Color Masterbatch vs. Liquid Colorants: Which One Is Better?
Introduction
Selecting the optimal coloring method is a critical decision in the plastics industry, as it significantly influences production efficiency, cost-effectiveness, and final product quality. Among the various options available, color masterbatch and liquid colorants are two of the most commonly used solutions, each offering distinct advantages depending on the application.
Manufacturers must consider several factors, such as processing requirements, color consistency, cost, and environmental impact, before determining which method best suits their needs. While color masterbatch provides stability, ease of use, and precise color control, liquid colorants offer flexibility and fast color changes, making them ideal for specialized applications.
So, which option is better? In this article, we will explore the key differences between color masterbatch and liquid colorants, analyze their pros and cons, and help you decide which one aligns best with your production goals.
1. Overview of Both Coloring Methods
Coloring plastics plays a crucial role in manufacturing, allowing companies to achieve a diverse range of vibrant colors, finishes, and effects in their final products. Among the various coloring techniques available, color masterbatch and liquid colorants are the two most widely used solutions, each offering distinct advantages depending on the application, production process, and material compatibility.
1.1. Color Masterbatch: Reliable and Versatile
Color masterbatch is a solid additive in pellet form, consisting of highly concentrated pigments or dyes dispersed within a carrier resin. This method is particularly popular in injection molding, extrusion, and blow molding due to its ease of handling, precise color control, and excellent dispersion properties. Manufacturers favor color masterbatch for its long shelf life, minimal mess, and ability to enhance polymer performance by improving UV resistance, heat stability, and mechanical strength. Additionally, it is compatible with various plastic resins, making it a versatile choice for multiple industries.
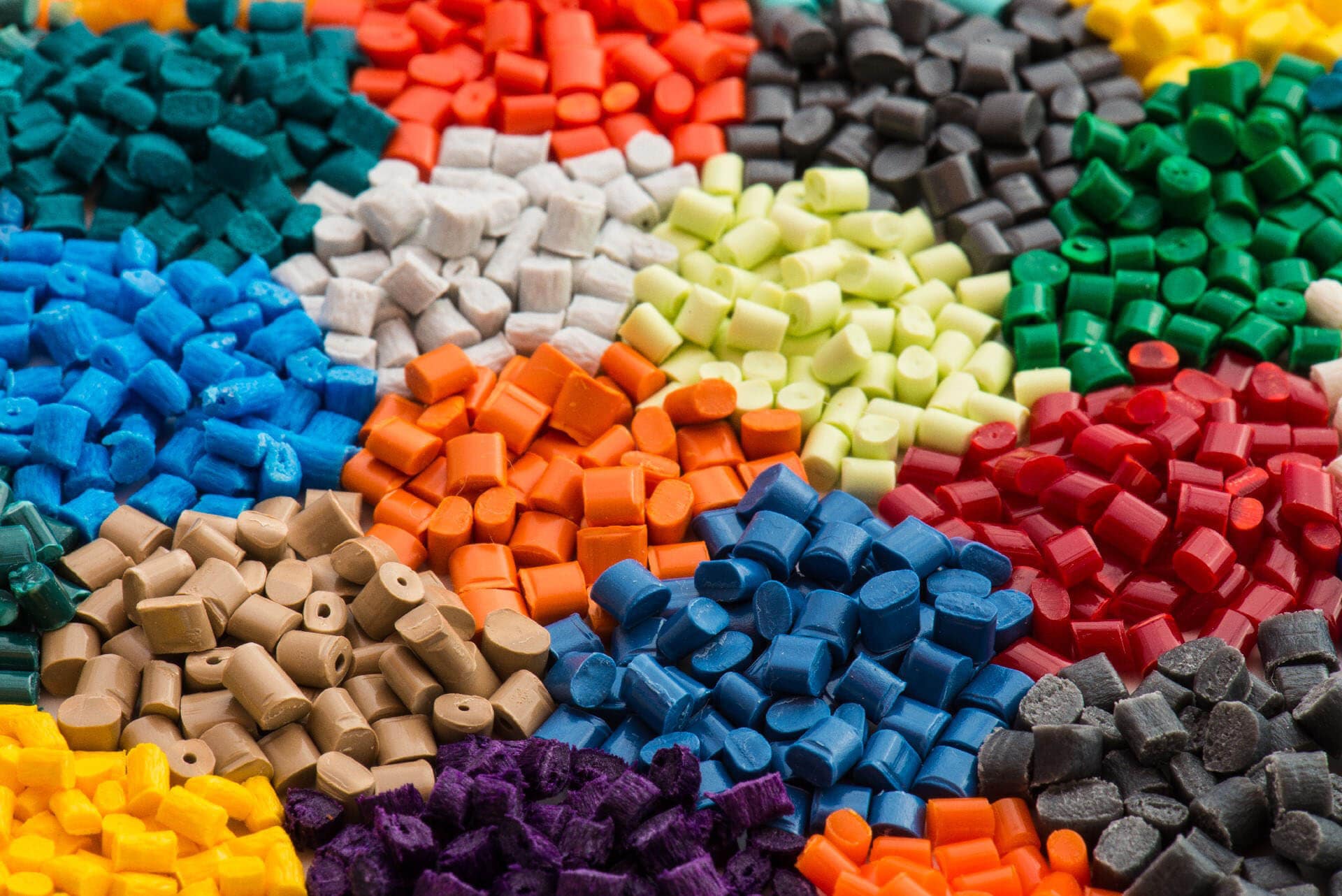
Color masterbatch is a solid additive in pellet form.
1.2. Liquid Colorants: Fast and Customizable
Liquid colorants, on the other hand, are highly concentrated liquid dyes or pigments mixed with a carrier liquid that allows for easy blending with raw plastic materials. They are commonly used in high-speed production processes where rapid color changes and precise color matching are essential. Their ability to provide uniform color distribution, lower let-down ratios, and reduced energy consumption makes them an attractive choice for industries requiring consistent, high-quality finishes. However, they require specialized storage conditions and careful handling to prevent spills, evaporation, or contamination.
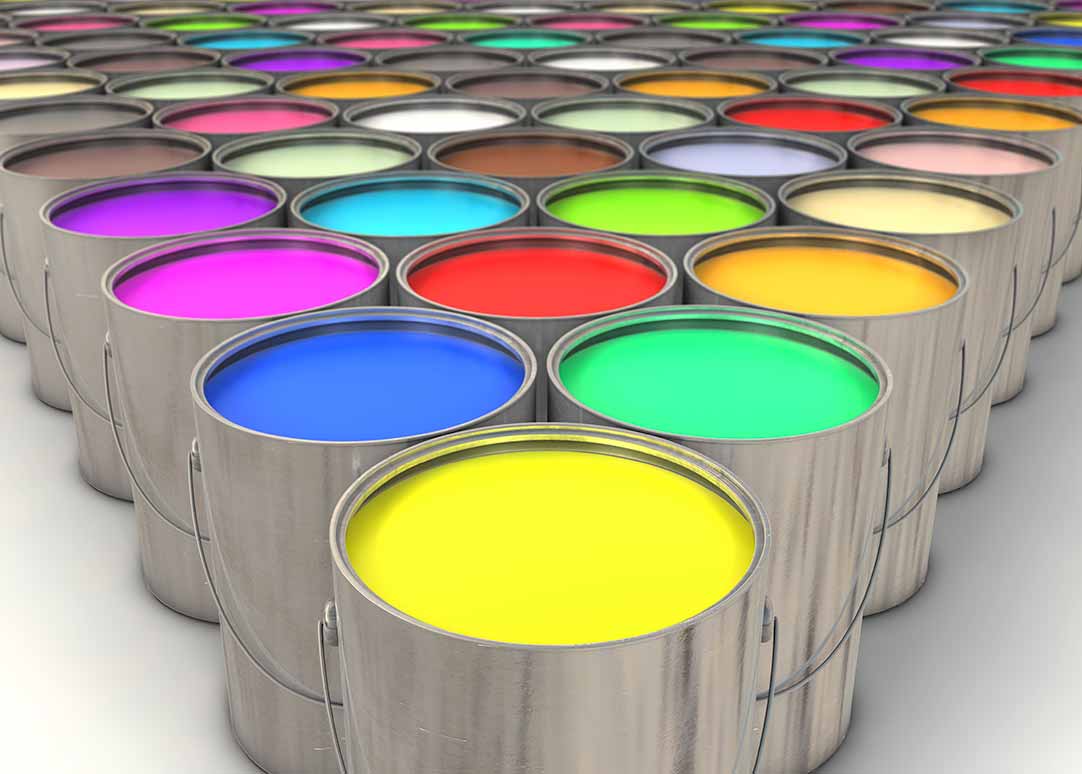
Liquid colorants are highly concentrated liquid dyes or pigments mixed with a carrier liquid.
