Injection molding is a technique for transforming liquid plastic into solid items or sections of objects. It is one of the most frequent manufacturing procedures. There are many common plastics for injection molding but they are not the same. Each material has particular properties that make it suitable for various goods.
It might be intimidating if you don't know your way around and pick the wrong material to produce your items. The following article will help you learn more about popular types of plastics for injection molding so you can decide what is ideal for your needs!
Related: Types of plastic extrusion and its manufacturing process
1. What is injection molding?
Injection molding is a shaping technique that uses molds. Materials such as synthetic resins are heated and melted before being poured into the mold and chilled to make the desired shape. 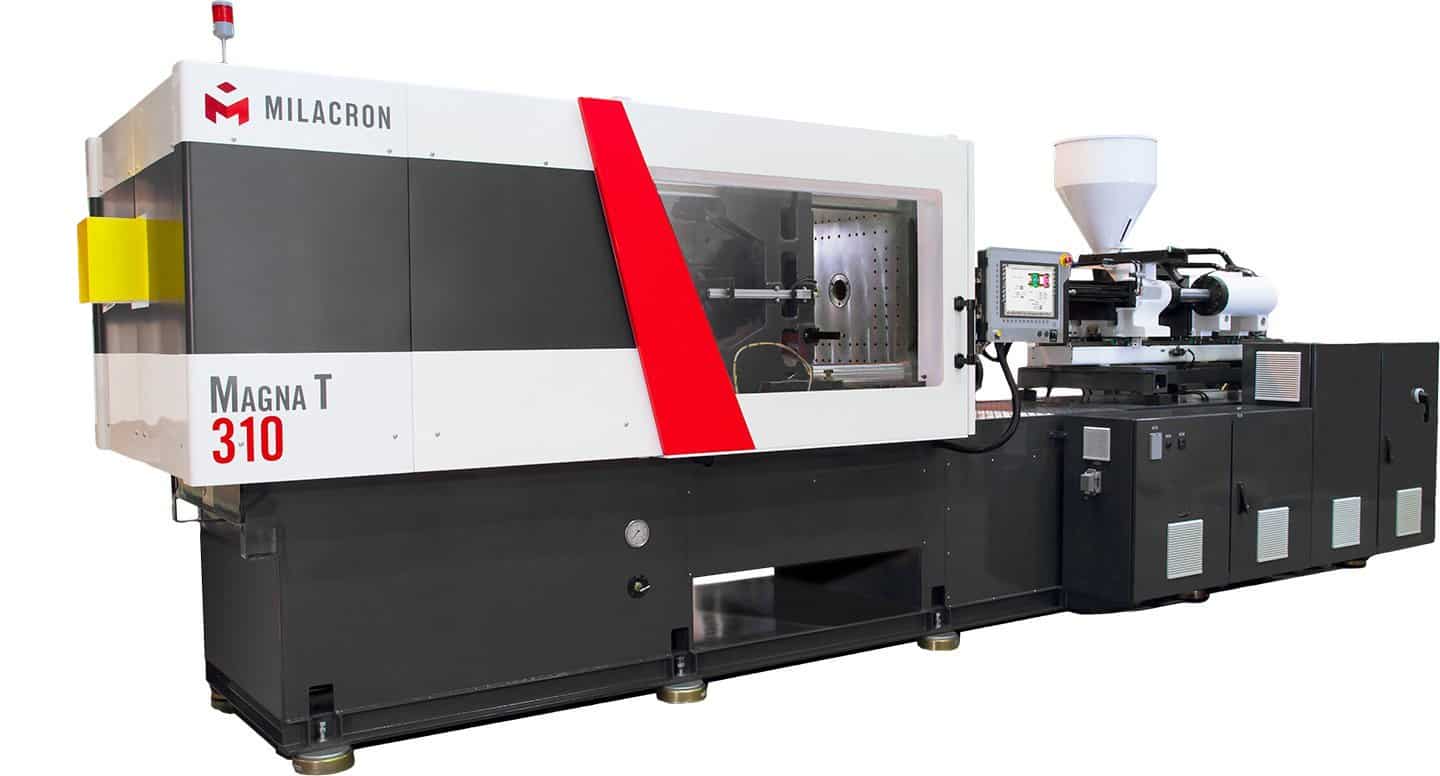
This procedure is known as injection molding because it is similar to injecting fluids using a syringe. The procedure is as follows: Materials are melted and placed into a mold, where they solidify before being removed and completed.
Injection molding machines are classified into three types: motorized machines powered by servo motors, hydraulic machines powered by hydraulic motors, and hybrid machines powered by a servo motor plus a hydraulic motor.
CNC (Computer Numerical Control) has recently been widely used in injection molding machines, boosting the popularity of models that permit high-speed injection under programmed control.
