Masterbatch is becoming the indispensable material in the 21th century. It's hard to imagine a life without additive masterbatch and because the plastic industry is very important to us, having profound knowledge on additives not only keeps this industry continuously developing but also supports other industries.
Read more: What are plastic additives? 8 most common plastic additives in plastic industry
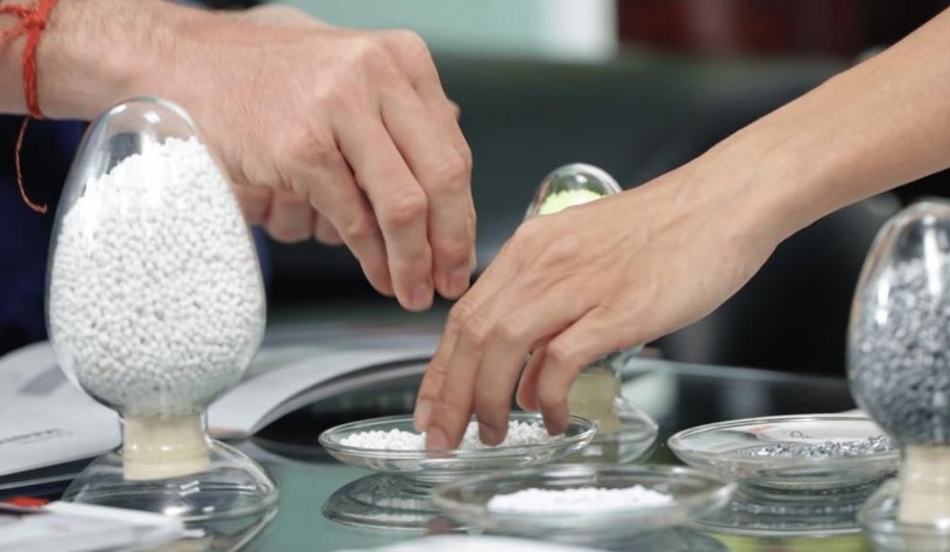
1. What is additive masterbatch and its importance in manufacturing industry?
Plastic additives are an essential element bringing the success to plastic-based products manufacturers and distributors worldwide. A plastic product not only needs a good base resin, but also needs different additives supporting and improving many features of the carrier plastic. Otherwise, that plastic product may not meet the required standards, or may not satisfy the needs of consumers.
So, what is additive masterbatch? According to the specialized definition, this is compound, inorganic or organic, derived from natural or synthetic sources. It will change the initial properties or add new properties to pure plastic. Depending on the requirements of the output product, the manufacturers will mix primary plastic with the additives in a certain amount and then mix these raw materials together through the process of casting, compression and pressing to create masterbatch. This can serve directly as the input material or in combination with other material (for example, wood powder) for making the plastic products through various shaping methods.
Different types of additives when mixed with plastic will give plastic different properties, such as increasing toughness, good insulation, enhanced glossiness, etc. Adding additive masterbatch not only help plastic utensils lighter in volume, but their color is also improved, the quality of final products is also more assured. That's why 90% of plastic-based products manufacturers in the world use additives. Basically, pure plastics are not available with the superior characteristics such as toughness, durability, hardness, etc. Hence, adding functional additives helps the final product to survive during long-term exposure to harsh conditions of the surrounding environment.
2. 7 common additive masterbatch with distinct properties in plastic field
Different types of additives will add different properties to the plastic such as increasing toughness, color retention, insulating, enhancing the glossiness, etc. There are some additives that can only cover one single aspect but there are also some can affect two or more features.
2.1. Additive masterbatch functioning as lubricates
There are 2 types of lubrication additive masterbatch:
- Internal lubricants: limit the friction between the circuits or the high molecular weight circuits of plastic and prevent molten plastic under the catalyst of heat.
- External lubricants: prevent the adhesion between the plastic and the inner surface of the cylinder, screw surface and mold during the injection of plastic into the mold.
In order to create the lubricant, we can use these ingredients: fatty wine, fatty acid, metal soap, paraffin, low molecular polyethylene.
