The transition from metal to plastic parts in various industries, from automotive to aerospace, has gained significant momentum. With the advancements in plastic technology, we are left wondering: Can plastic parts truly replace metal? In this article, we will explore the advantages of using plastic over metal, real-world applications, and how this shift is transforming different sectors.
1. Can Plastic Parts Replace Metal?
The debate over whether plastic parts can fully replace metal has been ongoing for years. With technological advancements, the potential for plastics to surpass metals in some applications is becoming a reality. However, the feasibility depends largely on the specific industry, the function of the part, and the mechanical properties of the materials involved.
Traditionally, metals are preferred for their durability, heat resistance, and high strength. However, the development of advanced polymers now allows plastic parts to offer comparable properties, such as high strength-to-weight ratios, corrosion resistance, and flexibility. These attributes make them suitable for applications where lightweight and cost-efficiency are crucial.
Industries such as automotive, aerospace, and medical devices have increasingly used plastic parts to replace metal in both structural and non-structural applications. For instance, components that do not require high heat resistance but demand lightweight and corrosion-free properties are now made from plastic.
Read more: What is plastic? Everything you need to know about plastic
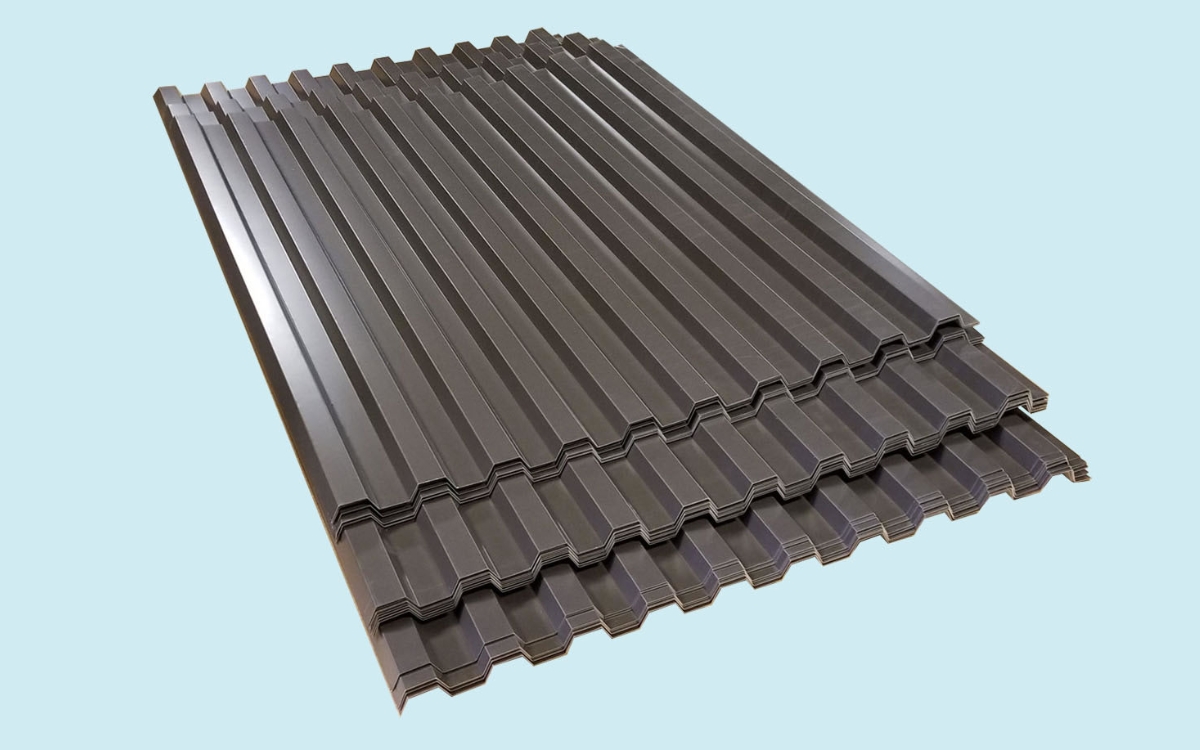
Anti-corrosion plastic sheet made from PVC/ASA plastic
2. The Advantages of Replacing Metal with Plastic Parts
There are several key advantages of using plastic parts instead of traditional metal components:
2.1. Weight Reduction
One of the most significant advantages of plastic parts is that they are considerably lighter than metal. Plastics like polypropylene or polycarbonate weigh much less than steel or aluminum, making them ideal for industries such as automotive and aerospace, where weight reduction directly translates to improved fuel efficiency and reduced emissions.
