In industrial applications, efficiency, productivity, and product quality are paramount. That's where the PPA masterbatch comes into play. PPA masterbatch, or polymer processing aids masterbatch, offers an array of benefits that contribute to optimized manufacturing processes and superior end products. Let's delve into the advantages that make PPA masterbatch a game-changer in industrial applications.
1. Understanding PPA masterbatch
1.1. The definition of PPA masterbatch
PPA masterbatch, also known as polymer processing aids masterbatch, is a specialized additive formulation used in polymer processing applications. It is typically composed of a carrier resin, such as polyethylene or polypropylene, blended with a small concentration of active ingredients known as polymer processing aids (PPAs). These PPAs are typically high molecular weight compounds, such as acrylic copolymers or fluoropolymers, that possess unique properties to enhance the processing characteristics of polymers.
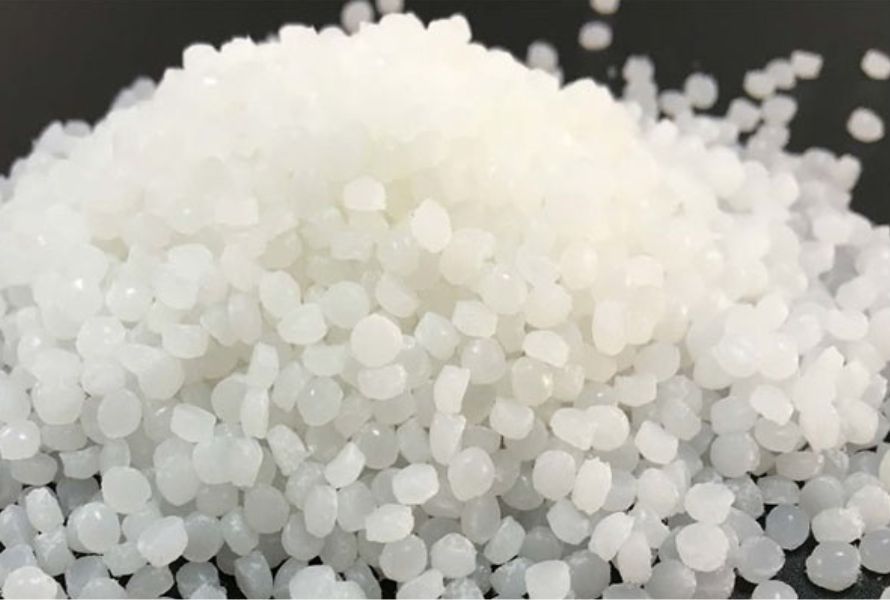
PPA masterbatch (processing aids masterbatch) is a specialized additive formulation used in polymer processing applications
1.2. The purpose of PPA masterbatch
The primary purpose of PPA masterbatch is to improve the processing efficiency and performance of polymers during various manufacturing processes. When added to polymer formulations, PPA masterbatch acts as a lubricant and flow enhancer, reducing the friction between polymer molecules. This helps to overcome processing challenges and optimize the flow behavior of the melted polymer.
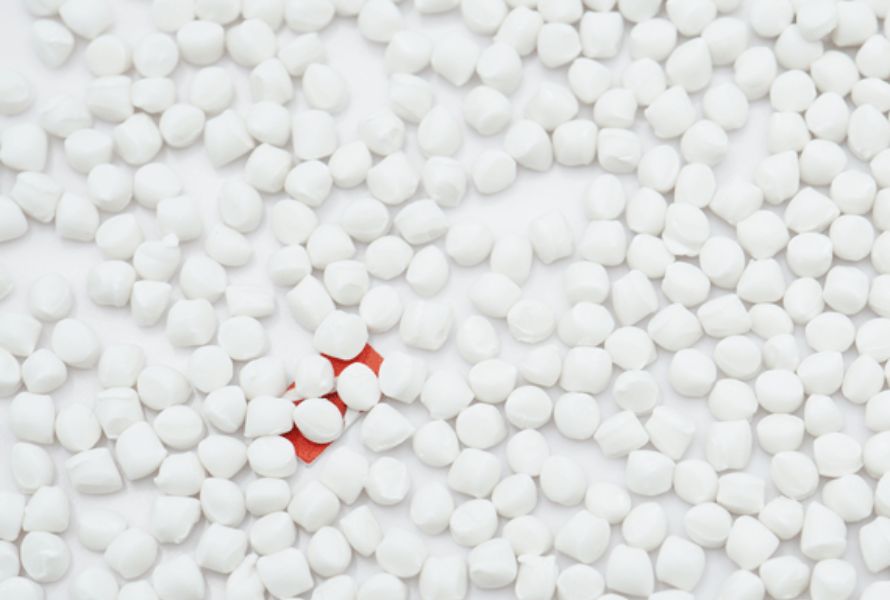
Enhancing polymer performance and processing efficiency across a range of manufacturing processes is the main goal of PPA masterbatch
1.3. How PPA masterbatch improves the processing characteristics of polymers
1.3.1 Melt flow improvements
PPA masterbatch reduces the viscosity and melt strength of polymers, allowing for smoother and more uniform flow during processing. It helps to overcome processing difficulties such as melt fracture, die build-up, and sticking. By reducing the resistance to flow, PPA masterbatch enables better control over the polymer melt, leading to improved productivity and enhanced processing efficiency.
