Polyphenylene Sulfide (PPS) is one of the most advanced engineering plastics. PPS is widely used in various industries. With outstanding properties such as high heat resistance, excellent mechanical strength, and chemical resistance, PPS has played a significant role in the development of modern technology. This article will help you better understand the definition, properties, and diverse applications of this special type of plastic.
1. What is PPS plastic?
Polyphenylene Sulfide (PPS) is a high-performance organic polymer consisting of rings linked by sulfurs. It is one of the special engineering plastics with excellent heat resistance and superior overall mechanical, thermal, electrical, and chemical properties. In its pure form, PPS is opaque white to light brown and has a relatively simple molecular structure, with the main chain alternating between benzene rings and sulfur atoms.
In the plastics industry, PPS is considered one of the most important materials due to its excellent high-temperature resistance and chemical stability. Compared to other engineering plastics such as polytetrafluoroethylene and nylon, PPS has many outstanding advantages such as low water absorption (about 0.02%), low shrinkage (about 0.3%), and good flame resistance.

1.1. Technical Properties
PPS has the following notable technical properties:
Density: 1.34 g/cm³ (according to ISO 1183), PPS is lighter than many other engineering plastics.
Low shrinkage: About 1.9%, ensuring that PPS products have high precision, minimizing dimensional differences compared to the original mold.
Low water absorption: 1.4% is an outstanding advantage of PPS. Thanks to this property, PPS can maintain stable dimensions in humid environments, limiting deformation and shrinkage. This helps minimize risks during processing and eliminates the need for pre-drying before production.
Excellent mechanical properties: With indicators such as bending strength, impact strength, tensile yield strength, and flexural modulus all at high levels. Thus, PPS is a material with outstanding mechanical properties, capable of withstanding large loads and strong external forces.
Flow length under standard conditions: Reaches 0.020%, allowing the plastic to flow evenly and fully into the mold during the injection molding process. This helps ensure product uniformity and minimizes defects such as pores, scratches, or dents.
1.2. PPS Production Process
The PPS production process is a complex process, requiring specialized technology and equipment. The following is a detail of the main production methods:
Injection Molding:
- Barrel temperature: 280-330°C for pure PPS and 300-350°C for 40% GF PPS
- Mold temperature: 120-180°C
- Injection pressure: 50-130 MPa
Extrusion:
- Feed section temperature: Below 200°C
- Transition section temperature: 320-340°C
- Barrel temperature: 300-340°C
- Die temperature: 300-320°C
Compression Molding:
- Preheating temperature: 360°C (15 minutes) for pure PPS plastic
- Molding pressure: 10-30 MPa
- Cooling to 150°C to remove from the mold
Coating:
- Heat treatment at a temperature above 300°C
- Hold at temperature for 30 minutes
2. Outstanding Properties of PPS Plastic
PPS plastic possesses exceptional properties, making it an ideal choice for numerous industrial applications.
2.1. Excellent Heat Resistance
PPS plastic exhibits outstanding heat resistance. It can operate continuously at high temperatures of 200-240°C without deformation or loss of performance. Even when exposed to higher temperatures for short periods, PPS maintains its stability and does not decompose. This property makes PPS an ideal choice for applications in harsh thermal environments, such as the automotive, electronics, and aerospace industries.
See more: Top high heat plastic materials for engineering applications
2.2. Mechanical Properties
PPS plastic possesses excellent mechanical properties, including high strength, stiffness, and toughness. When processed, PPS can double its tensile strength and flexural modulus, resulting in end products with superior load-bearing and impact resistance. Additionally, PPS has excellent fatigue resistance and can withstand repeated loads, ensuring the long-term durability of the product.
2.3. Electrical Insulation
PPS plastic is an excellent electrical insulator, capable of operating stably in a wide voltage range from -94V to 260V. This property makes PPS widely used in electrical and electronic devices where high insulation is required for safety and performance. Moreover, PPS is flame-resistant and self-extinguishing, minimizing the risk of fire.
