Welcome to our in-depth exploration of polyethylene (PE) film, a crucial material in the packaging industry that offers protection and efficiency for a wide range of products. If you’re a manufacturer or business owner looking to safeguard your goods during transport or storage, understanding the nuances of PE film is essential. In this article, we will break down the eight key criteria that define safe and high-quality PE film, addressing common pain points such as durability, flexibility, and moisture resistance. Whether you are struggling with packaging failures or seeking to enhance your operational efficiency, this guide will equip you with the knowledge you need to make informed decisions. Let’s dive in and discover how to choose the best PE film for your needs!
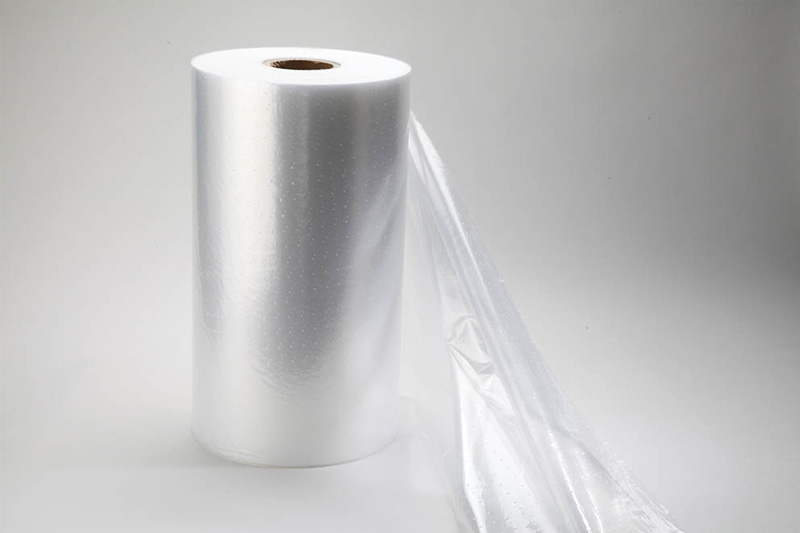
PE film - a crucial material in the packaging industry
1. Overview Of PE Film
Polyethylene (PE) film is a highly versatile material that has become indispensable in various industries due to its remarkable ability to protect goods from environmental factors. This thin, flexible plastic film is widely utilized for its protective qualities, wrapping a broad spectrum of products ranging from food items to industrial goods. The primary function of PE film is to shield these products from external elements such as moisture, dust, and even physical impact, which can compromise the quality and integrity of the contents.
The popularity of PE film among businesses and individuals alike can be attributed to its cost-effectiveness and ease of use. It presents a practical solution for packaging, reducing expenses while maintaining high efficiency. In the current marketplace, PE films are available in a diverse range of options, differing in terms of cost, quality, and specific applications. However, selecting the right film is crucial, as substandard products can significantly undermine the protective function of the film, leading to increased risk of damage and spoilage during transportation.
Read more: Common problems during PE film blowing process
2. Eight Criterias For Safe And High Quality PE Film
For those seeking reliable and durable PE film solutions, understanding the key criteria that define high-quality PE film is essential. Evaluating these criteria ensures that the film will meet the rigorous demands of various applications, providing peace of mind and reliable protection.
2.1. Tensile Strength
Tensile strength is a critical measure of a material's ability to withstand tension without breaking. High-quality PE films exhibit a tensile strength value exceeding 400 kp/cm², which signifies the material's capacity to endure significant stretching forces. This attribute is particularly important for packaging applications where the film must maintain its integrity under stress.
Achieving such durability is dependent on manufacturing processes that utilize unadulterated, pure plastic particles. This ensures that the film retains its strength and flexibility without succumbing to the stressors it might encounter during shipping and handling.
2.2. Tear Strength
Tear strength measures the film's resistance to tearing, which is a vital property in applications where the film is subjected to sharp or abrupt forces. Packaging solutions vary in their tear strength requirements based on their intended use. For instance, while potato chip bags benefit from low tear strength to facilitate easy opening, PE films used in industrial settings demand a higher tear strength. This ensures that the packaging remains intact during long-haul transportation, effectively safeguarding the goods within.
