In the world of industrial plastics, black PE—short for black polyethylene—has become a staple material in multiple sectors. Known for its toughness, chemical resistance, and UV stability, black PE finds applications ranging from municipal piping to greenhouse film. But what exactly makes black PE different from standard polyethylene? Why is it black, and how does that affect its properties? This article dives deep into black PE’s characteristics, variations, advantages, and real-world uses.
1. What is black PE?
Polyethylene (PE) is one of the most commonly used thermoplastics in the world. It's made by polymerizing ethylene gas, forming long chains of hydrocarbons. Depending on how densely these molecules are packed, PE comes in various forms: high-density (HDPE), low-density (LDPE), and linear low-density (LLDPE).
Black PE is simply polyethylene that has been compounded with carbon black or other black pigments. The addition of carbon black serves multiple functions—it doesn't just color the material but also drastically enhances its resistance to ultraviolet (UV) radiation. This UV shielding makes black PE particularly suitable for outdoor use, where sun exposure could otherwise degrade unmodified PE over time.
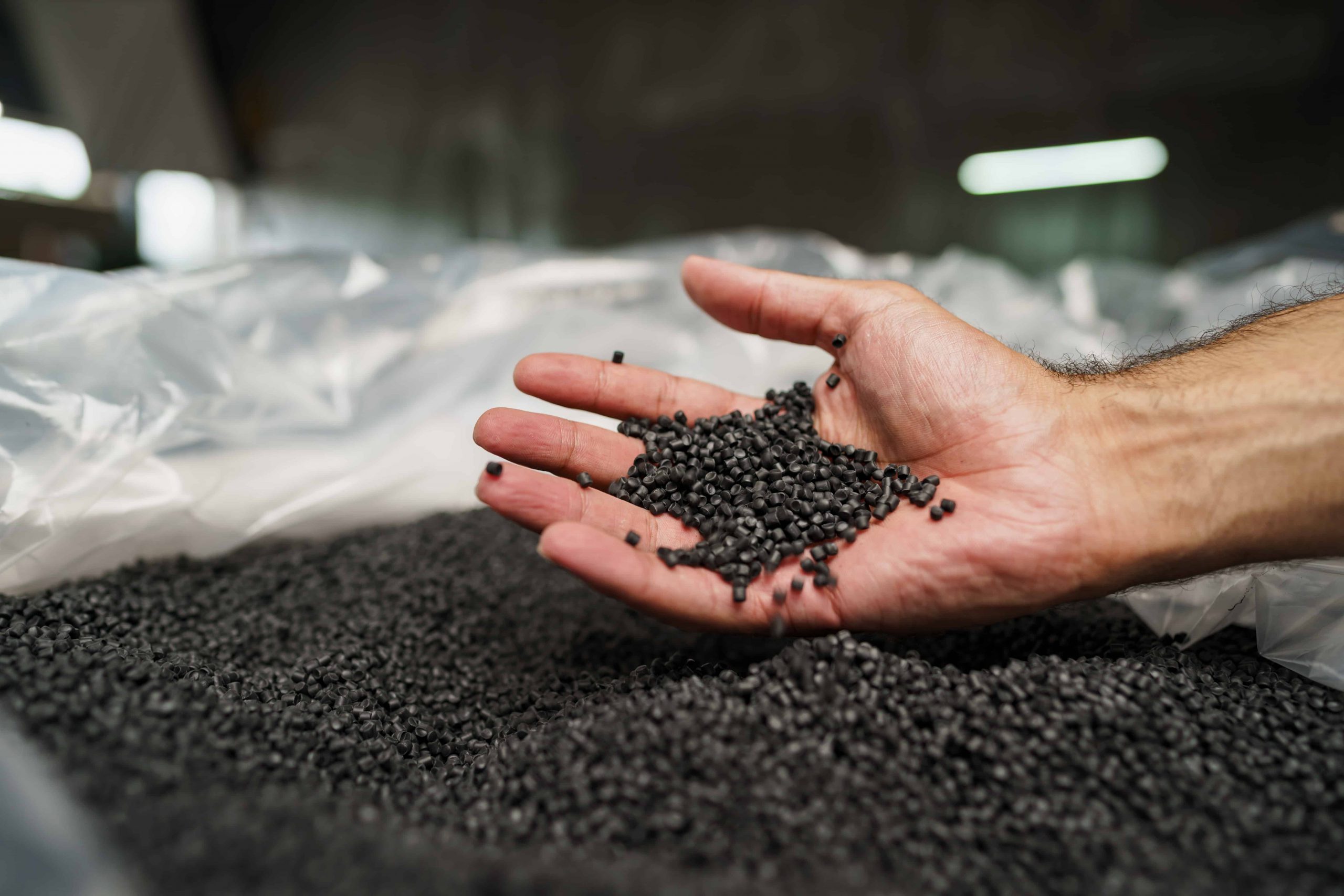
Black PE is simply polyethylene that has been compounded with carbon black or other black pigments.