1.3. Comparing Key Factors
Both color masterbatch and liquid colorants are designed to enhance the appearance and functionality of plastic products, but they differ in several key aspects:
Cost Efficiency: Color masterbatch typically has a lower upfront cost and is more economical for long production runs, whereas liquid colorants can be cost-effective for short runs and frequent color changes.
Processing Convenience: Masterbatch pellets are dust-free and easy to handle, making them ideal for automated manufacturing, while liquid colorants require careful metering and storage to prevent spills or evaporation.
Color Consistency & Precision: Liquid colorants excel in precise color matching and fast adjustments, but color masterbatch provides better batch-to-batch consistency and long-term stability.
Environmental Impact: Liquid colorants often require solvent-based carriers, which may pose environmental and regulatory concerns, whereas masterbatch is generally safer and more eco-friendly.
By understanding the strengths and limitations of each method, manufacturers can select the most efficient and cost-effective coloring solution tailored to their specific production needs and industry requirements.
2. Comparison of Color Masterbatch and Liquid Colorants
Factor |
Color Masterbatch |
Liquid Colorants |
Color Strength & Consistency |
Excellent dispersion, ensuring uniform color |
Requires precise mixing, may cause uneven distribution |
Processing Efficiency |
Easy to handle and store, no additional mixing required |
Requires special dosing equipment for precise application |
Cost-Effectiveness |
Cost-efficient for medium to large production runs |
Ideal for small batches but may increase costs for larger productions |
Compatibility |
Compatible with most resins and processing methods |
May require compatibility testing with certain resins |
Environmental Impact |
Minimal waste and lower risk of spills |
May cause spills or waste due to liquid handling |
Customization |
Available in a wide range of shades and properties |
Allows for on-the-fly color adjustments |
Each method has its strengths and limitations, making it important to consider production scale, color accuracy, and handling requirements before choosing the best option.
3. Which One Is Better?
Choosing between color masterbatch and liquid colorants depends on several key factors, including production scale, color accuracy, environmental impact, and storage requirements. Each method has its own advantages, making them suitable for different industrial applications.
3.1. High-Volume Production Efficiency
For manufacturers producing large quantities of plastic products, color masterbatch is the better choice due to its ease of handling, cost-effectiveness, and process stability. Since it is in pellet form, it integrates seamlessly with plastic resins, ensuring uniform dispersion and consistent color results across multiple production batches. Additionally, masterbatch does not require specialized metering equipment, making it ideal for automated manufacturing processes where precision and efficiency are essential.In contrast, liquid colorants require precise dosing systems to ensure accurate color ratios, which can increase operational complexity in large-scale production. Improper mixing may lead to color variations, affecting product consistency.
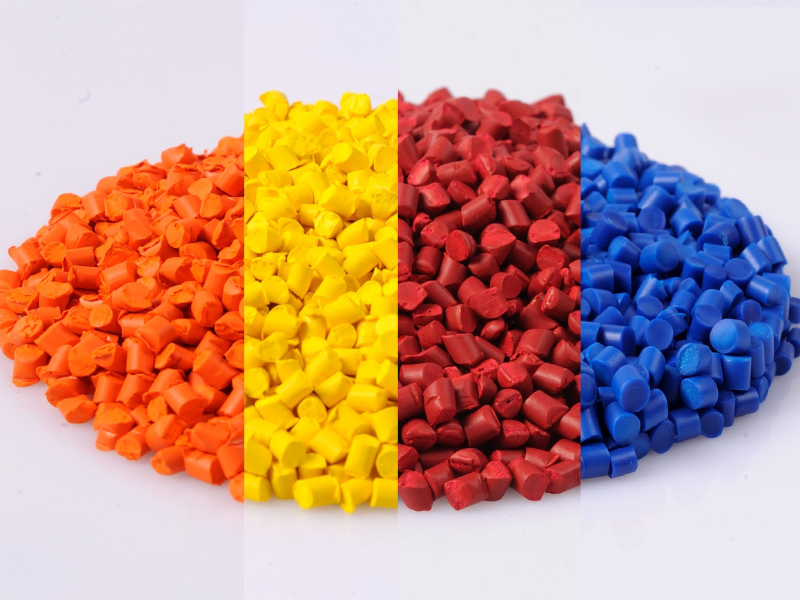
High-Volume Production Efficiency.
