PEEK vs. ABS: What Are The Differences?
In the world of plastics, choosing the right material for your application can be challenging. Two commonly compared plastics, PEEK and ABS, offer unique properties that cater to various industries. In this article, we will explore the differences between PEEK vs. ABS, their advantages, disadvantages, and applications, to help you determine which is the better option for your needs.
1. Overview of PEEK and ABS Plastics
1.1. What is PEEK?
Polyether Ether Ketone (PEEK) is a high-performance, semi-crystalline engineering thermoplastic known for its excellent mechanical strength, chemical resistance, and high-temperature performance. PEEK is widely used in demanding applications such as aerospace, automotive, and medical devices due to its superior thermal stability and resistance to harsh environments.
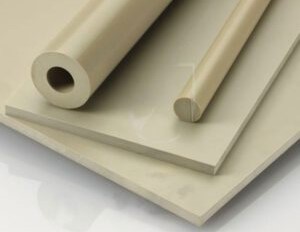
PEEK Plastic - High heat resistant hard plastic
1.2. What is ABS?
Acrylonitrile Butadiene Styrene (ABS) is a thermoplastic polymer well known for its affordability, toughness, and ease of use. ABS is commonly used in everyday products such as automotive parts, consumer electronics, and toys. Its impact resistance, combined with good dimensional stability and ease of processing, makes it an ideal material for many industries.
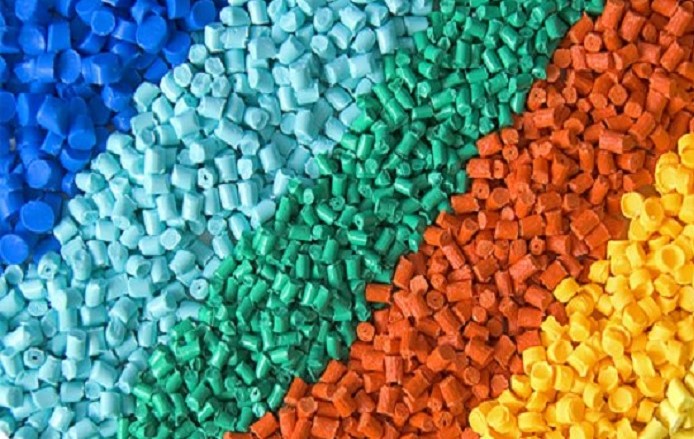
ABS plastic - popular thermoplastic
While both PEEK and ABS are popular choices in the plastics world, they cater to vastly different needs. The following sections will break down the differences between PEEK vs. ABS, from their properties to applications, helping you decide which material is best for your projects.
Read more: ABS plastic - Everything you need to know
PEEK plastic: Definition and Application
2. PEEK vs. ABS: Comparing Properties
When comparing PEEK vs. ABS, it is essential to consider their physical, mechanical, and thermal properties. Here's a closer look at how the two plastics differ:
Criteria |
PEEK |
ABS |
Mechanical Strength |
Very high, including tensile strength, flexural modulus, and impact resistance. Retains stiffness and strength even at elevated temperatures |