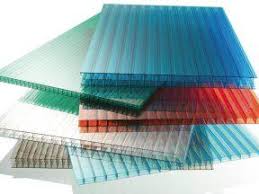
Solid polycarbonate sheet - Skylight roofing sheet
2.2. Cost Savings
Plastic parts generally offer lower production costs compared to metal components. Plastics can be molded into complex shapes much more easily than metals, reducing machining and assembly times. Additionally, the ability to mass-produce plastic components through injection molding or 3D printing contributes to further cost reductions, especially for high-volume manufacturing.
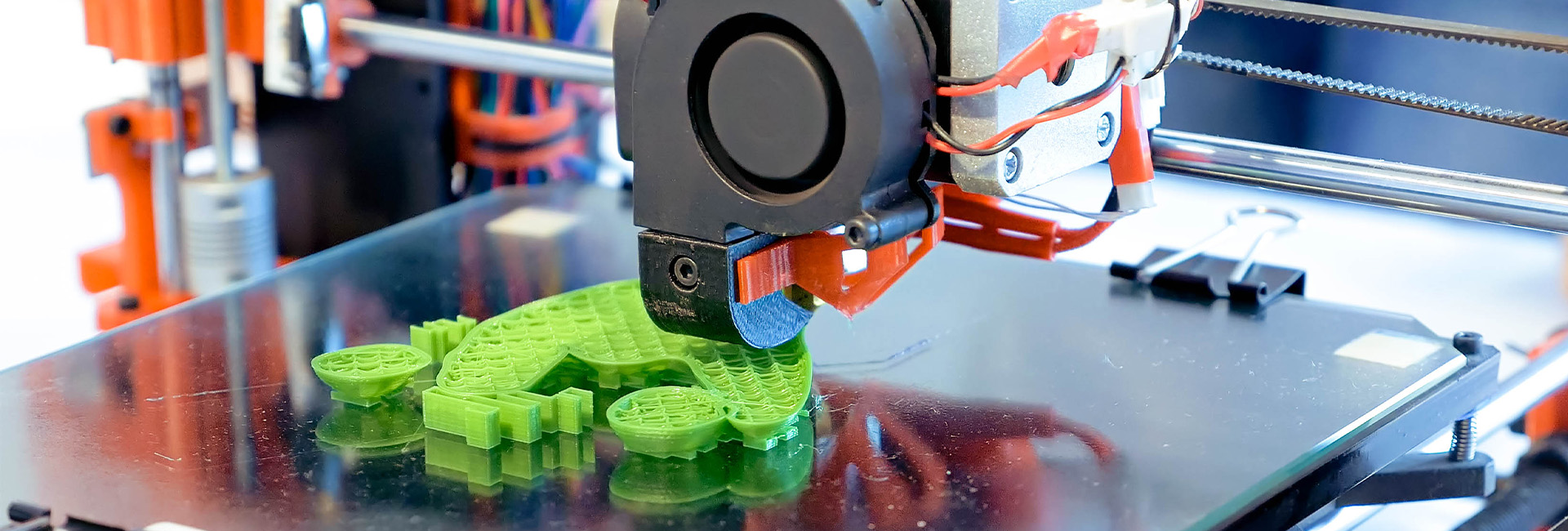
3D Printing - Plastic Parts Reduce Costs
2.3. Corrosion Resistance
Unlike metals, which can corrode or rust over time, plastic parts are naturally resistant to corrosion. This makes plastics particularly advantageous for applications exposed to moisture, chemicals, or saltwater environments, such as marine equipment or plumbing systems.
2.4. Design Flexibility
Plastic parts offer greater flexibility in design. They can be molded into intricate shapes and complex geometries that would be difficult or expensive to achieve with metal. This design freedom allows manufacturers to create more innovative, efficient, and aesthetically pleasing products.
