Due to its accuracy, precision, compatibility with complicated designs, plastic CNC machining is a frequent rapid prototype production technique. It is a subtractive process where a computer directs a CNC tool to remove a portion of a workpiece used to create the desired result using methods like milling, turning, etc.
Metals, polymers, and wood are just a few of the materials that CNC machines can work with. Recently, many producers of plastic goods have begun to adopt plastic CNC machining, which entails producing plastic goods using various CNC machine processes.
There are so many things more to plastic CNC machining. Therefore, in this article, we will guide you through every essential information that you need to know about this wonderful method of manufacturing!
Related:
- In Mold Labeling Process - The Ultimate Guide
- How is masterbatch plastic applied in 3D printing – A great technology in industry?
- Cast film extrusion process - The ultimate guide
I. What is plastic CNC machining?
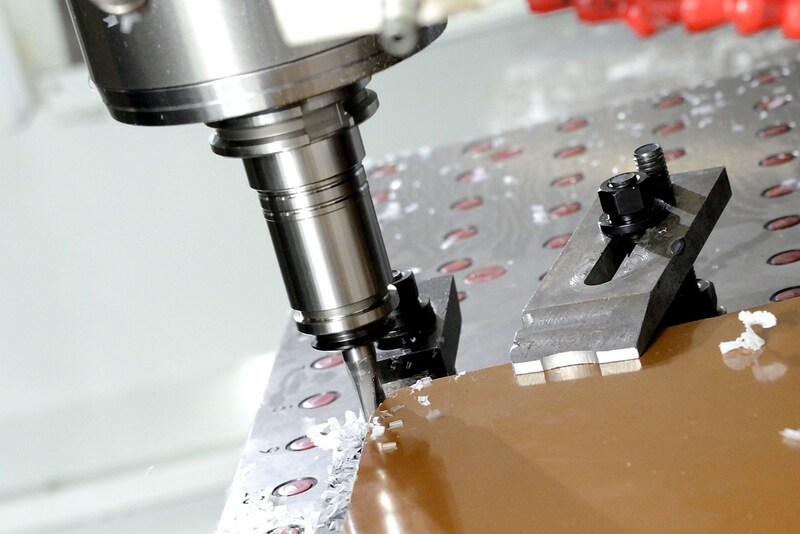
1. Definition:
Plastic CNC machining is a subtractive manufacturing method that involves placing a solid block of plastic against a moving cutting tool that removes material from the block. In the process of making 3D items out of plastic material, computer-aided design (CAD) and computer-aided manufacturing (CAM) are used. In order to form the final product, the cutting tool follows a predetermined tool path that is directed by a digital design file.
CNC machining is a popular way of producing plastic components. You may swiftly produce thousands of consistent and exact pieces with exceedingly tight tolerances with this manufacturing technique.
2. Benefits:
The method of CNC machining, which involves using computer-controlled tools to cut and shape plastic components, provides the following advantages:
- Speed: The procedure is swift and effective.
- High precision: Plastic CNC machining is a fantastic manufacturing option for products that require high precision specifications. This is so that it can accommodate measurements with small tolerances. For components that will be employed in high-precision sectors, this is crucial. Plastic parts may be produced using CNC machines with a very small amount of variance.
- Complex shapes: Additionally, complicated forms that would be challenging or impossible to construct using traditional techniques may be produced with CNC machining. With CNC machining, a computer directs the movement of the cutting tools, enabling the production of parts with a high degree of accuracy and precision.
- Fast prototype turnaround: For anyone who wants a prototype manufactured fast, plastic CNC prototypes are the ideal option. This is because no mold needs to be created. As a result, the procedure is somewhat quicker, and the prototype's cycle time will be shorter.
- Economical process: Molds must be built for other techniques, such as injection molding, which often requires a lot of time and resources. However, this is not a part of plastic CNC machining. As a result, component manufacture is often less expensive than other methods.
