallocene catalysts.
This type of PE exhibits excellent shock and impact resistance characteristics. Common applications for MDPE include gas pipes, fittings, sacks, shrink film, packaging film, carrier bags, and screw closures.
While MDPE displays a lower sensitivity to notches than HDPE, its stress-cracking resistance surpasses HDPE's. It possesses a softer nature compared to LDPE while still maintaining greater rigidity than LDPE.
3.4 High-Density Polyethylene (HDPE)
HDPE is a type of PE plastic with a high density and crystallinity. This material has a molecular weight of up to 200,000 g/mol.
HDPE is produced using low temperatures and pressures, resulting in a unique molecular structure without branches. This structural characteristic enables the polymer chains to pack together tightly, creating a dense and highly crystalline material with remarkable strength and moderate stiffness.
HDPE exhibits a high melting point. It can withstand frequent exposure to temperatures as high as 120 °C (250 °F), making it suitable for sterilization.
HDPE finds its application in various products, including blow-molded bottles for milk and household cleaners. Additionally, it is utilized to produce blow-extruded grocery bags, construction film, and agricultural mulch.
Moreover, injection-molded pails, caps, appliance housings, and toys are also manufactured using HDPE. HDPE is assigned the plastic recycling code number #2.
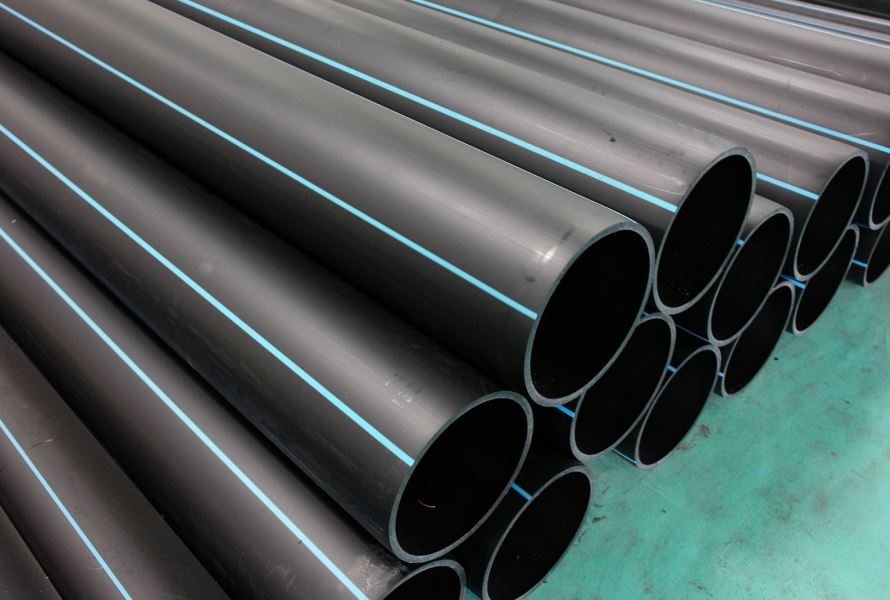
High-Density Polyethylene pipes
3.5 Ultra-High Molecular Weight Polyethylene (UHMWPE)
UHMWPE demonstrates a remarkable molecular weight range, ranging from 3,000,000 to 6,000,000 atomic units. Interestingly, this molecular weight is so remarkably high that conventional methods cannot measure it directly. Instead, it is determined through the intrinsic viscosity of the material.This particular type of polymer possesses the capability to undergo
spinning into fibers, which can subsequently be drawn or stretched to achieve a profoundly crystalline state. Consequently, the resulting material exhibits exceptional rigidity and an excellent tensile strength surpassing steels. These fibers are skillfully woven into the polyethylene fabric of bulletproof vests, rendering them highly effective in providing protection.
3.6 Cross-Linked Polyethylene (PEX)
Cross-linking refers to creating a three-dimensional network of polymer chains, which imparts enhanced stability and durability to the material. In its cross-linked form, polyethylene exhibits improved resistance to temperature extremes, pressure, impact, and chemicals compared to its non-cross-linked counterpart.
Cross-Linked Polyethylene, or PEX, is a type of PE plastic that has undergone a cross-linking process. This process enhances the properties of PEX, making it resistant to cracking, corrosion, and scaling. It also improves the material's flexibility, allowing it to be easily shaped and installed.
PEX finds extensive utilization in various industries, primarily encompassing building services pipework systems, hydronic radiant heating and cooling systems, domestic water piping, insulation for high-tension electrical cables…PEX pipes are highly flexible and can be bent to fit around obstacles without additional fittings.