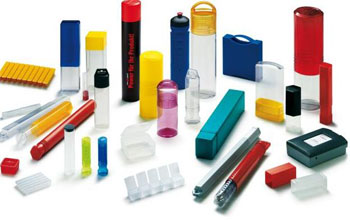
The versatility of plastic components in diverse designs
2.5. Noise Reduction
Plastic parts tend to absorb vibrations and sound better than metal components, making them ideal for applications where noise reduction is crucial, such as automotive interiors or machinery.
2.6. Electrical Insulation
Plastics are excellent electrical insulators, which is why they are often used in electronics and electrical applications. Metal parts, on the other hand, require additional insulation to prevent electrical conduction, adding to production complexity and cost.
3. Examples of Replacing Metal with Plastic Parts
3.1. The Automotive Industry
In the automotive industry, plastic parts have replaced metal in numerous components. Under-the-hood parts like air intake manifolds, fuel tanks, and battery housings are now made from high-performance plastics. These materials not only reduce weight but also resist corrosion and withstand the harsh conditions of the engine bay.
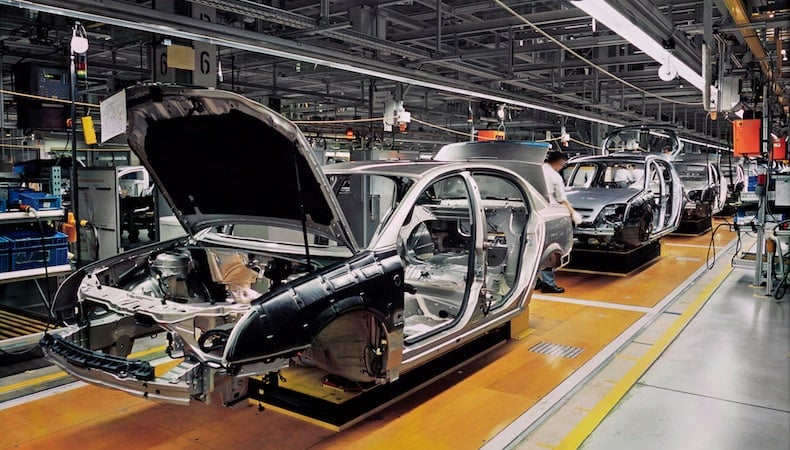
Importance of Nylon in the Automotive Industry
For example, the use of nylon for engine covers helps reduce the overall weight of the vehicle, leading to improved fuel efficiency and lower CO2 emissions. Additionally, plastic fuel tanks are favored over metal ones due to their corrosion resistance and ability to be molded into complex shapes, optimizing space utilization.
3.2. The Aerospace Industry
The aerospace industry has also adopted plastic parts, particularly in non-structural applications. Aircraft interiors, such as seat components, tray tables, and overhead bins, are often made from polycarbonate or composite plastics. These components offer the dual benefits of weight reduction and increased design flexibility.

Plastic parts play an important role in the aviation industry
Moreover, plastic parts in aircraft contribute to fuel savings due to their lighter weight compared to metal components. Aerospace engineers are continually developing advanced plastics that can withstand the extreme conditions of flight while maintaining durability.
3.3. Medical Equipment
In the medical field, plastic parts are widely used in both disposable and long-term applications. Plastics like polyethylene, polypropylene, and silicon are used to manufacture syringes, IV bags, and surgical instruments. These materials are preferred due to their biocompatibility, chemical resistance, and cost-effectiveness for single-use devices.
