In the past few years, the cast film extrusion process has grown in popularity and continues to expand. With enhanced efficiency and environmental standards, cast film is used by roughly 70-80% of the industry globally. This article explains what is cast film extrusion, describes the cast film extrusion process and shows the differences between cast film extrusion vs blown film extrusion.
Related:
- What is BOPP plastic film? BOPP film manufacturing process
- 3 layer blown film extrusion process
- Types of plastic extrusion and its manufacturing process
- Casting Film Process: oxidized gels, carbon spots and unmixed gels
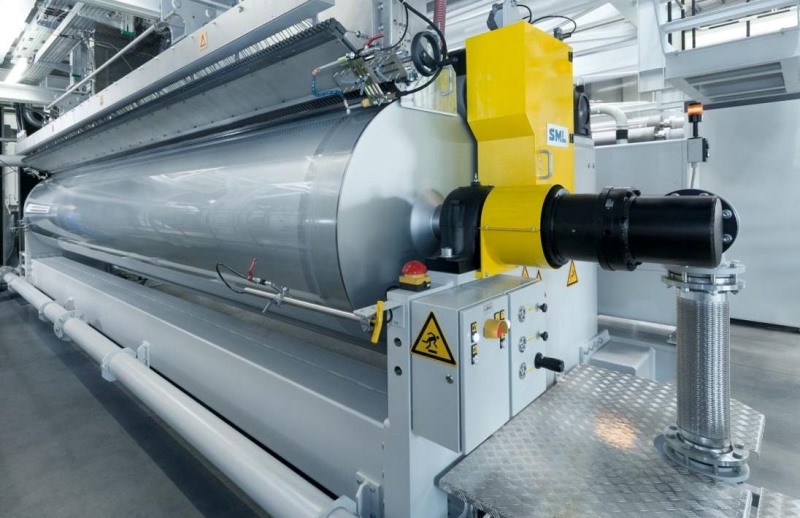
1. What is cast film extrusion
Cast film extrusion is the process of melting plastic resins and wounding them into rolls. The product of the cast film extrusion process is plastic films with a vast range of colors, finishes, and printing.
It is ideal for producing food packaging and technical, stretch, and bubble film (PE, PET, PP, PVB, PS...). Additionally, cast film extrusion provides easy integration with laminating, coating, embossing, and printing units.
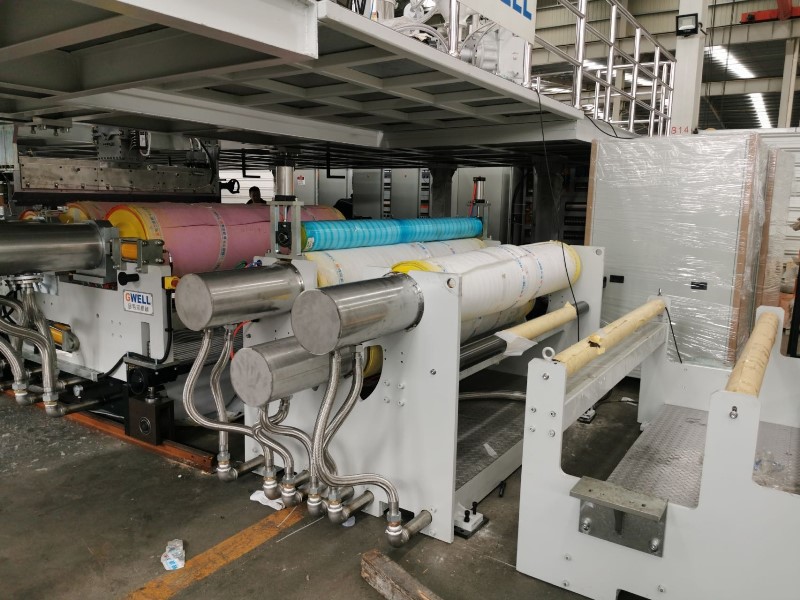
2. Cast film extrusion process
The cast film extrusion process requires a high-quality and high-consistency cast film extrusion line. Automatic and complex components allow the process to be more consistent and efficient than other traditional ways.