2.3. Resistance To Impact
PE film can be used to protect the goods
The ability of PE film to resist impact is paramount, particularly when it is used to package heavy or bulky items. Impact resistance ensures that the film can absorb and withstand sudden forces or shocks without tearing or breaking, thus providing an additional layer of protection for the goods. This property can be tested by evaluating the force required to pierce or break the film when subjected to a controlled impact, providing a reliable measure of the film's durability in real-world scenarios.
2.4. Flexibility
Flexibility is a defining characteristic of high-quality PE films, ensuring that the material can adapt to a variety of packaging requirements. The film must strike a balance between softness and rigidity; too much hardness can impede its use in packaging machinery, while excessive softness can lead to easy tearing. The ideal flexibility allows the film to conform to different shapes and sizes, facilitating a seamless packaging process that enhances productivity and reduces waste.
2.5. Heat Resistance
Heat resistance is an indispensable feature of PE films, as it determines the material's ability to withstand temperature variations without degrading. During both manufacturing and transportation, films are often exposed to high temperatures, which can cause inferior materials to melt or warp. Conversely, low temperatures can make some films brittle, leading to cracking. A film with good heat resistance remains stable and effective across a wide range of temperatures, ensuring consistent performance regardless of environmental conditions.
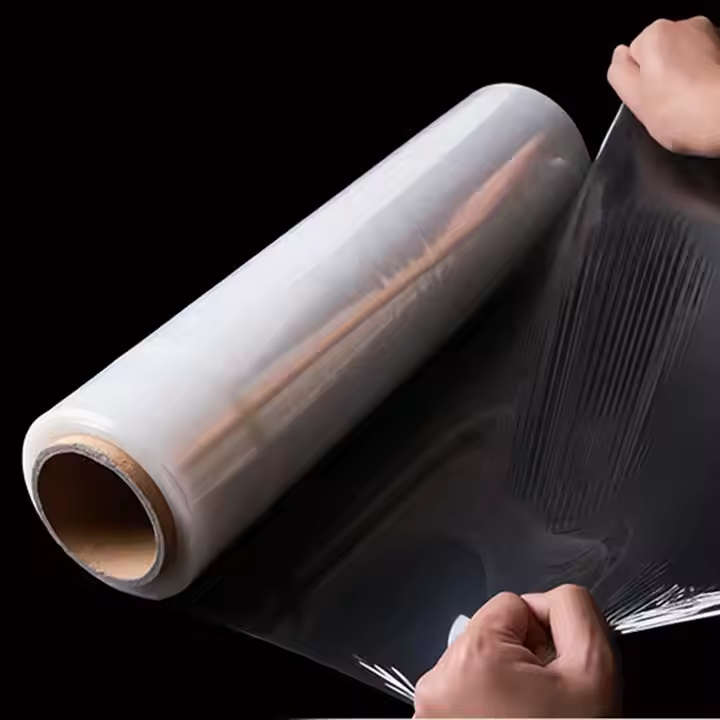
A PE film with good heat resistance
2.6. Opacity
The aesthetic quality of PE film is often judged by its gloss and opacity. High-quality PE films are characterized by a clear, colorless, and odorless appearance. This transparency is not only visually appealing but also indicative of the purity of the materials used in production. Films that exhibit a yellow tint or milkiness often suggest the use of recycled or impure materials, which can detract from the product's presentation and overall quality.
2.7. Moisture Resistance
Moisture resistance is a critical factor in preserving the contents of the package, especially in humid or damp environments. High moisture resistance prevents the ingress of water vapor, thereby protecting goods from mold, spoilage, and other moisture-related damage. This property is particularly important for packaging sensitive items such as electronics, textiles, or food products, where maintaining dryness is essential to preserving quality and extending shelf life.
