Polypropylene is a versatile thermoplastic material that has found its way into many industries due to its excellent properties. But are there different types of polypropylene? The answer is yes. In fact, there are seven different types of polypropylene, each with its own unique properties and applications. In this blog, we will discuss these seven types of polypropylene and their respective uses.
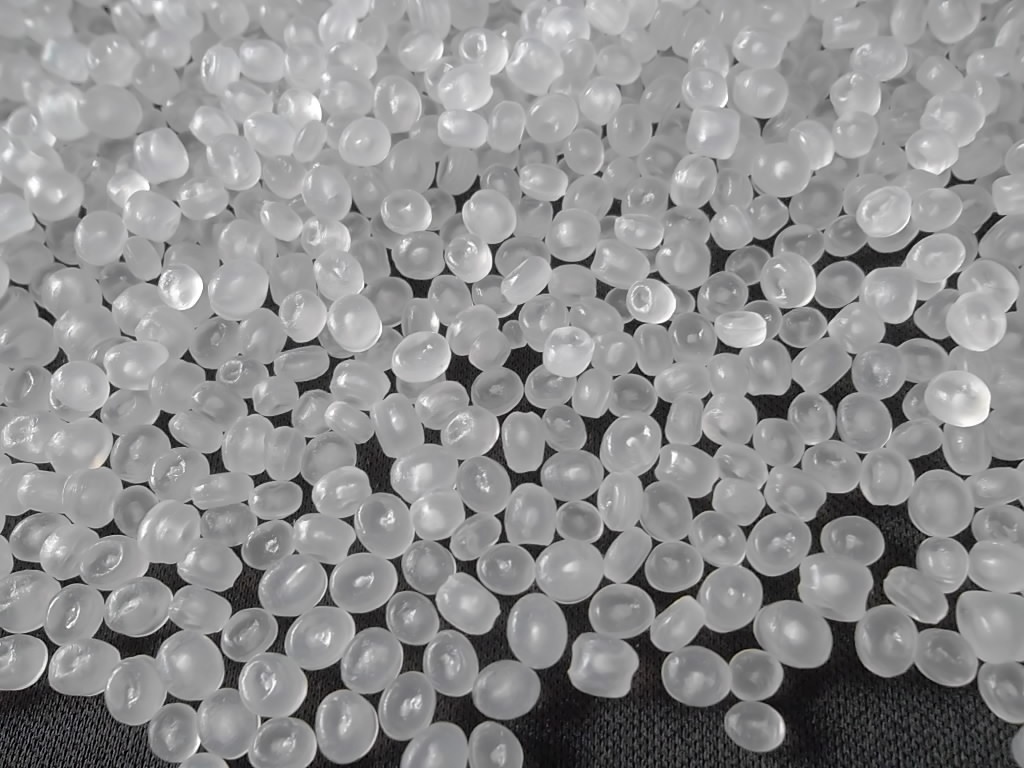
Many people may ask: is polypropylene a homopolymer or copolymer? And the answer to this question is that polypropylene can be either a homopolymer or copolymer depending on how it is produced. To help you know which is more suitable, we shall include both types in our post.