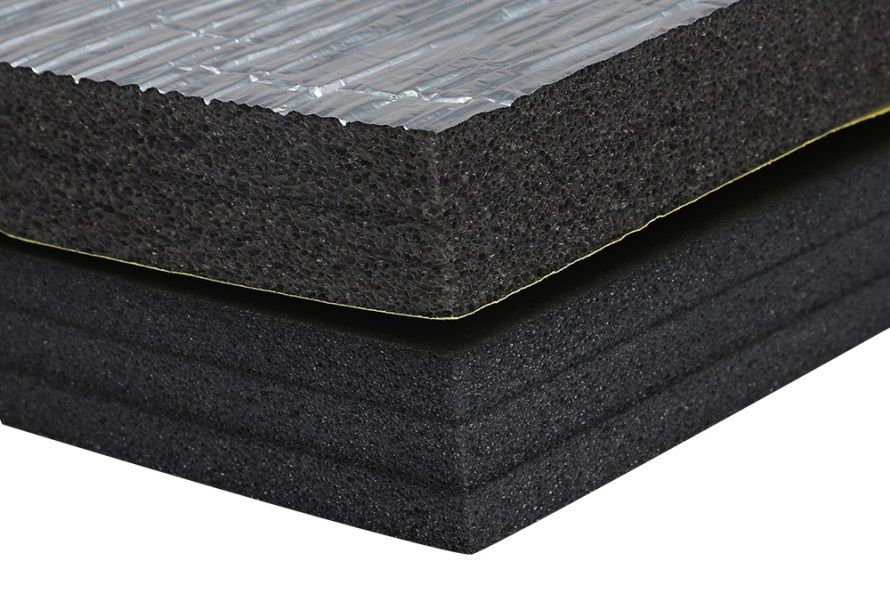
Cross-Linked Polyethylene foam sheets
4. Common uses of PE plastic
PE plastic finds widespread application across various industries. Some of the common uses of PE plastic include:
4.1 Packaging
Polyethylene material is extensively used in the packaging industry due to its excellent moisture barrier properties, lightweight, and durability. It is commonly used to produce plastic bags, shrink wraps, food containers, and bottles. The versatility of polyethylene allows it to be molded into different shapes and sizes, catering to the specific packaging needs of various products.
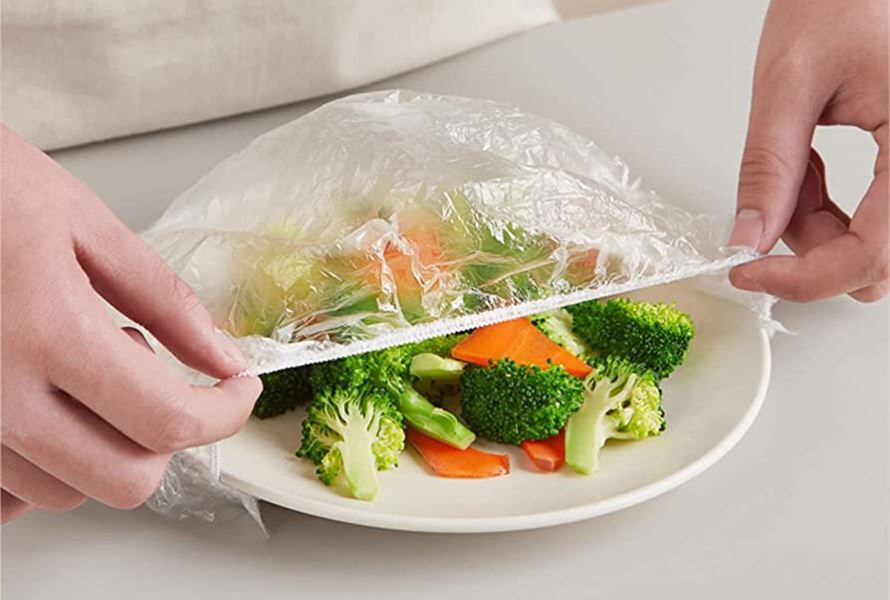
PE plastic is used to produce plastic bags, shrink wraps, food containers, and bottles
4.2 Construction
In the construction industry, polyethylene is crucial in providing insulation, waterproofing, and protection against corrosion. It is used to produce pipes, fittings, geomembranes, and roofing materials. The durability and resistance to chemicals make polyethylene a preferred choice for long-lasting construction applications. HDPE pipes, in particular, are favored for their high strength, corrosion resistance, and long service life.