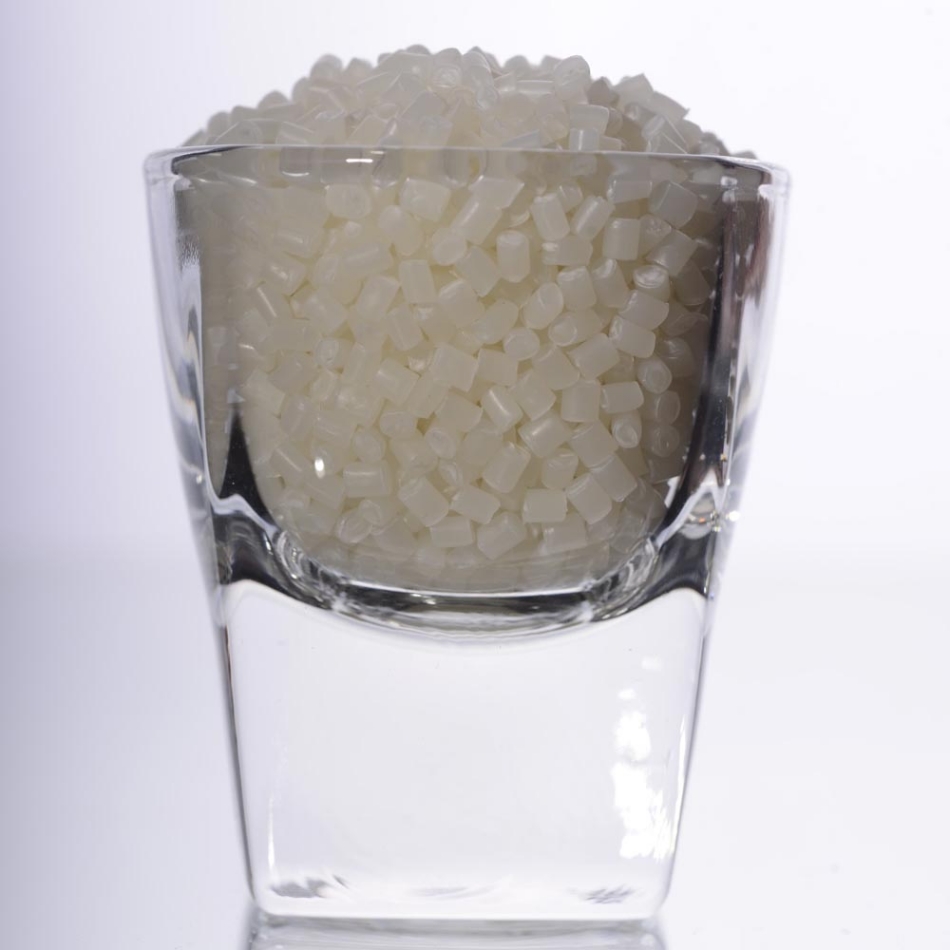
2.2. Plasticized additive masterbatch for more flexible products
This type of additive works to make the input plastic mixture easier to fill the mold, making the polymer circuitry more flexible and easier to melt when heated.
The plasticizer additive masterbatch is made from 2 components: the main plasticizer and secondary plasticizer. The main plasticizers include esters of acid or of alcohol, acids with rings in their structure (Terephtalic, benzoic), long chain acids (Adipic, Azelaic) and both monohydric or polyhydric alcohol. Secondary plasticizers are aromatic oils and chlorinated paraffin and ester.
2.3. Additive masterbatch increase stability to prevent damage for finished products
This additive masterbatch include heat stabilizers, ultraviolet stabilizers, etc., serving with the purpose of preventing plastic from being damaged during machining.
The thermal stabilizer is mainly used for rigid and soft PVC resins, which work to ensure a stable plastic, not decomposed when machining at a melting temperature. To create additive masterbatch with thermal stability, we can use organic substances such as salt, cadmium, calcium, zinc ...
Ultraviolet stabilizer additives use hydroxybenzo, ester of Acrylic acid, hydroxyphenyl, benztriazoles, ... to protect plastics when outdoors must be exposed to the sun for a long time.
