A plastic granulator is a vital tool in recycling and material processing industries, but operational missteps can significantly affect performance and lifespan. Understanding these frequent errors is crucial for maintaining machine efficiency, reducing downtime, and avoiding unnecessary costs. In this article, we’ll explore 5 common mistakes and offer simple solutions to keep your granulator running smoothly.
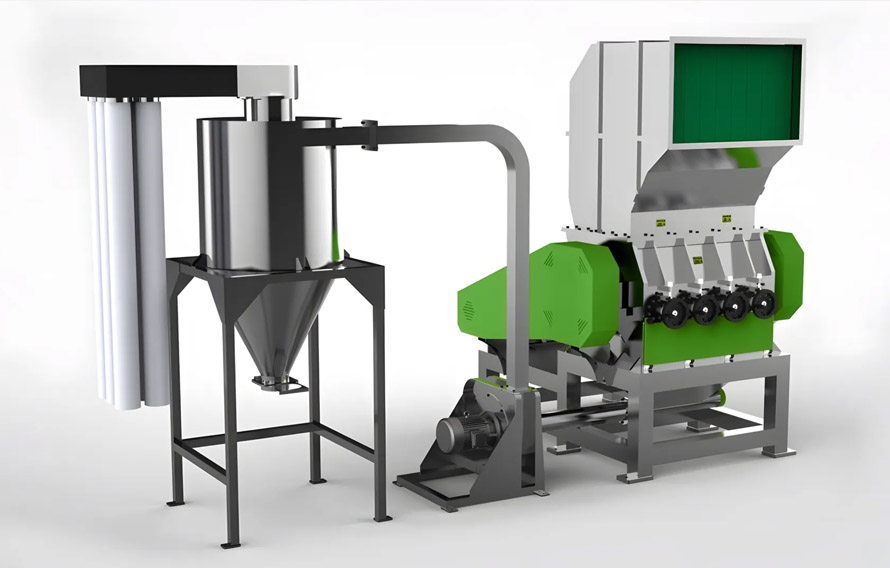
Understanding common plastic granulator errors is essential for maintaining production efficiency and reducing costs.
1. The Importance of A Plastic Granulator
1.1. What is a Plastic Granulator?
A plastic granulator is a specialized machine designed to break down plastic waste into smaller, reusable pieces. This process, known as granulation, transforms discarded plastic items into valuable raw materials for new products.
1.2. Types of Plastic Granulator
Various granulator types are tailored to different materials and recycling needs:
- Centrifugal Granulators: Use rotational force to cut plastics efficiently, ideal for soft and semi-soft materials.
- High-Speed Granulators: Operate at rapid speeds, suited for high-output recycling operations.Slow-Speed
- Granulators: Quieter and durable, designed for noise-sensitive environments or reduced maintenance costs.
- Hybrid Granulators: Combine high-speed and slow-speed features for versatile recycling applications.
1.3. Key Roles of Plastic Granulators
Annually, over 400 million tons of plastic waste are produced, with much coming from single-use plastics. Despite rising awareness, only 9% is recycled, leaving the rest to pollute the environment. Daily, over 2,000 garbage bags of plastic enter water bodies, worsening the crisis. Addressing this issue requires effective plastic waste management, and plastic granulators are at the forefront of this effort.
Plastic granulators offer a multitude of environmental and economic benefits. By effectively recycling plastic waste, these machines contribute to a more sustainable future.
Environmental Benefits
- Minimized Waste: Granulators convert plastic waste into reusable pellets, reducing landfill and ocean pollution.
- Energy Conservation: Recycling plastic consumes less energy than producing new materials.
- Pollution Control: Proper recycling minimizes environmental pollution caused by plastic waste.
- Sustainability: Encourages circular economies by enabling reuse of plastic in manufacturing.
Economic Benefits
- Job Growth: Boosts the recycling and manufacturing sectors, creating employment.
- Cost Efficiency: Recycled materials are more economical than creating new ones from raw resources.
- New Revenue Streams: Recycled plastic can be sold to manufacturers, adding value to the economy.
Plastic granulators are indispensable in recycling, transforming waste into usable materials, promoting sustainability, and stimulating economic growth. Their effectiveness depends on responsible and sustainable use, ensuring maximum benefits with minimal downsides.
