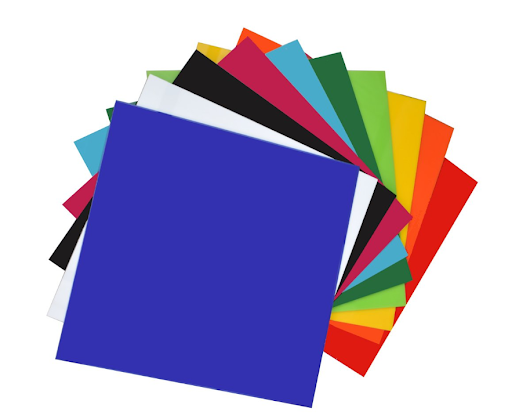
Thermoplastic sheets
Thermoplastic sheets for molding are increasingly receiving attention as the market prioritizes environmentally friendly products. Thanks to its recyclable molding properties, thermoplastic sheets for molding both help solve the problem of environmental waste and optimize costs. The production process of thermoplastic products is not complicated and does not require the production of new materials, so it saves most operating costs for investors. Most consumers are attracted to thermoplastic sheets for molding because they are timeless and durable, helping to save on repair and maintenance costs. Right now, let's learn about the outstanding features of thermoplastic sheets for molding in the treasure trove of material knowledge below!
1. An overview of thermoplastic sheets for molding
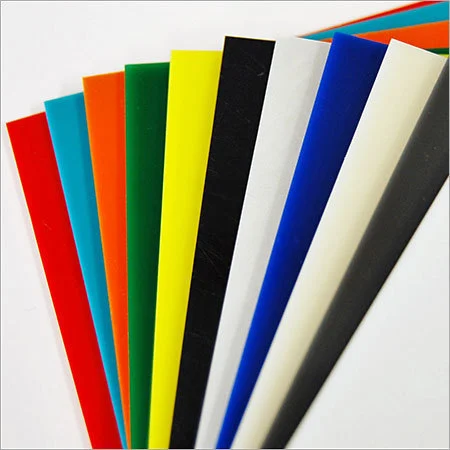
Thermoplastic sheets for molding in many colors
Thermoplastic sheets for molding are a type of material derived from the polymer group. Polymer chains bond with the help of intermolecular forces. This material liquefies when heated and hardens when cooled. Thermoplastics sheets for molding are easily heated or cooled repeatedly, demonstrating their recyclability. When the temperature increases they easily weaken. The heating process changes the physical properties of thermoplastics, turning them into a homogeneous liquid but does not change the inherent chemical composition. People will perform steps such as injection molding, extrusion, and blow molding to create a liquid compound. Thermoplastics sheets for molding contribute greatly to reshaping products in terms of size or form as well as recycling because thermoplastics harden as they cool. Thermoplastics sheets for molding are widely classified based on their composition, crystal structure, and density. Thermoplastics sheets for molding are suitable for a variety of manufacturers' needs due to their strong resistance to chemical attack. Let's learn more about their characteristics below!
2. Thermoplastic sheets for molding properties
2.1 Recyclability
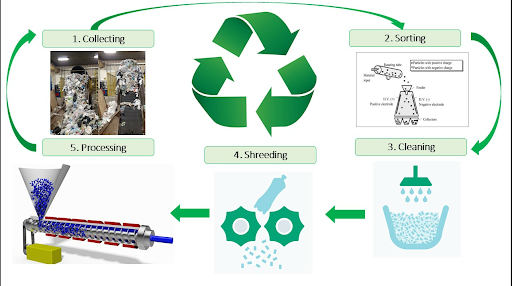
Thermoplastic can be recycled
One of the important characteristics that makes thermoplastics sheets for molding attractive to most consumers and investors is their recyclability. Thermoplastic sheets for molding have a fairly low melting point, so they can easily be heated into a liquid state. Carrying out the stages of blowing, pressing, and molding, we can easily obtain new products according to needs. The special advantage is that because thermoplastics do not undergo chemical changes, manufacturers can recycle and reshape the material many times without harming human health.
Because of this characteristic, thermoplastic sheets for molding are classified as environmentally friendly materials. The plastic recycling process contributes to greatly reducing the amount of waste released into the environment, helping to maximize material efficiency and bringing great economic benefits.
2.2 Flexibility
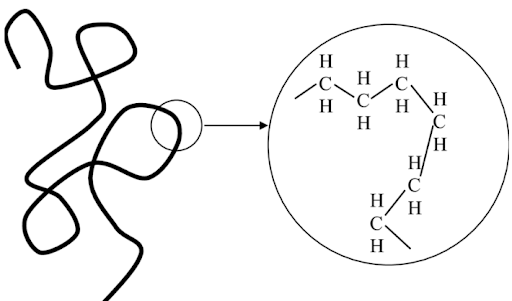
Flexibility of thermoplastic
Besides recyclability, flexibility is also one of the advantages of thermoplastic sheets for molding. Although their heat resistance is quite low, they have a higher tensile strength than metals. Therefore, thermoplastics can also be used for designs that require flexibility or rigidity. Depending on the specific type, the elasticity rate of thermoplastics can range from 5% to 700% and some types can return to their original shape after being stretched regularly.