2.8. Grease Resistance
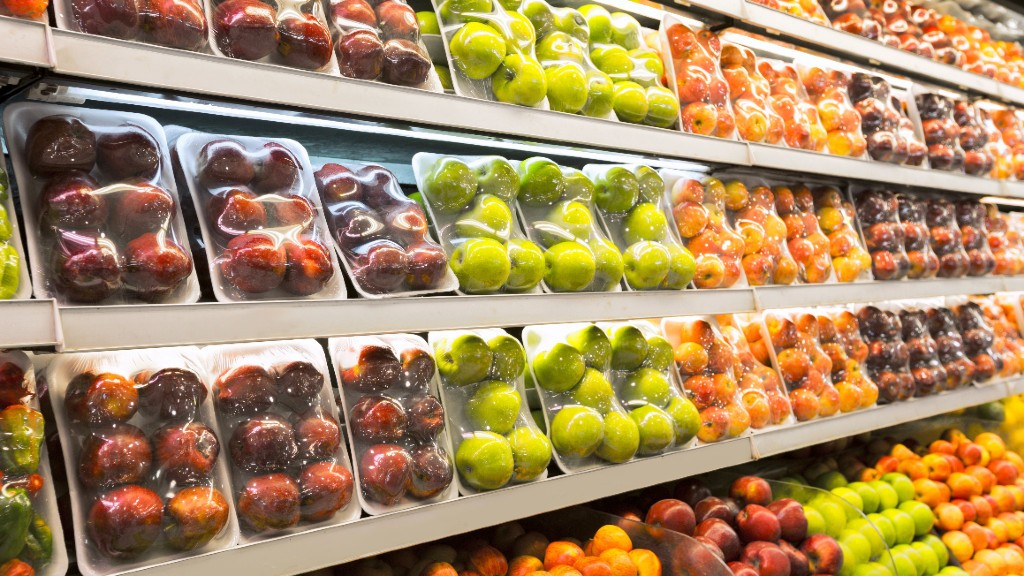
PE film can be applied for food packaging applications
Grease resistance is another key attribute of PE films, especially for applications involving food packaging. The ability to resist grease prevents oils and fats from penetrating the film, which can otherwise compromise the integrity of the packaging and the quality of the goods. Testing for grease resistance involves assessing how well the film repels oily substances over time, ensuring that it maintains its protective qualities in diverse conditions.
3. Conclusion
In conclusion, understanding these eight criteria is vital for selecting a PE film that meets the highest standards of safety and quality. Each criterion plays a crucial role in determining the film's overall performance, ensuring that it can effectively protect and preserve the goods it encases. By prioritizing these criteria, businesses and consumers alike can make informed decisions, selecting PE films that offer maximum efficiency and reliability in their packaging solutions.
4. About EuroPlas’ PE Products
EuroPlas is a global leader in the production and supply of PE filler masterbatch, a high-quality product designed to enhance the performance of plastic manufacturing. Our PE filler masterbatch is expertly formulated from PE resin, CaCO3 powder, and specialized additives such as processing aids and dispersion agents. This innovative combination not only reduces production costs but also significantly improves various properties of end products, including impact resistance, heat resistance, surface hardness, strength endurance, and ductility.
Our PE filler masterbatch is widely used in applications such as injection molding and blown film, resulting in products like shopping bags and T-shirt bags. In the food packaging industry, it serves as an effective replacement for standard PE resins and is also utilized for producing PP woven bags and laminated films. By offering a more cost-effective option, our filler masterbatch enhances the stiffness, flexibility, and thermal resistance of finished goods.
