1. Six Applications Of Pressure Forming
1.1. Packaging
One of the most prominent applications of the pressure forming process is in the packaging industry. This method is ideal for creating custom packaging solutions that offer superior protection and aesthetic appeal. Pressure forming enables manufacturers to produce detailed and complex shapes, such as clamshells, blisters, and trays, which are widely used for consumer electronics, medical devices, and food products. The precision and quality of the formed packages ensure that the contents are well-protected and presented attractively.
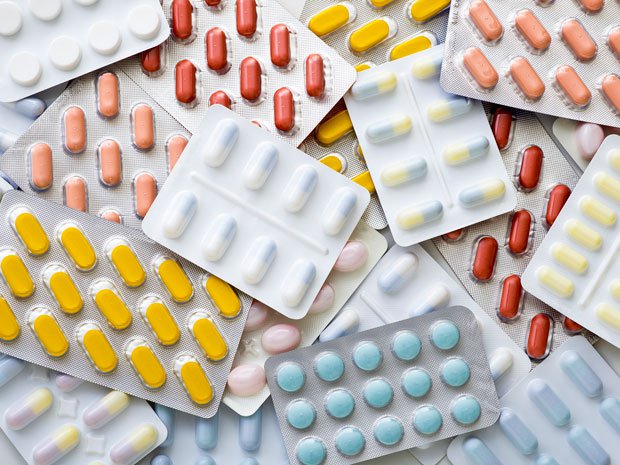
The application of the Pressure Forming Process in blister packaging.
1.2. Consumer Products
The pressure forming process is extensively used in the production of various consumer products. From household appliances to personal care items, this method allows for the creation of high-quality plastic components with fine details and attractive finishes. Products such as vacuum cleaners, coffee makers, and cosmetic containers benefit from the precision and versatility of pressure forming.
In vacuum cleaners, the outer casings and internal compartments are typically created using pressure forming due to the need for precision and durability. For coffee makers, the water reservoirs and control panels benefit from pressure forming, ensuring a high-quality finish and accurate dimensions. Cosmetic containers, including lids and base components, are often manufactured through pressure forming to achieve the intricate designs and consistent quality required for these products. The ability to produce detailed textures and complex shapes makes it a preferred choice for manufacturers looking to enhance the aesthetic and functional appeal of their products.
1.3. Dental
In the dental industry, the pressure forming process is crucial for creating customized dental appliances. This includes items like retainers, aligners, and mouthguards. The process ensures that each piece fits perfectly to the patient’s unique dental structure, providing comfort and effectiveness. Pressure forming is also used to produce dental trays and molds that are essential for various dental treatments and procedures. The accuracy and quality of these products contribute to better patient outcomes and satisfaction.
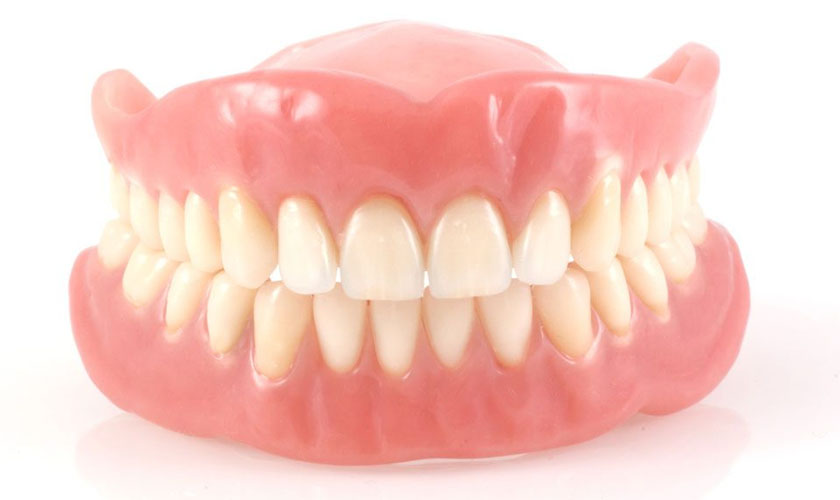
The application of the Pressure Forming Process in the production of dental prosthetics.
1.4. Automotive
The automotive industry relies heavily on the pressure forming process for manufacturing interior and exterior components. This technique is used to create intricate and durable parts such as dashboards, door panels. The high level of detail and precision achieved through pressure forming ensures that these components meet the stringent quality standards of the automotive industry. Additionally, the process allows for the use of different textures and finishes, enhancing the overall look and feel of the vehicle’s interior.
