In the modern manufacturing landscape, colour masterbatch plays a pivotal role in ensuring consistent and vibrant colors for various products, from packaging to automotive components. However, maintaining color consistency across production batches is no small feat. It requires a blend of technical expertise, high-quality materials, and advanced technology. This consistency is essential for ensuring product quality, maintaining brand identity, reducing operational costs, and fostering customer loyalty. This article delves deep into why color consistency is crucial, the methods to achieve it, the role of technology, and how industry leaders like EuroPlas are setting the standard for excellence.
1. Why Colour Consistency in Masterbatch is Important
1.1. Uniformity Across All Products and Batches
Color consistency is crucial to ensure uniformity across all products. Variations between batches or within the same batch can diminish a product's appearance and harm its market reputation.
For example, a washing machine manufacturer must ensure the same shade of white for every unit to maintain customer trust. Similarly, unevenly colored packaging can make a brand seem unprofessional. High-quality colour masterbatch ensures accurate color reproduction across production cycles, maintaining consistent visual standards for all products.
.png)
High quality color masterbatch will help create accurate colors
Read more:
Different kinds of color masterbatch you should know
What is color masterbatch and how was masterbatch produced?
1.2. Strengthening Brand Recognition
Color is often the first thing a customer notices about a product. Brands like Coca-Cola, Tiffany & Co., or IKEA have signature colors deeply ingrained in their identities. Any variation in these colors could weaken the brand's recognition and confuse consumers.
For manufacturers relying on colour masterbatch, consistency ensures that brand colors remain unaltered across all product applications, from packaging to marketing materials. Even slight deviations can harm the overall brand image, particularly for premium or luxury products where aesthetics play a crucial role.
1.3. Minimizing Production Waste and Costs
Production inconsistencies lead to waste—not just in terms of materials but also time and energy. Products with defective coloring often need to be scrapped or reprocessed, resulting in unnecessary resource consumption. In industries where tight margins are essential, such inefficiencies can severely impact profitability.By adopting a
dvanced colour masterbatch solutions and implementing stringent quality controls, manufacturers can drastically reduce waste. Consistent production means fewer rejected batches, lower rework costs, and a smoother production flow.
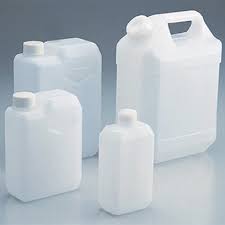
Uniformity in production will help reduce costs
1.4. Enhancing Consumer Satisfaction and Loyalty
Customers expect products to deliver consistent quality. Whether it's a set of vividly colored plastic utensils or automotive interiors, visible inconsistencies in color can lead to dissatisfaction. In markets with intense competition, such dissatisfaction often results in negative reviews or lost customers.
Using consistent colour masterbatch, manufacturers not only meet customer expectations but also build trust and loyalty. Happy customers are more likely to recommend a product, further boosting the brand’s reputation and market share.
1.5. Meeting Industry Standards
In industries like pharmaceuticals, food packaging, and automotive, stringent regulatory standards demand uniformity in every aspect, including color. Deviations could lead to non-compliance and result in significant penalties or product recalls.
By ensuring color consistency with high-performance colour masterbatch, manufacturers not only adhere to these regulations but also enhance their reputation as reliable industry leaders.
.jpg)
Color uniformity will meet industry standards
2. Methods to Ensure Consistency
Ensuring color consistency in colour masterbatch production involves a combination of precise formulation, high-quality raw materials, standardized manufacturing processes, rigorous testing, and skilled workforce management. Each of these elements works together to create a final product that consistently meets the exact color specifications, no matter the scale or complexity of the production process.
2.1. Precise Formulation and Recipe Development
The backbone of consistent color in colour masterbatch production is the precise formulation of the recipe. A carefully developed recipe defines the exact proportions of pigments, resins, and additives that must be used to create the desired color. This careful formulation process allows manufacturers to replicate the same color in each batch, regardless of changes in production size or conditions.
To ensure the formulation remains consistent, advanced tools like spectrophotometers and colorimeters are essential. These tools help fine-tune the formulation by providing accurate data on the color properties of the masterbatch. By using these instruments, manufacturers can make adjustments to the formulation as needed to align with the target color specifications. This scientific approach minimizes the risk of color deviations caused by manual errors or inconsistencies in the mixing process. Additionally, formulations are often standardized within a company, ensuring that the color matches the original recipe in future productions.
By meticulously managing the formulation process, manufacturers can ensure that the colour masterbatch will consistently meet the desired color expectations, providing reliable and repeatable results in every production cycle.
