As you rightly pointed out, delving deeper into the PBT family is crucial. As one of the most widely used and versatile PBT variants, this product line offers a range of specialized grades that are worth exploring further. Let's take a closer look at some of the key grades.
1. What is PBT?
PBT, or Polybutylene Terephthalate, is a widely used engineering thermoplastic polymer known for its excellent mechanical, thermal, and electrical properties. This versatile material has found application in a diverse range of industries, making it a crucial component in modern manufacturing.
Some key properties of them include:
- High strength and stiffness: PBT has excellent mechanical properties, including high tensile strength, flexural strength, and impact resistance.
- Dimensional stability: It exhibits good dimensional stability, which makes it suitable for applications where precise dimensions are required.
- Thermal resistance: The material can withstand high temperatures up to around 150°C (302°F) without significant degradation of its properties.
Electrical insulation: PBT has good electrical insulation properties, making it suitable for use in electrical and electronic components.
- Chemical resistance: This material exhibits good resistance to a wide range of chemicals, including oils, fuels, and mild acids and bases.
- Easy processing: PBT can be easily molded, extruded, or machined, making it suitable for a variety of manufacturing processes.
It is often compared to another engineering plastic, Polyethylene Terephthalate (PET), but PBT generally has better mechanical properties, thermal stability, and chemical resistance compared to PET. It is commonly used in applications such as automotive parts (e.g., engine components, electrical connectors), electrical and electronic components (e.g., switches, connectors, housings), and various industrial and consumer products.
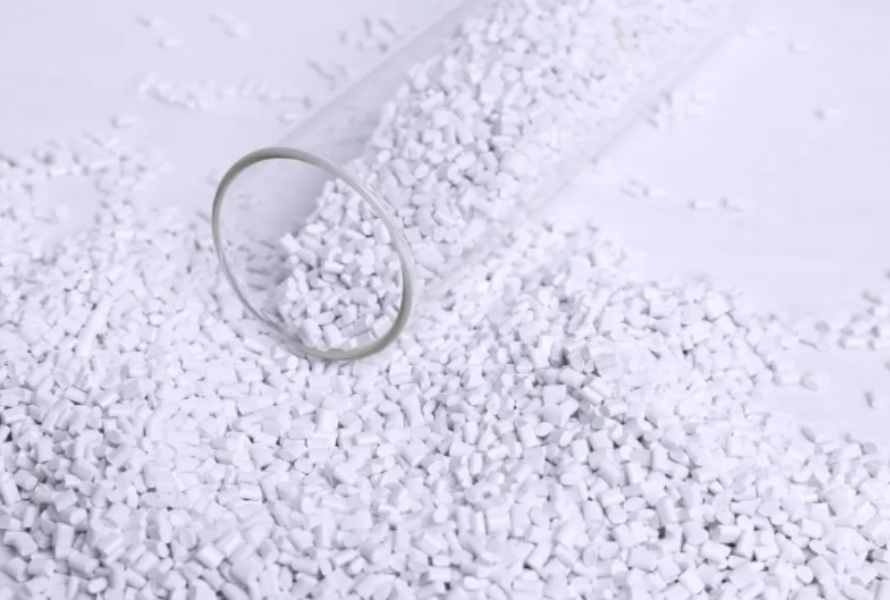
PBT's versatile properties make it a sought-after engineering material, driving innovation across industries.
2. Different Types of PBT
2.1. Standard PBT
The standard PBT grade serves as the foundation for many of the specialized variants, such as the glass-filled and mineral-filled grades.
The standard, unmodified grade is a popular choice for a wide range of applications, such as housings and enclosures for electrical and electronic devices, automotive interior and exterior components, and various industrial and consumer goods.