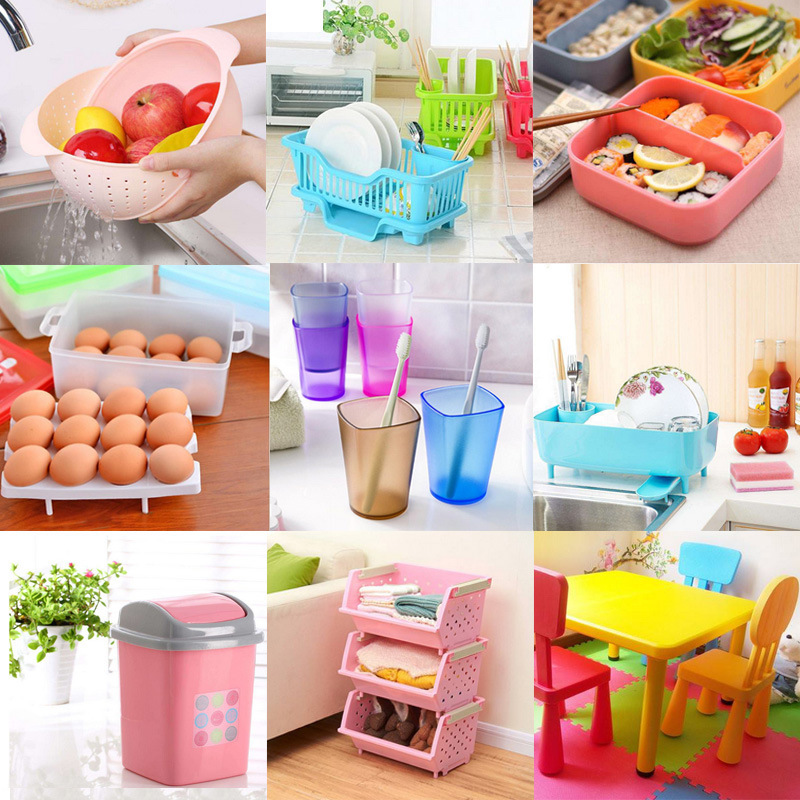
Some products made from injection molding
Injection molding procedure
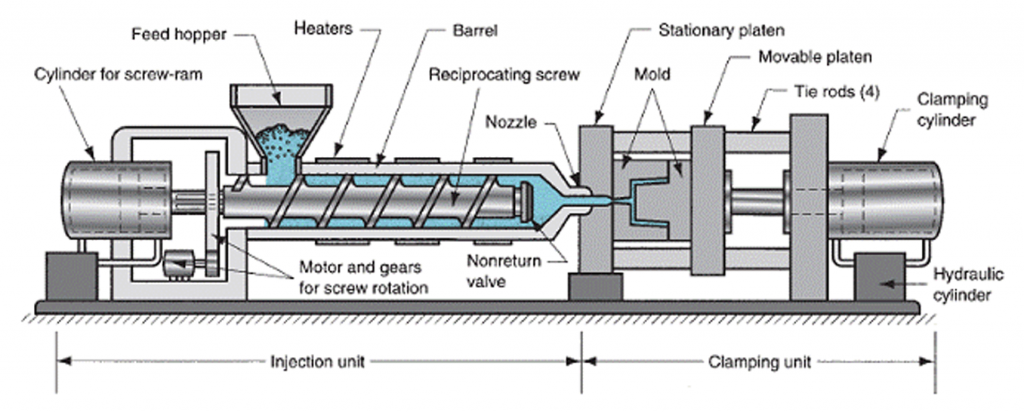
Step 1: An injection molding machine's construction may be characterized as an injection unit that puts melted materials into the mold and a clamping unit that operates the mold.
Step 2: The material is then driven through the injection unit's nozzle before being supplied into the mold cavity via a channel in the mold known as a sprue and branching runners.
Step 3: After the material has cooled and hardened, the mold is opened, and the molded object is ejected. To complete the molded item, the sprue and runner are removed.
Because there is generally more than one cavity within the mold, allowing for the manufacture of more than one item at a time, the melted material must be evenly supplied throughout the mold.
As a result, the mold form should be built in such a way that this is ensured, such as by having runners of the same proportions.
2. Common plastics for injection molding
When you look for plastic injection molding materials, you will see a list of hundreds, perhaps even thousands of plastic stocks. It really matters when you choose injection molding plastic types as they can affect the product that you’re making.
And with so many options, it can take a lot of work to narrow down just what you need. We have done the hard work to list 15 common plastics for injection molding that you should know about.
Related: How to effectively apply colorants in your plastic injection molding?
2.1. Acrylic (PMMA)
Acrylic is a durable, transparent thermoplastic lighter and more shatter-resistant than glass. Furthermore, this material has excellent optical clarity, enabling a great amount of light to pass through. Unlike certain polymers, acrylic can withstand contact with water.
