Polyvinyl chloride (PVC) is one of the most widely used thermoplastics globally, known for its versatility in applications ranging from pipes and flooring to cables and medical devices. A key property that influences how PVC is processed and performs in these end products is its melting point. This article explores the typical PVC melting point, how it differs from traditional melting behavior, and why it matters in practical product design and manufacturing.
Read more:
1. What Is PVC Melting Point?
1.1. Definition and Basic Concept
The PVC melting point is one of the fundamental factors in determining the thermal properties of the material. For PVC, the melting point is the temperature at which the material begins to transition from a solid to a liquid state. Unlike metals, the PVC melting point of thermoplastics like PVC is not a fixed value. Instead, it depends on various factors, including the polymer structure and the additives used in production.
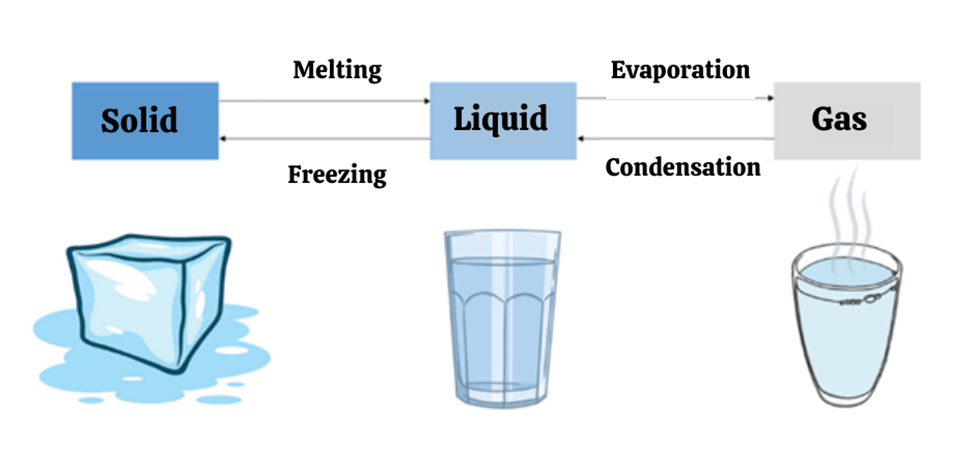
Melting state of PVC
PVC is unique compared to many thermoplastics because it does not exhibit a sharp melting point. Instead, it softens over a temperature range. Typically, rigid PVC starts to soften around 75–105°C and reaches a processing temperature range of 160–200°C, depending on its formulation. Flexible PVC, which contains plasticizers, softens at lower temperatures.
This softening range rather than a single PVC melting point means that manufacturers must carefully control heating during production to avoid degradation while achieving the desired shaping properties.
1.2. Thermoplastic Properties of PVC
PVC belongs to the group of thermoplastics, meaning it can be melted and cooled multiple times without losing its basic properties. The PVC melting point is crucial because it allows PVC to be remelted and continuously processed, optimizing production processes, minimizing material waste, and ensuring consistency in final products.
The thermal stability of PVC, influenced by the PVC melting point, also plays a vital role in maintaining the mechanical and chemical properties during processing. This ensures that the final product is of high quality and meets stringent technical standards.
2. The Role of PVC Melting Point in Product Manufacturing
2.1. Thermal Stability in Processing
One of the most important factors in ensuring the quality of the final PVC product is controlling temperature during processing. The PVC melting point plays a decisive role in adjusting processing parameters, directly affecting the quality and durability of the product.
If the processing temperature is not precisely controlled around the PVC melting point, issues such as thermal deformation, cracking, or other defects may occur. Particularly for products requiring chemical resistance or use in high-temperature environments, the PVC melting point and its associated thermal stability are critical to ensuring the product retains its essential features throughout its lifecycle.
For example, during the production of PVC water pipes, maintaining a precise PVC melting point is necessary to ensure the pipes do not deform or crack during installation or use. Any failure in controlling the PVC melting point could lead to significant economic losses during production.