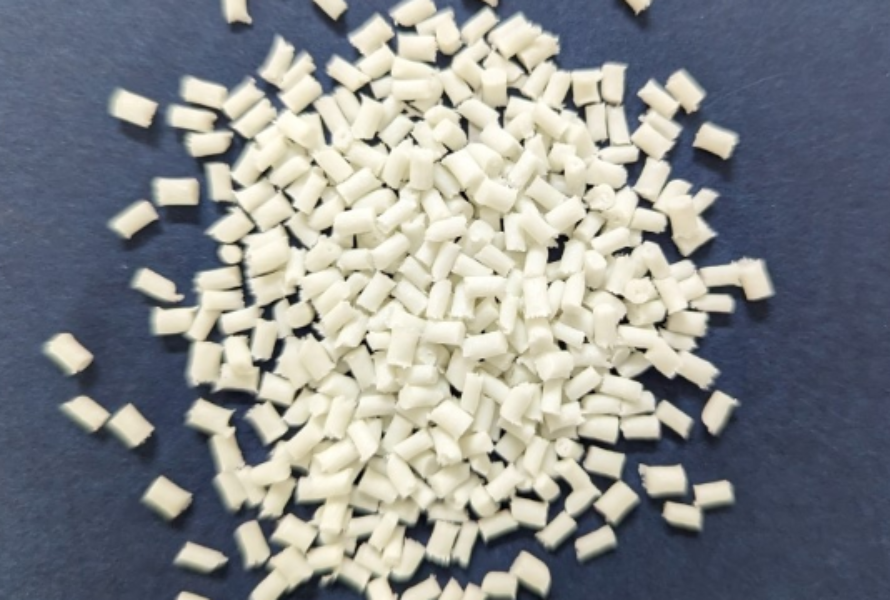
The standard PBT grade serves as the foundation for many specialized variants.
2.2. PBT GF
The most widely used GF type is PBT GF30, which contains 30% glass fiber reinforcement. This material offers an excellent balance of mechanical properties, dimensional stability, and cost-effectiveness, making it a popular choice for a wide range of applications.
PBT GF30 is commonly found in structural automotive components, power tool housings, gears and pulleys in industrial machinery, and various electrical and electronic enclosures. The addition of glass fibers significantly enhances the stiffness, strength, and thermal resistance of the base polymer, allowing it to meet the demanding requirements of many engineering applications
Read more: PBT GF30: What is it? Properties, key benefits & uses
Besides GF30, there are also GF20 and GF40:
- GF20: This grade contains 20% glass fiber reinforcement. It offers a balance of mechanical properties and cost-effectiveness, making it suitable for applications that don't require the highest level of stiffness and strength.
- GF40: Containing 40% glass fiber, this grade provides enhanced stiffness, tensile strength, and dimensional stability compared to the PBT GF30. It is often used in more demanding applications that need higher performance.
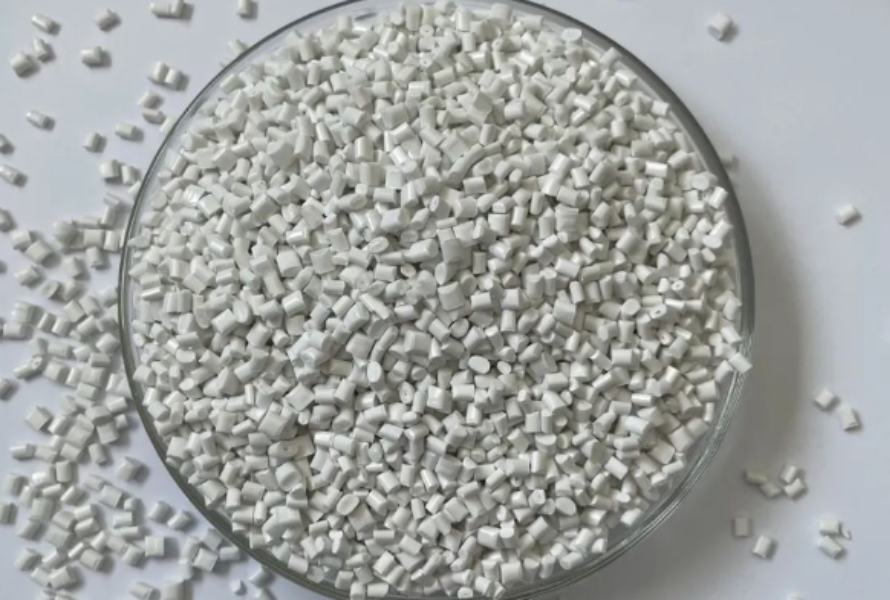
PBT GF 30 refers to a type of Polybutylene Terephthalate that is reinforced with 30% glass fibers.