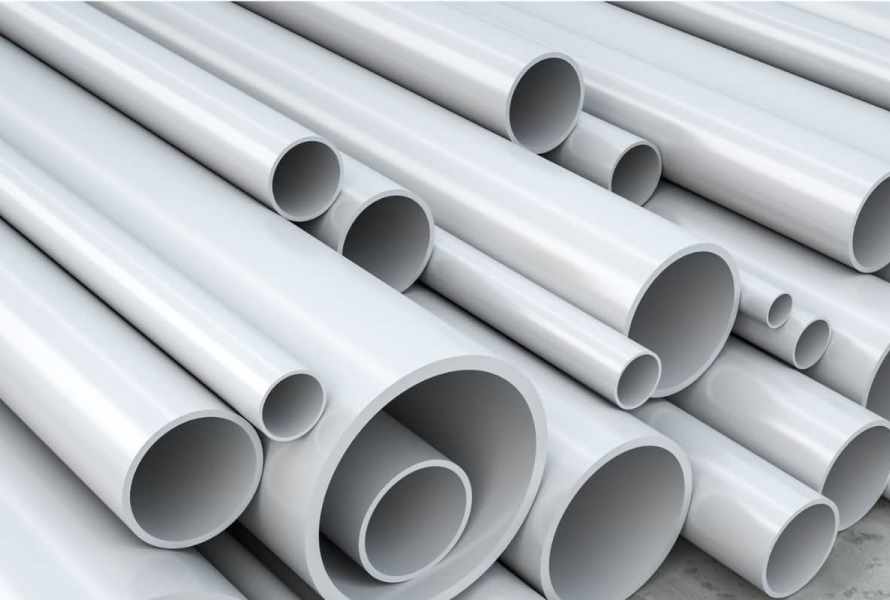
PE plastic pipes are favored for their high strength and long service life
4.3 Automobiles
PE plastic finds applications in the automotive industry for manufacturing fuel tanks, interior components, electrical connectors, and wiring harnesses. Its lightweight nature helps improve fuel efficiency, while its impact resistance ensures safety in case of accidents. Additionally, polyethylene's resistance to chemicals and environmental factors makes it suitable for various automotive applications.
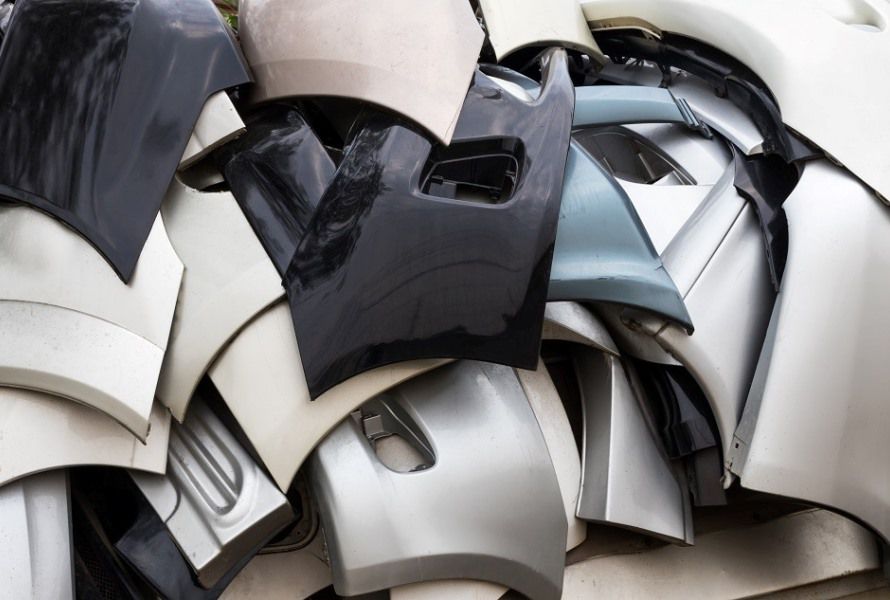
4.4 Agriculture
In agriculture, polyethylene is utilized in producing greenhouse films, irrigation systems, mulching films, and silage bags. These applications help enhance crop yield, control pests, and conserve water resources. Polyethylene's resistance to degradation, flexibility, and UV stability make it ideal for withstanding harsh agricultural conditions.