1.3.2. Enhanced mold filling
The addition of PPA masterbatch improves the flowability of melted polymers, allowing them to fill the mold cavities more effectively. This leads to better replication of intricate details and reduced occurrence of surface defects, resulting in improved part quality and dimensional accuracy. The enhanced mold filling also helps reduce the processing pressure, enabling the use of lower processing temperatures and reducing the risk of thermal degradation.
1.3.3. Reduction of processing temperature
PPA masterbatch reduces the melt viscosity of polymers, enabling them to flow more easily at lower processing temperatures. This temperature reduction can result in energy savings during processing and minimize the risk of thermal degradation, particularly for heat-sensitive polymers. By optimizing the processing temperature, PPA masterbatch helps maintain the integrity of the polymer and improves the overall efficiency of the manufacturing process.
1.3.4. Homogeneity and consistency
PPA masterbatch promotes better dispersion and distribution of additives, fillers, and pigments throughout the polymer matrix. This ensures a more homogeneous and consistent blend, leading to improved product quality and performance. The enhanced dispersion also helps prevent agglomeration and reduces the risk of uneven properties within the final product.
2. Benefits of PPA masterbatch in industrial application
2.1. Enhanced processability
PPA masterbatch significantly improves the processability of polymers during manufacturing. It reduces viscosity and enhances melt flow properties, making the materials easier to process. This leads to smoother processing operations, reduced processing difficulties, and improved overall productivity. Manufacturers can achieve higher production rates and faster cycle times, resulting in increased efficiency and cost-effectiveness.
2.2. Improved surface finish
The use of PPA masterbatch in industrial applications helps achieve superior surface finish in the final products. It minimizes surface defects, such as flow marks, weld lines, and sink marks, resulting in a smoother and more aesthetically pleasing appearance. This benefit is particularly crucial in industries like automotive, consumer goods, and electronics, where visual appeal is essential.
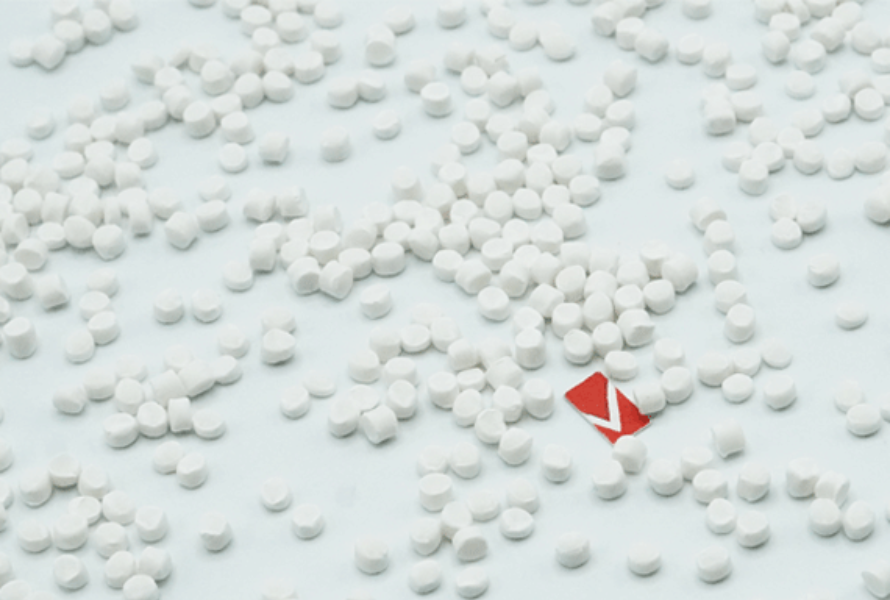
PPA masterbatch is used in industrial applications to help produce final products with superior surface finishes
2.3. Reduced processing issues
PPA masterbatch acts as a lubricant and reduces the friction between polymer molecules during processing. This property helps prevent issues like melt fracture, die build-up, and sticking, which can hamper productivity and degrade product quality. By mitigating these processing issues, PPA masterbatch ensures smoother operations, reduces downtime for maintenance, and improves overall production efficiency.