2. Types of black PE and their properties
Black PE isn’t a single material but a category encompassing several types of polyethylene, each with specific performance characteristics:
2.1. Black HDPE (High-Density Polyethylene)
Black HDPE is known for its high strength-to-density ratio. It is stiff, durable, and chemically resistant, making it suitable for pressure piping, water tanks, and heavy-duty containers. Its resistance to UV and cracking under environmental stress is further improved with carbon black, allowing it to withstand harsh conditions for decades.
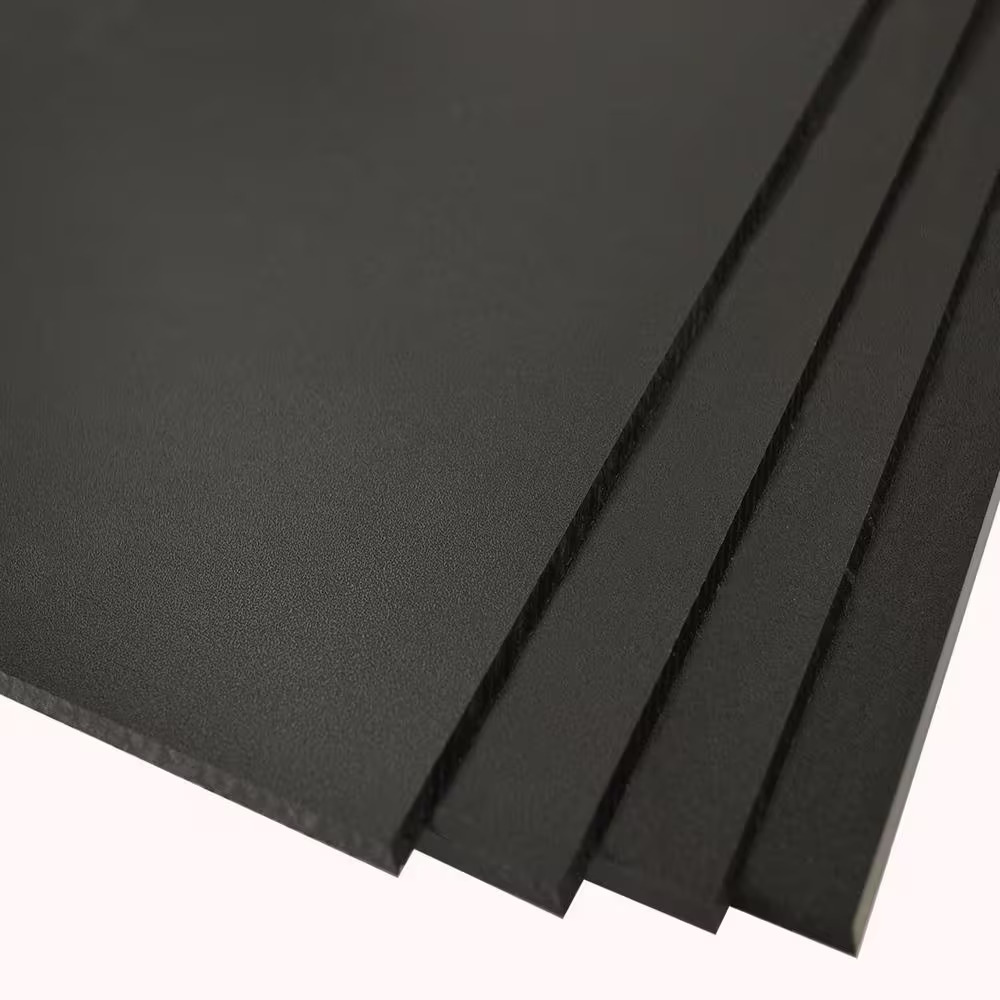
Black HDPE is known for its high strength-to-density ratio.