3.2. Precision and Customization in Color Matching
For applications where frequent color changes and precise shade adjustments are required, liquid colorants provide a more flexible solution. Since they are in liquid form, they allow for on-the-fly adjustments without the need for extensive recalibration. This makes them particularly useful for industries such as automotive, fashion, and specialty packaging, where customized color matching is a priority.
However, color masterbatch offers greater stability and batch-to-batch consistency, making it the preferred option for applications where color uniformity is more important than real-time customization.
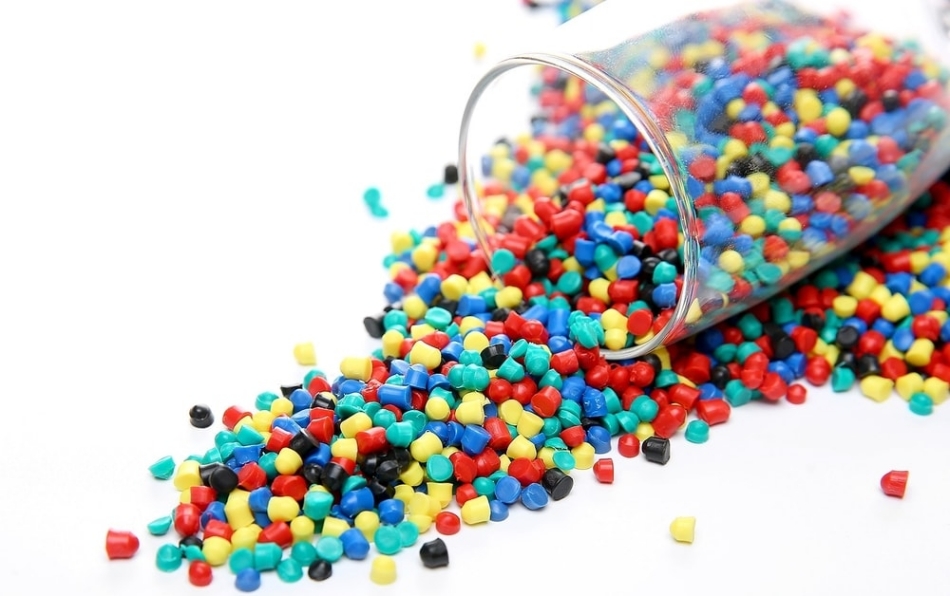
Precision and Customization in Color Matching.
3.3. Environmental and Safety Considerations
From an environmental perspective, color masterbatch is generally safer and cleaner to handle than liquid colorants. Since it is a solid additive, it minimizes the risks of spills, evaporation, and hazardous chemical exposure during processing. Additionally, masterbatch does not require solvent-based carriers, reducing the potential for volatile organic compound (VOC) emissions.
On the other hand, liquid colorants can pose handling challenges, as improper storage or spillage may lead to waste and contamination. Some liquid colorants also contain chemical solvents, which may require additional safety measures to comply with environmental regulations.