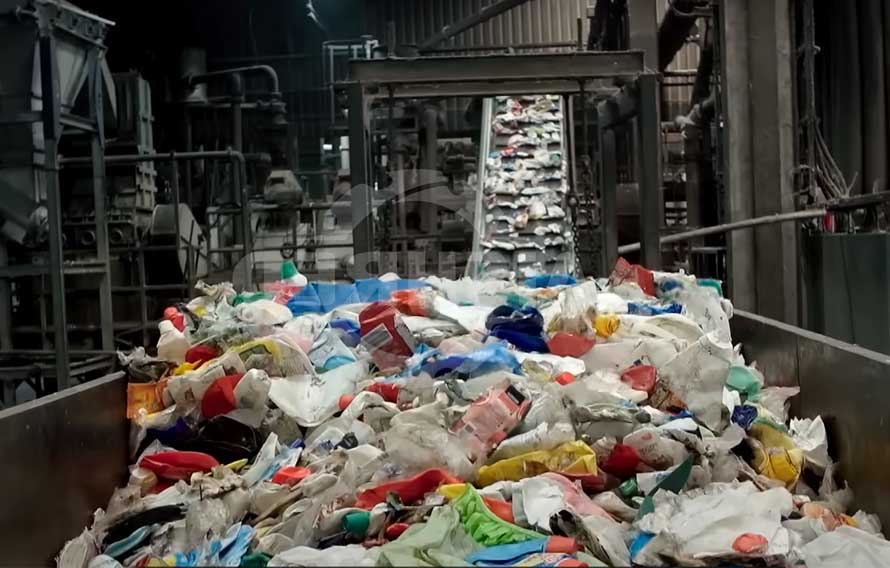
Plastic granulators offer a multitude of environmental and economic benefits
2. Common Errors of Plastic Granulator You Should Avoid
Plastic granulators are essential machines in the recycling industry. However, like any machinery, they can encounter operational issues. Here are some common errors and solutions:
2.1. Screw Running Normally but No Discharge
Causes: Inconsistent feeding, blockages at the inlet, or metal objects obstructing the screw groove.
Solutions:
- Increase feed volume for stable operation.
- Stop the machine and remove blockages or eliminate "bridging."
- Shut down immediately if metal objects are detected, and clear the screw groove.
2.2. Main Motor Torque Issues
Overloading
Cause: Excessive motor torque can be caused by factors like inadequate lubrication, misalignment, or foreign objects in the feed material or vibration damaging motor bearings.
Solutions:
- Regularly clean and inspect the lubrication system.
- Use vibration and temperature monitoring tools to detect issues and track trends.
Underloading
Cause: Insufficient motor torque may result from feeding system failures or heating issues. leading to twin-screw idling.
Solutions:
- Check for faults in the additive or main feeding system.
- Clear any blockages promptly.
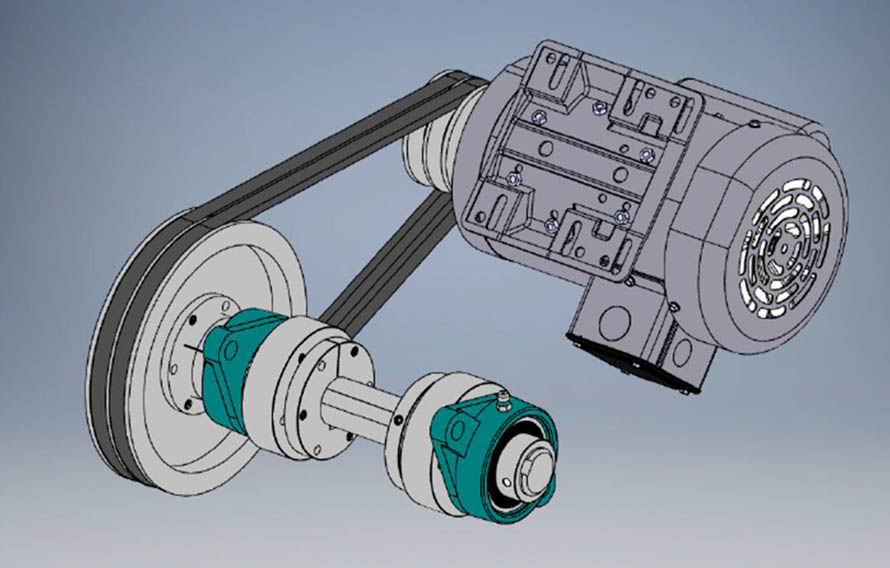
Overloading and underloading motor torque issues of plastic granulator can be resolved with regular inspections and monitoring.
2.3. Friction Clutch Issues
Causes: Low starting voltage, overheating or aging of friction components, or insufficient air pressure.
Solutions:
- Avoid starting during peak power usage.
- Limit restarts to intervals of 30 minutes or longer.
- Use forced cooling methods, especially in summer.