2.4. Enhanced mechanical properties
PPA masterbatch improves the mechanical properties of polymers, making them stronger, tougher, and more durable. It enhances dimensional stability, impact resistance, and tensile strength of the materials. This benefit is particularly valuable in applications where robustness and reliability are crucial, such as in automotive components, construction materials, and industrial equipment.
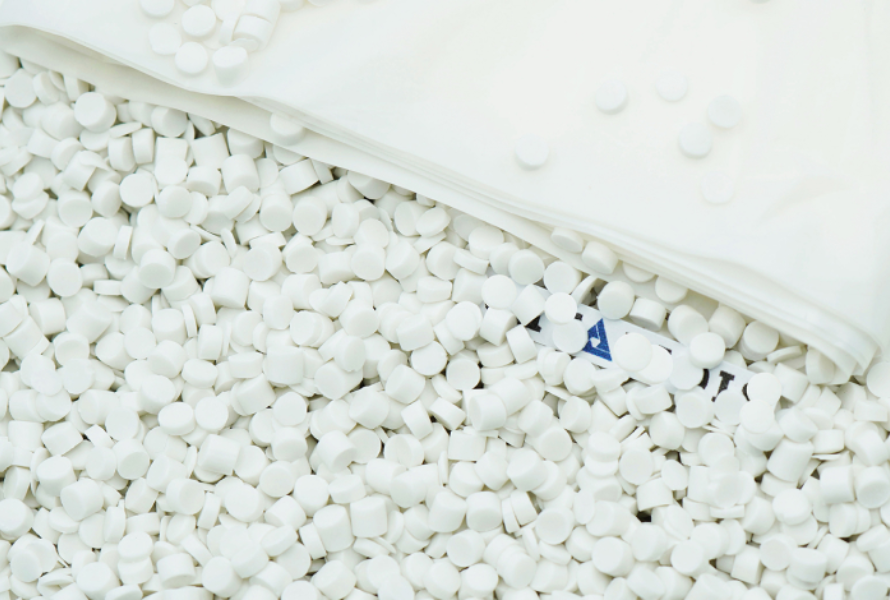
The PPA masterbatch strengthens, toughens, and extends the mechanical properties of polymers
2.5. Cost savings
The use of PPA masterbatch can lead to significant cost savings in industrial applications. By enhancing processability and reducing processing difficulties, manufacturers can minimize material waste and scrap rates. The improved melt flow properties and reduced energy consumption contribute to cost-efficiency and sustainability. Additionally, the enhanced mechanical properties of the final products can extend their lifespan, reducing the need for frequent replacements and maintenance.
2.6. Compatibility with various polymers
PPA masterbatch exhibits excellent compatibility with a wide range of polymers, including polyethylene (PE), polypropylene (PP), polyvinyl chloride (PVC), polystyrene (PS), and more. This versatility allows manufacturers to incorporate PPA masterbatch into different polymer formulations without compromising performance. It ensures consistent results across various materials and applications.
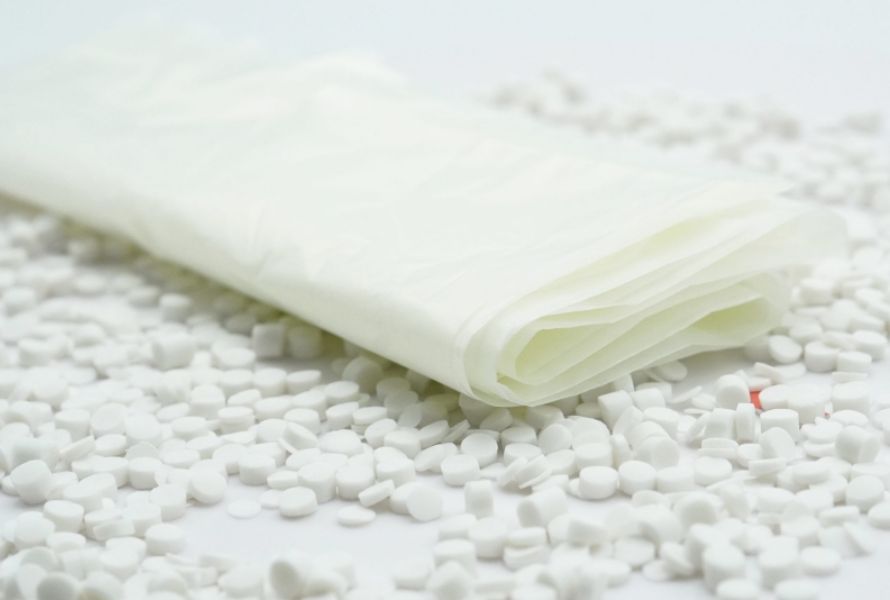
PPA masterbatch shows outstanding polymer compatibility across a broad spectrum
2.7. Facilitates complex processing techniques
PPA masterbatch enables the successful implementation of complex processing techniques, such as blow molding, injection molding, extrusion, and film casting. It improves melt stability, reduces viscosity variations, and enhances flow control during these intricate manufacturing processes. This benefit opens up possibilities for innovative product designs and advanced manufacturing techniques.