- Suitable for various plastic polymers: All of the processes work with a variety of materials. However, plastic CNC machining works well with a larger spectrum of polymers, particularly difficult ones, with few complications.
- Resistance to corrosion and chemicals: This distinguishes CNC-machined plastic components from metal ones. Plastic components are more durable than metal components, which are susceptible to rusting after prolonged usage.
- Accuracy and repeatability: The method is excellent for mass-producing complicated parts since it can be repeated and can be used to make huge numbers of identical parts.
Thanks to the mentioned benefits, the creation of a wide range of plastic components is possible using a CNC machine, which is a flexible and effective instrument.
3. Applications:
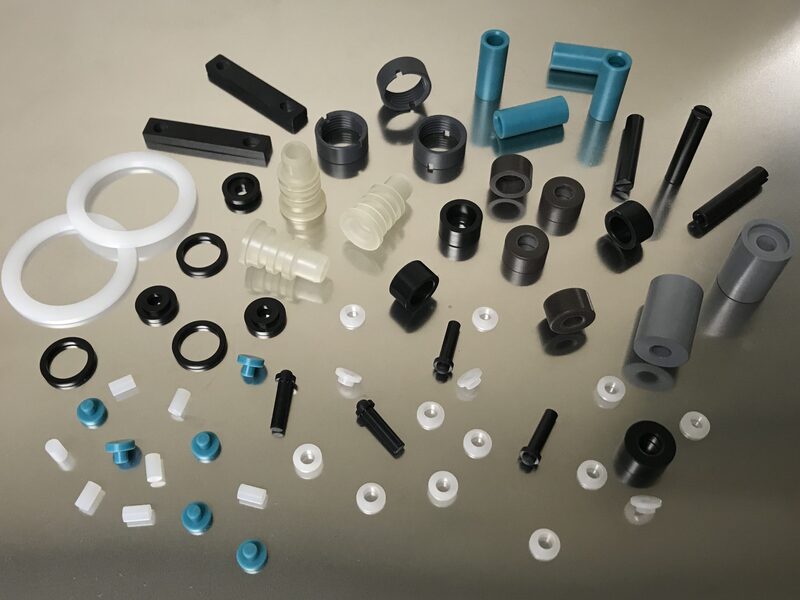
Using CNC machining, you may create a wide variety of plastic items, including:
- Medical equipment including heart implants and dental surgical guides.
- Spray bars and other assembly-line items are examples of parts used in the food and beverage sector.
- Watertight seals and electrical insulators are examples of semiconductor parts.
- Components from the automotive and aerospace industries, including pump gears, valve seats, and fire blocks.
II. CNC machining processes
Depending on the material and the final output, different types of CNC machining processes are used. Here are the top three plastic machining procedures out of the several procedures utilized in popular fast prototyping services:
1. Plastic CNC turning
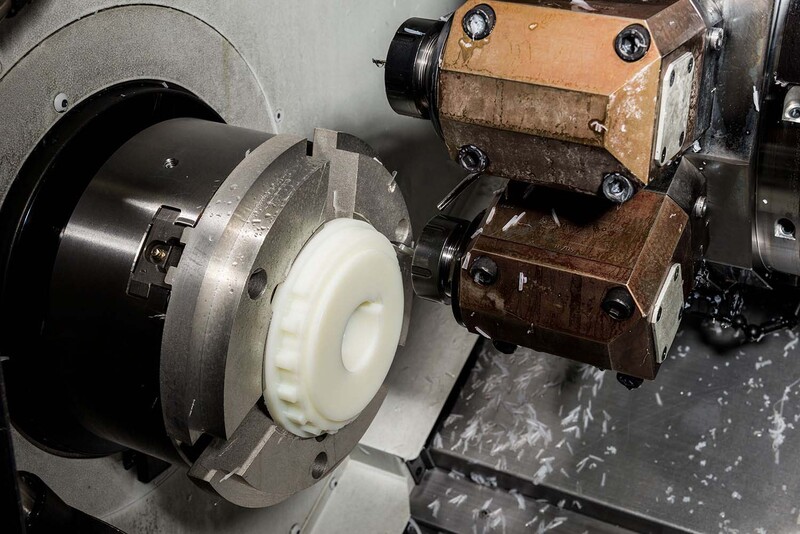
1.1. Definition:
Plastic CNC turning is a CNC machining process in which a piece of circular raw stock is positioned on a spindle, spun at high speed, and manipulated with multiple tools to add specific characteristics. These features and forms can include grooves, bevels, rings, slots, radii, and internal facets such as threading. The stock is often supplied constantly, allowing for optimum automation and efficiency.