2.3. PBT MF
PBT MF30, with 30% mineral filler, is the most prevalent Mineral-Filled PBT grade. It is often used in housings for power tools and small appliances, telecommunications equipment parts, and various fittings and fasteners due to its improved dimensional stability, reduced shrinkage, and cost-effective performance.
2.4. Flame-retardant PBT
For applications that demand robust fire safety, PBT FR20, containing 20% flame retardant additives, is the most common choice for electrical and electronic enclosures, switchgear, and circuit breaker components, where exceptional fire safety is a critical requirement. This highly flame-resistant PBT grade ensures reliable performance in applications with stringent fire safety regulations.
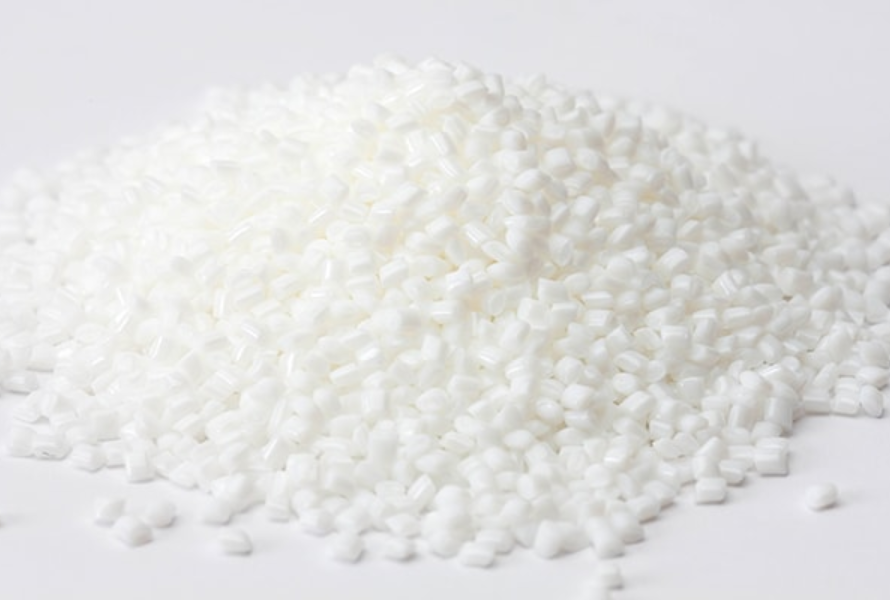
PBT FR20 with 20% flame retardant additives significantly improves fire resistance.
2.5. Heat-stabilized PBT
When both flame retardancy and heat resistance are necessary, the PBT GF20 FR HS grade is a popular choice. This material combines the heat-stabilized properties with flame-retardant additives, making it a suitable option for electrical and electronic components exposed to high temperatures.