Good mechanical strength, but not on par with PEEK under high-stress conditions. However, it is durable enough for everyday applications. |
Temperature Resistance |
Withstands temperatures up to 260°C (500°F) without losing mechanical properties, ideal for high-temperature applications. |
Withstands temperatures up to 80°C (176°F) before deforming. Limited use in high-temperature environments. |
Chemical Resistance |
Exceptional chemical resistance to many chemicals such as acids, bases, and organic solvents. |
Moderate chemical resistance, more susceptible to degradation from certain chemicals like organic solvents and strong acids. |
Weight and Density |
Lightweight, with a density of around 1.30 g/cm³, ideal for weight reduction applications like aerospace and automotive. |
Lighter, with a density of approximately 1.04 g/cm³. Suitable for weight-sensitive applications where high performance isn't critical. |
Electrical Insulation |
Excellent electrical insulating properties, suitable for high-performance electrical and electronic applications, even at high temperatures. |
Good electrical insulation, though not as effective as PEEK in high-temperature or high-voltage environments. Commonly used in consumer electronics. |
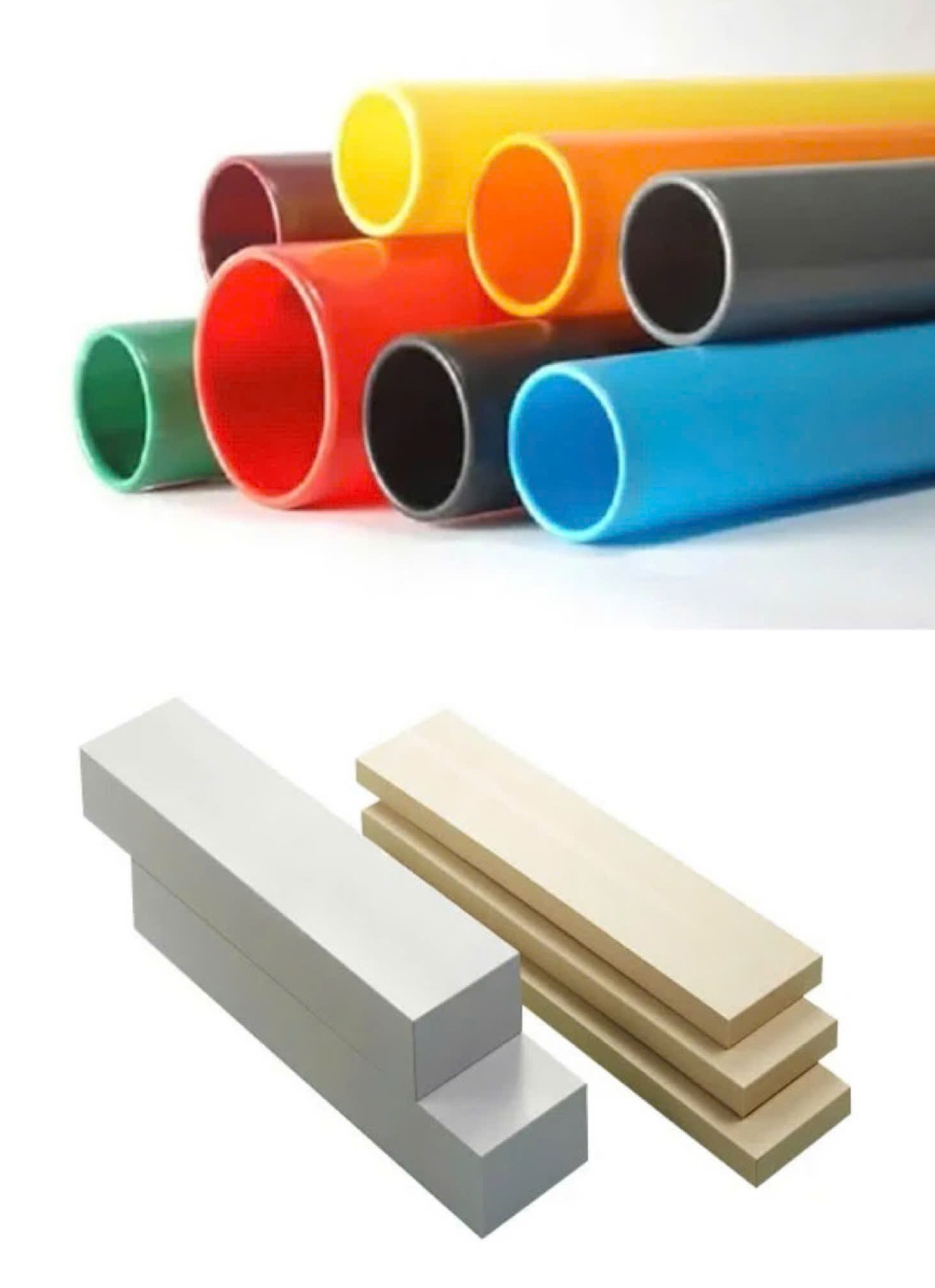
Properties of PEEK vs. ABS plastics
3. PEEK vs. ABS: Pros and Cons
Criteria |
PEEK |
ABS |
Advantages |
- Superior mechanical strength and stiffness
- High-temperature resistance
- Excellent chemical resistance
- Excellent electrical insulation
- Good dimensional stability
|
- Affordable and cost-effective
- Easy to process and mold
- Good impact resistance
- Versatile and suitable for many industries
- Available in many colors and finishes |
Disadvantages |
- Higher cost compared to other plastics
- More difficult to process due to high melting point
- Limited color options |
- Limited heat resistance
- Lower chemical resistance
- Brittle at very low temperatures |
4. PEEK vs. ABS: Comparing Applications
Both PEEK and ABS are used across a variety of industries, but their applications differ based on their distinct properties. Let’s look at where these materials are typically employed.