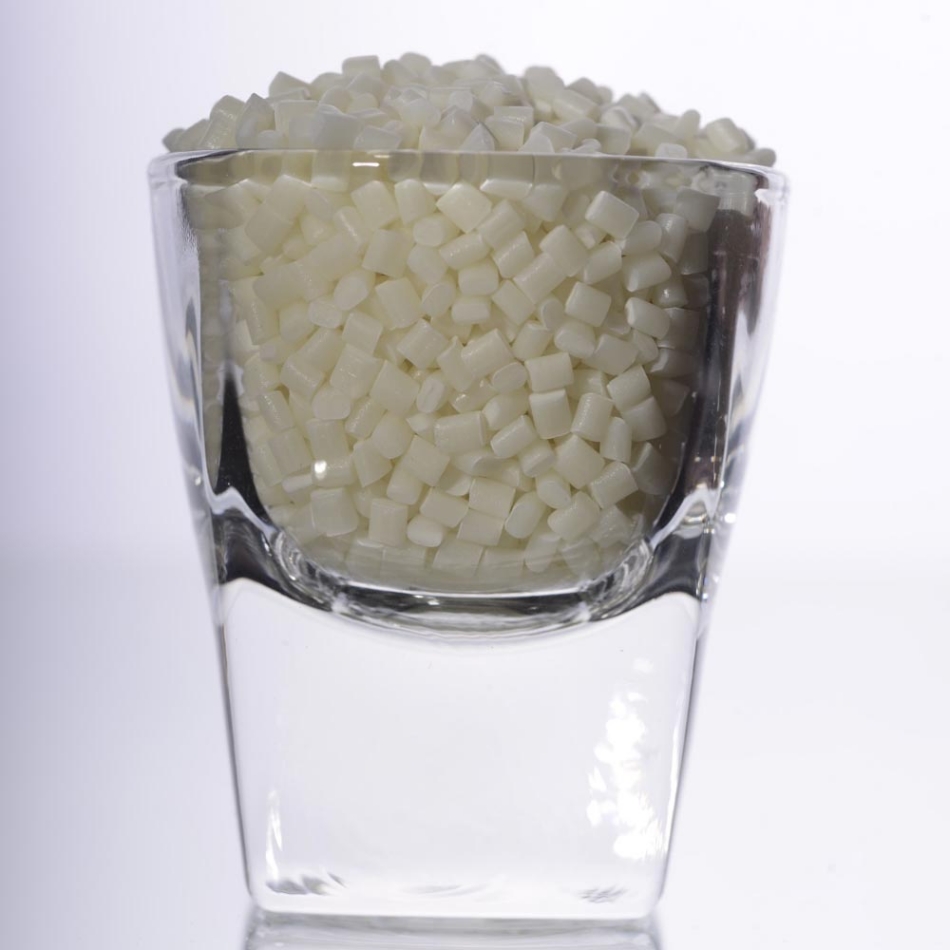
2.4. Anti-aging additives for plastics increases the life time for materials
The anti-aging additives used in masterbatch industry have the ability to widen the limited temperature range for plastics, increasing the lifespan of the plastic so the usage time is longer. This additive works by slowing the development of reactive oxygen or proxide reactions.
The anti-aging masterbatch consist of two types of anti-aging substances including Phenonic, Amine, sulfur or phosphor mixtures.
2.5. Anti-static additive masterbatch helps products less stuck by dust
Anti-static is one of the additives most used by plastic-based products manufacturers. Anti-static plastic additives always include the anti-static agents coming from different source such as inorganic salts, polyhydric alcohols, etc. that will reduce the charge between the masterbatch membrane surface and other surfaces to ensure safety for the production process. At the same time these agents also minimize the suction, dusk-sticking problems when transporting, displaying and during the using time of products.
