ABS vs. PVC Plastic: Which One Is Better?
1. Overview of ABS and PVC Plastics
When choosing materials for manufacturing, two common plastics that often come into comparison are ABS (Acrylonitrile Butadiene Styrene) and PVC (Polyvinyl Chloride). Both of these plastics are widely used in various industries, ranging from automotive to construction, thanks to their unique properties. However, they each have specific strengths and weaknesses that make them more suitable for certain applications than others.
ABS is known for its toughness and impact resistance, making it ideal for products requiring durability and strength. ABS is a thermoplastic, meaning it becomes pliable at a specific temperature and hardens upon cooling, which makes it a popular material for injection molding.
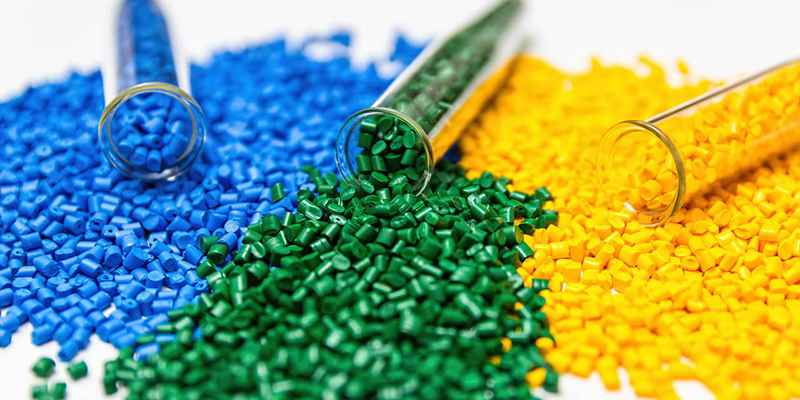
ABS is known for its toughness and impact resistance.
On the other hand, PVC is a versatile and cost-effective plastic that is commonly used in construction and piping due to its resistance to corrosion and chemicals. It is often found in electrical insulation, plumbing pipes, and window frames. PVC can be rigid or flexible, depending on its formulation, making it adaptable to various industrial needs.
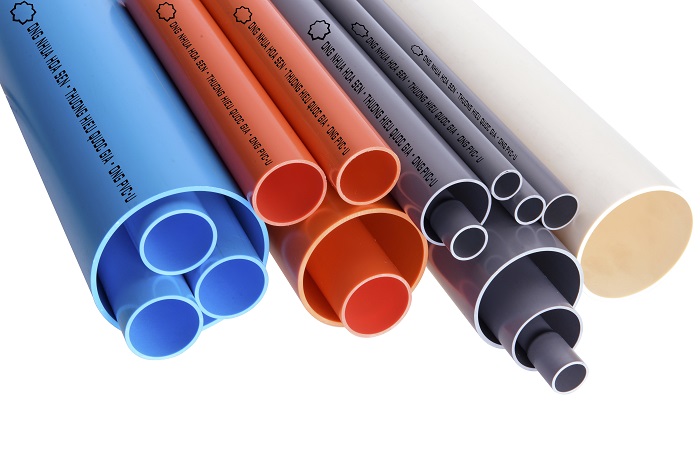
PVC is a versatile and cost-effective plastic.
Understanding the properties and applications of ABS and PVC can help in making an informed decision when selecting the right material for specific uses.
2. ABS vs. PVC: Comparing Properties
When comparing ABS and PVC, it’s essential to look at their properties to understand how they perform under different conditions. These properties include mechanical strength, thermal resistance, chemical resistance, and ease of processing.
- Mechanical Strength: ABS is highly valued for its superior impact resistance and toughness. It can withstand physical stress without cracking or breaking, making it an excellent choice for products that may endure physical abuse, such as automotive parts and helmets. PVC, while durable, is not as impact-resistant as ABS. It is more prone to cracking under heavy loads or sudden impacts, which makes it less suitable for applications requiring high toughness.
- Thermal Resistance: ABS can handle higher temperatures than PVC, with a higher melting point of around 105°C (221°F). This property makes ABS ideal for applications that require heat resistance, such as electrical housings and automotive components. PVC, on the other hand, has a lower melting point (around 80°C or 176°F) and is more likely to deform under high temperatures, which limits its use in environments with significant heat exposure.
- Chemical Resistance: PVC is known for its excellent resistance to chemicals, oils, and greases, making it a preferred choice for pipes, tubing, and electrical insulation. ABS, while resistant to many chemicals, is less effective against strong solvents or acids compared to PVC. This makes PVC more suitable for applications where chemical exposure is a significant concern.
- Ease of Processing: Both ABS and PVC are thermoplastics, meaning they can be melted and reshaped multiple times without losing their mechanical properties. However, ABS is generally easier to machine, mold, and finish, which is why it’s commonly used in 3D printing and injection molding processes. PVC, on the other hand, can release harmful gases when processed at high temperatures, which requires more specialized handling during manufacturing.
