Introduction
The plastic industry is witnessing 5 trillion plastic bags waste a year, and the numbers are only rising. Therefore, the use of bio-derived plastics could be a big catch in controlling this waste and creating a more sustainable packaging sector.
The big key concern about plastic in packaging, let alone bioplastic, is safe for human contact. It needs to be non-toxic for ingestion, skin contact, etc.
Using bioplastic can motivate manufacturers standing for a better future and minimizing unwanted impacts. So, pull back and explore some of the most common bioplastics being utilized in the packaging industry.
1. A List of 5 Bioplastics That Suitable For Packaging Needs
1.1. Bio-Polyethylene Terephthalate (bPET)
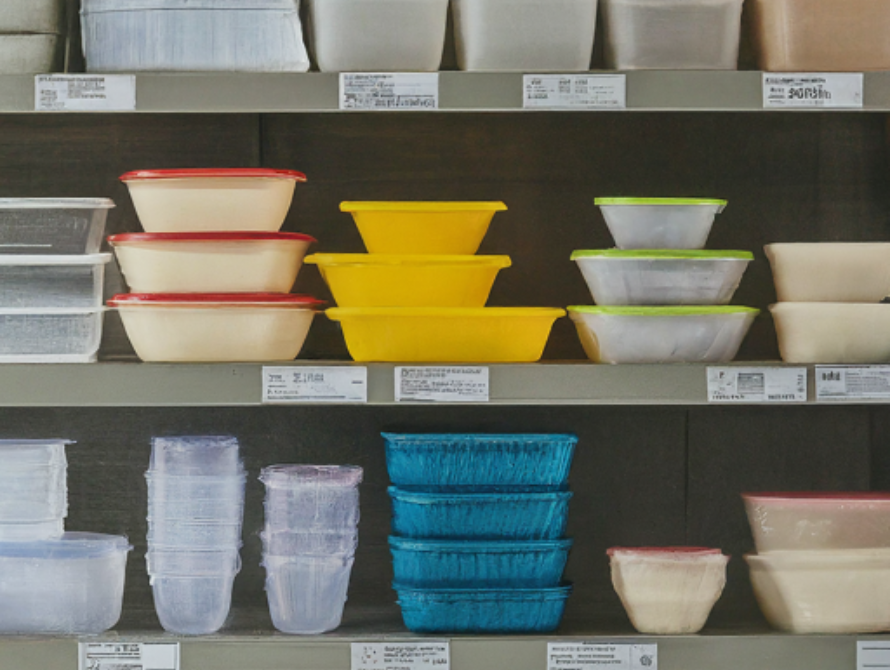
Bioplastic food containers offer a more sustainable alternative to traditional plastic packaging.
Able to alternate traditional PET plastic in beverage bottle and food container applications, bPET is dominating the bioplastics market. According to
Allied Market Research, this market is expected to grow from 441.3 million USD in 2021 and potentially exceed 10% of the EU's annual output.
Unlike traditional PET plastic derived from petroleum, bPET is made from renewable resources like corn starch, sugarcane, or even coffee grounds. The process of creating bPET is similar to PET, involving complex chemical reactions to create monomers that are then polymerized to form PET.
In addition to similar properties to PET, bPET really shines with its biodegradability. Under properly processed conditions, it can break down into natural compounds such as water, carbon dioxide and biomass, which are readily absorbed by the environment.
1.2. Bio-Polypropylene (bPP)
Bio-polypropylene (bPP) is a type of polypropylene made from biomass sources such as plant starch or cellulose, reducing dependence on limited resources such as fossil fuels. These materials are fermented, converting biomass materials into monomers that are then polymerized into bPP.
Companies like
Mitsui Chemicals Group in Japan, is in the process of commercializing bPP production to support mitigation efforts to reduce greenhouse gas emissions.
bPP can replace polypropylene (PP) in a number of applications such as food packaging, textiles and auto parts. bPP typically has the same efficiency as PP strength, moisture resistance, and chemical resistance, making it suitable for packaging dry food items such as cereals or pasta.
1.3. Bio-Polyethylene (bPE)
Derived from sugar or vegetable oil to replace PE, bPE takes bio-ethylene as the main raw material. This bio-ethylene is then converted into bio-PE through a conventional catalyst-based polymerization process.
Similar to PE in terms of flexibility, durability and moisture resistance, bPE still pops up with the ability to capture and sequester CO2 from the atmosphere. Despite its simple structure, PE is undoubtedly the most commonly used plastic in the world over the years. It is mainly seen in packaging material (bags, films, bottles…). The chemical composition of biological PE is the same as fossil-based PE. Therefore, it can be used in both rigid and flexible packaging as well as all other applications.
bPE encountered difficulties in its early years of development. Since 2010, Braskem pioneered bPE production through bio-ethanol dehydration. One of the main raw materials used to create plastic is fossil ethylene derived from natural gas, and reduced costs have increased profit margins, impeding the development of renewable ethylene.
Want a more lightweight and eco-friendly option, find no more. Bioplastic water bottles are here
1.4. Bio-derived Polyethylene Furanoate (PEF)
PEF is derived from renewable resources such as biomass, which can encompass plant-based materials or even food waste. This flexible feedstock allows for a degree of variation in the production process.
PEF provides enhanced protection against oxygen and carbon dioxide than traditional bioplastics, making it suitable for packaging oxygen-sensitive foods and beverages. Although PEF is not a direct replacement for a specific traditional plastic, it nevertheless provides similar functions to PET while potentially being obtained from renewable sources.
PET is partly of biological origin but its biodegradability depends on certain specific conditions. Appropriate recycling infrastructure is critical to maximize the sustainability benefits of PEF.
