Plastic surface treatment is a critical process that enhances the properties of plastic materials, enabling them to bond effectively with coatings, adhesives, and other substrates. However, treating plastic surfaces requires specific steps to ensure the material is prepared correctly, avoiding defects and enhancing performance. In this article, we’ll guide you through the essential steps of plastic surface treatment.
1. Overview Of Plastic Surface Treatment
Plastic surface treatment is a critical process in many industries. It enhances the surface properties of plastics, allowing them to bond more effectively with coatings, adhesives, or other materials. Industries that require plastic surface treatments include:
1.1. Automotive Industry
The automotive industry depends on plastic materials for both interior and exterior parts. To ensure that paints and coatings adhere properly to plastic car components, manufacturers use various methods to treat the plastic surfaces. These treatments help enhance the strength and durability of bumpers, dashboards, and other molded plastic components exposed to environmental factors such as moisture, UV radiation, and temperature changes.
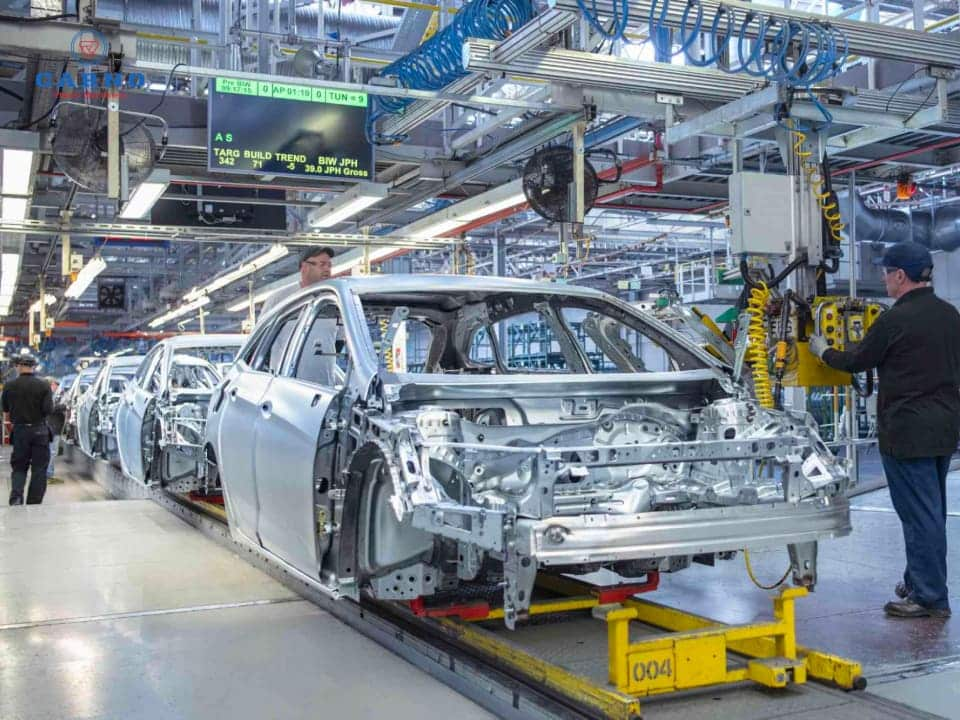
Plastic surface treatment enhances the strength of car covers
1.2. Packaging
Plastics play a significant role in the packaging industry because of their lightweight nature, cost-effectiveness, and versatility. However, in applications like food packaging, where labels and designs are applied, surface treatment is essential to ensure proper adhesion of inks or adhesives for labels. Additionally, surface treatment improves barrier properties, safeguarding the contents of the package from contamination.