4.1. PEEK Applications:
- Aerospace: PEEK is often used in aircraft components due to its high strength-to-weight ratio and resistance to extreme temperatures.
- Automotive: In the automotive industry, PEEK is used for high-performance engine parts, fuel systems, and other components that need to withstand heat and chemicals.
- Medical Devices: PEEK is biocompatible, making it suitable for medical implants and devices that require sterilization and durability.
- Oil and Gas: PEEK’s chemical resistance and durability make it ideal for use in oil exploration equipment and pipelines.
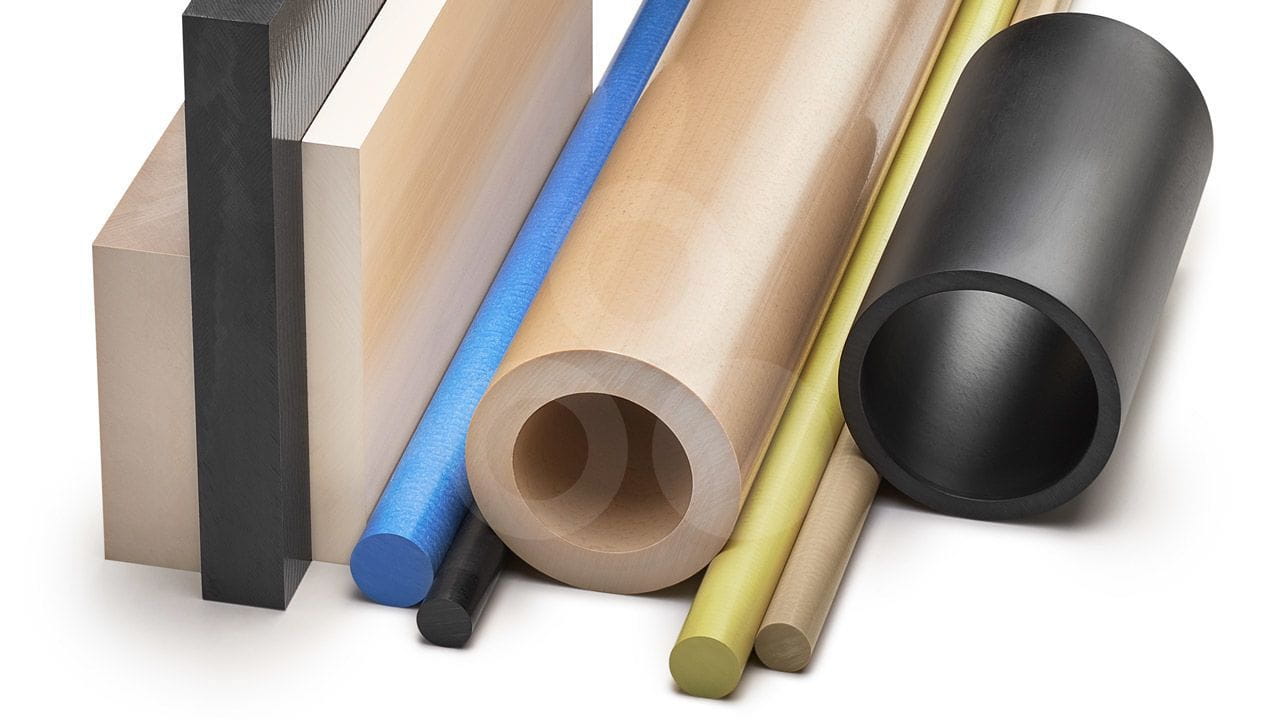
PEEK plastic with good heat resistance is indispensable for the above industries
4.2. ABS Applications:
- Consumer Electronics: ABS is used in housings for electronics, such as computers, televisions, and smartphones, due to its ease of molding and good impact resistance.