1. Polypropylene Homopolymer
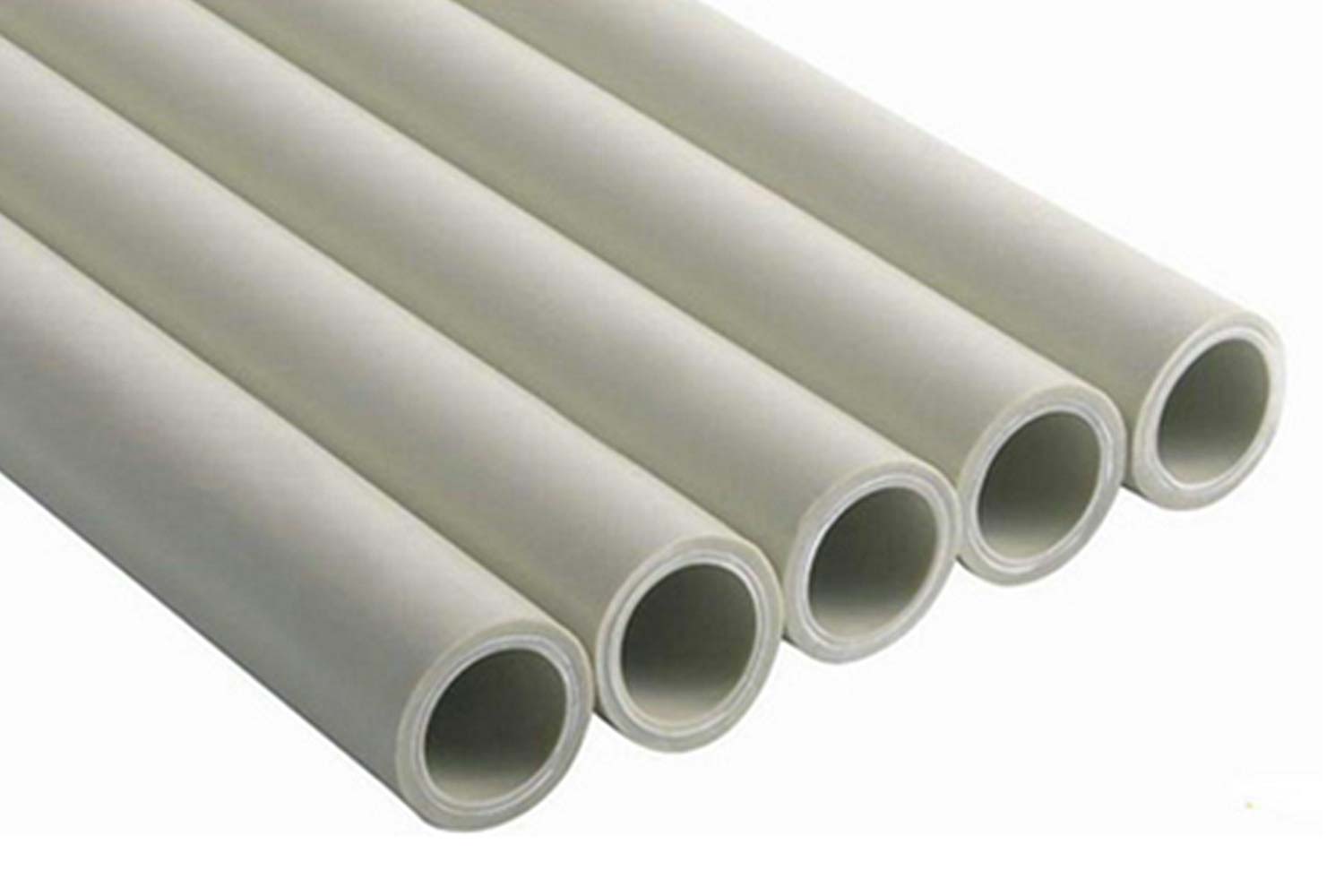
Polypropylene homopolymer is a thermoplastic material that is produced through a polymerization process, which involves the reaction of propylene monomers with a catalyst under high temperature and pressure. It is a homopolymer composed of a single monomer unit, which is propylene.
Properties: Polypropylene has excellent chemical resistance, stiffness, and high melting point, which make it suitable for use in harsh environments. In addition, it has good electrical properties, low moisture absorption, and high impact strength. It is a translucent material that can be easily molded, extruded, or machined. Additionally, it has a relatively low cost compared to other engineering plastics, becoming an attractive option for manufacturers.
Applications: Polypropylene homopolymer is widely used in various industries, including medical equipment, food containers, packaging, automotive, and consumer goods. It provides excellent chemical resistance and can withstand corrosive substances, making it ideal for laboratory equipment, pipes, and tanks. It's good dimensional stability makes it suitable for precision parts like gears and bearings. It's also used to make fibers, films, and sheets for clothing, carpeting, and protective packaging. Polypropylene homopolymer fibers are durable and moisture resistant, while films and sheets have excellent clarity and low haze.