1.5. Polytrimethylene Furandi carboxylate (PTF)
PTF is a bio-based plastic that is still being developed but it has the potential to offer more excellent barrier properties than PEF. PTF is supported by the
DuPont - Tate & Lyle joint venture in Tennessee.
Similar to PEF, PTF is not a direct replacement source but provides similar functions to PET with the potential to create a more sustainable source. PTF is produced from renewable resources and undergoes the same complex chemical process as PEF.
PTF can be used for a variety of packaging applications, including oxygen-sensitive foods or medical supplies. PTF is still in the development phase, with ongoing research focused on optimizing the manufacturing process and achieving cost-effectiveness.
Learn more about how bioplastics are manufactured:
How are bioplastics made?
2. Major Benefits of Bioplastics to Packaging Industries
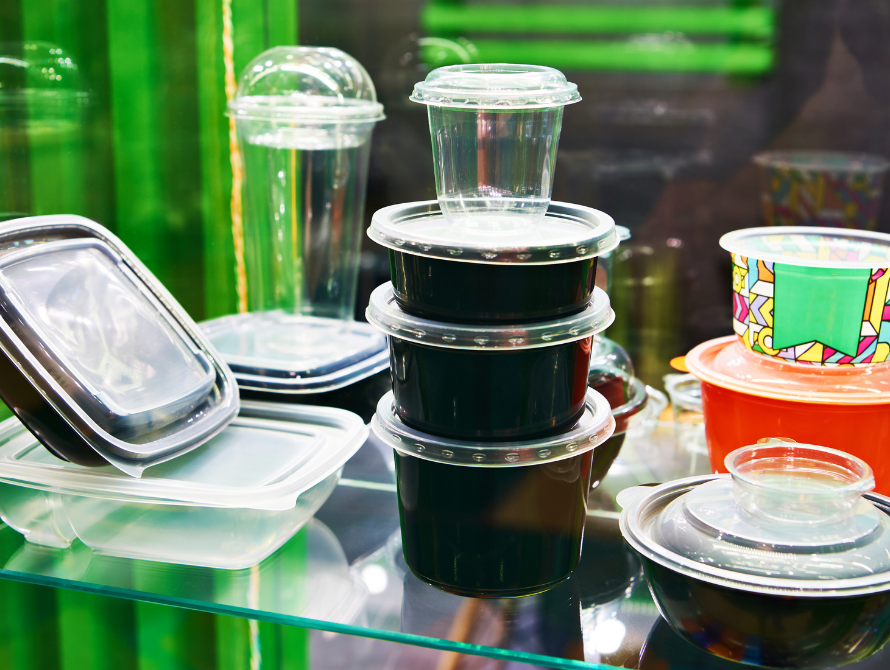
Safety is the first and foremost requirement when it comes to human contact. And that's what bioplastic can offer.
Reduce greenhouse gas emissions: Bioplastics offer significant advantages over traditional plastics by reducing greenhouse gas emissions. Studies show that completely replacing fossil fuels with sugarcane could reduce emissions by 25%, while recycling existing plastic could achieve similar reductions. Additionally, switching to renewable energy sources for plastic production could cut emissions.
Biodegradability: Unlike conventional plastics that persist in the environment for centuries, bioplastics can be broken down by microorganisms into harmless substances such as water, carbon dioxide and biomass. This asset addresses growing concerns about microplastic pollution and its adverse effects on ecosystems.
Closed-loop system: Bioplastics contribute to a more circular economy by enabling the creation of a closed-loop system. Biomass is first used to produce bioplastics, and after their useful life, these materials can be converted into energy or even new bioplastics.
Flexibility in application: Bioplastics can be tailored to meet the specific requirements of different applications. For example, PLA has become popular in 3D printing due to its biodegradability and ease of processing. On the other hand, Bio-PE has applications in packaging and agricultural films.
Biodegradability in bioplastics is an undeniable solution that can ease out environmental problems
Recycling potential: Bioplastics can be recycled into higher quality materials through new chemical and biological methods. This capability helps extend the lifespan of these materials and further contribute to a circular economy.
When choosing a bioplastic for packaging applications, it is important to consider a number of factors, such as the type of product being packaged, the required shelf life, and the desired end-of-life options. Bioplastics can be a more sustainable alternative to traditional plastics, but it is important to choose the right type of bioplastic for the application.
3. Conclusion
These 5 outstanding plastic types all bring the same greatest benefit, which is to replace current virgin plastic, reducing pressure on both the supply of plastic raw materials and the environmental ecosystem.
Using bioplastics can be a wise step indeed, but requires much more effort and considerations in order to fully possess bioplastics. Continuing research and development will be the key to bring out the full picture about bioplastics and other sustainable plastic solutions.
4. About EuroPlas’ BiONext
EuroPlas, a plastics manufacturing unit with 17 years of industry-leading experience, our research experts have launched a dedicated line of bioplastics products.
EuroPlas' BiONext, a product line made of biodegradable plastic compounds, is an environmentally friendly alternative. With this product, we confidently commit that products using bioNext will be the perfect combination of strong biodegradability, preserving plastic function and aesthetics.
BiONext products decompose within 12 months after use, minimizing environmental impact and promoting a circular life cycle. BiONext products can be processed directly without additional materials, simplifying the manufacturing process and reducing waste.
BiONext product lines are designed with a variety of formulations (102, 152, 400, 500, 600, 700) with specific properties to meet the needs of different end products.
Contact us now to find more detailed information about these plastics and we will be happy to sit with you to find the most optimal solution.
Don't miss out our blog, where innovative information about plastic solutions is updated weekly.