1.5. Aerospace
In the aerospace sector, the pressure forming process is used to produce lightweight and durable components. These include interior panels, seat parts, and storage compartments. The ability to create complex shapes and detailed designs while maintaining structural integrity is crucial for aerospace applications. Pressure forming also allows for the use of advanced materials that contribute to the overall performance and efficiency of aircraft. The precision and reliability of the formed parts are essential for ensuring safety and comfort in the demanding aerospace environment.
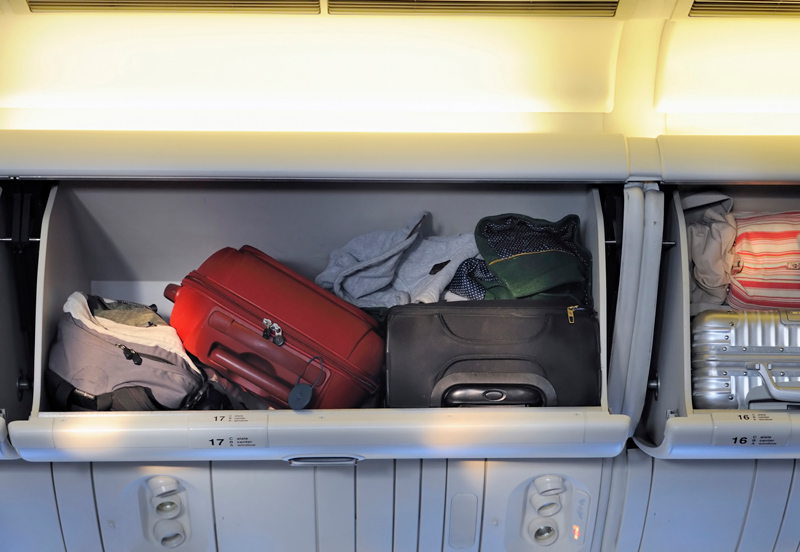
The application of the Pressure Forming Process in the creation of aircraft storage compartments.
1.6. Industrial
The industrial sector benefits from the pressure forming process in the production of various equipment and machinery components. This includes housings, enclosures, and panels that require high durability and precision. Pressure forming allows for the creation of parts with complex geometries and detailed features, which are essential for the functionality and performance of industrial machines. The process also supports the use of high-performance materials that enhance the strength and longevity of the components.
1.7. Additional Applications
Beyond the mentioned industries, the pressure forming process finds applications in various other fields. This includes medical devices, electronics, and recreational products. The versatility and efficiency of pressure forming make it a valuable manufacturing technique for any industry that requires high-quality plastic components with intricate designs.
2. Tips for Successful Pressure Forming
To achieve the best results with the pressure forming process, consider the following tips:
Material Selection: Choose the right plastic material that suits the specific requirements of your application. Factors such as durability, flexibility, and thermal resistance should be considered.
Tooling Design: Invest in high-quality tooling that ensures precise and consistent results. The design of the mold plays a crucial role in the success of the pressure forming process.
Process Parameters: Optimize the process parameters such as temperature, pressure, and cycle time to achieve the desired quality and efficiency.
Quality Control: Implement strict quality control measures to ensure that the formed parts meet the required specifications and standards.
3. Conclusion
The pressure forming process is a versatile and efficient manufacturing technique that offers numerous advantages across various industries. From packaging and consumer products to automotive and aerospace applications, this process enables the production of high-quality plastic components with intricate designs and excellent finishes. By understanding the applications and tips for successful pressure forming, manufacturers can leverage this technology to enhance their product offerings and achieve greater success in the market.
4. About EuroPlas
As the world's leading producer of filler masterbatch, EuroPlas is proud to offer unique plastic material solutions that help customers optimize production costs and enhance their competitiveness in the market. EuroPlas provides a range of products, including:
Bioplastic compound: Green material solution enables end-products to be biodegradable within 12 months
Color masterbatch: Material solution enhances end-products' aestheticity by providing exact color
Plastic additives: Material solution improves production efficiency and end-products' functions
Engineering plastic compound: Full-function-in-one-material solution for end-products
Filler masterbatch: Cost-effective material solution for plastic enterprises
Bio filler: Cost-effective material solution for bioplastic end-products
Contact EuroPlas today! Visit our blog for the latest updates on plastics and advanced manufacturing solutions.