2.1. Component of a cast film extrusion line
Feeding System: Feeding systems regulate the amount of material fed into extruders by weight rather than volume. In many situations, the film is made from ingredients that are a combination of a base polymer and one or more secondary components.
Extruder: An extruder's primary functions are to melt plastic materials and mix the resulting molten polymer to obtain a homogeneous mixture. This is accomplished by moving the material with a spinning screw along a heated barrel.
Filtration System: The filtration system is used to prevent the downstream passage of melt impurities and gels generated during the process. Filters with metallic mesh are the most frequently used.
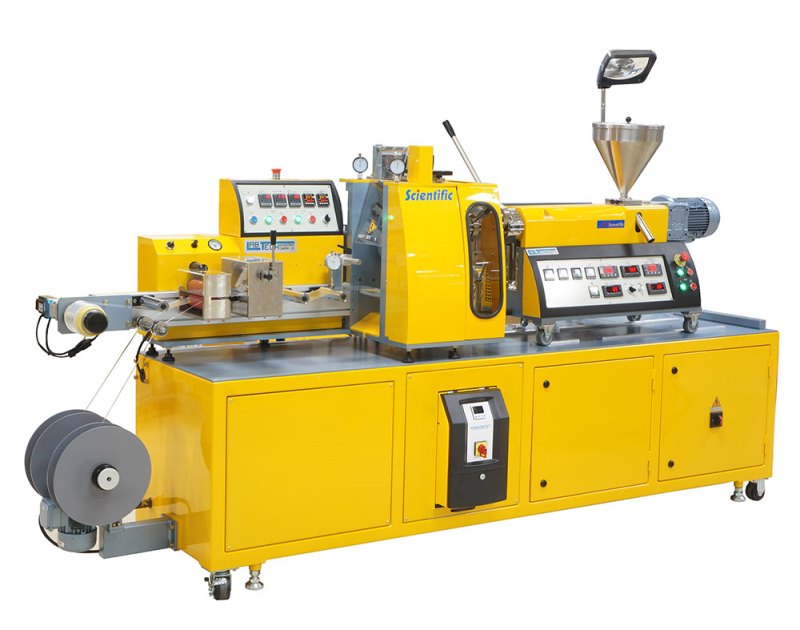
Flat Die System: Flat die system is the heart of a cast film coextrusion line. This system consists of the coextrusion feedblock, flat die, and melt transfer adapters that deliver various molten resins from the extruders to the feedblock input ports.
Cooling Unit: A primary roll, a secondary roll, a motorized roll, a vacuum box and an air knife are components of the cooling unit. The rolls are often chrome coated to improve surface polish and heat transfer during the film cooling process. Water that circulates inside the rolls is typically used as a cooling agent. The primary quenching roll cools one side of the film while the secondary roll cools the other.
Automatic Gauge Control System: The gauge control system, or APC, measures and controls film thickness. This system is made of a radiation emission device and a control console. The radiation unit moves over the machine, scanning the film in cycles. Meanwhile, the control system provides power to the thermal translators as needed, and the lip gap is controlled through the thermal expansion of the adjustment element.
Corona Treatment: A surface treatment is required to assist the adhesion of inks or coatings onto the film surface. Corona treatment is the most widely used procedure currently available. It increases the surface energy and thus the surface tension of the film.
Winder: Winders transform extruded film into rolls of material. The winding procedure must be consistent so that the film's qualities and dimensions are preserved when the rolls are unwound and transformed in other downstream operations.