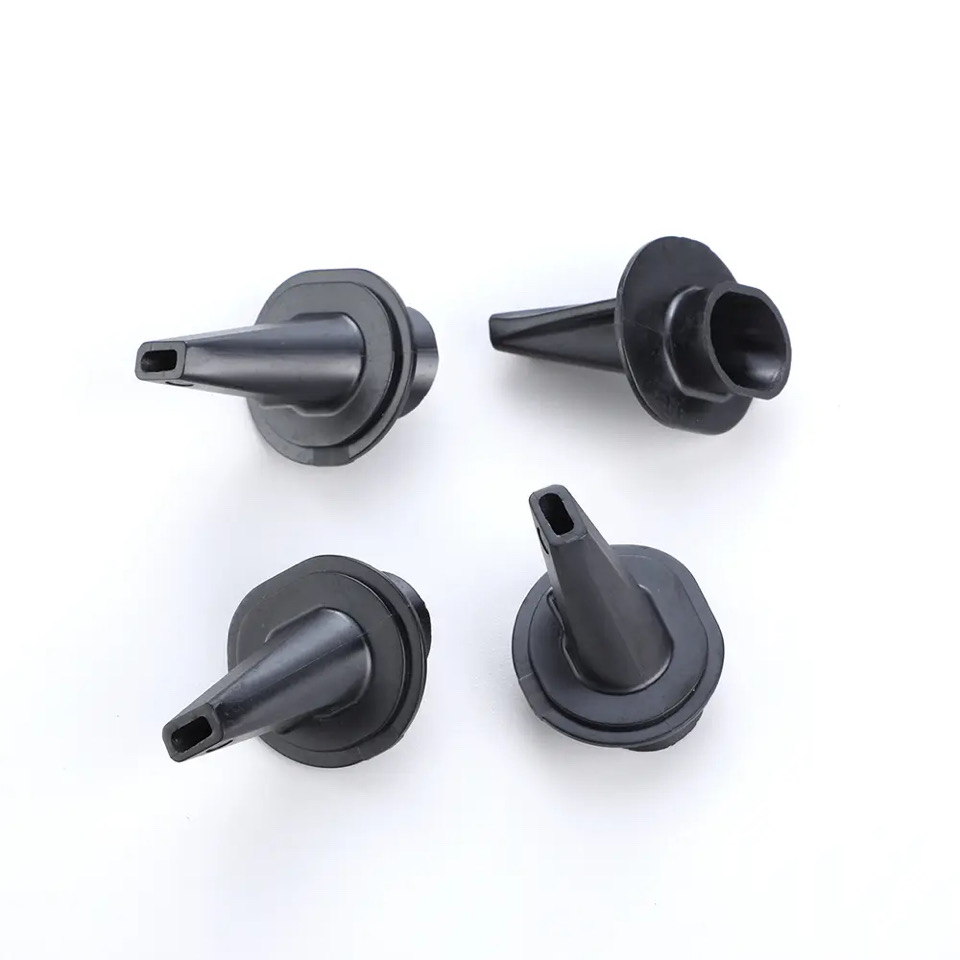
2.4. Chemical Stability
PPS plastic has excellent chemical resistance, being inert to most acids, bases, organic solvents, and other chemicals. This ensures the long-term durability and stability of products in harsh chemical environments.
2.5. Wear Resistance
PPS plastic has excellent wear resistance, providing products made from PPS with a longer lifespan and reduced maintenance costs. This property is particularly important for products that are subjected to frequent friction and abrasion, such as mechanical components and industrial equipment.
In general, PPS plastic is a high-end technical material with many outstanding advantages such as good heat resistance, high mechanical properties, electrical insulation, chemical stability and abrasion resistance. Thanks to these properties, PPS has been widely applied in many industries, from automobiles, electronics to chemicals.
3. Diverse Applications of PPS plastic in Various Industries
PPS plastic, with its unique combination of high performance properties such as heat resistance, chemical resistance, and mechanical strength, finds extensive applications in various industries.
3.1. Automotive Industry
PPS plays a crucial role in the automotive industry. Its excellent heat and chemical resistance make it suitable for manufacturing engine components. PPS is used to produce parts that are in direct contact with high-temperature fluids and corrosive substances, ensuring the durability and reliability of the engine. Additionally, its electrical properties make it ideal for electrical components in vehicles, contributing to overall safety and performance.