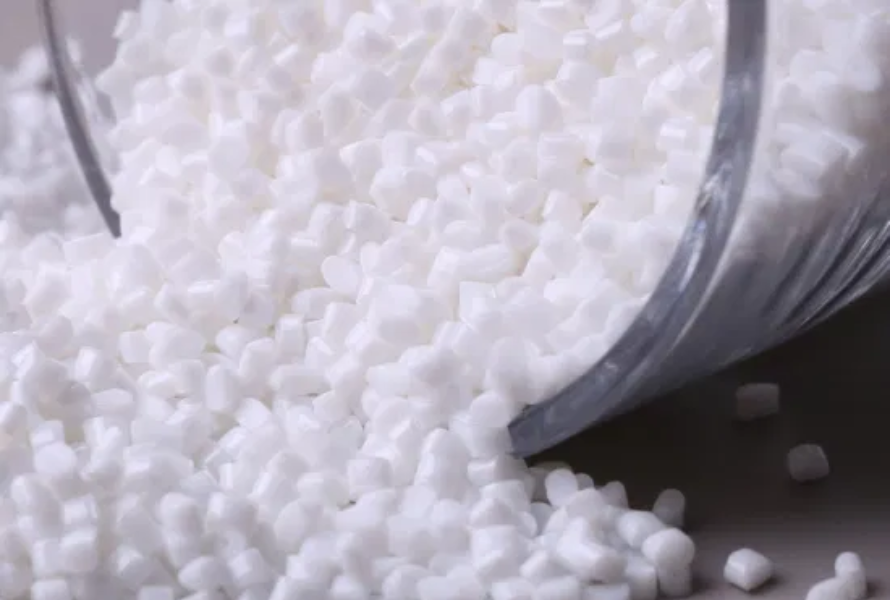
PBT GF20 FR HS is a heat-stabilized grade that combines 20% glass fiber reinforcement with flame retardant additives.
3. Choosing the Right PBT
By carefully evaluating these key factors, you can select the most appropriate material that will provide the desired performance, cost-effectiveness, and compliance for your specific application requirements.
3.1. Performance requirements
Determining the performance requirements for the intended application is crucial when selecting the appropriate PBT grade.
The mechanical properties, such as strength, stiffness, and impact resistance, need to match the demands of the end-use. Thermal stability is also a critical factor, especially for components that will be exposed to high temperatures or repeated thermal cycling.
For certain applications, additional specialized properties may be required, such as flame retardancy for electrical enclosures or food-contact compliance for components in contact with consumables. Carefully evaluating these performance criteria will help narrow down the PBT options to ensure the selected material can reliably meet the product's functional needs.
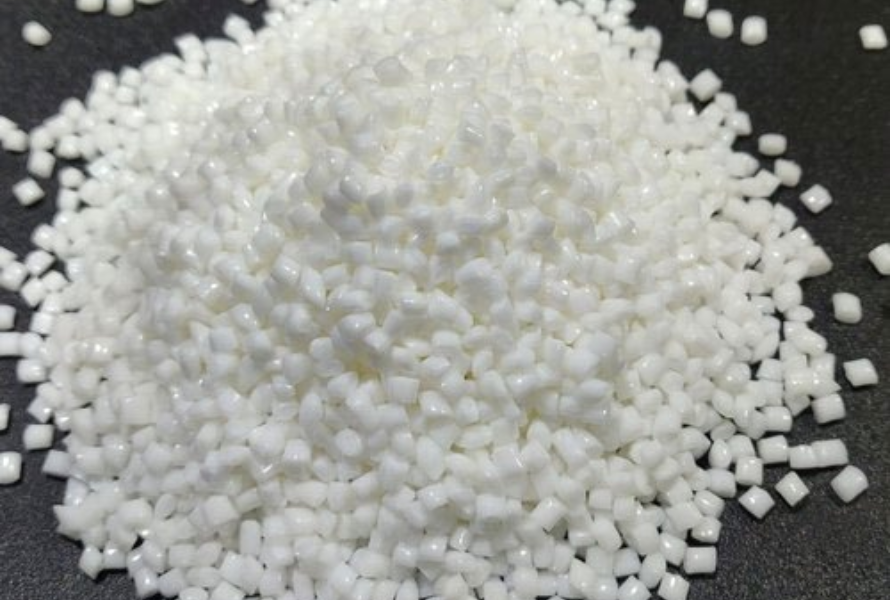
Selecting the right PBT grade is critical and depends on understanding the specific performance requirements of the intended application.