There are several types of plastic CNC turning, each with its own set of goals and outcomes. Straight or cylindrical CNC turning, for example, is suitable for big cuts, whereas taper CNC turning produces a characteristic cone-like form.
1.2. Process:
The process of CNC turning may be very complicated. We will provide you with a streamlined, step-by-step overview of the procedure, from design to manufacture, though.
Step 1: Change CAD design file to CNC program.
The first stage entails getting a CAD file ready for conversion into CNC turning machine language. The manufacturing engineer can then use the program to test the component's ability to be manufactured.
Step 2: Setup the CNC turning machine
The setup of the machine is the subsequent phase. Although most of the operations are automated, an operator is still required. Since inaccurate estimates will have an impact on the final product, the machinist must calculate the machine's proper speed and feed rate. Additionally, incorrect calculations in the use of particular materials may result in the workpiece being permanently damaged or having an uneven finish.
Step 3: Make CNC turned parts
Making the desired part is the last stage. Depending on the outcome you want, you can select from a variety of turning procedures. The raw material utilized throughout the production process will determine the ultimate product. The functioning and surface grit of a plastic component will be different from those of a metal component.
1.3. Recommendations:
The following are specific recommendations for using plastic CNC turning machines to produce plastic parts:
- By ensuring that cutting edges have a negative back rake, rubbing may be reduced.
- Giving cutting edges large relief angles
- Polishing top surfaces to improve the surface quality and lessen material accumulation
- Use fine C-2 grade carbide inserts
- Choose the feed rate of 0.015 IPR for rough cuts and 0.005 IPR for more accurate final cuts.
Product teams should be aware that the clearance angle, rake angle, and side angle of a CNC turn will vary depending on the material utilized.
2. Plastic CNC milling
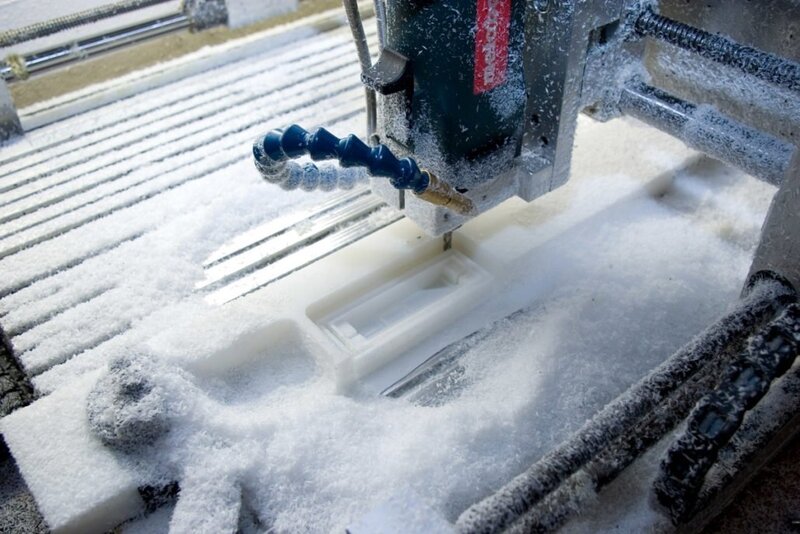
2.1. Definition:
Plastic CNC milling is a CNC machining process that removes material from a solid workpiece using a cylindrical rotating tool known as a milling cutter. In contrast to CNC turning, CNC plastic milling uses stationary material and rotating tools.