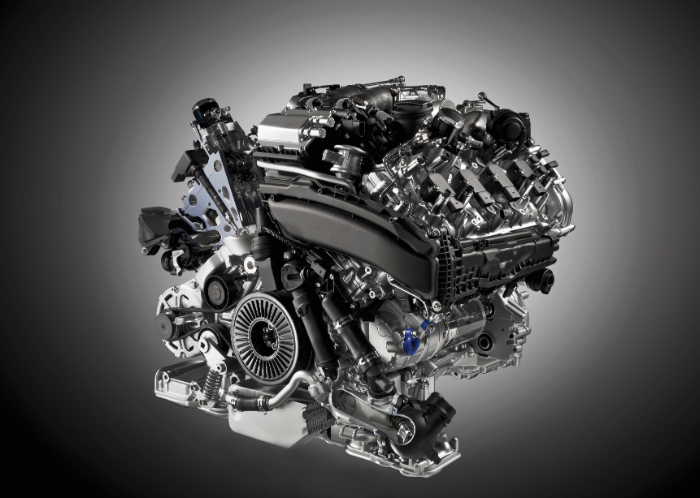
3.2. Electronics Industry
PPS is also widely used in the electronics industry. Its excellent electrical insulation properties make it suitable for producing electronic components and insulating materials. PPS is used in printed circuit boards, connectors, and housings for electronic devices. Its dimensional stability and resistance to moisture and chemicals ensure the long-term reliability of these components.

3.3. Aerospace Industry
PPS is used in the aerospace industry for manufacturing structural components such as interior window frames, storage compartments, and control panels. Its high strength-to-weight ratio, heat resistance, and chemical resistance make it an ideal choice for aerospace applications. PPS contributes to reducing the overall weight of aircraft, improving fuel efficiency, and ensuring passenger safety.

3.4. Food Processing Industry
PPS plastic is also used in the food processing industry. Its inertness to chemicals and ability to withstand high temperatures make it suitable for manufacturing food processing equipment. PPS is used to produce trays, molds, and other components that come into contact with food. Its non-toxic properties ensure food safety and compliance with strict industry regulations.
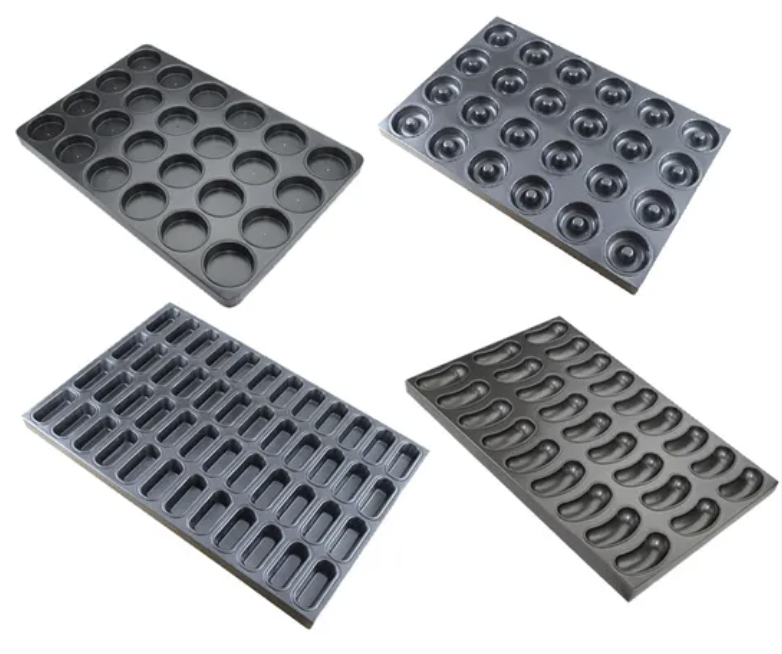
3.5. Chemical Industry
PPS plastic plays a crucial role in the chemical industry. Its exceptional chemical resistance makes it an ideal material for lining chemical tanks and producing chemical equipment. PPS provides excellent corrosion resistance, protecting equipment from the corrosive effects of chemicals and ensuring the safety of operators and the environment.