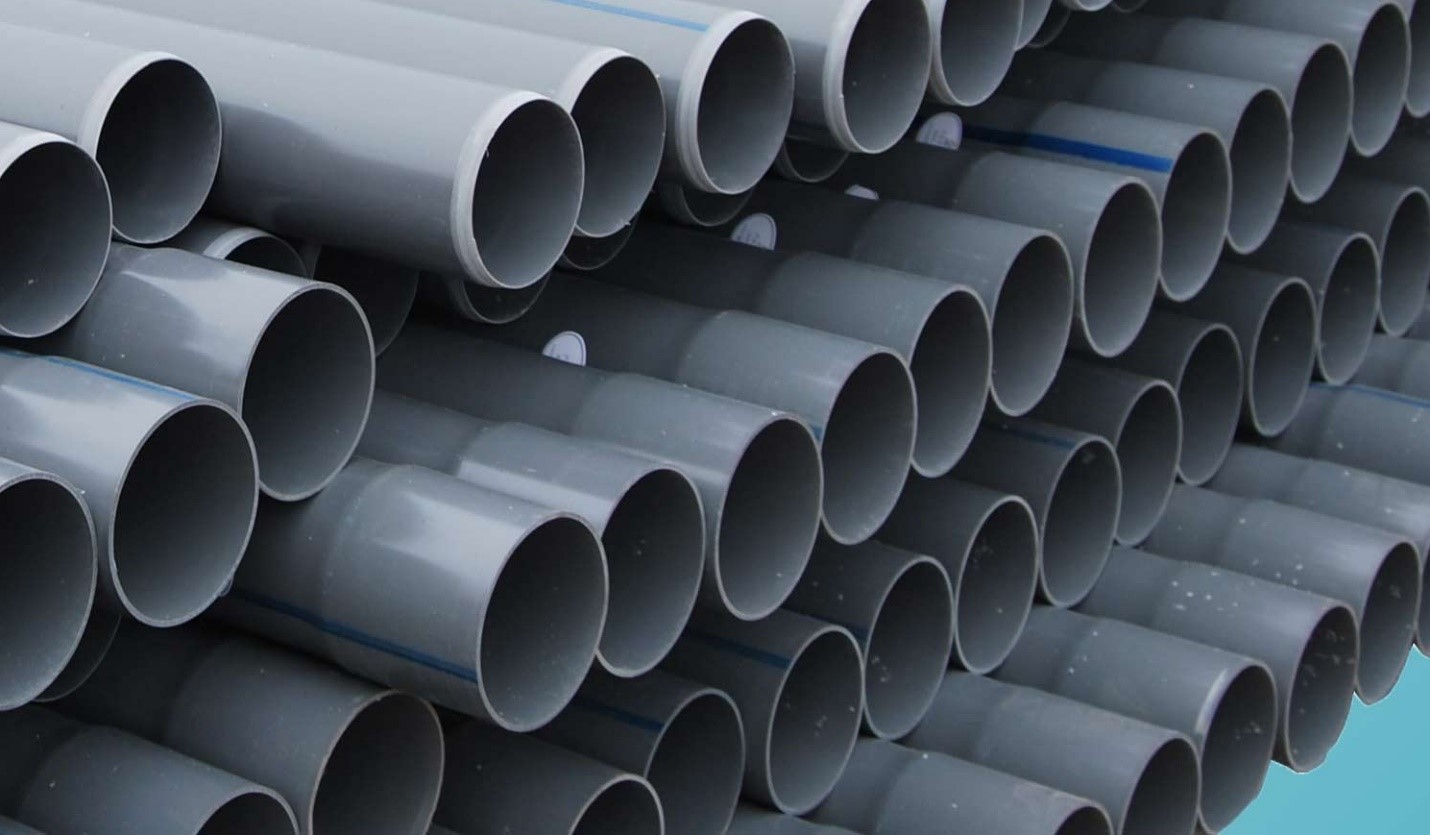
PVC water pipe
2.2. Optimizing Production and Product Efficiency
Understanding and controlling the PVC melting point not only ensures the quality of the final product but also helps optimize the manufacturing process. When the PVC melting point is controlled effectively, production time is minimized, increasing efficiency and reducing costs. This is particularly important for industries requiring large and continuous production.
Maintaining a stable PVC melting point helps minimize material waste during production. With the ability to be remelted and processed multiple times, PVC provides high flexibility, and controlling the PVC melting point helps manufacturers significantly reduce costs. Moreover, this flexibility ensures that PVC products can be easily adjusted to meet the strict demands of various industries.
3. Applications of PVC and How Melting Point Influences Them
3.1. Applications in the Construction Industry
PVC plays a key role in the construction industry, where it is used to produce products such as water pipes, roofing sheets, windows, and insulation materials. The PVC melting point directly affects the durability of these products under harsh environmental conditions, including high temperatures and chemical exposure.