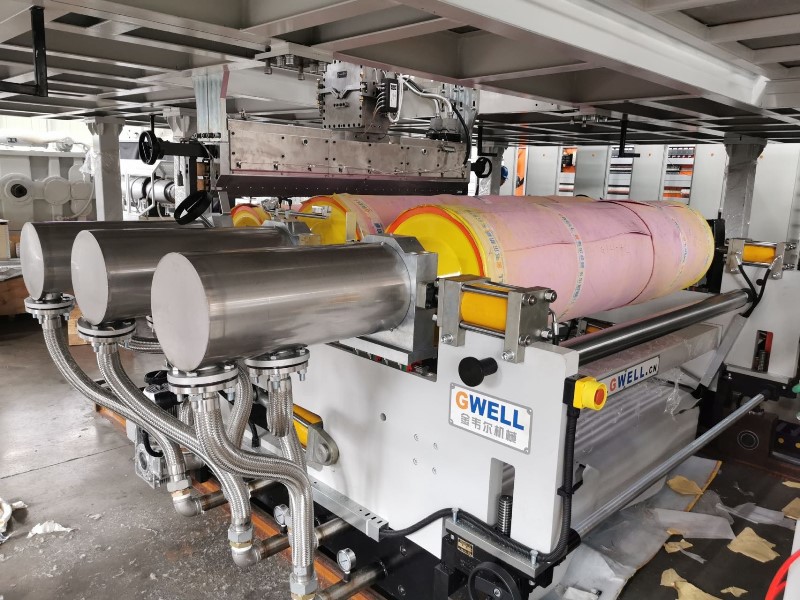
Computerized Control System: The main components of a cast film extrusion line described above do not operate manually but are integrated and governed by a computerized supervisory and control system. The main functions of this system are controlling the line's start-up, shutdown, and speed, maintaining a steady throughput, monitoring the weight of material supplied into the extruders and managing the speed of the extruders, etc.
2.2. Cast film extrusion process
Thanks to modern technology, the cast film extrusion process is done automatically. This process consists of 3 steps: Melting the thermoplastic materials, Flattening and solidifying, and Trimming and rolling.
In the cast film extrusion process, the molten materials are extruded through a slot die onto an internally cooled chill roll. Then, it goes through a set of rollers that determine the qualities of the cast film such as thickness. After this step, the cast film is trimmed and rolled.
Step 1: Melting the thermoplastic materials
The process starts with the feeding of plastic resins using a gravimetric feeding system to one or more extruders. The materials are subsequently melted and mixed into a consistent mixture by the extruders. The most commonly used materials for cast film extrusion are polyethylene (PE) and polypropylene (PP).
Step 2: Flattening and solidifying
Once molten by the extruders, the materials travel to a flat die to be flattened into a thin film. This film is drawn to the surface of a cold roller, where it is cooled and solidified by using an air knife or vacuum box.
The main two rolls subsequently cool both sides of the product. This step helps the fine film rapidly quench, which improves its mechanical features and clarity. The thickness of the film might range from less than 10 microns to 200 microns. The cast film can be monolayer or multilayer, with a maximum of 5 layers.
Step 3: Trimming and rolling
In the final stage, the film is then passed through a sequence of cold, polishing, and nip rolls to help form the desired thickness. It is then trimmed and wound into a drum for storage by a winder.
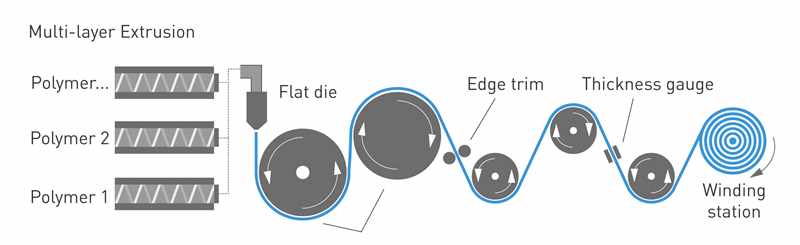
3. Cast film extrusion vs blown film extrusion - which one is better?
Business owners are increasingly shifting away from traditional blown film extrusion and choosing the cast film extrusion process instead. With improved efficiency and sustainability standards, cast film is used by around 70-80% of the industry globally. Here are the main differences between Cast film extrusion vs blown film extrusion.
- Direction and type of die: Blown film extrusion process extruded resins vertically with a circular die, creating a thick layer of film with bubbled shape. Cast films are made by melted thermoplastic horizontally through a flat die to create a fine sheet of film.
- Cooling speed: The cooling process of blown film extrusion is much slower because the bubble-shaped film is gradually cooled. While the instant cooling technology of cast film extrusion enables faster production line speeds.