2.2. Black LDPE (Low-Density Polyethylene)
Black LDPE has a more flexible structure due to its lower molecular density. While it is not as strong as HDPE, its pliability makes it ideal for film applications such as protective plastic sheeting or geomembranes. When colored black, it gains added outdoor durability.
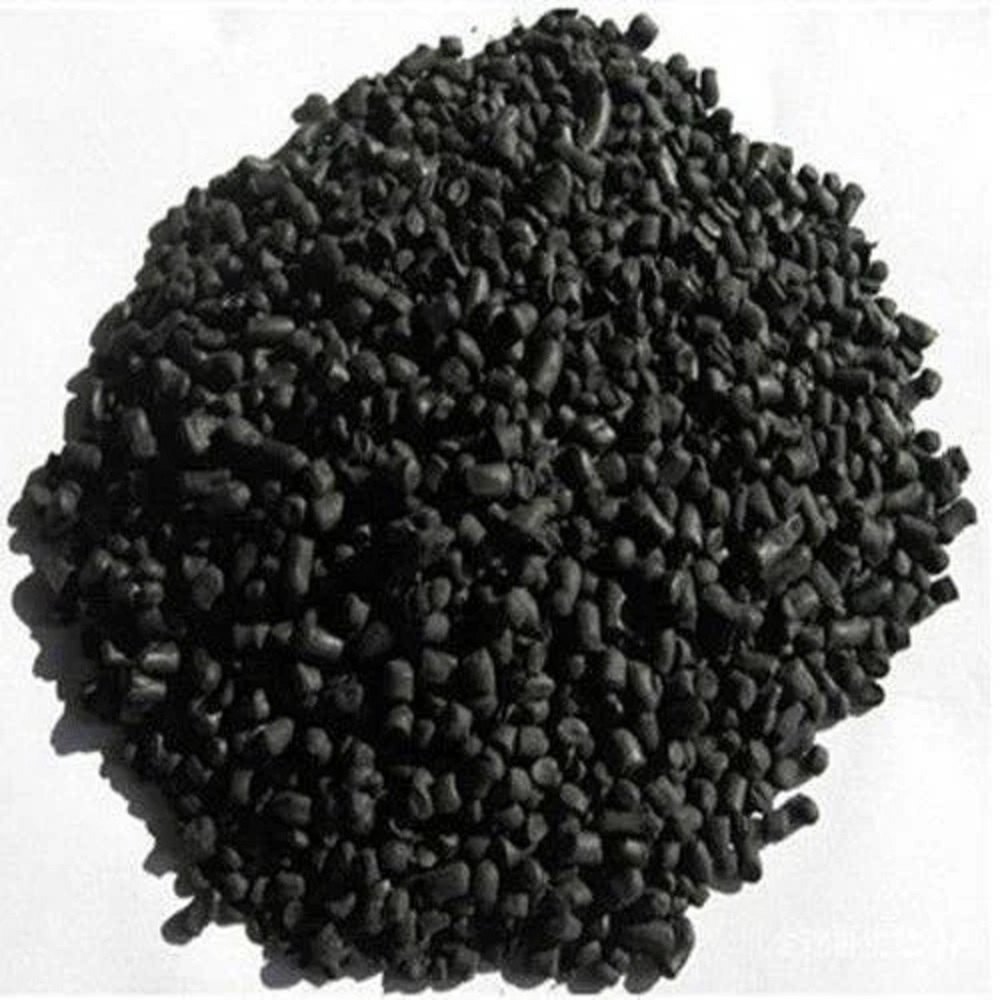
Black LDPE has a more flexible structure due to its lower molecular density.
2.3. Black LLDPE (Linear Low-Density Polyethylene)
Black LLDPE balances strength and flexibility, often used in stretch films, tubing, and liners. It is less rigid than HDPE but tougher than LDPE. Black pigmentation extends its lifespan in outdoor packaging, tarpaulins, and agricultural covers.