3. ABS vs. PVC: Advantages and Disadvantages
|
Advantages |
Disadvantages |
ABS (Acrylonitrile Butadiene Styrene) |
- High impact resistance, making it durable in tough conditions.
- Good heat resistance, capable of withstanding higher temperatures.
- Easy to machine and fabricate into different shapes and sizes.
- Offers good dimensional stability, maintaining shape over time.
- Can be easily painted or finished for aesthetic purposes.
- Good electrical insulation properties.. |
- More expensive than PVC, which may impact budget-sensitive projects.
- Poor chemical resistance to certain solvents and oils.
- Limited UV resistance, leading to potential degradation when exposed to sunlight.
- Heavier than PVC, which may not be suitable for lightweight applications.
- Difficult to recycle, often requiring special processes for disposal.
|
PVC (Polyvinyl Chloride) |
- Excellent chemical resistance, suitable for various environments.
- Lightweight and easy to handle, making it convenient for various applications.
- Cost-effective and widely available, reducing production costs.
- Can be rigid or flexible, providing versatility in applications.
- Low moisture absorption, reducing the risk of mold and mildew.
- Can be formulated for additional fire resistance.
|
- Less impact-resistant compared to ABS, making it more prone to cracking under stress.
- Can become brittle at low temperatures, limiting its use in cold environments.
- Requires additives for flexibility, which can complicate manufacturing.
- Potential environmental concerns due to the production and disposal processes.
- May release harmful chemicals during combustion.
|
4. ABS vs. PVC: Comparing Applications
The distinct properties of ABS and PVC make them suitable for various applications, each thriving in different environments and serving unique purposes.
- Automotive Industry: ABS is the preferred material for many automotive parts, including dashboards, trim components, and exterior parts. Its high impact resistance and heat stability make it ideal for components that must withstand physical stress and exposure to heat. PVC, while not as commonly used in car manufacturing, is often found in automotive wiring insulation and piping systems due to its resistance to chemicals and ability to insulate against electrical currents.
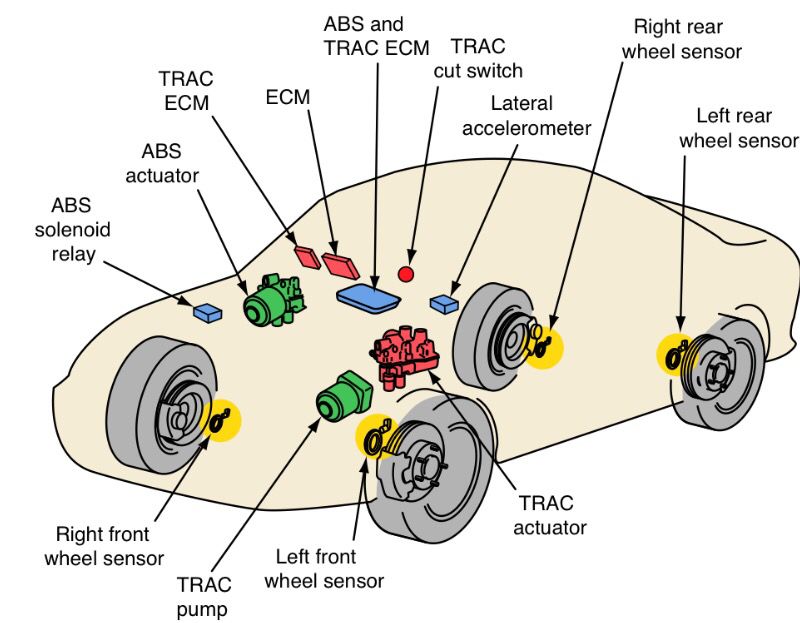
ABS is the preferred material for many automotive parts.
- Construction Materials: PVC dominates in construction, especially in piping, plumbing, and electrical insulation. Its resistance to corrosion and affordability make it the material of choice for plumbing pipes, drainage systems, and electrical conduit. ABS, although less common in construction, can be found in pipes where durability and resistance to impact are needed, such as in underground drainage systems.
- 3D Printing and Prototyping: ABS is a popular material for 3D printing due to its ease of molding and durability. It is often used to create prototypes, models, and finished parts that require precision and strength. PVC, being more difficult to process, is not commonly used in 3D printing.

ABS is a popular material for 3D printing.
- Consumer Products: ABS is commonly used in products that require a combination of strength, aesthetics, and durability. Examples include LEGO bricks, toys, electronic housings, and kitchen appliances. PVC, due to its chemical resistance and flexibility, is often used in items such as shower curtains, inflatable products, and raincoats.
- Electrical Components: PVC’s excellent electrical insulation properties make it a preferred material for wiring and cables. It can effectively protect against electrical leakage, making it ideal for use in both residential and commercial wiring. ABS, while used in electrical housings, is less effective for insulation compared to PVC.