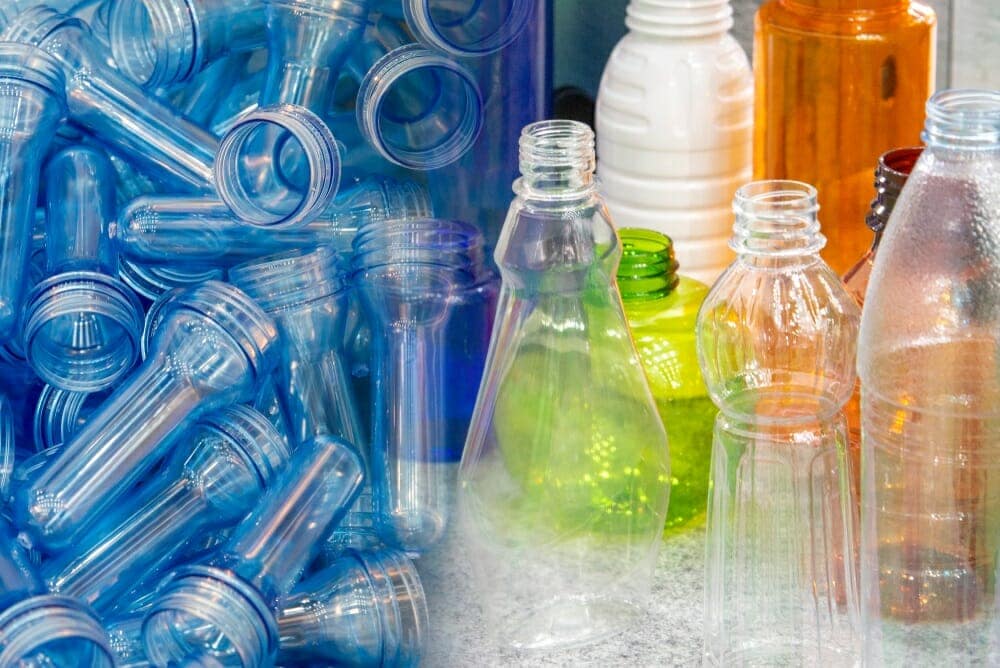
Packaging industries
1.3. Electronics
Plastics are commonly used in the electronics industry as insulation materials and protective casings for devices. Surface treatment is necessary to ensure that these casings can withstand electrical currents, resist corrosion, and allow coatings to adhere properly. This treatment enhances the safety, durability, and functionality of electronic devices.
1.4. Medical Devices
The medical industry requires the use of plastics that can be sterilized, coated, and effectively bonded with other materials. Surface treatments are applied to enhance adhesion for coatings, reduce friction in moving parts, and ensure that the plastic material is safe for use in medical applications. This process is essential for manufacturing equipment like catheters, syringes, and other plastic-based medical tools.
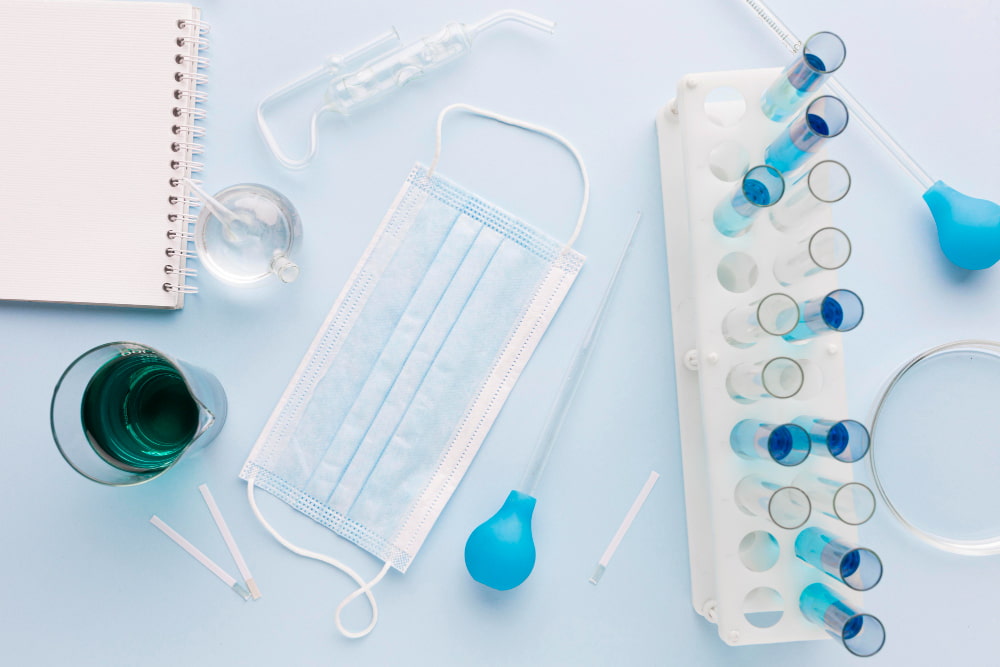
Medical devices made from plastic
1.5. Consumer Goods
In the production of everyday consumer goods such as kitchenware, toys, and appliances, plastic surface treatment ensures that paint and coatings adhere securely, leading to products that are more durable and visually appealing.