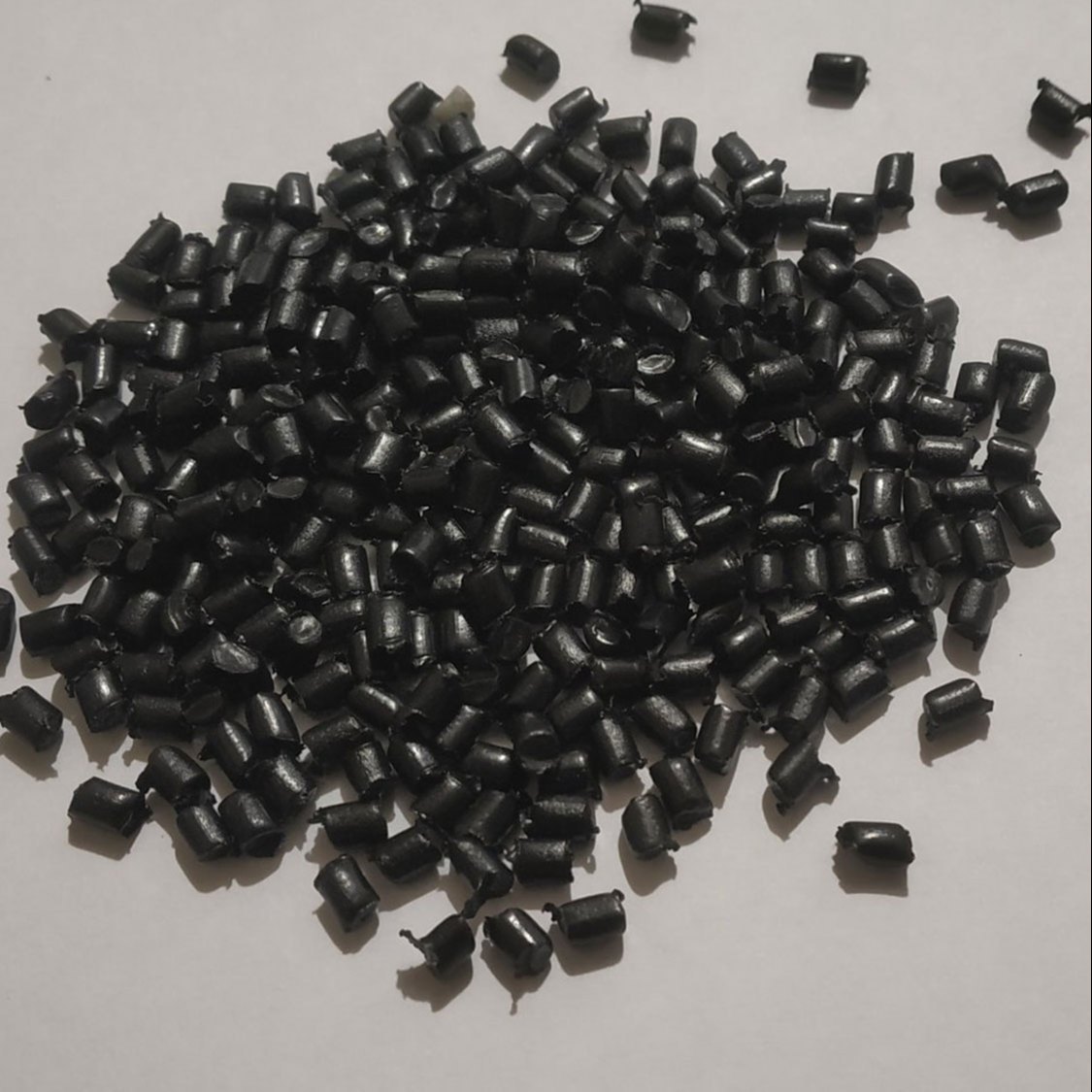
Black LLDPE balances strength and flexibility, often used in stretch films, tubing, and liners.
3. Why is it black? The role of carbon black
The defining feature of black PE is the presence of carbon black—a finely divided form of elemental carbon. Typically added at concentrations of 2–3%, carbon black absorbs and dissipates UV rays, preventing degradation of the polyethylene chains.