2. Polypropylene Copolymer
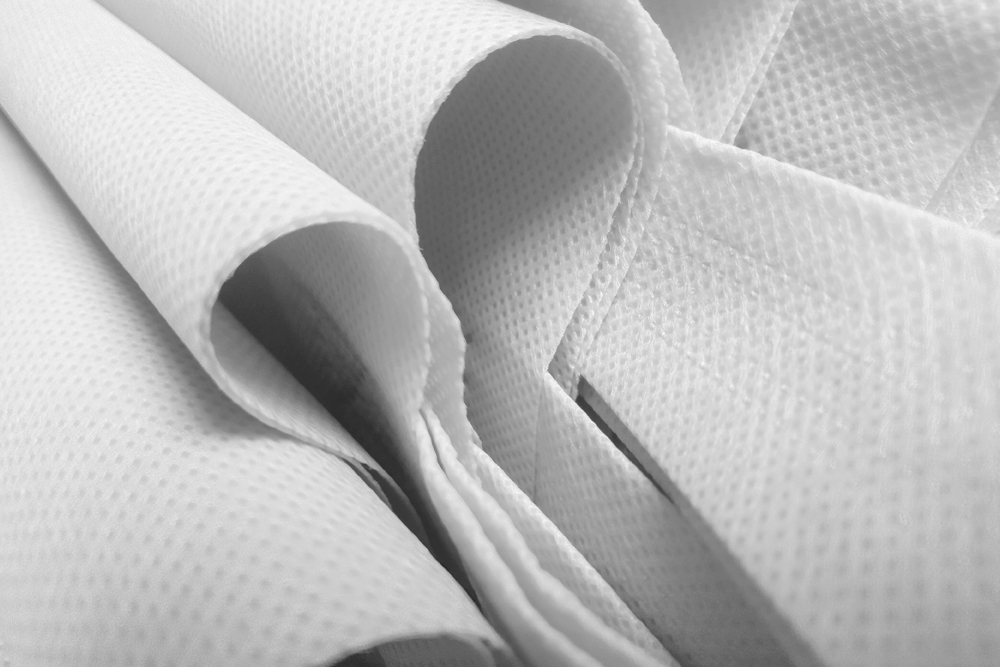
Polypropylene copolymer is a thermoplastic material produced by the copolymerization of propylene and ethylene monomers using a catalyst under specific conditions. The resulting material contains both propylene and ethylene monomer units in its molecular structure. This is the difference between polypropylene homopolymer vs copolymer.
Properties: Because of its excellent chemical resistance, high impact strength, and relatively low density, polypropylene is the material for items that must be both lightweight and long-lasting. It is perfect for use in goods that are put under repetitive stress because of its excellent fatigue resistance. It is widely used for consumer items since it also has good transparency and a high gloss finish.
Applications: Polypropylene is commonly found in packaging, household items, automobile parts, textile production, and medical instruments. The textile industry also employs it to create nonwoven textiles for protective gear and filters.
3. Polypropylene, Impact Copolymer
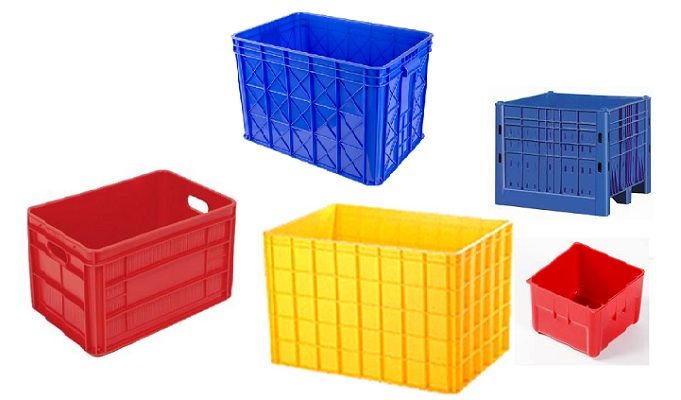
Polypropylene Impact Copolymer, also known as PPICP, is a thermoplastic material that is produced through the copolymerization of propylene and ethylene monomers with a specialized catalyst. It is designed to have high impact resistance and toughness while maintaining the other desirable properties of polypropylene.