2. What Is A Completed Plastic Surface Treatment Process?
A comprehensive plastic surface treatment process involves multiple steps. These steps prepare the plastic for further processing, ensuring optimal adhesion and performance in the final products. Below are the steps for treating plastic surfaces.
2.1. Cleaning The Surface
The first step in plastic surface treatment is cleaning. Plastics can accumulate oils, dust, and residues from manufacturing processes. These contaminants must be removed to ensure the surface is clean and ready for further treatment. Various cleaning methods include:
- Solvent Cleaning: Using chemical solvents to remove oils and grease.
- Soap and Water: Mix a few drops of mild dish soap with warm water, then use a soft cloth or sponge to gently wipe the plastic surface.
- Non-Abrasive Cleaners: Apply a small amount of the product to a soft cloth or sponge, then gently wipe the plastic surface.
Before proceeding with surface modification techniques, it is crucial to ensure that the plastic surface is contaminant-free.
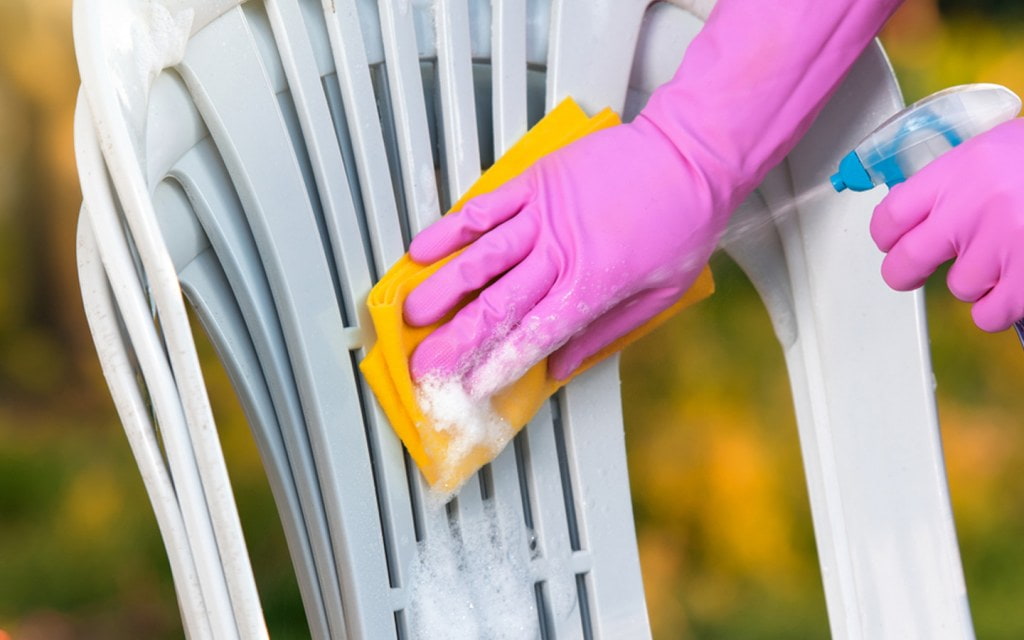
Cleaning the plastic surface
2.2. Surface Priming
Surface priming involves applying a primer to the activated plastic surface. Primers enhance adhesion by creating a better bonding layer between the plastic and the coating or adhesive. Depending on the application's requirements, primers can be solvent-based, water-based, or UV-cured. This step is crucial in industries such as automotive manufacturing, where strong adhesion between plastic parts and coatings is necessary to withstand harsh environments.