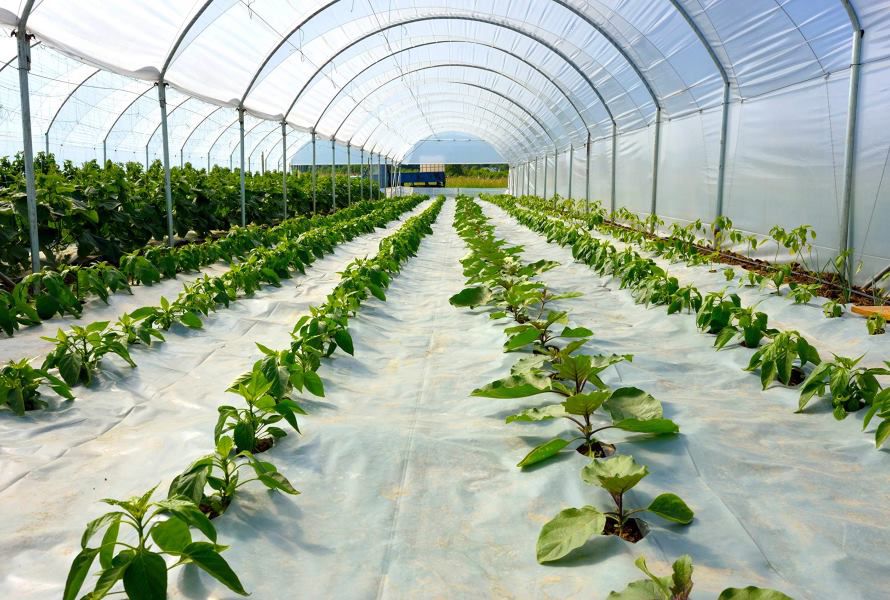
Greenhouse films made from PE plastic is widely used in agriculture
4.5 Healthcare
Polyethylene plays a vital role in the healthcare industry, particularly in manufacturing medical devices, surgical equipment, and packaging for pharmaceutical products. Its biocompatibility, stabilizability, and chemical resistance make it suitable for applications such as syringes, catheters, and medicine bottles.
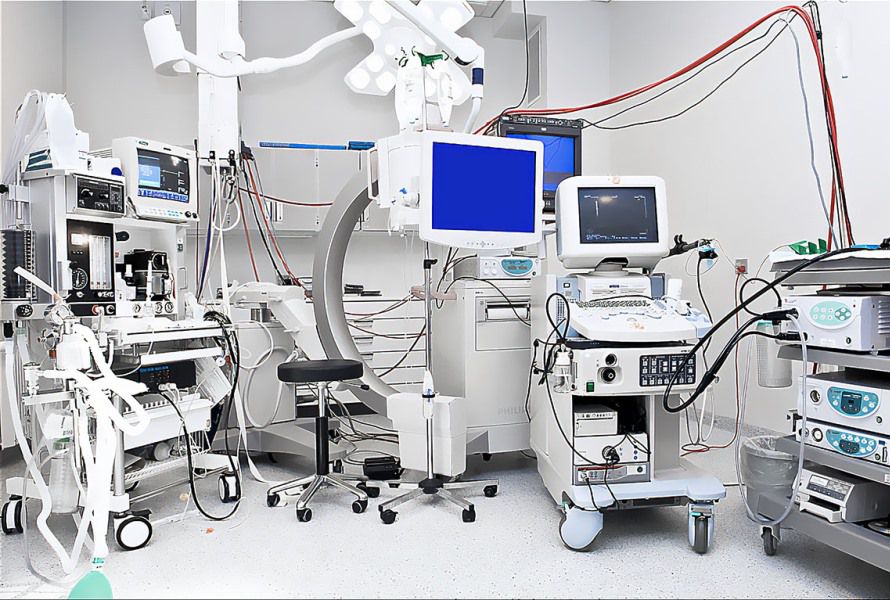
Polyethylene can be used to manufactured medical devices or surgical equipment
4.6 Electrical and Electronics
The electrical and electronics industry utilizes polyethylene for insulation purposes. It is commonly used in cables, wires, electrical connectors, and insulation tapes. Polyethylene's excellent electrical properties, including high dielectric strength and low electrical conductivity, ensure efficient and safe electricity transmission.