This injection-molded material is also capable of maintaining tight tolerances. PMMA is unable to tolerate chemicals or absorb odors. Grease and oils may also easily mark it. Despite its excellent tensile strength, acrylic is susceptible to stress cracking when exposed to high loads.
Acrylic is used in various applications, including windows, greenhouses, solar panels, shower enclosures, and other transparent elements for outdoor, architectural, and lighting purposes.
2.2. Acrylonitrile butadiene styrene (ABS)
ABS is an engineering-grade plastic having a low melting point that allows it to be easily molded. This opaque polymer facilitates the use of colorants, as well as various textures and surface treatments.
ABS is widely renowned for its strength and impact resistance. However, it has low resilience to sunlight, water, and weather. When compared to acrylic, injection-molded ABS is not suitable for outdoor applications.
ABS plastic injection molding is used to make keyboards, protective headgear, wall plates for electrical outlets, dashboards, wheel coverings, and other vehicle components.
2.3. Nylon (polyamide, PA)
Nylon is a synthetic polyamide with great toughness and heat resistance, as well as strong abrasion resistance, fatigue resistance, and noise-dampening qualities.
Nylon does not withstand strong acids and bases, as well as other polymers. It falls short of polypropylene and polycarbonate in strength and impact resistance.
Nylon is commonly used in strong mechanical components such as bearings, bushings, gears, and slides. It is also suitable for dynamic components, threaded inserts, casings, snap-fit closures, jigs, and fixtures.
2.4. Polycarbonate (PC)
Polycarbonate is a lightweight, robust, and naturally transparent material. PC's physical properties stay consistent across a wider temperature range.
Polycarbonate's predictable and uniform shrinkage allows for fine dimensional control and tighter tolerances. While not scratch-resistant, polycarbonate is significantly more robust and tougher than glass.
Although it retains its color and strength when pigmented, this material has remarkable optical properties that aid in light transmission.
Polycarbonate plastic is used to make machinery guards, transparent and tinted windows, diffusers and light pipes for LEDs, and clear tubing. It may also be used to create translucent molds for silicone and urethane casting.
2.5. Polyethylene (PE)
Polyethylene is the most widely used plastic worldwide and the commercial polymer that may be chosen based on density. High-density polyethylene and low-density polyethylene are chemically resistant, but their hardness, flexibility, melting temperature, and optical transparency differ.
Related: After mixed with masterbatch, how was plastic processed with injection molding?
These plastic materials may not be appropriate for various processing applications because they cannot endure high service temperatures. Injection-molded polyethylene is often used in household goods, toys, food containers, and automobile parts.
2.6. Polyoxymethylene (POM)
Polyoxymethylene, often known as acetal, is an engineering plastic. It has a low coefficient of friction and combines outstanding stiffness with thermal stability. POM plastics have a naturally opaque and white look. Acetal plastics are classified into homopolymers with better hardness and tensile strength and POM copolymers.
Injection-molded POM is utilized in bearings, gears, conveyor belts, and pulley wheels due to its low coefficient of friction. Fasteners, eyeglass frames, knife and handgun parts, lock systems, and high-performance engineering components are among the other uses.
2.7. Polypropylene (PP)
Polypropylene is the world's second most common plastic. It has a high melting point, a high chemical resistance. It keeps its shape after torsion or bending, and does not degrade when exposed to dampness or water. PP, often known as injection molded polypro, is a recyclable material.
Despite its advantages, polypropylene is very flammable and UV-sensitive. This injection-molded plastic degrades at temperatures over 100° C, producing hazardous aromatic hydrocarbons. Polypropylene plastic is very difficult to paint and bind.
Polypropylene is used in a variety of products, including toys, storage containers, sporting goods, packaging, appliances, and power tool bodies.
2.8. Polystyrene (PS)
Polystyrene plastics are light and affordable and resistant to moisture and bacterial development. The two most common types are general-purpose polystyrene and high-impact polystyrene.
Furthermore, these common polymers are resistant to gamma radiation and have a high chemical resistance to dilute acids and bases, which are both used to sterilize medical equipment.
Polystyrene is used in medical, optical, electrical, and electronic applications. Because of its improved impact strength, HIPS is widely used with machines and appliances. Injection-molded GPPS is used to make plastic trays, cases, and toys. Both compounds, however, are flammable and susceptible to UV degradation.
2.9. Thermoplastic elastomer (TPE)
TPE is a rubber and plastic composite material. TPE (thermoplastic rubber) may be stretched to intermediate elongations before snapping back into place when the force is removed.
TPE is less expensive to mold than liquid silicone rubber and easier to work with. TPE is susceptible to creep, which is the tendency of a solid material to deform permanently under sustained load.