2.8. Customizable solutions
PPA masterbatch formulations can be customized to address specific processing challenges or to meet unique requirements of different industrial applications. Manufacturers can work closely with suppliers to tailor PPA masterbatch solutions that optimize processability, enhance product quality, and address specific industry regulations or standards. This customization ensures a more precise and effective solution for each application.
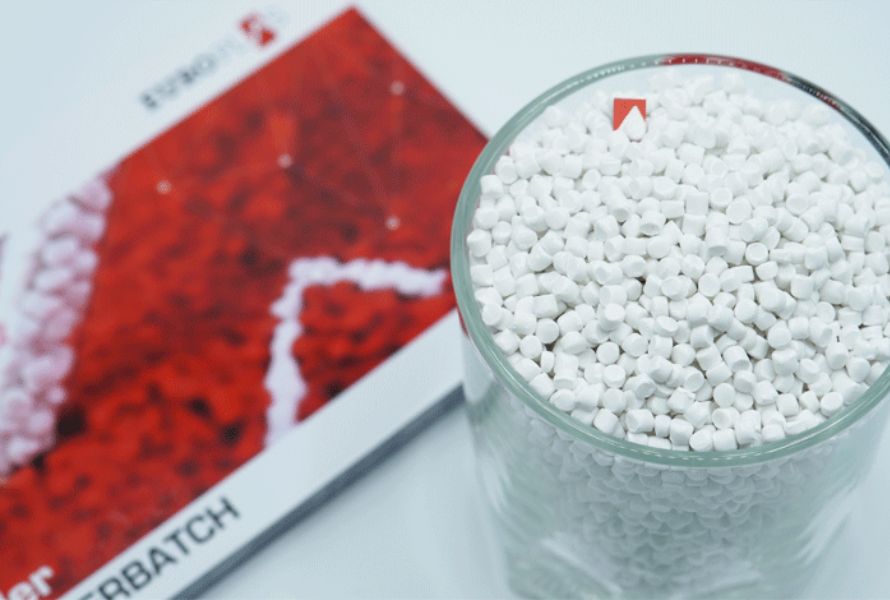
PPA masterbatch formulations can be tailored to meet the particular needs of various industrial applications or to address particular processing challenges
2.9. Regulatory compliance
PPA masterbatch formulations can be developed to comply with industry regulations and standards, such as FDA (Food and Drug Administration) regulations for food contact applications or specific safety requirements. This ensures that the final products meet the necessary compliance criteria, allowing manufacturers to confidently use PPA masterbatch in applications with strict regulatory guidelines.
3. PPA masterbatch at EuroPlas
With nearly 14 years of experience, EuroPlas has emerged as a renowned manufacturer of filler masterbatch, establishing a distinguished reputation within the industry. EuroPlas offers PPA masterbatch to cater to diverse application requirements and enhance the quality of your end products.
To learn more about EuroPlas' PPA masterbatch, kindly visit the PPA masterbatch Search - EuroPlas - The world's largest filler masterbatch manufacturer.
4. Conclusion
PPA masterbatch has emerged as a transformative force in industrial applications, fundamentally reshaping manufacturing processes with its wide-ranging benefits. By enhancing efficiency, elevating product quality, and driving cost savings, PPA masterbatch offers an unparalleled advantage to industrial businesses.
Its ability to improve processability, deliver impeccable surface finishes, enhance mechanical properties, exhibit compatibility with diverse polymers, and enable advanced processing techniques empowers manufacturers to reach unprecedented levels of productivity and innovation. With the integration of PPA masterbatch into their operations, industrial businesses can optimize performance, craft superior products, and maintain a competitive edge amidst the ever-evolving landscape of today's industries.
If you are interested in exploring our products, we encourage you to get in touch with us promptly or visit our blog for additional information on the plastic industry.