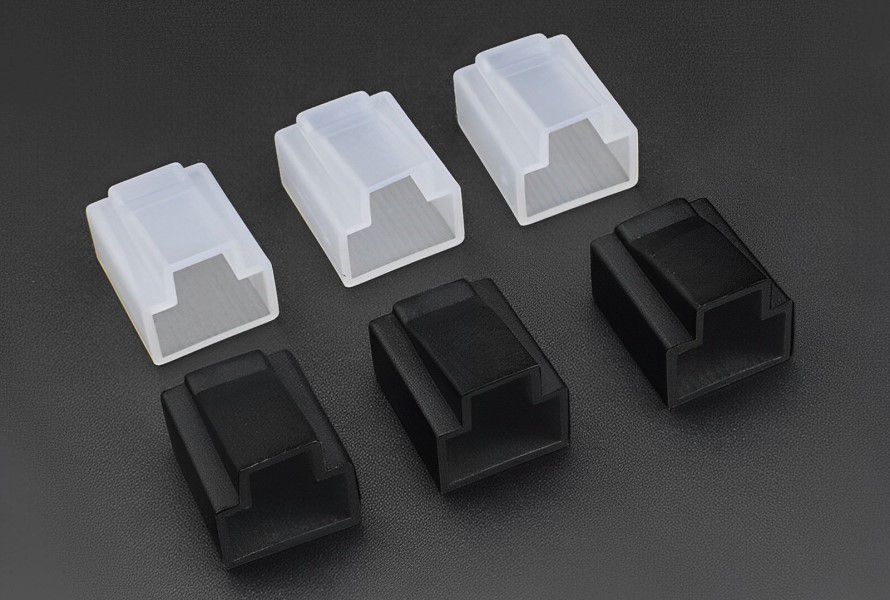
5. EuroPlas masterbatch for PE plastic products
EuroPlas is one of the world's leading filler masterbatch suppliers. Our company manufactures high-quality filler masterbatches for various plastic products, including PE plastics.
EuroPlas PE filler masterbatch combines PE resin, CaCO3, and additional substances like processing aid and dispersion agent. This unique mixture serves multiple purposes: reducing manufacturing expenses, enhancing the impact resistance and heat resistance of the final goods, improving surface hardness, bolstering strength endurance, and increasing ductility.
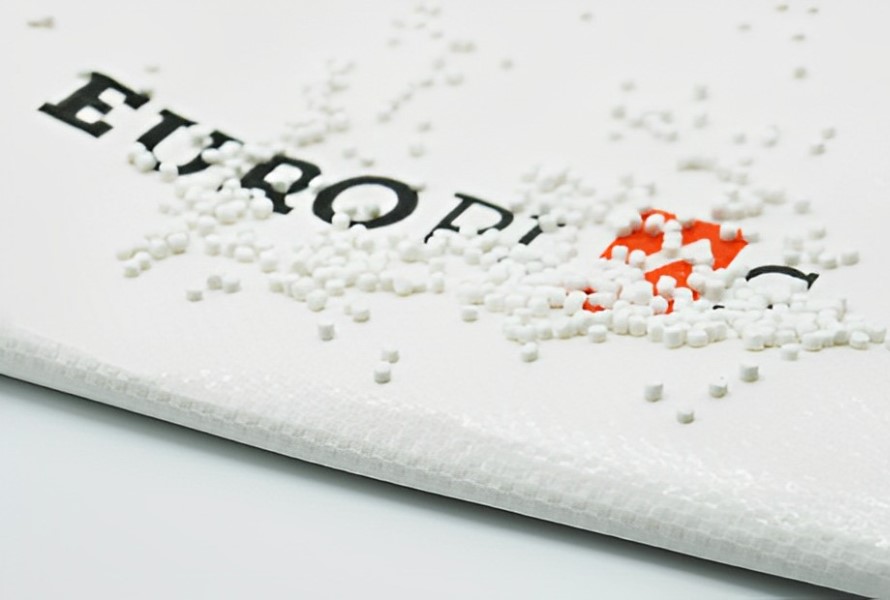
Advantages of EuroPlas masterbatch:
- Improved properties: Adding filler materials enhances PE plastic products' mechanical strength, making them more durable and resistant to impact and stress. This results in products that can withstand heavy loads and rough handling.
-
Increased dimensional stability: Europlas masterbatch also helps to reduce shrinkage and warping of PE plastic products during the cooling process, ensuring better dimensional stability. This is particularly important for applications that require precise measurements and tight tolerances.
- Enhanced heat resistance: Incorporating specialized additives in the filler masterbatch improves the heat resistance of PE plastics. This allows the products to withstand higher temperatures without deformation or loss of structural integrity.
- Cost efficiency: Europlas masterbatch is a cost-effective solution to reduce the consumption of the base polymer. This results in lower production costs while maintaining the desired properties of the end products.
EuroPlas prides itself on producing filler masterbatches that are consistent in quality and performance. The company employs stringent quality control measures throughout manufacturing to ensure that the masterbatches meet the highest industry standards.
Don't hesitate to contact us for more detailed information about EuroPlas' PE filler masterbatch and its specific applications.