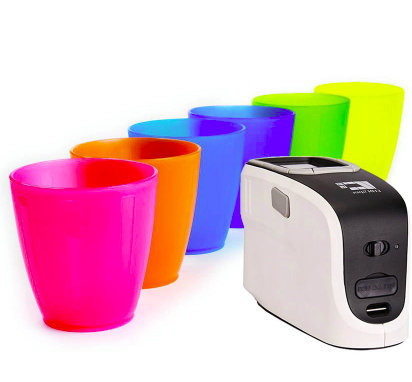
That machine color spectrum helps provide accurate data
2.2. Use of High-Quality Raw Materials
The quality of raw materials used in colour masterbatch is another critical factor in ensuring consistent color. The pigments, resins, and additives must be of the highest quality to maintain uniformity in the final product. Inferior pigments can lead to a number of issues, such as color degradation over time, poor dispersion, or inconsistent reactions when exposed to heat or pressure during processing. These issues can result in visible color variations and poor overall product quality.
To mitigate these challenges, manufacturers must source their raw materials from trusted and reliable suppliers who meet strict quality standards. It is essential to thoroughly vet suppliers and perform regular quality checks to ensure that the materials are consistently high-quality. This process includes testing pigments for stability and ensuring that resins do not degrade or react unexpectedly under processing conditions.
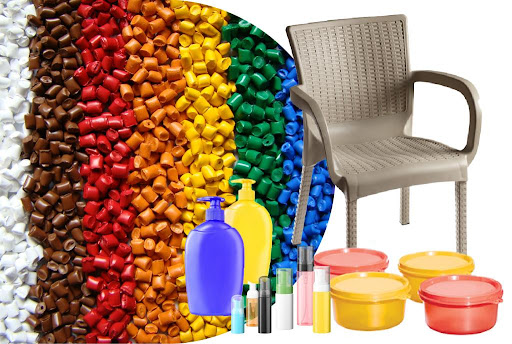
High quality raw materials will help ensure consistent product color
Investing in premium-quality pigments and resins is key to producing vibrant, durable, and consistent colour masterbatch. High-quality raw materials help prevent issues like uneven pigment dispersion or fading over time, resulting in a more reliable final product that can withstand varying environmental conditions, ensuring its color stays true even with prolonged exposure to light, heat, or stress.
By using the best available materials, manufacturers can enhance the overall quality of their colour masterbatch, contributing to consistent color performance across a range of applications.
2.3. Standardized Manufacturing Processes
Standardizing manufacturing processes is essential for achieving uniformity in colour masterbatch production. Parameters such as temperature, pressure, mixing speed, and extrusion time must be carefully monitored and regulated throughout the production cycle. Consistent control over these variables ensures that each batch of colour masterbatch maintains the desired characteristics, preventing color variations from batch to batch.For example, precise control over the mixing temperature is crucial to achieving even dispersion of pigments within the polymer matrix. If the temperature is too high or too low, pigments may not fully dissolve or disperse evenly, leading to streaks or blotches in the final product. Standardized processes, which are often supported by automated control systems, allow for tighter tolerances, ensuring that each batch of colour masterbatch performs to specification.
.png)
Standardize the production process to achieve uniformity in colour masterbatch production
Manufacturers also use state-of-the-art machinery, such as twin-screw extruders, which provide consistent mixing and shear forces. These machines allow for precise control of the extrusion process, ensuring uniform distribution of pigments and additives in the final colour masterbatch. Twin-screw extruders, for example, are capable of processing various resins and pigments more efficiently, improving color consistency even in large-scale production environments.
By maintaining standardized processes, manufacturers reduce the risk of human error and ensure that every batch of colour masterbatch adheres to the same high-quality standards.
2.4. Comprehensive Testing and Inspection
Rigorous testing and quality inspection are essential to guarantee that the colour masterbatch produced meets the required specifications for color consistency. Testing begins at the formulation stage, where samples are analyzed using advanced tools such as spectrophotometers. These devices measure the color properties of the sample with extreme precision, comparing them against predefined color standards. Any discrepancies or variations that are detected during this stage can be corrected immediately, before the production process continues.
In addition to spectrophotometric analysis, visual inspections are also an integral part of the quality control process. These inspections take place under carefully controlled lighting conditions to ensure that the color appears consistent and meets the required specifications. Sometimes, color variations are not detectable through machines alone and must be assessed visually to ensure the product looks as expected in real-world conditions.