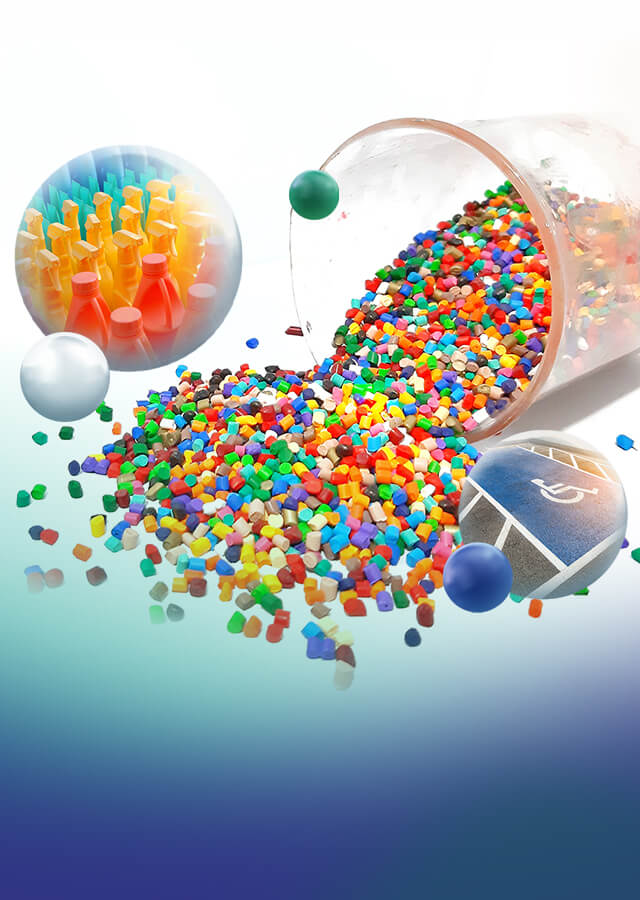
Environmental and Safety Considerations.
3.4. Storage and Shelf Life
Color masterbatch is more stable and easier to store compared to liquid colorants. Due to its pelletized form, it is resistant to separation or settling, ensuring consistent quality over time. This makes it suitable for long-term storage without compromising performance.
Conversely, liquid colorants may experience pigment settling or separation, requiring regular agitation or mixing before use. If not stored properly, they may lose their effectiveness, leading to inconsistent coloration.
Final Verdict: Which One Should You Choose?
For most plastic processing industries, color masterbatch is the preferred choice due to its convenience, color consistency, ease of handling, and cost efficiency. It is particularly well-suited for large-scale production, automated manufacturing, and applications requiring high color stability.
However, liquid colorants remain a strong alternative for industries that need high precision, frequent color changes, and immediate customization. If your production involves small batches, rapid prototyping, or specialized color requirements, liquid colorants may offer greater flexibility despite their handling and storage challenges.
Ultimately, the choice between color masterbatch vs. liquid colorants depends on your specific manufacturing needs, operational priorities, and regulatory requirements. Understanding the advantages and trade-offs of each method will help you select the best solution for your production process.
4. Conclusion
The choice between color masterbatch and liquid colorants depends on several key factors, including production scale, color precision, environmental impact, and storage requirements. Here's a breakdown of when to choose each option:
For High-Volume Production:
Color masterbatch is the better choice due to its ease of handling, consistent color dispersion, and cost-effectiveness in large-scale manufacturing.
It reduces production downtime and eliminates the need for specialized dosing equipment.
For Precise Color Adjustments:
Liquid colorants provide greater flexibility and customization, making them ideal for applications that require frequent color changes or real-time adjustments.
They allow for fine-tuning color shades with high accuracy, which is useful in small-batch or specialized production.
For Environmental Considerations:
Color masterbatch is generally safer and cleaner to handle, reducing the risk of spills, waste, and exposure to volatile chemicals.
Since it is a solid additive, it does not require additional solvents or stabilizers that may impact worker safety and environmental compliance.
For Storage and Shelf Life:
Color masterbatch has a longer shelf life and is easier to store, as it remains stable over time and does not separate like liquid colorants.
Liquid colorants may require special storage conditions, as pigments can settle or degrade if not properly maintained.
5. About EuroPlas’ Color Masterbatch
EuroPlas is a leading provider of high-quality color masterbatch solutions, offering a wide range of customized colors and advanced formulations to meet various industry demands. With a strong commitment to innovation and quality, EuroPlas’ color masterbatch ensures excellent dispersion, delivering uniform and vibrant colors for plastic products. Designed for durability, our formulations maintain stable color performance under different processing conditions while optimizing cost efficiency for manufacturers. Compatible with various resins and plastic manufacturing processes, EuroPlas’ color masterbatch is the ideal choice for businesses seeking reliable and high-performance coloring solutions. Looking for the best color masterbatch for your production needs? Contact EuroPlas today to explore our premium range of color additives and enhance your plastic manufacturing process!