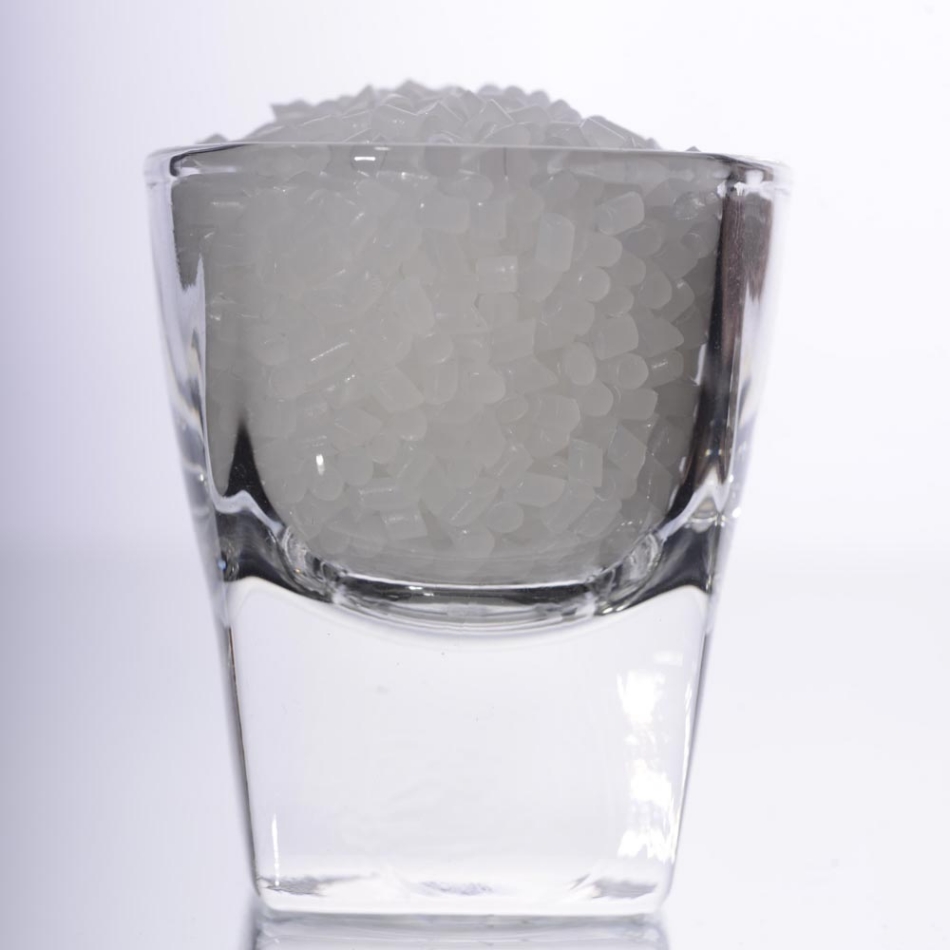
2.6. Fire retardant additives ensure safety during the utility of plastic
The flame-retardant additives work in a way that prevents oxygen on the plastic surface from contacting fire or heat by creating a protective surface layer. Raw materials for the fire retardant masterbatch consist of 2 types: physical effects and chemical effects, often containing aluminum, antimony, boron, bromine, fluorine, molibden, sulfur, nitrogen and phosphor in their compositions.
2.7. Additives increase the porosity for finished products
Using foaming additives is the effective solution for plastic-based products manufacturers to create tiny pores inside the product aiming to reduce volume of required input materials, but still ensure product quality. Output products will be improved heat and sound insulation, increased plastic structure durability and minimized shrinkage and protrusion on plastic surfaces.
Additive masterbatch to increasing the porosity of plastic has 2 types and are categorized based on the type of containing foaming agent:
- Physical foaming agents: compressed nitrogen, liquid CO2 and short-chain fatty hydrocarbons.
- Chemical foaming agents: azodicabonamide (ADC), azisobutylric, benzene, sullfonyl hydazide.
2.8. Additives that deodorize plastic to not make consumers feel uncomfortable
Plastic additives are also used in recyclable products such as children's toys, food bags, stationery, plastic tubes, etc. Products generated from recycled plastics or even primary plastics without this additive will be smelly because the chemicals in the production process will release NH3, C2H4, H2S, etc.
Besides the mentioned additives, plastic-based products manufacturer also uses a lot of other additives (for example the optical brightener, anti-slip masterbatch, plastic processing aids, etc.). The decision of using additives and how much it should be used depends on customers’ requirements.
3. Conclusion
Overall, plastic additives are essential for the plastics industry as they significantly improve the performance, durability, and safety of plastic materials. Moreover, Their wide range of beneficial features and applications across various industries within the plastics sector make them indispensable for shaping the industry.
Hope this reaches you well. For more information and consultation, please feel free to contact us
HERE! Our team at
EuroPlas is ready to assist you.