2.4. Friction Clutch Malfunction
Causes:
- Low starting voltage of the main motor.
- Overheating or aging of the friction components.
- Insufficient air pressure in the clutch mechanism.
Solutions:
- Avoid starting during peak electricity usage.
- Maintain a minimum 30-minute interval between restarts, extending further in hot weather.
- Employ forced cooling systems, such as fans, to manage overheating.
2.5. Vent Hole Problems
Causes: Impurities in raw materials, excessive feed rate, or inadequate plasticizing temperature.
Solutions:
- Clean raw materials or replace the filter.
- Reduce feed rate to stabilize extrusion.
- Increase plasticizing temperature for smoother operations.
- Addressing these errors ensures efficient, safe, and reliable operation of plastic granulators.
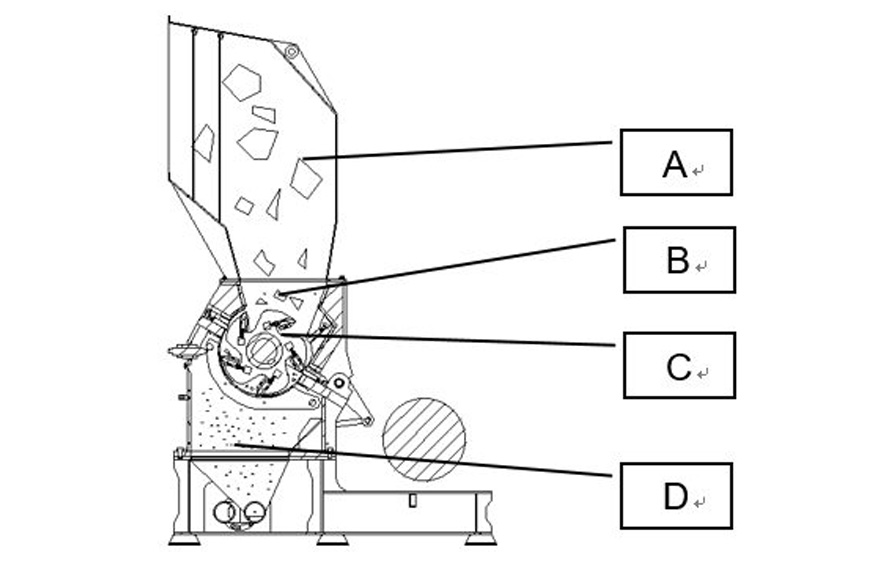
A robust checking and maintenance schedule ensures plastic granulators' long-term performance, reliability, and efficiency.
3. How to Prevent These Errors
Plastic granulators are vital in reducing waste and cutting costs in injection molding and extrusion operations. To ensure long-term performance and reliability, a robust preventative maintenance schedule is essential. Below are guidelines to prevent common issues and maximize efficiency:
3.1. Pre-Operational Checks
- Manual Rotor Inspection: Before starting the machine, manually rotate the rotor to check for any obstructions or signs of damage.
- Foreign Material Removal: Thoroughly inspect the feed hopper for any foreign objects that could potentially harm the machine or compromise the quality of the output granules.
3.2. Regular Blade Maintenance
- Visual Inspection: Periodically inspect the blades for signs of wear, chipping, or dulling.
- Sharpening or Replacement: Dull blades can significantly impact granulation efficiency and output quality. Sharpen or replace blades as needed.
3.3. Screen Maintenance
- Screen Inspection: Regularly check the screen for clogging or damage. A clogged screen can reduce throughput and affect the quality of the granules.
- Screen Replacement: Replace worn-out screens to maintain optimal performance.
3.4. Consistent Material Feeding
- Avoid Overfeeding: Excessive material can overload the machine and lead to overheating and reduced efficiency.
- Maintain Steady Feed Rate: A consistent feed rate ensures smooth operation and prevents material buildup.
3.5. Regular Lubrication
- Lubricate Moving Parts: Proper lubrication of bearings, gears, and other moving components is crucial for preventing wear and tear.
- Follow Manufacturer's Guidelines: Adhere to the manufacturer's recommended lubrication schedule and use the specified lubricants.
3.6. Monitor Motor Performance
- Check Motor Load: Monitor the motor's load to identify potential issues like overloading or underloading.
- Inspect Belts and Pulleys: Ensure proper tension and alignment of belts and pulleys to prevent slippage and premature wear.
By following these guidelines, you can significantly improve the efficiency and longevity of your plastic granulator, reducing downtime and optimizing production.