Periodic testing throughout the manufacturing process will help create uniformity between products
Moreover, colour masterbatch samples undergo regular batch testing throughout the production cycle to verify consistency across different production runs. This ongoing testing process ensures that even if production scales up or materials are adjusted, the final product maintains uniform color performance. Regular quality checks also help to identify any potential issues early on, allowing manufacturers to take corrective action before they impact the entire production batch.
Comprehensive testing ensures that every batch of colour masterbatch maintains the same high level of quality and that any deviations from the color standards are identified and addressed promptly.
2.5. Employee Training and Expertise
While the latest tools and technologies play a crucial role in achieving consistent color, human expertise remains an irreplaceable asset in the colour masterbatch production process. Skilled technicians and operators are essential in identifying potential issues that may not be immediately apparent, such as slight color shifts caused by temperature fluctuations or subtle variations in pigment dispersion.
Regular training programs for employees are vital to ensuring they are familiar with the latest industry practices, technologies, and quality control techniques. Knowledgeable workers can better assess the production process and make informed decisions to address problems, ensuring that colour masterbatch production stays on track.
.png)
Experienced staff training will contribute to the production process
Additionally, experienced employees contribute to troubleshooting and improving the manufacturing process. They can offer valuable insights into improving formulations, adjusting parameters for better consistency, and finding innovative solutions to challenges in color production. Ensuring that employees are well-trained and knowledgeable about best practices improves the overall quality of the colour masterbatch and enhances consistency across batches.
Training and expertise in the workforce, combined with the latest technology, result in a more robust and reliable color production process, which leads to consistent, high-quality colour masterbatch every time.
3. Role of Technology in Colour Masterbatch Consistency
3.1. Automation in Manufacturing
Automation revolutionizes the production of colour masterbatch by enhancing precision, consistency, and efficiency. Automated systems eliminate human error in tasks like pigment measurement and material feeding. Features such as automated feeders and self-regulating extrusion machines ensure accurate pigment dispersion and consistent color outcomes across large-scale production.
Furthermore, automation boosts operational speed, enabling continuous, high-volume manufacturing without compromising quality. This streamlined process is vital for industries like automotive and packaging that demand both precision and scalability, reducing waste and improving overall productivity.
.jpeg)
Automation process in color masterbatch production process
3.2. Artificial Intelligence and Machine Learning
AI and ML technologies optimize colour masterbatch production by analyzing manufacturing data to predict and correct inconsistencies. Real-time adjustments made by AI systems prevent defects such as streaks caused by uneven mixing or temperature fluctuations, ensuring uniformity.
Machine learning enhances this process by learning from historical data, continually improving manufacturing efficiency and color accuracy. These technologies minimize downtime and errors, helping manufacturers consistently deliver high-quality products, even with complex formulations or changing conditions.
3.3. Digital Color-Matching Technology
