ABS compound has gained significant traction in automotive manufacturing due to its remarkable properties. This thermoplastic polymer excels in strength, durability, and versatility, making it ideal for various car components. Its lightweight nature enhances fuel efficiency, while its resilience ensures long-lasting performance. Delve into the advantages of ABS compound and why it is a preferred choice for car manufacturers.
Read more: ABS Plastic - A top choice for toy manufacturing
1. Overview of ABS Compound
ABS compound is a widely recognized engineering plastic that offers significant advantages over traditional plastic materials. Unlike conventional plastics, ABS compound is synthesized from virgin ABS resin, enhanced with various reinforcing agents such as glass fibers, flame retardants, and insulating materials, along with appropriate additives. The formulation and composition of ABS compounds can vary depending on the specific technical requirements of the final product.
For instance, when manufacturing household electrical components, the reinforcing agents may include antistatic additives and colorants. Conversely, in the production of electronic devices, conductive and flame-retardant materials are prioritized to ensure safety and functionality. This versatility allows ABS compounds to effectively address the major limitations of standard plastics, particularly their lack of specialization.
Moreover, the intrinsic properties of ABS compounds enable businesses to directly integrate this engineering plastic into their production lines without the need for additional blending processes. This streamlining of the manufacturing process not only simplifies operations but also saves time and enhances labor productivity. As a result, ABS compound stands out as a superior choice for various applications, offering a blend of performance, efficiency, and adaptability that meets the evolving demands of the industry.
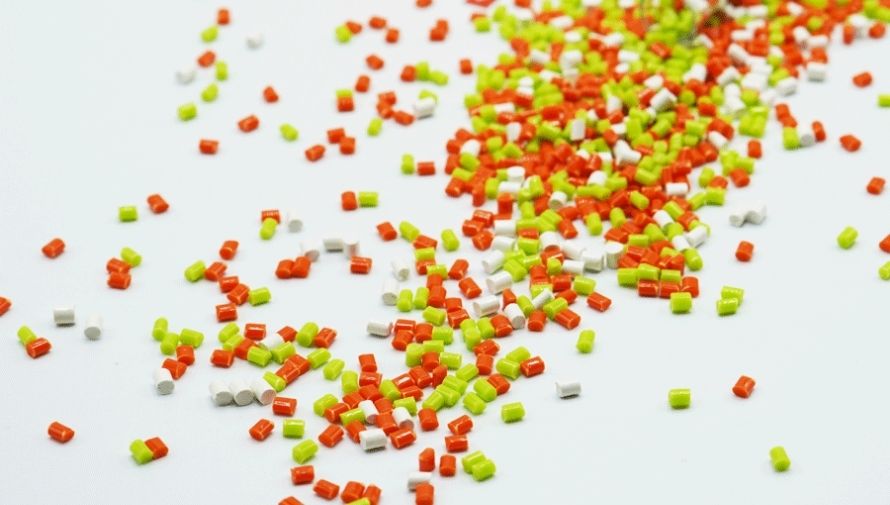
2. Why is ABS Compound Fitted for Automotive Applications?
When considering materials for automotive applications, ABS compound stands out due to its unique combination of properties that cater specifically to the demands of the industry. Its versatility and performance make it an ideal choice for various vehicle components. Below are the key reasons why ABS is increasingly favored in automotive manufacturing:
- Outstanding Impact Resistance: ABS compound excels in absorbing shocks and impacts, making it an ideal choice for critical automotive components such as bumpers, body panels, and interior trims. The butadiene rubber content enhances its toughness and flexibility, ensuring passenger safety during collisions.
- Exceptional Strength and Durability: Beyond its impact resistance, ABS boasts high tensile strength and hardness, ensuring longevity in automotive applications. It effectively withstands harsh chemicals and environmental conditions, including temperature fluctuations, road debris, and UV exposure, maintaining its shape and structural integrity over time.
- Lightweight Composition: Significantly lighter than traditional metals like steel, ABS contributes to substantial weight reduction in vehicles. This not only enhances fuel efficiency but also improves overall performance, with parts being approximately 10% lighter than metal alternatives, a considerable advantage for modern automotive design.
- Robust Heat Resistance: While not suitable for engine components, ABS can endure temperatures up to 180°F, making it perfect for under-hood applications. This heat resistance is a crucial factor in its popularity for custom engine bay enhancements and covers.
- Ease of Manufacturing: ABS can be easily injection molded into complex shapes, offering manufacturers the flexibility to create intricate designs that may be challenging with other materials. This capability allows for the consolidation of multiple parts into single components, streamlining production processes.
- Recyclability: Known for its recyclability, ABS plastic is an environmentally friendly option within the automotive industry. It can be recycled multiple times without significant degradation of its properties, promoting sustainable practices and reducing landfill waste. Increasingly, municipal recycling programs accept ABS, facilitating its reuse in new automotive parts and other products.
- Cost-Effectiveness: ABS is generally more affordable to produce and process compared to high-performance materials such as aluminum and carbon fiber. This cost advantage, combined with its durability and ease of manufacturing, makes ABS an attractive choice for automakers aiming to reduce production costs while maintaining high-quality, lightweight components.