UV light can break down polymer chains, leading to discoloration, embrittlement, and loss of mechanical properties. Carbon black works like sunscreen for PE, blocking out UV rays and acting as a thermal stabilizer. This makes black PE a go-to choice for outdoor applications that demand long service life.
Moreover, carbon black also acts as a conductive agent in certain formulations, allowing black PE to be used in applications where static dissipation or electrical conductivity is required—such as in cable insulation or electronic packaging.
4. Applications across industries
Thanks to its durability, cost-effectiveness, and adaptability, black PE is employed in a wide range of sectors:
4.1. Infrastructure and piping
One of the most common uses of black HDPE is in piping systems—for potable water, wastewater, natural gas, and even fire suppression systems. Its chemical resistance and long-term durability reduce maintenance and replacement costs for municipalities.
Black PE pipes are often extruded in large diameters and can last over 50 years underground without significant degradation. Their flexibility also allows for trenchless installation methods such as horizontal directional drilling.
4.2. Agriculture
In agriculture, black PE is used for irrigation tubing, greenhouse films, and mulch films. The carbon black content not only resists UV rays but also absorbs sunlight, helping to warm the soil and control weed growth under mulch films.
Greenhouse films made of black LLDPE help control light penetration and maintain humidity levels. They also resist punctures from wind or equipment, which is crucial for maintaining controlled environments.
4.3. Construction
Black PE plays a significant role in the construction industry as vapor barriers, damp-proof membranes, and protective films. These sheets protect building materials from moisture and contamination, and their UV resistance means they can be exposed to sunlight without rapid degradation.
It’s also used for temporary enclosures and surface protection during construction or renovation projects. Black PE sheeting provides privacy, weather protection, and debris containment.
4.4. Packaging and consumer goods
LLDPE films pigmented black are used in stretch wrap for industrial packaging, garbage bags, and pallet covers. These films are both opaque (concealing contents) and UV-resistant, which is advantageous for long-term outdoor storage.
Other consumer applications include black PE containers, trays, and even piping for DIY plumbing kits. Their clean appearance and resistance to staining make them ideal for both functional and aesthetic purposes.
4.5. Electronics and telecom
Black PE compounds with conductive carbon black are used in cable jacketing and electronic packaging. These prevent static build-up and protect sensitive components from electrostatic discharge.
In fiber optic cable applications, black PE jacketing protects inner components from moisture and UV exposure, ensuring signal integrity over long distances.
5. Advantages of black PE
Black PE offers a well-rounded set of advantages that make it ideal for many industrial and consumer applications. One of its most significant features is its resistance to ultraviolet radiation, which is achieved through the addition of carbon black during manufacturing. This enhancement allows black PE products to maintain their integrity and performance even under prolonged exposure to sunlight, making them suitable for outdoor environments such as agricultural films, piping, and roofing membranes.
Another major benefit of black PE is its chemical resistance. It can withstand contact with a variety of corrosive substances, including acids, bases, and many solvents, which extends its applicability to chemical storage, transport, and protective layers in industrial settings. Depending on the formulation, black PE can also range from being flexible (as in LLDPE) to highly rigid and durable (as in HDPE), giving manufacturers considerable versatility in design and usage.
From a cost perspective, black PE is a more affordable alternative to engineered plastics while still delivering solid mechanical and environmental performance. It can be processed using conventional plastic technologies like extrusion, blow molding, injection molding, and rotational molding, which adds to its attractiveness from a manufacturing efficiency standpoint.
Its black coloration also serves a practical purpose—it helps conceal dirt, imperfections, or recycled content within the product. This makes black PE a popular choice for secondary packaging, industrial liners, and waste management applications.