2.3 Chemical resistance
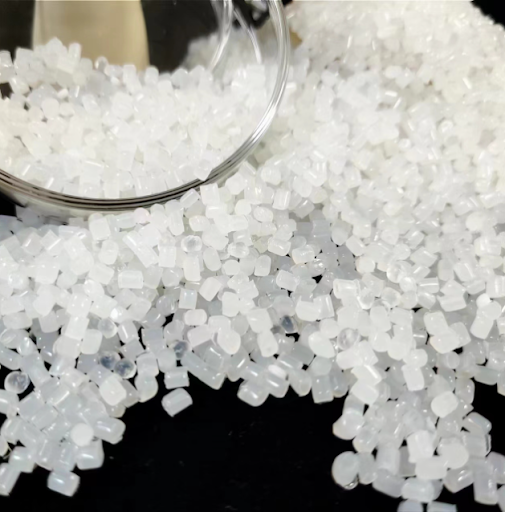
Thermoplastic polymer has good chemical resistance
As mentioned above, most thermoplastic sheets for molding have excellent chemical resistance. Specifically, they possess a fairly slow corrosion process and a long degradation time when exposed to or immersed in corrosive gases or liquids. Because of this property, thermoplastics become the ideal material for designs that can withstand harsh environments. Fields such as water filtration, pharmaceuticals, medical implants, energy transmission, and aerospace also often benefit from thermoplastics.
2.4 Strength and durability
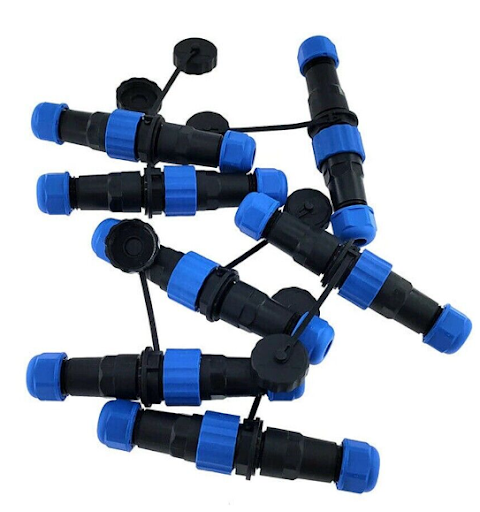
Aviation cable made of thermoplastic
The strength-to-weight ratio of thermoplastic sheets for molding is higher than some metals, so they are preferred over metals. They are not only helpful in durability but also significantly reduce weight. When compared with some other types of polymers, thermoplastics also have an advantage in terms of resistance to abrasion, pressure and high fatigue. That's why thermoplastics sheets for molding are considered to have unparalleled durability.
2.5 Production process is easy
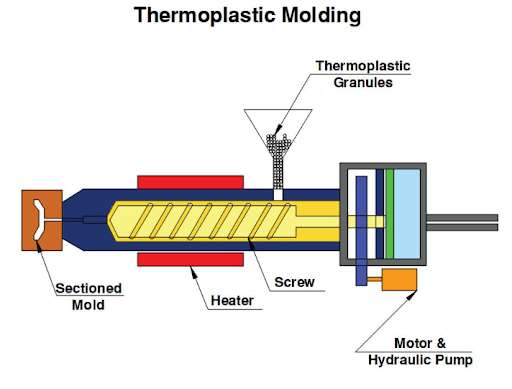
Thermoplastic molding
With the same piece of material, thermoplastic sheets for molding can produce many products with diverse sizes, shapes, and appearances. After being melted and newly shaped, thermoplastics only need to be cooled at normal temperatures without the need for complicated refrigeration machinery. Manufacturers easily mold thermoplastics without using additional joints, wires or screws to connect parts together.
3. Thermoplastic sheets for molding: 5 most famous applications
3.1 Aerospace
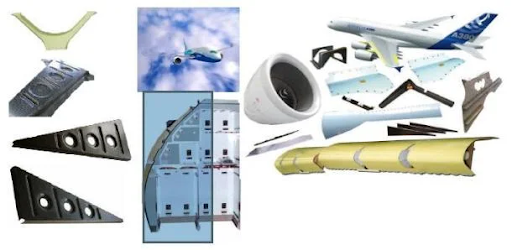
Thermoplastic used in aerospace
The aerospace industry is taking advantage of the strength-to-weight ratio, flexibility, and stiffness of thermoplastics sheets for molding. Typical examples include high-performance thermoplastics such as PEEK (Polyether Ether Ketone). Besides durability, thermoplastic sheets for molding are more affordable than other materials, so they help manufacturers save costs without losing the expected features of the product part. Because of its light weight, thermoplastics also help save weight, helping the engine operate less fuel.