3.2. Processing characteristics
The processing method chosen for manufacturing the PBT part is a key consideration when selecting the right material grade.
Factors like melt viscosity, shrinkage, and ease of flow during injection molding or extrusion will impact the suitability of different PBT variants. For instance, a PBT with lower melt viscosity may be preferred for complex geometries or thin-walled parts to ensure complete mold filling and replication of fine details. Dimensional stability is also crucial, as the chosen polymer should exhibit predictable shrinkage and warpage behavior to maintain tight tolerances. Aligning the material properties with the specific processing techniques is essential for achieving consistent, high-quality components.
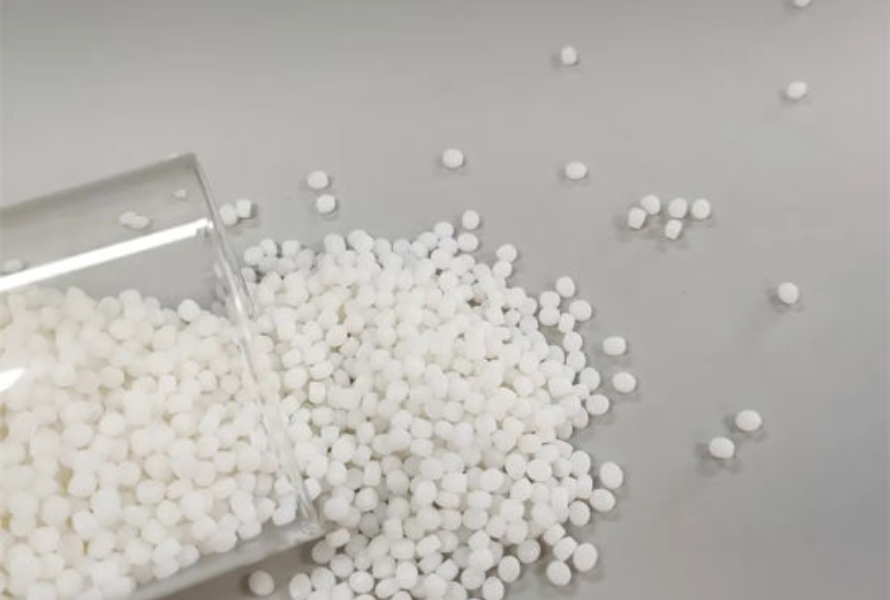
The manufacturing process is an important factor when choosing the optimal PBT grade.
3.3. Cost and availability
While the more specialized PBT variants, such as glass-filled or flame-retardant grades, may offer enhanced performance, they often come at a higher cost. For high-volume applications or cost-sensitive products, a standard PBT or a mineral-filled PBT may provide a more cost-effective solution without sacrificing essential properties.
Additionally, ensuring the availability and reliable supply of the chosen PBT material is crucial, as disruptions in the supply chain can impact the manufacturing process. Striking the right balance between cost, performance, and material availability is key when choosing the optimal PBT for a given application.