Digital color-matching tools enable precise formulation of colour masterbatch by using algorithms and spectral analysis to identify ideal pigment combinations. This eliminates the trial-and-error approach of manual matching and ensures exact color reproduction, catering to industries needing customized hues.
These systems also allow color simulation under various lighting conditions, reducing discrepancies between expectations and the final product. Their speed and flexibility improve prototyping efficiency and responsiveness to customer needs, making them a cornerstone in modern color-matching processes.
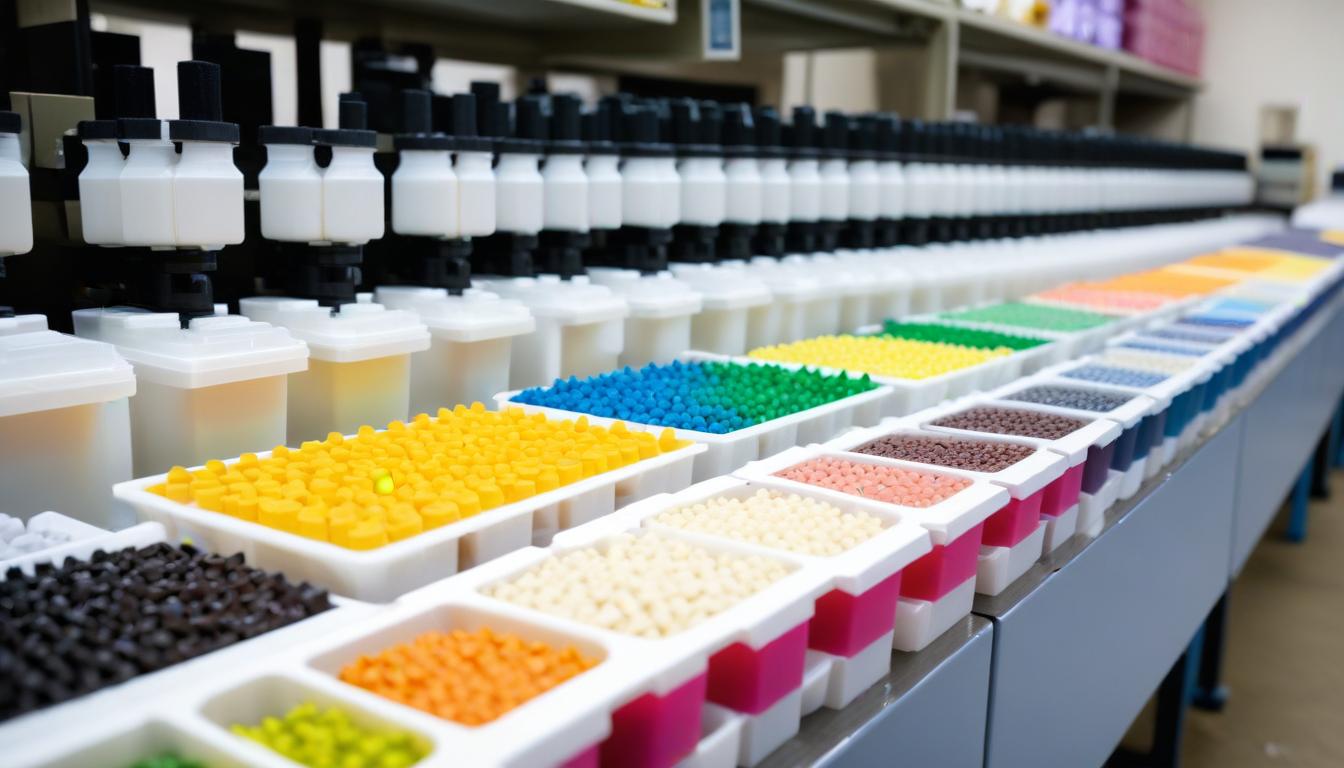
Use digital color matching technology to create precise color masterbatch formulas
3.4. High-Performance Extrusion Equipment
High-performance extrusion equipment, such as twin-screw extruders, ensures precise mixing and uniform pigment dispersion. By monitoring and adjusting parameters like temperature and mixing speed in real time, these machines prevent clumping and achieve consistent coloration.
Twin-screw extruders excel in breaking down pigment agglomerates, delivering homogeneous masterbatches suitable for demanding applications. Advanced sensors further enhance quality control, ensuring reliable production and reduced waste while meeting stringent color consistency standards.
.jpg)
Extrusion equipment contributes to product quality
3.5. Spectrophotometers and Quality Control Tools
Spectrophotometers play a critical role in ensuring color consistency in masterbatch production. These devices compare batch samples with predefined color standards, detecting even minor deviations and enabling timely corrections to maintain accuracy.
Portable spectrophotometers and other tools like colorimeters and gloss meters provide comprehensive quality assessments, including texture and finish. By integrating these technologies, manufacturers deliver products that meet both technical and aesthetic requirements, ensuring customer satisfaction and trust.
.jpg)
Spectrophotometer helps ensure color consistency
4. Conclusion
Maintaining color consistency in colour masterbatch production is essential for delivering high-quality, aesthetically pleasing, and reliable products. Inconsistent colors can tarnish a brand's image, disrupt production processes, and lead to financial losses. By adopting advanced technologies, implementing strict quality control measures, and sourcing high-quality raw materials, manufacturers can overcome these challenges and deliver consistent results.
.png)
Uniformity in color ensures high quality products
In a competitive market, color consistency is more than a technical requirement—it is a cornerstone of customer trust and brand success. Businesses that prioritize it not only stand out but also build lasting relationships with their clients.
5. About EuroPlas’ Color Masterbatch
EuroPlas, a globally recognized leader in the colour masterbatch industry, is committed to delivering unparalleled quality and consistency. With state-of-the-art manufacturing facilities, advanced testing laboratories, and a dedicated team of experts, EuroPlas ensures that every batch meets the highest standards.
.jpg)
EuroPlas color masterbatch products
Our color masterbatches are crafted using premium-grade pigments and cutting-edge technology to provide vibrant, uniform, and durable solutions for a wide range of applications, from packaging and textiles to automotive and construction.
Partnering with EuroPlas means choosing reliability, innovation, and excellence in every product. Let us help you achieve your color consistency goals with solutions tailored to your specific needs.
Contact us today to learn more about our colour masterbatch products and discover the best solutions for your needs. Don't forget to visit our blog for in-depth industry insights that will help you improve your production capabilities with EuroPlas' advanced plastic solutions.