3.2 Automobile industry
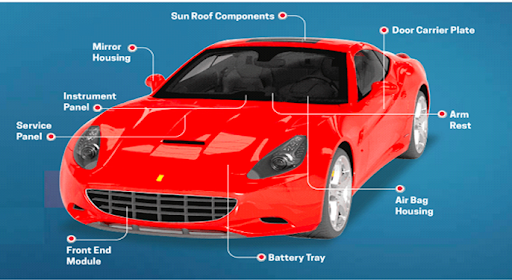
Thermoplastic used in automobile
Similar to the aerospace industry, thermoplastic sheets for molding also show promise in improving performance as vehicle weight is significantly reduced. The high strength-to-weight ratio of materials helps vehicles save on fuel costs, lower emissions, and saves costs for manufacturers and drivers globally. Based on the characteristics of each type of thermoplastic, the manufacturer will choose the appropriate type for auto components to optimize this industry.
3.3 Fluid handling and management
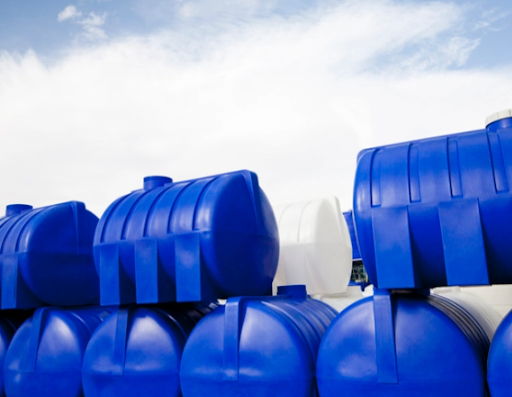
Thermoplastic fluid containers
Thermoplastic sheets for molding have very good chemical stability so they will not affect or contaminate the liquid they contain. Even when exposed to corrosive liquids, thermoplastics show little damage. Thanks to its waterproof properties, low absorption of impurities, and easy installation, thermoplastic sheets for molding are an ideal choice for handling or containing liquids.
3.4 Medical and pharmaceutical
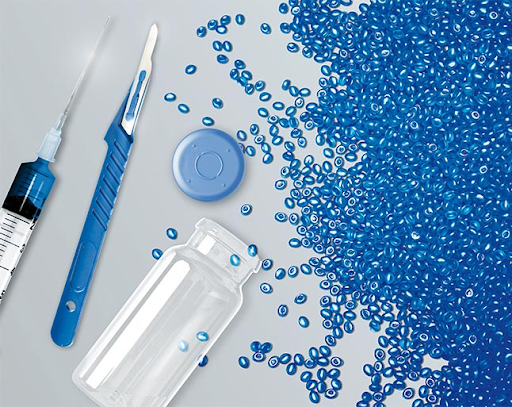
Thermoplastic in manufacturing of medical devices
Thermoplastic sheets for molding have proven to be one of the best options in the manufacturing of medical devices, medicine bottle caps, catheters, syringe tips, etc. The main reason is due to properties such as durability, extensibility, flexibility, sealability, low friction and good bio-chemical compatibility. Besides examination equipment, thermoplastics for filtration systems, sterilization and other pharmaceutical processing processes.
3.5 Resource exploitation components
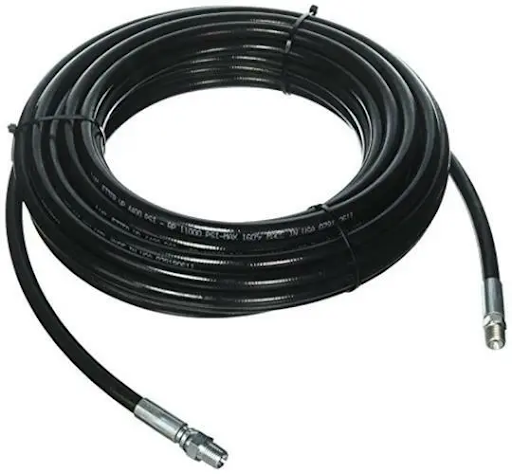
Thermoplastic cable
Thermoplastic sheets for molding are a suitable choice for deep underground drilling and mining applications. The mining process requires exposure to harsh environments, requiring perfect resistance and abrasion resistance of thermoplastics. Choosing the right thermoplastic component production helps mining equipment last longer, require less maintenance, and decompose many times slower than metal.
4. Conclusion
In short, thermoplastic sheets for molding are highly flexible from production to application. Molding to create new products from thermoplastics plays a huge role in protecting our environment. Consumers can own a perfect product that is environmentally friendly and durable over time. Read more useful blog posts about materials at EuroPlas that can help you make optimal decisions for your upcoming project.