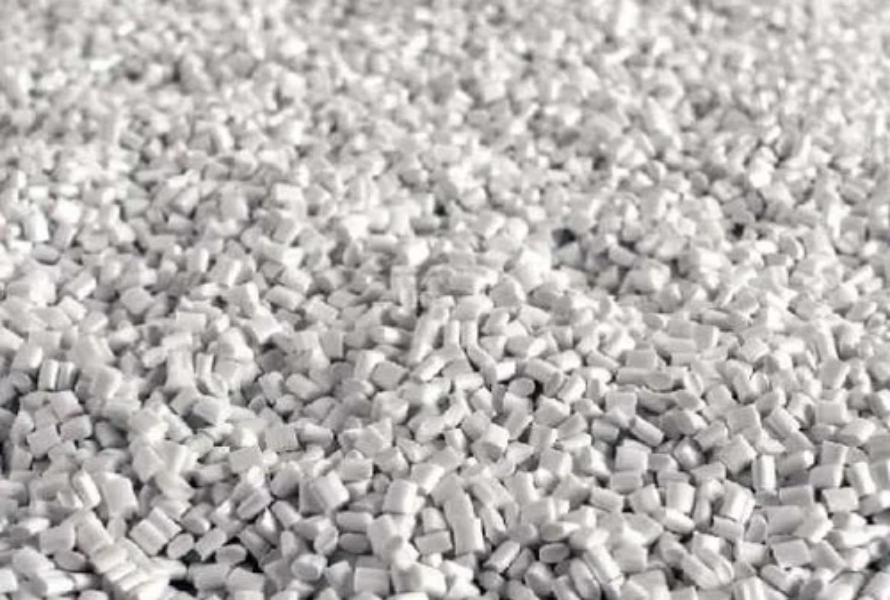
The budget and production volume requirements play a significant role in selecting the appropriate PBT grade.
4. Conclusion
The PBT GF family offers a diverse range of grades that cater to the specific needs of various applications. By thoroughly understanding the unique characteristics and capabilities of these materials, designers and engineers can make informed decisions to select the optimal grade for their products.
The most widely adopted glass-reinforced variant is PBT GF 30 (the 30% fiber-filled grade). This material offers an excellent balance of mechanical properties, dimensional stability, and cost-effectiveness, making it a popular choice for a broad spectrum of applications.
Key considerations when choosing the suitable one include performance requirements, processing characteristics, cost and availability. By understanding this, you can unlock new design possibilities, improve product reliability, and deliver innovative solutions for evolving market needs.
5. About EuroPlas
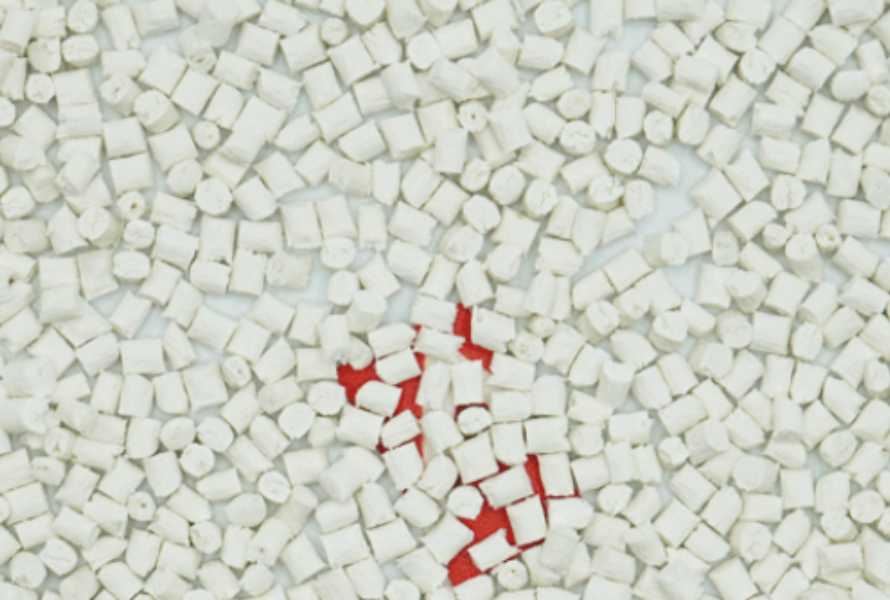
EuroPlas is committed to providing exceptional plastic raw material solutions that optimize production costs and strengthen market competitiveness. As a reliable supplier, we offer high-quality PBT GF-FR compound with the following features:
- All functions in one single material
- Allow to directly processed without any materials required
- Tailor-made based on end-products' requirements
- Prevent abrasion and discoloration due to UV light, thus improving end-products' durability and longevity
- Great flame retardancy and high stiffness
Contact us today to unlock the benefits of our high-quality materials and to receive advice and support.