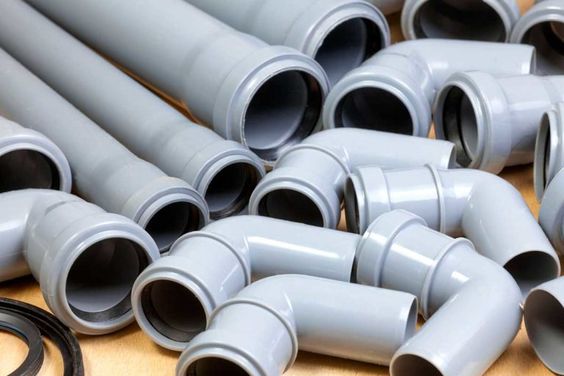
Plastic pipe
In construction, PVC products like water pipes must ensure high thermal stability to withstand pressure and temperature fluctuations without cracking or deforming. The PVC melting point ensures that these products have a long lifespan, reducing maintenance and replacement costs for construction projects.
3.2. Applications in the Electronics Industry
In the electronics industry, cables and insulation rely on well-calibrated softening points to maintain flexibility and heat resistance. That is why PVC is often used as insulation for electrical cables and other components, where safety and durability are crucial. The PVC melting point must be tightly controlled to ensure that the product does not deform or fail when exposed to high temperatures during the operation of electronic devices.
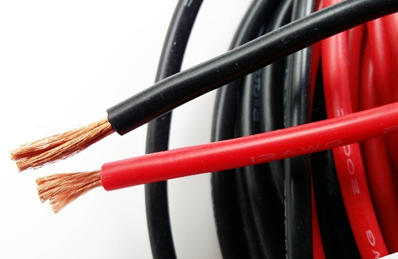
Plastic covering the wire
Additionally, the thermal stability derived from controlling the PVC melting point ensures that electronic products can resist chemical and environmental factors, enhancing the durability and safety of electrical systems.
3.3. Applications in the Medical Industry
In the medical sector, items such as IV tubing and blood bags demand high precision in melting and sealing. A minor deviation in thermal settings can compromise both product integrity and patient safety. Therefore, familiarity with PVC’s thermal transition range is indispensable for ensuring compliance with industry standards and patient wellbeing.
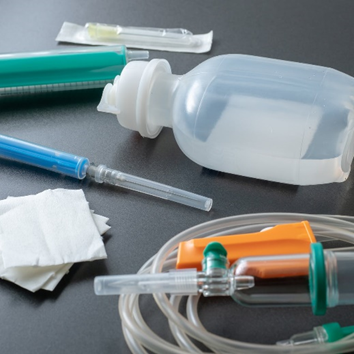
Medical plastic
For example, during the production of IV bags, controlling the PVC melting point is a key factor to ensure that the final product does not deform or become contaminated, thus ensuring the safety and effectiveness of patient care.
4. Effect on final product performance
The way PVC is processed—especially how heat is managed relative to its melting behavior—plays a critical role in the final product’s performance. Proper control of the PVC melting point during manufacturing ensures that the polymer reaches optimal fusion, which results in smooth surface finishes, precise dimensional accuracy, and enhanced mechanical strength. For instance, in multi-layered products or molded components, uniform melting enables better interlayer bonding and reduces the risk of warping.
On the other hand, if the processing temperature is too low, the PVC granules may not fully fuse, leading to weak joints, rough surfaces, or brittleness. Conversely, excessive heating can cause thermal degradation, leading to discoloration, embrittlement, or even structural failure. This balance between softness for shaping and avoidance of decomposition is one of the most important aspects of working with PVC in any product line.
5. Conclusion
In summary, the PVC melting point is a crucial factor in ensuring the quality, efficiency, and applicability of the material. Understanding and accurately controlling the PVC melting point helps optimize the production process, ensuring that PVC products meet the stringent standards of various industries. PVC not only offers durability and flexibility but also possesses exceptional chemical resistance, enhancing product efficiency and reliability in fields such as construction, electronics, and healthcare.
6. About EuroPlas
With years of experience in providing plastic solutions, EuroPlas is proud to be a leading supplier in Vietnam of high-quality plastic products and services. We offer a wide range of products, including Filler masterbatch, Color masterbatch, Additives, Bioplastics, Biofillers, and Engineering plastics compound. Each of these products is designed to enhance performance, reduce costs, and provide sustainable solutions for manufacturers. We are committed to helping our customers optimize their manufacturing processes, ensuring that the final product always meets the most stringent technical requirements.
Contact us today for expert advice and discover advanced plastic solutions. Let us help you optimize production and meet all your technical requirements efficiently!