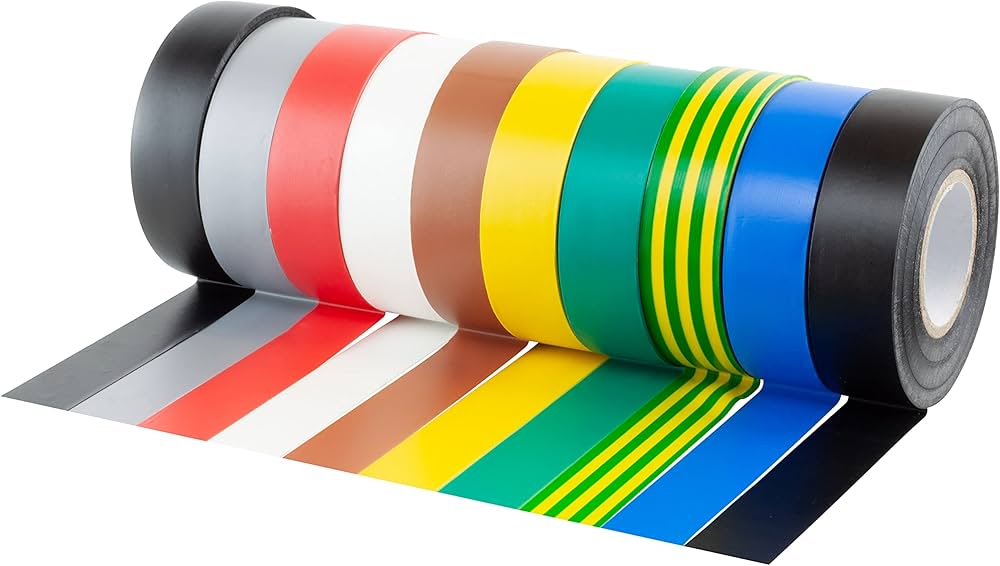
PVC’s excellent electrical insulation properties make it a preferred material for wiring and cables.
5. ABS vs. PVC: Which One Is Better?
When comparing ABS and PVC, the choice of which one is better depends entirely on the specific needs of the application. Both materials have their strengths and weaknesses, and the decision should be based on the intended use, budget, and environmental factors.
- ABS is better for applications requiring high impact resistance, toughness, and heat stability. It excels in automotive parts, consumer electronics, and 3D printing where detailed molding and strength are important. However, it comes at a higher cost and has lower chemical resistance.
- PVC is better for applications where chemical resistance, affordability, and versatility are key. It is widely used in construction, plumbing, and electrical insulation where exposure to chemicals and corrosion is a concern. PVC’s flexibility and lower cost make it ideal for large-scale projects, but it may not perform well in high-temperature or high-impact environments.
In short, neither material is universally better than the other. The choice between ABS and PVC depends on the specific requirements of the project. If you need a material that can withstand physical stress and heat, ABS is the way to go. If your project requires chemical resistance and cost-effectiveness, PVC is the better option.
6. Conclusion
Choosing between ABS and PVC depends on the specific application, as both plastics offer distinct advantages. ABS is known for its toughness, impact resistance, and machinability, making it ideal for high-stress and high-temperature applications. On the other hand, PVC excels in chemical resistance, affordability, and versatility, making it the material of choice for construction and electrical insulation.
Both materials have their limitations, with ABS being more expensive and less resistant to chemicals, while PVC struggles with impact resistance and thermal stability. By understanding these differences, manufacturers and designers can make informed decisions when selecting the right plastic for their projects.
7. About EuroPlas’ ABS filler masterbatch
EuroPlas offers a diverse range of high-quality ABS products designed to meet the varying demands of different industries. Our portfolio includes specialized compounds such as ABS glass fiber, ABS antistatic, and ABS flame retardant compounds, each engineered to enhance performance and suitability for specific applications.
- ABS Glass Fiber Compound: Our ABS-GF compound combines ABS resin with glass fiber reinforcement, resulting in a composite material that boasts improved mechanical properties such as increased strength, stiffness, and dimensional stability. This innovative material also raises the heat deflection temperature, making it ideal for applications in car fuel tank caps, printers, automotive interiors, and earphone components.
- ABS Antistatic Compound: Our ABS-antistatic compound incorporates antistatic additives into ABS resin, enabling the dissipation of static electricity while preserving the mechanical and processing properties of ABS. This specialty compound is particularly beneficial for electronic components, pallets, mobile chargers, power sockets, and earphones, where static electricity can pose risks to product integrity and user safety.
- ABS Flame Retardant Compound: Our ABS-FR compound is modified with flame retardant additives to enhance fire resistance, compliant with UL94 standards (V0, V1, and V2). This material is essential for applications where fire safety is paramount, such as mobile chargers, electronic components, power sockets, earphones, and vacuum cleaners. The flame retardant properties are complemented by the mechanical strength typical of traditional ABS, ensuring that safety does not compromise performance.
At EuroPlas, we are committed to providing high-performance ABS solutions tailored to meet the unique requirements of our customers. Our expert team is ready to assist you in selecting the right ABS compound for your projects. Explore our extensive range of products to find the perfect fit for your needs, and stay updated on the latest trends in the plastic industry by visiting our blog.