Properties: Polypropylene possesses excellent chemical resistance, high impact strength, and a comparably low density. It also has remarkable resistance, excellent transparency and glossy finish.
Applications: Polypropylene impact copolymer is widely used in various applications, including packaging, household products, automotive components, textile industry, and medical devices. It is often used in food containers, beverage bottles, and storage bins. In the textile industry, it is used to produce nonwoven fabrics for protective clothing and filters. Furthermore, it is a popular choice in medical devices, including syringes and IV bags, due to its biocompatibility and sterilization capabilities. The automotive industry also uses it in the production of bumpers, dashboard components, and door trims due to its high impact strength.
4. Expanded Polypropylene
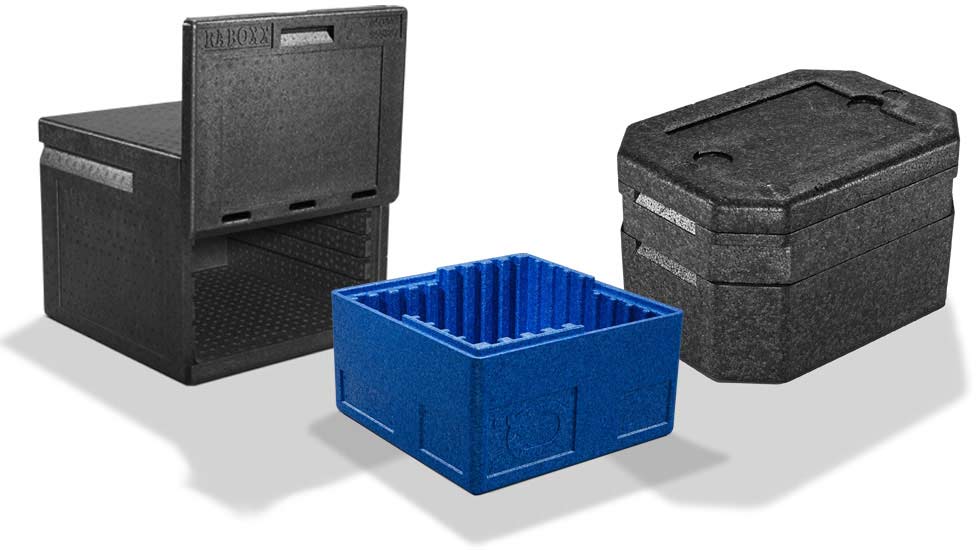
Expanded polypropylene (EPP) is a type of foam plastic made from expanded beads of polypropylene. EPP is produced by heating and melting small beads of polypropylene, which are then expanded using steam or other physical means to create a lightweight, closed cell foam material.
Properties: EPP has earned its reputation for its impressive ability to absorb shocks, offer thermal insulation, and resist water. Its superior strength and durability enable it to withstand repetitive impacts without succumbing to deformation or losing its form. EPP is both non-toxic and recyclable, and can be molded effortlessly into diverse shapes and sizes.
Applications: EPP is used for packaging electronics, appliances, and automobile components. It is widely utilized for producing sports equipment, such as knee pads, chest protectors, and helmets. In the construction industry, EPP is frequently utilized as an insulating material for foundations, roofs, and walls. Lightweight furniture, including stools, chairs, and tables, are popularly manufactured using EPP due to its favorable attributes.