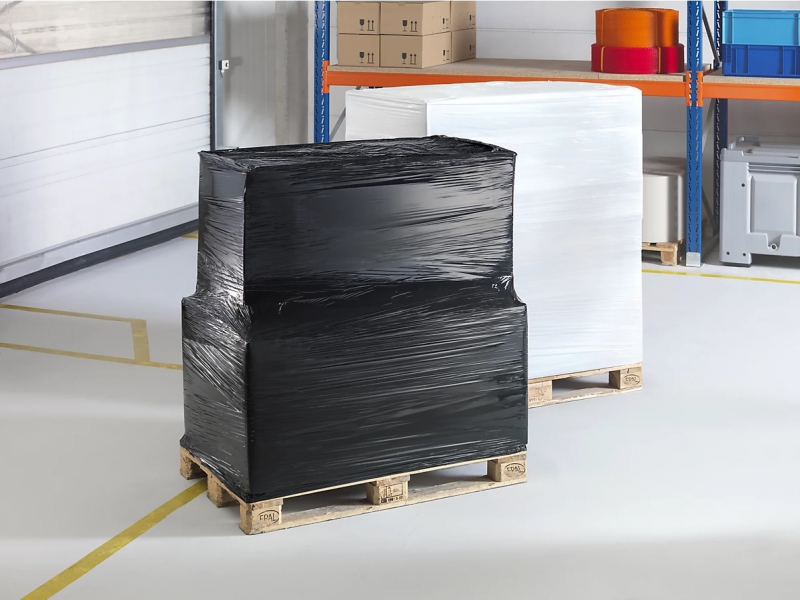
From a cost perspective, black PE is a more affordable alternative to engineered plastics.
6. Considerations and limitations
Despite its numerous strengths, black PE comes with a few caveats that are worth considering before choosing it for a specific application. One of the primary concerns is its recyclability. The black pigment, especially carbon black, hinders automatic optical sorting systems used in recycling facilities. As a result, black PE often ends up in lower-grade recycling streams or is not recycled at all, unless specific measures are in place.
Another limitation is its compatibility with food-grade applications. While some black PE formulations are approved for food contact, others may contain additives that can migrate into food products. This makes it crucial to verify regulatory compliance before using black PE in food packaging or handling systems.
Thermal resistance is also a limiting factor. With melting points ranging between 105°C and 135°C, black PE is not suitable for high-temperature processes or environments. It can deform under heat and is not recommended for applications involving sustained thermal exposure, such as hot liquid storage or high-temperature piping.
Ultimately, while black PE excels in many areas, it is essential to evaluate its suitability based on the specific environmental, regulatory, and mechanical demands of each use case.
Despite its strengths, black PE is not without drawbacks:
- Recyclability: The carbon black pigmentation makes optical sorting difficult in recycling facilities. While black PE is recyclable, it’s often diverted to lower-grade applications.
- Food contact restrictions: Some black PE may not be suitable for direct food contact due to potential migration of additives unless specifically approved.
- Thermal limitations: PE has relatively low melting points (between 105°C and 135°C), limiting its use in high-temperature applications.
7. Black PE in sustainable manufacturing
As industries shift toward greener materials, black PE’s role is also evolving. Some manufacturers are now producing black PE with recycled content while maintaining performance. Biobased polyethylenes derived from sugarcane or other renewable resources are also being compounded with carbon black to create more sustainable black PE variants.
Additionally, alternative pigments and machine-readable colorants are being developed to make black PE easier to sort during recycling. These innovations could significantly improve black PE’s end-of-life circularity.
8. Conclusion
Black PE is more than just a pigmented plastic—it’s a high-performance, UV-resistant material that supports critical infrastructure, agriculture, and packaging across the globe. From underground pipelines to greenhouse roofs, black PE’s blend of versatility, affordability, and durability ensures it remains a go-to choice in modern manufacturing.
Understanding its composition, processing methods, strengths, and limitations helps users make informed decisions, whether they’re specifying a material for a water pipeline or choosing the right packaging film.
9. About EuroPlas
EuroPlas is one of the world’s leading manufacturers of plastic compounds and masterbatches, with 7 factories across Vietnam and Egypt and an annual capacity of 800,000 tons. We offer a full portfolio of solutions including filler masterbatch, color masterbatch, plastic additives, engineering plastic compounds, bioplastics, and biofillers.
Our black masterbatch solution which has many features:
- Create black color for end-products
- Great dispersion
- High color fastness and thermal resistance
- Improve end-products' properties, such as UV resistance
- Various color choices
.jpg)
Whether you’re in agriculture, infrastructure, or packaging, EuroPlas has the right material to meet your needs. To learn more, visit our Blog or Contact us for more information about the product.