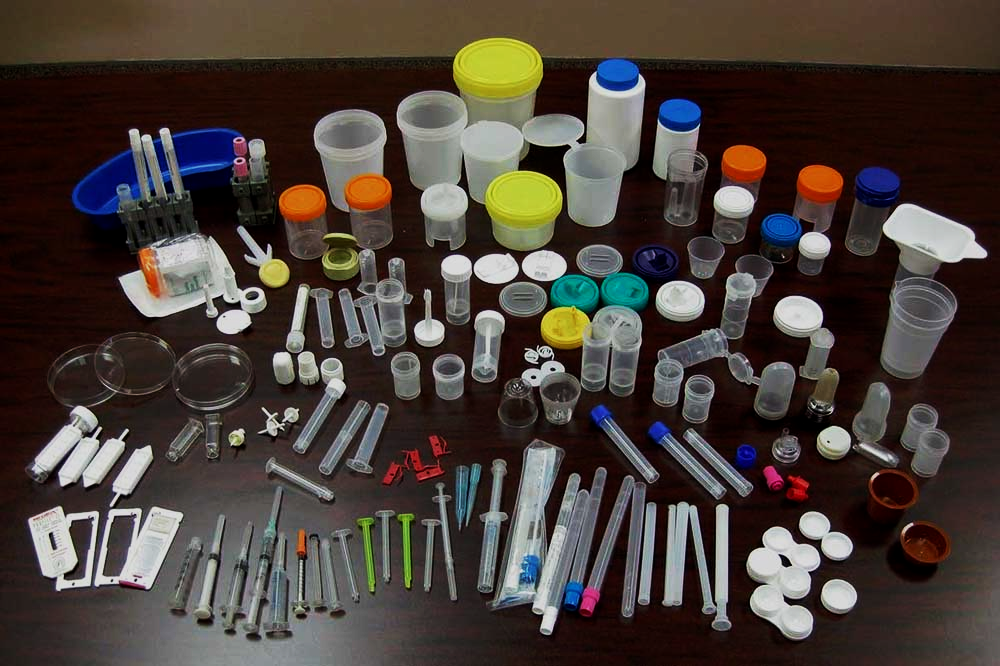
Metal components are all replaced by plastic components in medicine
Metal components in medical equipment are often replaced with plastic to prevent corrosion and reduce weight, especially in devices like prosthetics or implants. The flexibility of plastics also allows for custom designs tailored to individual patients, enhancing the overall treatment experience.
3.4. Consumer Electronics
In consumer electronics, plastic parts have increasingly replaced metal casings and internal components. Mobile phones, laptops, and tablets are now predominantly protected by plastic shells, offering lightweight protection. Plastics also enable slimmer, more ergonomic designs, making modern devices more portable and user-friendly.
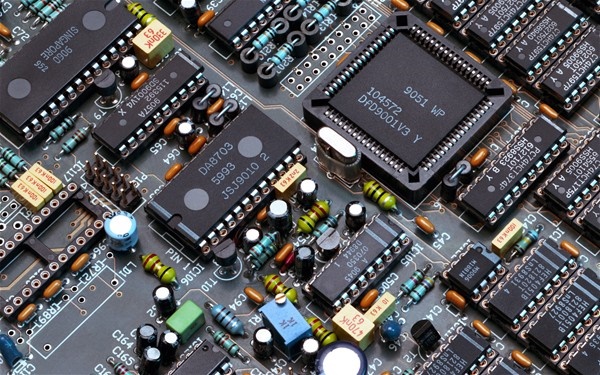
Plastic electrical equipment protects consumers
4. Conclusion
While metals still play a vital role in manufacturing, the trend of replacing metal components with plastic parts is undeniable. Industries like automotive, aerospace, and medical devices have seen significant benefits from weight reduction, cost savings, corrosion resistance, and design flexibility by using advanced plastics. As materials science continues to evolve, plastic parts will increasingly take on a more prominent role in replacing metals, helping to revolutionize manufacturing processes.
For industries looking to optimize performance without sacrificing quality, plastic parts offer a sustainable and viable alternative to metals. With advancements in polymer technology, materials are now available that can surpass metals in several aspects, meeting the growing demands for efficient and sustainable manufacturing in the future.
5. About EuroPlas
EuroPlas products are designed to enhance the mechanical, thermal, and chemical properties of plastic materials. By providing high-quality solutions, EuroPlas helps manufacturers reduce costs, improve product performance, and contribute to sustainability by decreasing the reliance on metals.
EuroPlas is a global leader in the plastics industry, offering a wide range of products, including Filler masterbatch, Color masterbatch, Plastic additives, Engineering plastic compound, Bioplastic compound, Bio filler. Explore advanced plastic solutions at EuroPlas to optimize your production. Contact us today to learn more!