5. Polypropylene Terpolymer
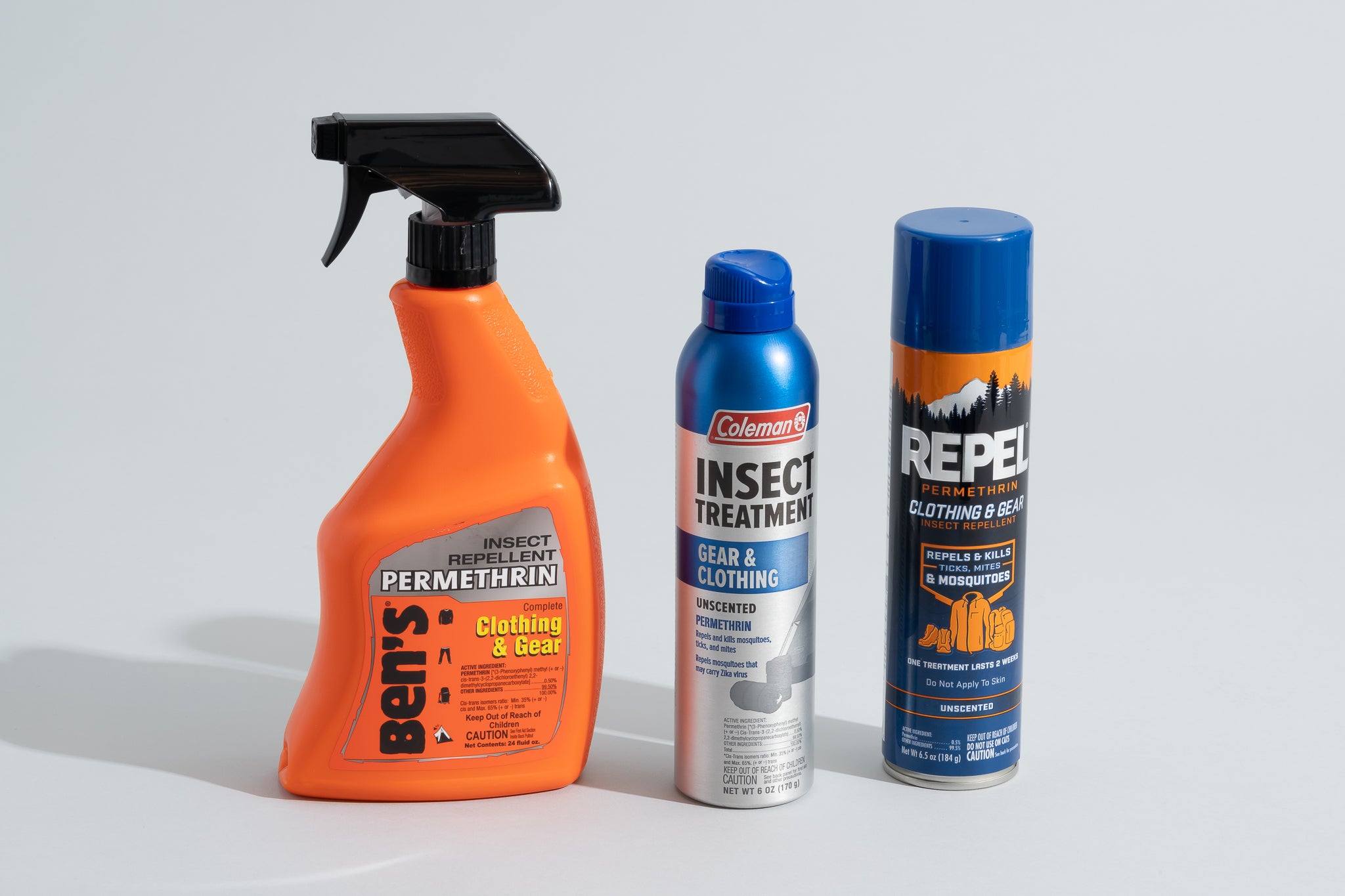
Polypropylene terpolymer is a thermoplastic material produced by the polymerization of three monomers propylene, ethylene, and a third monomer such as butene or hexene. The resulting material contains all three monomer units in its molecular structure. This is the main difference between polypropylene terpolymer and other types of polypropylene such as polypropylene homopolymer vs copolymer.
Properties: Polypropylene has excellent chemical resistance, high impact strength, and good dimensional stability. The material's relatively low density imparts it with a lightweight property that facilitates easy handling. Furthermore, its malleability allows for effortless processing and molding into numerous shapes.