- Clarity: Cast film tends to be clearer and shinier, whereas blow film gives less clarity due to crystallization that occurs during manufacturing.
- Resistance to stretch: Blown stretch film is very resistant to puncture while cast films are not as good as the former.
- Unwind noise: Cast film extrusion makes less noise unwinding than the other.
- Usage: Factories usually preferred blown film for wrapping sharp-edged products and heavy loads, and cast film for lighter products.
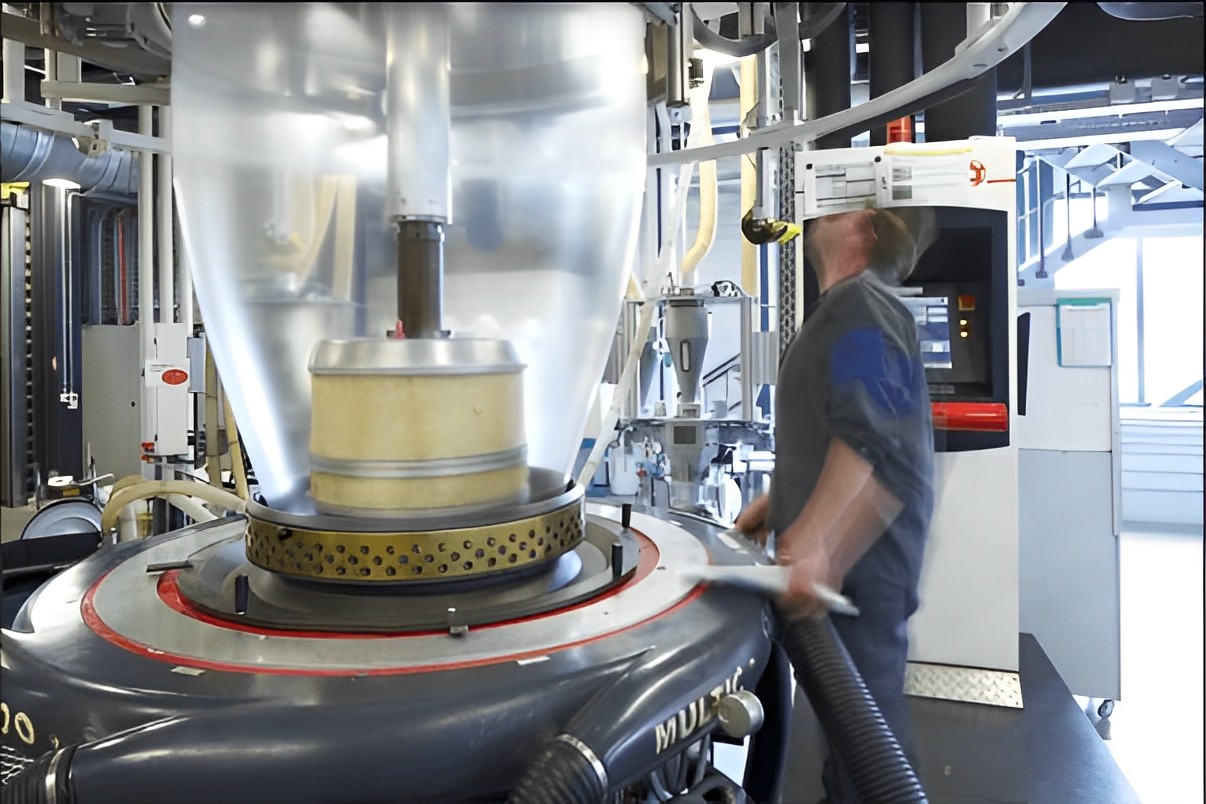
The cast film extrusion process is melting and turning plastic resins into film rolls. It is more proficient than blowing extrusion, with improved cooling and optimal control over the finished product's sizes and qualities. This is the reason why it is more and more popular among manufacturers. Hope this article has helped you understand more about this process and its advantages.
Whether you are looking for standard or customized products,
EuroPlas is a trusted supplier that can meet your needs.
Contact us directly to discuss your specific needs and requirements.