- Automotive Interiors: ABS is widely used for interior components in vehicles, such as dashboards and trim, thanks to its low cost and ease of manufacturing.
- Toys: ABS is a popular choice for manufacturing toys, including LEGO bricks, because of its toughness and ability to be molded into complex shapes.
- Household Appliances: ABS is commonly used in small household appliances, like vacuum cleaners and kitchen gadgets, due to its good aesthetic properties and durability.
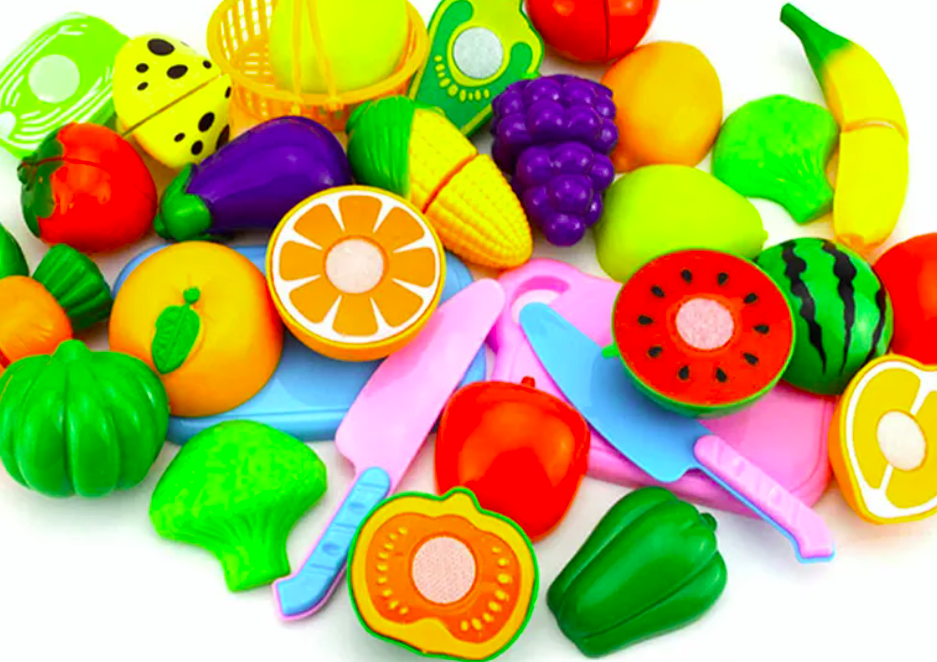
ABS plastic is widely used in the production of children's toys
5. Which Plastic Should You Use?
When deciding between PEEK vs. ABS, consider the specific requirements of your application. If your project demands high performance in terms of mechanical strength, temperature resistance, and chemical resistance, PEEK is the superior choice. However, if cost and ease of manufacturing are primary concerns, and the application doesn’t require extreme durability or temperature resistance, ABS is a more practical option.
- Choose PEEK if you need a material that can withstand high temperatures, harsh chemicals, or mechanical stress. Its higher cost is justified by its outstanding performance in demanding environments.
- Choose ABS if you’re looking for an affordable, versatile material that’s easy to process and offers sufficient durability for general-purpose applications.