Applications: Polypropylene terpolymer finds extensive usage across various industries, including but not limited to automotive, packaging, construction, and healthcare. It is used for automotive components like fenders, bumpers, and interior trims. As for packaging, applications like bottle production, container design, and cap formation are usually made from polypropylene terpolymer. In the construction sector, people use it to manufacture insulation materials, fittings, and pipes. Additionally, its biocompatibility and sterilization properties make it a fitting material for surgical instruments and implantable medical devices.
6. Polypropylene, High Melt Strength
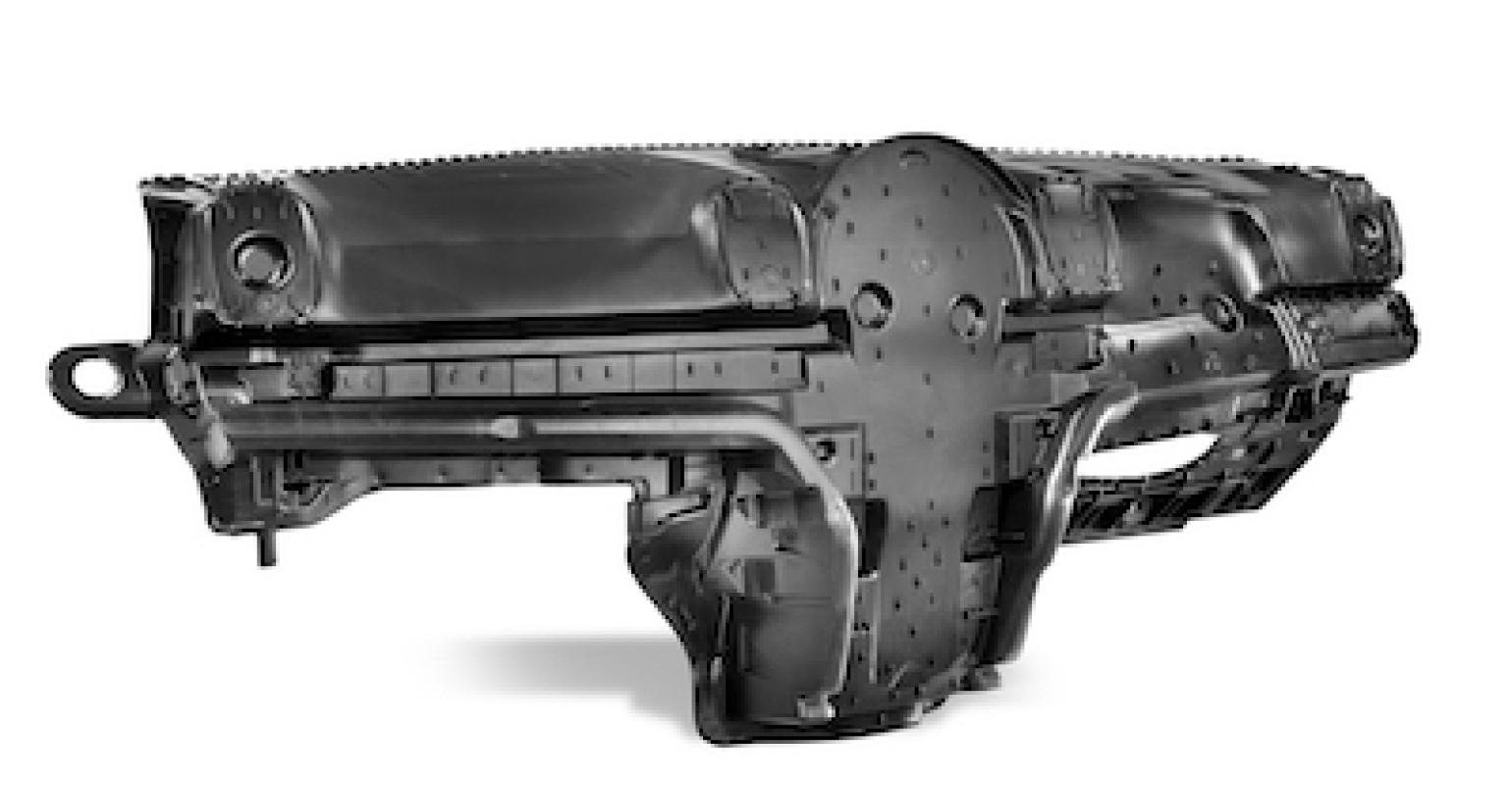
Polypropylene high melt strength (HMS) is a type of thermoplastic material that is produced by incorporating a specific amount of long chain branching into the polypropylene polymer chain during the polymerization process. As a result, a material with high viscosity and melt strength is produced, which is suitable for a variety of applications that call for outstanding processability and strength.