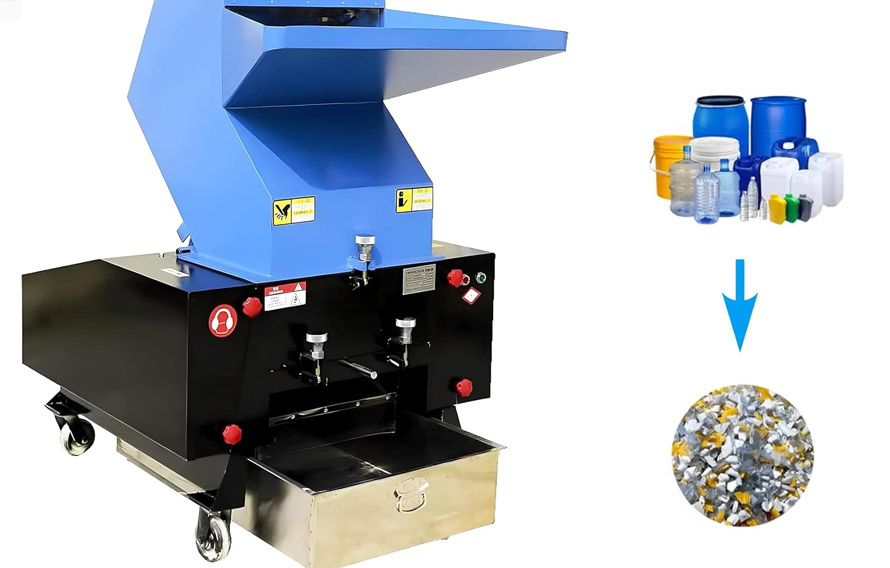
By breaking down large plastic items into smaller granules, plastic granulators streamline transportation and handling of waste.
4. Conclusion
To ensure optimal performance and longevity, avoiding the common errors in plastic granulator operation is essential. Regular inspections, proper maintenance, and adherence to manufacturer guidelines can help prevent issues like screw blockages, torque imbalances, clutch malfunctions, and vent hole problems.
By addressing these concerns proactively, businesses can reduce downtime, improve efficiency, and minimize costly repairs. Investing in regular blade checks, proper feeding practices, and lubrication routines safeguards your equipment’s productivity. A well-maintained granulator not only reduces operational risks but also supports sustainability by enhancing recycling efficiency.
5. About EuroPlas
EuroPlas stands at the forefront of the plastics industry, offering premium products like filler masterbatch, plastic additives, and compounds. Our solutions are engineered to optimize plastic properties, such as strength, flexibility, and thermal resistance, catering to industries like agriculture, healthcare, and electronics. EuroPlas emphasizes high-quality raw materials and advanced manufacturing techniques, ensuring consistent excellence. By integrating EuroPlas’s products with a plastic granulator, manufacturers can achieve superior results, including efficient recycling and precise material handling.
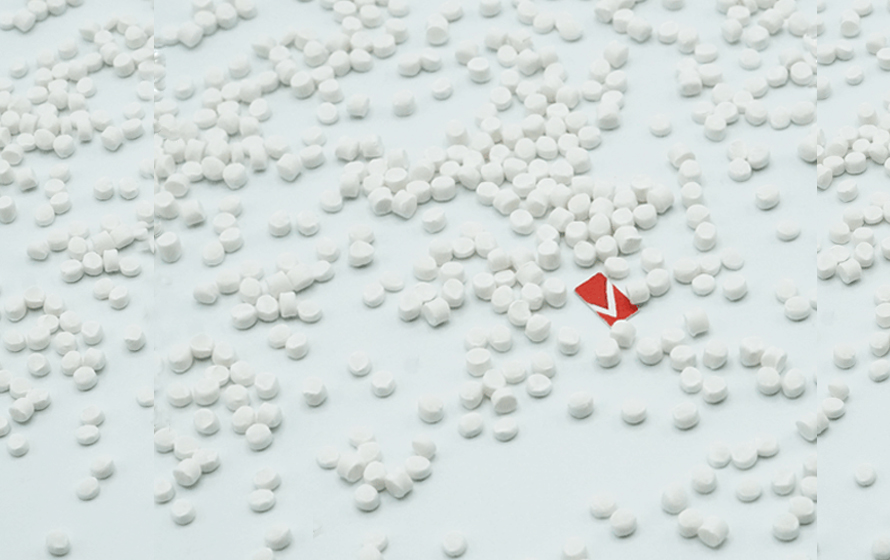
Integrating EuroPlas products with a plastic granulator enhances efficiency, strength, and versatility.
For more information or to explore how we can support your business, contact us today!