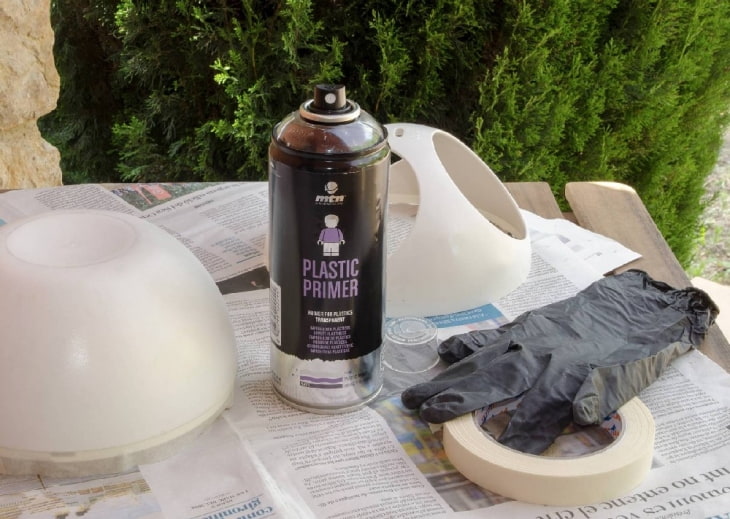
Surface priming
2.3. Coating Or Adhesive
After the surface has been cleaned and dried, the next step is to apply the coating or adhesive. Coatings can serve various functions, from enhancing the appearance of the plastic to providing protection against environmental factors such as UV rays, heat, and chemicals. Adhesives are used when plastic parts need to be bonded to other materials or components. There are several methods for applying coatings and adhesives to plastic parts:
- Spray Coating: This method involves applying the coating material to the plastic surface using a spray gun. It is commonly used in the automotive industry for plastic parts that require a uniform finish.
- Dipping: Dipping involves immersing the plastic part in a coating solution. This method is suitable for small parts that need to be evenly coated and is often used for consumer goods and electronic components.
- Roll Coating: In this method, the plastic part is passed through rollers that apply a uniform layer of coating. It is commonly used in packaging and film production.
- Adhesive Bonding: Adhesive application follows surface priming and ensures that plastic parts are securely bonded to other components, such as metals or other plastics.
2.4. Curing and Drying
Once the coating or adhesive has been applied, the next step is to cure and dry the plastic. Depending on the type of coating, this process can involve heat, UV light, or simply air drying. Proper curing ensures that the coating or adhesive bonds properly to the plastic and forms a durable finish.
- Heat Curing: This method is used for coatings that require high temperatures to bond to the plastic surface. The plastic part is placed in an oven where it is exposed to controlled temperatures for a specific time.
- UV Curing: UV curing is a fast and efficient method for curing coatings and adhesives. It uses ultraviolet light to harden the material and is commonly used in the electronics and packaging industries.
- Air Drying: Some coatings and adhesives simply require time to dry and bond to the plastic. This method is commonly used for household goods and packaging applications.
2.5. Printing
Plastic parts printing is a process in which the required patterns are printed on the surface of plastic parts using pad printing, screen printing, and transfer printing.