Properties: HMS provides an exceptional chemical resistance, and high stiffness. It is great for applications that need dimensional stability since it also has a low coefficient of thermal expansion. Due to its high melt strength, it may also be processed using a variety of techniques, including blow molding, thermoforming, and extrusion.
Applications: Automotive, packaging, and construction are just a few of the areas where polypropylene HMS is used extensively. For vehicle parts like instrument panels, door panels, and interior trimmings, its high melt strength and superior impact resistance allow it to be the ideal material. It is also widely used in the packaging industry for producing containers and closures for food and beverage products. In the construction industry, polypropylene HMS is used for producing geotextiles, geofoam, and insulation products. Additionally, it is used in producing toys, sports equipment, and household appliances due to its excellent processability and strength.
7. Biobased Polypropylene
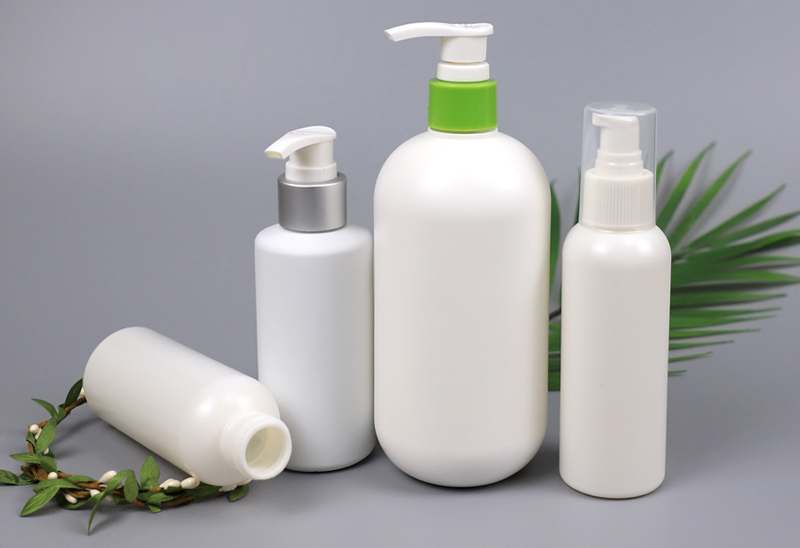
Biobased polypropylene is a thermoplastic material that is derived from renewable biomass sources such as plants, algae, and bacteria. It is produced through the fermentation of biomass feedstocks into monomers that are then polymerized into bio based polypropylene. This process reduces the reliance on fossil fuels and reduces greenhouse gas emissions.
Properties: High stiffness, strength, and superior chemical resistance are all characteristics that bio based polypropylene shares with conventional polypropylene. It also has low density and a slightly lower melting point and thermal stability compared to traditional polypropylene. Biobased polypropylene is biodegradable under specific conditions, making it an environmentally friendly alternative to traditional polypropylene.
Applications: Biobased polypropylene has a wide range of applications in various industries, including packaging, automotive, textiles, and consumer goods. It is commonly used in food packaging, as it is safe for contact with food and can reduce the environmental impact of plastic waste. In the automotive industry, it is used for interior parts and exterior components, such as bumpers and body panels. Biobased polypropylene can also be used for clothing and industrial applications.
We hope this article provides usefulness to you and don’t forget to follow other information on our blog!
Additionally, if you are looking for a reliable supplier of safe PP plastic, EuroPlas is the trusted source. With over 15 years of experience in the industry and a commitment to delivering top-quality materials, we are a reliable partner for manufacturers across various industries. So, don't hesitate to contact us HERE!