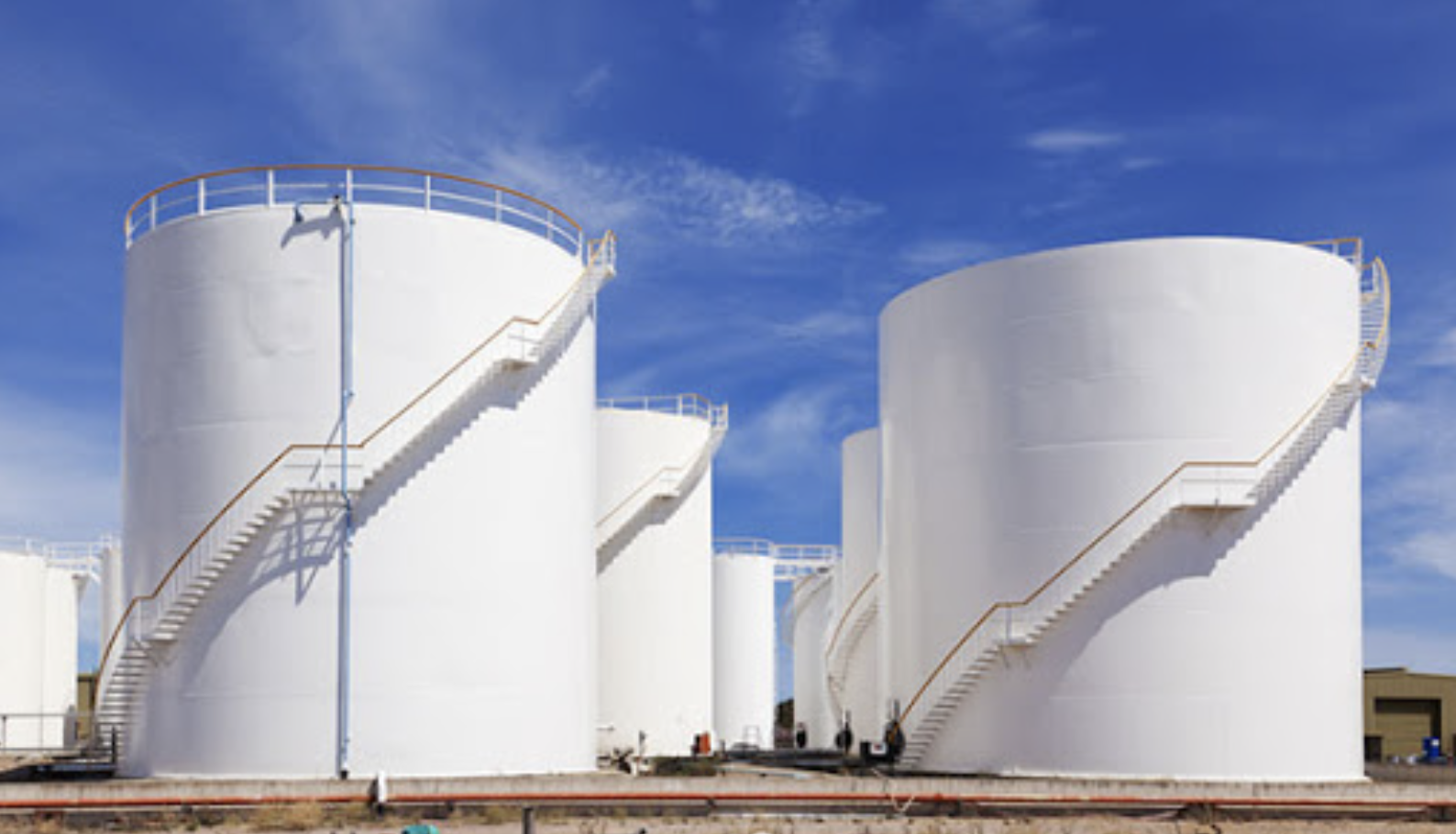
4. Conclusion
PPS plastic is a high-performance engineering plastic with a wide range of applications. Its outstanding properties, including heat resistance, chemical resistance, and mechanical strength, make it a valuable material in various industries. The continuous development of PPS production technologies and its increasing popularity have made it a vital material in modern manufacturing. With its excellent properties, PPS is poised for even greater adoption in industries that require high-performance, heat-resistant materials.
5. About EuroPlas
EuroPlas, a leading filler masterbatch manufacturer in Vietnam, is proud to offer high-quality PA compound solutions tailored to meet the diverse needs of our customers. With a dedicated team of experts and advanced manufacturing facilities, EuroPlas is committed to partnering with you from consulting and design to production, helping you create superior plastic products. To stay competitive in the market, contact our experts for personalized advice and solutions. If you are seeking a high-quality PA supplier, please contact EuroPlas's expert consultants for detailed advice and tailored solutions.