Plastic CNC milling machines are classified into two types: 3-axis mills and multi-axis mills. 3-axis mills are better for generating simpler patterns since they move the cutting tool or workpiece along three linear axes — left to right, back and forth, and up and down. Multi-axis mills, which include milling machines with four or more axes, are ideal for producing plastic components with complex geometries.
2.2. Process:
Three key steps may be separated out in the CNC milling process:
Step 1: Get a 2D or 3D CAD model ready
Your program will determine how to set up a CAD file for CNC machining. Make a 2D/3D design of the finished product that can be machined using CAD/CAM software.
Step 2: Convert your design to a file format compatible with CNC
The CAD/CAM program needs to export your CAD model into CNC-friendly file formats. The file, which will be converted, will instruct the machine on the rotational and linear movement, cutting sequence, toolpath, machine, and workpiece speed related to the operation.
Step 3: Configure and run the CNC milling machine
After setting the workpiece down on the table, the operator will attach the cutting tools to the spindle. The machine will then be configured to start the machining program and milling will then start.
2.3. Recommendations:
For producing plastic components using CNC machining, specific guidelines include:
- When milling a thermoplastic that has been reinforced with glass or carbon fibers, use carbon tooling.
- Increasing spindle speeds by using clamps
- To reduce stress concentration, round interior corners and pockets using end mills.
3. Plastic CNC drilling
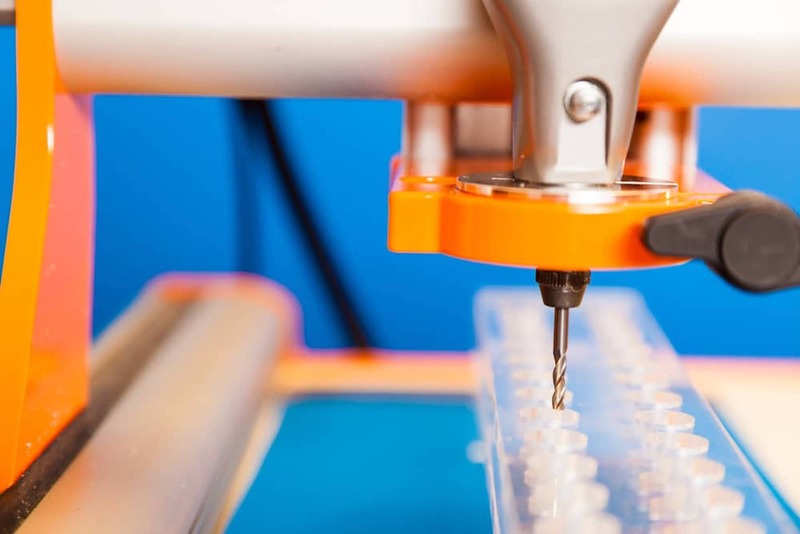
3.1. Definition:
Plastic CNC drilling is a CNC machining process that involves drilling holes into a plastic block using a drill bit. A spindle descends onto the block and drills the appropriate-sized holes after securing the block and CNC drill. You may utilize a CNC drilling machine with a variety of drill presses, including upright, bench, and radial CNC drill presses.
3.2. Process:
Step 1: Create a CAD file
Creating a CAD file for the CNC-drilled component using software like Autodesk Inventor or SolidWorks is the first stage in the drilling process. Technical details regarding the components, such as tolerance, size, etc., will be sent to the operator via the CAD file.
Step 2: Convert your design in a file format compatible with CNC
Only formats like STEP and STL are understood by CNC machines. You must thus convert the produced CAD file into a format that is appropriate. This functionality is incorporated into certain applications. For those who don't, you can utilize an internet service for file conversion. The file will regulate the machine's speed, toolpath, rotational and linear movement, and other features.
Step 3: Configure the machine and run
Attach the CNC drilling bits to the drilling machine to set it up. Next, attach the workpiece to the device. Finally, start the drilling process and watch the machine go to work. After drilling is finished, inspect the part to look for any flaws or faults.