- Pad Printing: It is an indirect dentable rubber head printing technology. The designed pattern is first etched on the printing plate, the etching plate is coated with ink, and then most of the ink is transferred to the printed object through the silicone head.
- Screen Printing: It is the main printing method in stencil printing: the printing plate is in a net shape, and the ink on the printing plate is leaked from the through hole part of the plate to the substrate under the squeeze of the squeegee during printing. Usually, the wire mesh is made of nylon, polyester, silk or metal mesh.
- Transfer Printing: This method is divided into water transfer and thermal transfer.
Water transfer: It is a kind of printing that uses water pressure to hydrolyze the transfer paper/plastic film with color patterns.
Thermal transfer: It is a technique in which patterns or patterns are printed on heat-resistant adhesive paper, and the patterns and patterns of the ink layer are printed on the finished material by heating and pressing.
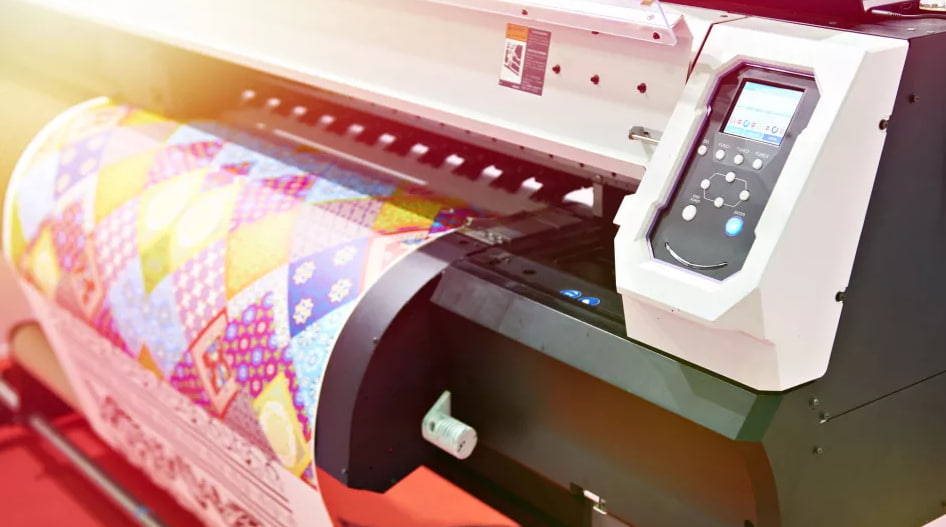
Printing
2.6. Laser Carving
Laser engraving or laser marking, is a process that uses optical principles to perform surface treatment. It is similar to screen printing. Through laser engraving, you can type or pattern on the surface of the product.
2.7. Biting Flowers
It is a process in which chemicals such as concentrated sulfuric acid are used to corrode the inside of the plastic molding mold to form lines in the form of snakes, etched, and plowed fields. After the plastic is molded through the mold, the surface has corresponding lines.
3. Conclusion
Plastic surface treatment is an essential process that enhances the functionality, durability, and performance of plastic components across various industries. By understanding the distinct steps involved, from cleaning to priming, coating, and curing you can ensure that your plastic materials are treated effectively for their intended use. Investing in the right surface treatment techniques will result in better performance, increased longevity, and a higher-quality finished product.
4. About EuroPlas
EuroPlas is a global leader in the production of masterbatch and plastic additives, known for delivering top-quality plastic raw materials to industries worldwide, including bioplastic compounds, color masterbatch, plastic additives, engineering plastic compounds, filler masterbatch and bio filler. EuroPlas products enhance the performance, appearance, and functionality of plastics used in various sectors such as packaging, automotive, electronics, and consumer goods.
Dedicated to sustainable development, EuroPlas is focused on creating eco-friendly material solutions that contribute to reducing environmental impact. Their commitment to excellence and innovation continues to make EuroPlas a trusted partner for businesses looking for high-quality and reliable plastic material solutions globally.
For more information and samples, please contact us HERE!