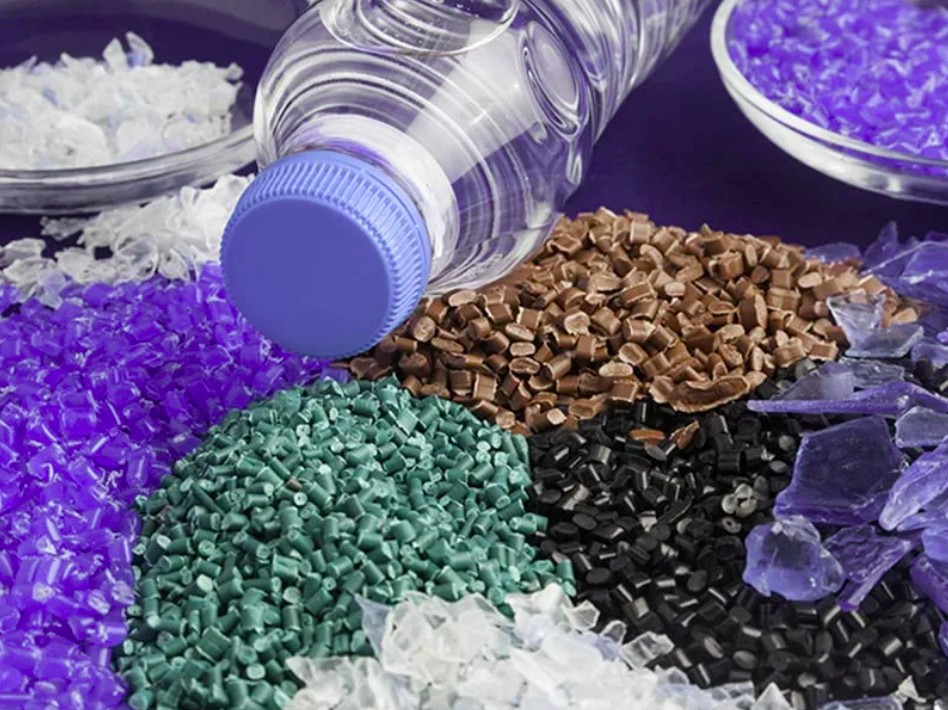
ABS plastic is widely used in life
6. Conclusion
In the PEEK vs. ABS comparison, both materials offer unique advantages that cater to different needs. PEEK is a high-performance plastic ideal for demanding applications in aerospace, automotive, and medical industries, while ABS is a more economical option suitable for everyday products like electronics and automotive interiors. Understanding the strengths and limitations of each material is crucial for selecting the right one for your specific requirements.
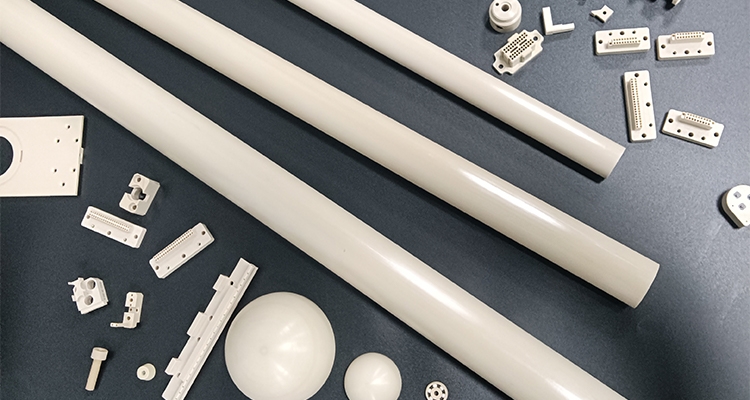
PEEK plastic with high demand in special industries
7. About EuroPlas' ABS Plastics
EuroPlas plays a pivotal role in this transformation by providing innovative plastic solutions that enhance material properties and reduce production costs. Through a comprehensive range of products—including Filler Masterbatch, Color Masterbatch, Plastic Additives, Engineering Plastics Compounds, Bioplastic Compounds, and Bio Filler —EuroPlas helps manufacturers optimize their processes and replace more costly materials. By embracing automation and advanced materials, businesses can stay competitive and thrive in an evolving market.
Contact us today to discover how our advanced plastic solutions can elevate your business and deliver outstanding benefits. For more information, visit our blog to explore other helpful topics!