3.3. Recommendations:
It is vital to keep CNC drill bits sharp while manufacturing plastic components using CNC drilling. Drills that are dull or poorly formed might impose too much stress on the component, producing tooling troubles and poor performance. We propose a 90 to 118° drill bit with a 9 to 15° lip angle for most thermoplastics. When drilling with acrylic, a 0° rake is recommended.
The ejection of the CNC drill is particularly critical since poor ejection can create friction and heat buildup. Because CNC drilling creates the most heat of any CNC machining operation, heat reduction is crucial to reducing stress and damage. To remove a CNC drill safely and without injuring the item, limit the drilling depth to three or four times the drill diameter and lower the feed rate when the drill is almost out of the material.
III. How to choose a proper plastic for CNC machining
Choosing the material from which a component should be made is the first stage in part design. The choice of plastic for CNC machining doesn't end just because you determine the item should be made of plastic and CNC-machined. In recent years, there are be a wide variety of machinable plastics available, each with a unique set of qualities. In general, CNC-machined plastic parts are affordable and make good prototypes.
In this article, we'll help you match the ideal plastic for CNC machining with the requirements of your project.
1. ABS
1.1. Overview:
ABS is a well-rounded general-purpose plastic that is frequently utilized. At a cheap cost, it provides electrical resistance, hardness, and high impact strength. It may easily be painted, glued, or welded together, making finishing off the project simple. Depending on how it is machined, ABS can have a little sparkly appearance, although it will often have a matte finish. CNC milling machines are used in ABS CNC machining to cut or engrave objects.
1.2. Characteristics:
When pre-molding prototypes, general-purpose prototyping, impact-resistant components, or cheap cost are priorities, ABS is a great option. ABS will melt in acetone, while it is not very resistant to chemicals or abrasion. Furthermore, the plastic is not particularly robust.
1.3. Applications:
Pre-injection molding prototypes, electronics enclosures, home appliances, and even the famous Lego bricks are some of the most frequent uses for ABS.
2. Nylon
2.1. Overview:
Nylon is a strong and long-lasting plastic that is utilized for a variety of uses. With the stiffness required to maintain its shape and the strength to resist deformation under loading circumstances, it has a reasonably strong chemical and heat resistance.
2.2. Characteristics:
Nylon has excellent electrical insulation, high strength and stiffness that it retains over a wide temperature range, and outstanding chemical and wear resistance. For applications where sturdy, long-lasting parts are required at a reasonable price, nylon 6/6 is a viable option.
Nylon 6/6, on the other hand, will absorb moisture and expand, losing part of its dimensional precision. Due to internal tensions in the material, it may also distort if there is a significant degree of asymmetric material removal during machining.
3.3. Applications:
The components of medical gadgets, circuit board mounting hardware, electrical insulation, vehicle engine compartments, and aircraft are the most frequent uses of nylon. It is utilized in several of these applications as a cost-effective substitute for metals.
3. Acrylic
3.1. Overview:
Acrylic, often known as Plexiglass or Luctie, has a chemical makeup that is known as PMMA (Poly Methyl MethAcrylate) plastic. It's robust, with good impact strength and scratch resistance, and it's simple to bond with acrylic cement.
3.2. Characteristics:
It works effectively for any applications that need optical transparency or translucence as well as a less expensive, less robust substitute for polycarbonate. Because of its scratch resistance, it is also ideal for locations with somewhat abrasive surroundings. Acrylic, on the other hand, is a brittle plastic that tends to shatter or split rather than extend as a ductile substance would. Acrylic components' wall thickness should be taken into consideration because thinner walls are more fragile.
A piece of acrylic that has been machined will lose its transparency and develop a frosted, transparent look. As a result, it is typically a good idea to specify whether or not an acrylic portion should be left at stock thickness to retain transparency. An extra post-processing step called polishing can be used if a machined surface has to be transparent.