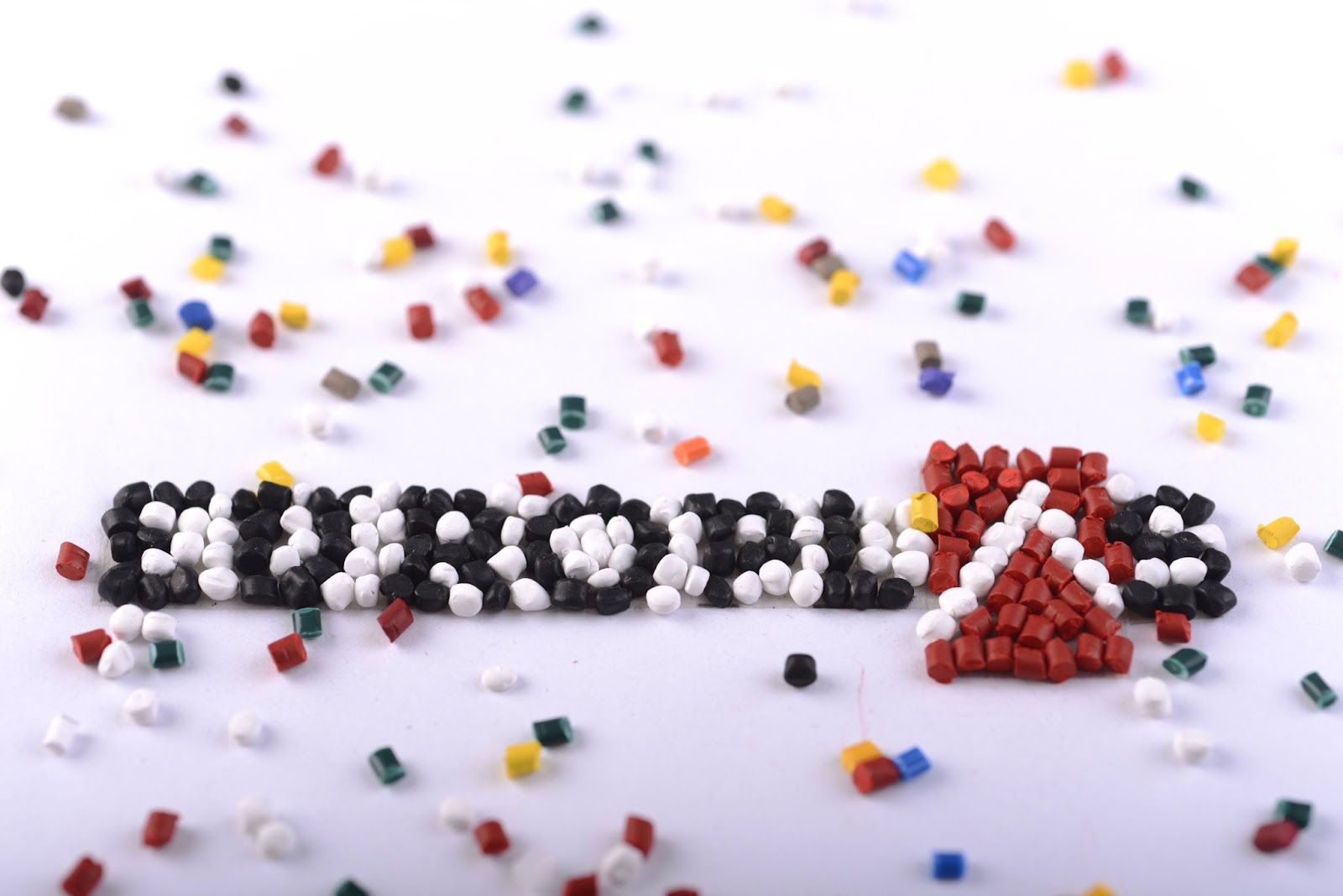
Europlas - A World's Leading PE Film Manufacturer
With over 15 years of experience in the industry, EuroPlas takes pride in providing high-quality and economical solutions to plastic manufacturers worldwide. Discover the features of our PE filler masterbatch, including cost savings, improved brightness and opacity, reduced shrinkage, energy efficiency due to CaCO3's excellent thermal transmission capabilities, and increased manufacturing process stability.
For more information about our PE filler masterbatch and how it can benefit your production needs, please don’t hesitate to reach out. Contact us today!