- Lifecycle Impact: The lifecycle of ABS plastic - from production to disposal - demonstrates its sustainability. It requires less energy to produce compared to metals, contributing to lower greenhouse gas emissions. Its lightweight nature enhances vehicle fuel efficiency, reducing fuel consumption and emissions throughout the vehicle's lifespan.
Incorporating ABS compound into automotive applications not only enhances performance and safety but also aligns with the industry's shift towards more sustainable and efficient vehicle designs.
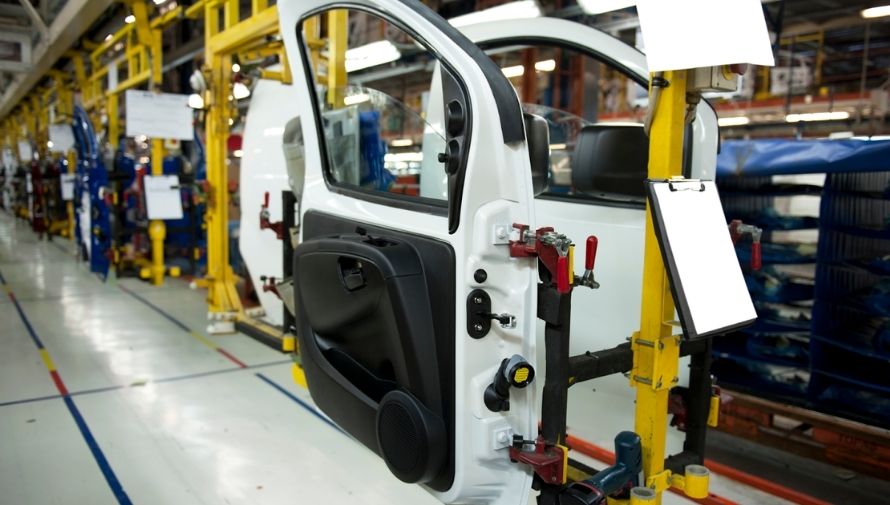
Read more: ABS Sheet vs. PVC Sheet: What Are The Differences?
3. Conclusion
In conclusion, ABS compound stands as a pivotal material in the automotive manufacturing sector, renowned for its exceptional strength, durability, and versatility. Extensively utilized in various components such as dashboards, bumpers, fenders, and both exterior and interior trims, ABS offers a unique combination of properties that make it ideal for these applications. As the automotive industry continues to evolve, the demand for high-performance materials like ABS compound is likely to increase, paving the way for even broader applications in future vehicle designs. Its ability to withstand challenging conditions while maintaining aesthetic appeal ensures that ABS will remain a cornerstone in automotive manufacturing for years to come.
4. About EuroPlas’ ABS Compound
EuroPlas is proud to present our innovative ABS flame retardant compounds, expertly formulated from high-quality ABS resin combined with advanced flame retardant additives. Designed to meet varying fire resistance levels according to the UL94 standard - V0, V1, and V2 - our ABS-FR compounds are ideal for applications where fire safety is paramount.
Acrylonitrile Butadiene Styrene (ABS) is renowned for its excellent processability, toughness, and impact strength, making it a versatile choice in numerous industries, including automotive and electronics. Our flame retardant ABS compounds not only enhance fire resistance but also retain the exceptional mechanical and physical properties of traditional ABS. This allows for seamless integration into products such as mobile chargers, electronic components, power sockets, earphones, and vacuum cleaners.
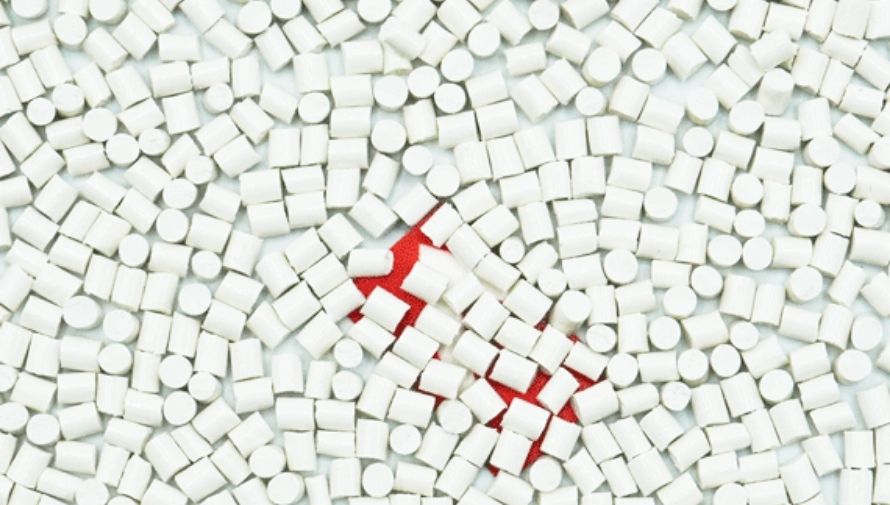
Our tailor-made solutions cater to specific product requirements, ensuring optimal performance without the need for additional materials. For reliable, high-performance materials that enhance safety and efficiency, contact us today to discover how EuroPlas’ ABS flame retardant compounds can elevate your product offerings!