3.3. Applications:
Acrylic is transparent when machined and is most frequently used as a low-weight alternative to glass or for light pipes. Light tubes, tanks, panels, vehicle lighting components, and optical engineering components are a few more frequent usage.
4. Delrin
4.1. Overview:
Delrin is a kind of semi-crystalline thermoplastic acetal resin, often known as POM, or polyoxymethylene. It features a high rigidity, great dimensional stability, and a slick, low friction surface. This acetal resin is available in a variety of categories, such as standard, toughened, low friction, glass-filled/reinforced, and UV-stabilized.
4.2. Characteristics:
For applications like these or any others requiring high rigidity, tight tolerances, or high friction, Delrin/POM is an excellent plastic. Due to its dependability and longevity, it has been utilized in commercial industries for decades. Additionally, it possesses outstanding resistance to impact, chemicals, moisture, and fatigue. Delrin/POM is also simple to CNC machine. Delrin is a great material option for CNC plastic machining components that demand dimensional precision and close tolerances because of its high stiffness and rigidity.
The slick, durable surface of Delrin has the drawback of being exceedingly difficult to glue. Additionally, the material possesses internal tensions that render it vulnerable to warping in regions that are thin or have significant asymmetric material loss. Furthermore, overheating Delrin/POM might cause harmful off-gassing.
4.3. Applications:
Delrin is frequently used in the manufacture of fasteners, bushings, bearings, jigs and fixtures for assembly, as well as parts for automobiles, buildings, and electronics.
5. HDPE
5.1. Overview:
HDPE stands for high density polyethylene. It has a waxy texture and is inherently opaque due to its crystalline structure, however it is also marketed with a dyed black finish.
5.2. Characteristics:
Contrary to its name, HDPE is the least thick plastic that Fictiv provides and also has great chemical and electrical insulation as well as a slick surface. It provides a low coefficient of friction and strong impact resistance at low temperatures. Overall, it is a cost-effective and reliable option for CNC-machined plastic parts.
The fundamental drawback of HDPE is its weak strength, especially under strain and flexing. This makes it vulnerable to stress cracking.
5.3. Applications:
In fluid applications including fuel tanks, plastic bottles, and fluid flow pipes, HDPE is frequently employed. Due to its chemical resistance and slipperiness, it works well for producing plugs and seals. It also works well for applications involving weight or electrical sensitivity.
6. Polycarbonate
6.1. Overview:
Polycarbonate, aka PC, is a transparent thermoplastic. Additionally, it is one of the polymers that is most often CNC machined and recycled internationally. It has a clear milky-blue look in its natural state, but is also marketed in a black color. The milky-blue and black hues are also naturally lustrous.
6.2. Characteristics:
Due to its excellent rigidity and impact resistance, polycarbonate can withstand a broad variety of temperatures without losing its functionality. It is also optically semi-transparent, yet if opaqueness is required, it may be colored black. Applications requiring a highly strong or resistant plastic or those requiring optical clarity are best suited for polycarbonate. Polycarbonate is one of the most often used and recycled polymers as a result. Since polycarbonate is 250 times more impact resistant than glass and has a higher resilience than acrylic, it is frequently used instead of glass in construction.
Pure polycarbonate is prone to scratches and has poor wear resistance. To increase wear resistance or optical clarity, anti-scratch coatings and vapor polishing can be applied as a post-processing step, if needed. The size of parts that may be constructed of polycarbonate is further restricted by the fact that it is difficult to get sections that are thicker than two inches.
6.3. Applications:
Because of its strength and transparency, polycarbonate is used to create a variety of products, including optical disks, bulletproof glass, safety glasses, light pipes, CDs, and DVDs.
EuroPlas is a reputable company with over 16 years of experience in manufacturing and supplying bioplastics and plastic additives. The company is committed to providing high-quality products at competitive prices along with excellent customer service.
If you are in need of a reliable and high-quality supplier of bioplastics and plastic additives, then
European Plastic Corporation is an excellent choice for you.