TPEs poured into molds are used to produce footwear, medical equipment, car parts, and pet products. In autos, the usage of shock dust boots and weather seals. Medical equipment includes ventilation masks, catheters, valves, and breathing tubes.
2.10. Thermoplastic polyurethane (TPU)
TPU is a kind of TPE frequently referred to separately due to its popularity. Because of its greater durometer, it possesses the suppleness of rubber yet may be used as a substitute for hard rubber.
TPU is more resistant to severe temperatures and chemicals than TPE. TPUs, on the other hand, maybe excessively hard for some injection molded items.
TPUs that have been injection molded are utilized in footwear, gaskets, caster wheels, and athletic items. Cases or enclosures for electronics and medical devices are further examples of applications. TPUs are occasionally used in medical applications instead of polyvinyl chloride, a material that can cause skin irritation.
2.11. Low-density polyethylene (LDPE)
LDPE (low-density polyethylene) is a lightweight, soft plastic substance. Low-temperature flexibility, toughness, and corrosion resistance are all characteristics of LDPE.
It is not suitable for applications requiring rigidity, high-temperature resistance, or structural strength. It is frequently used in orthotics and prosthetics. LDPE is resistant to chemicals and impacts and is simple to produce and mold.
LDPE is used to make a variety of containers, including dispensing and squeeze bottles, tubing, computer component plastic parts, molded laboratory equipment, and various caps and closures.
2.12. High-density polyethylene (HDPE)
High-density polyethylene (HDPE) is a petroleum-based thermoplastic polymer. It is perfect plastic pellets for injection molding meant to be utilized in injection molding applications that need high impact, high-stress fracture resistance, and extreme durability.
HDPE is ideal for laundry, shampoo, conditioner, home cleaning goods, motor oil, antifreeze, and recycling bins because of its chemical resistance.
2.13. High-impact polystyrene (HIPS)
HIPS (High impact polystyrene), is a low-temperature amorphous thermoplastic polymer. HIPS is a versatile, low-cost polymer made from strong polystyrene resins.
It is frequently specified for low-strength structural applications that need impact resistance, machinability, and cheap cost. It has great dimensional stability and is simple to manufacture.
HIPS is frequently used for point-of-purchase displays and indoor signage where the simplicity of production is critical. It's also used to make yogurt containers, plastic cutlery, salad bowls, refrigerator liner, medical industry trays, and electrical insulation.
2.14. Thermoplastic rubber (TPR)
TPR is a form of injection molding resin that is a copolymer substance or a physical mixture of components such as plastic and rubber.
TPR materials have both rubber and plastic physical qualities, as well as thermoplastic and elastomeric properties. Thermoplastic rubber has great fatigue resistance, chemical resistance, impact resistance, and high recyclability.
TPR compounds are commonly used in footwear, gaskets, cable jacketing, toys, automotive applications, soft touch over-molding, and general-purpose molded items.
2.15. Polyether Ether Ketone (PEEK)
Polyether ether ketone plastic is a highly sought-after engineering material due to its excellent combination of strength, resistance, and workability. PEEK plastic is very resistant to heat, as well as wear, chemicals, fatigue, and creep. It has a high strength-to-weight profile that rivals metals like aluminum and will not decay in chemically or physically demanding settings like metals.
In addition, PEEK possesses unique features such as 100% biocompatibility, UV resistance, pure radiolucency, gamma-ray resistance, and low/no toxicity in all forms.
Because of these qualities, PEEK plastic may be used in various technical applications, including automobile engine components, medical implants, bearings, chemical equipment, and even radioactive applications.
2.16. Engineered Thermoplastic Polyurethane (ETPU)
ETPUs, commonly known as stiff thermoplastic polyurethanes, are amorphous polymers created by reacting isocyanate with glycol. These products combine amorphous resin toughness and dimensional stability with crystalline material chemical resistance.
ETPUs are distinguished by their excellent clarity, strong impact, high rigidity, superior abrasion, and chemical resistance. ETPUs are often produced by injection molding due to their extremely low melt viscosity.
Fuel bowls, IV connections, water valves, ball valves, underground electrical box lids, oil and gas sucker rods, wheelchair components, and high-strength nuts and bolts are examples of typical uses.
3. Injection-molded plastic manufacturers
As one of the leading injection molded plastic manufacturers, EuP has been producing plastic pellets for over 15 years and has been producing high-quality plastic pellets with excellent mechanical properties and durability.
Our Plastic engineering compounds are widely used to create injection molded parts, food containers, packaging, and other applications.
We have a high level of experience in the development and production of plastic materials for injection molding, as well as in the use of plastics for technical applications such as extrusion and blow molding.
Our expertise lies in our ability to develop new materials, which we then market under our brand name or through third parties.
With this post, we hope to have supplied you with valuable information to help you understand more about common plastics for injection molding. Please contact EuP to learn more about how we can help you design your next injection molded item.