Carbon fiber and fiberglass are considered two versatile materials widely used in heavy industries. Products made from carbon fiber and glass have stable hardness, lightweight and durable physical structure. In particular, fiberglass and carbon fiber both have their own advantages and are fully utilized by manufacturers. In this article, EuroPlas will send customers detailed information about the characteristics, differences and applications of carbon fiber and fiberglass in life. Refer now!
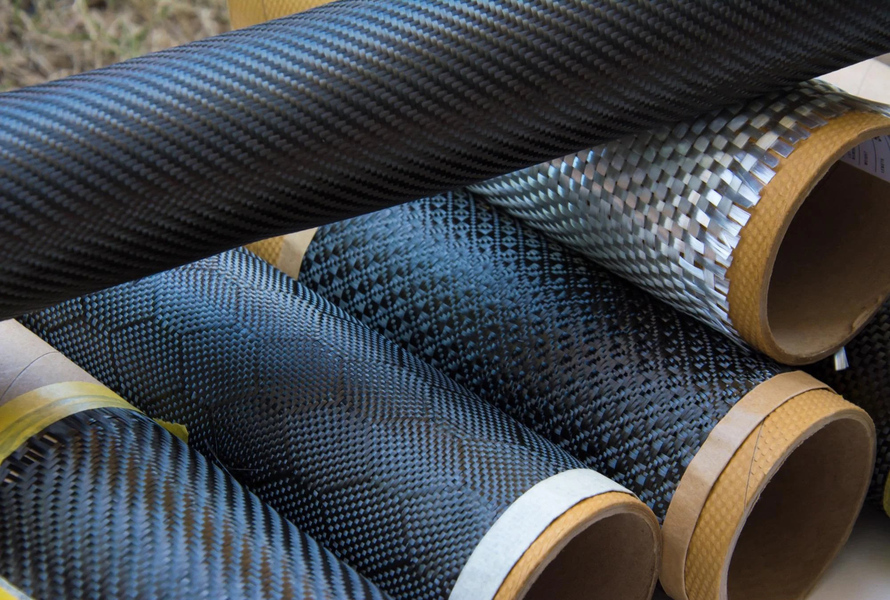
1. Summary of fiberglass and carbon fiber
1.1. Carbon fiber
The most basic structure of carbon fiber includes 90% carbon atoms with a diameter thickness of 5 - 10mm. The physical structure of carbon fiber is formed from the tight bonding of long chains of carbon atoms. Currently, carbon fiber is produced from a variety of materials such as: polyacrylonitrile PAN fiber, cellulose fiber, graphite fiber (carbon ratio > 99%), coal, petroleum or some other fibers.
In addition, the physical interaction and adaptability of carbon fiber is also highly appreciated because they are easily combined with other materials such as: glass fiber, additives to increase characteristics as well as serve each specialized industry. Additionally, carbon fiber also has characteristics that meet production standards. Specifically as follows:
-
Heat resistance: The heat resistance level of carbon fiber is divided into 3 levels. The highest level can withstand temperatures of more than 2000 degrees Celsius and can be combined with UHM fiber. The lowest temperature that carbon fiber can withstand is about 1000 degrees Celsius.
-
High hardness and light weight: Carbon is a very hard fiber and is lighter in weight than other materials. Specifically, it is twice as hard as steel and 5 times stronger than steel but only weighs about 2/3 of the weight of steel.
-
Low elasticity: The expansion coefficient of carbon fiber is -0.74x 10 ^ 6 / K. This is a fairly low index and helps carbon fiber still be able to maintain its state, shape and mechanical properties in high temperature environments.
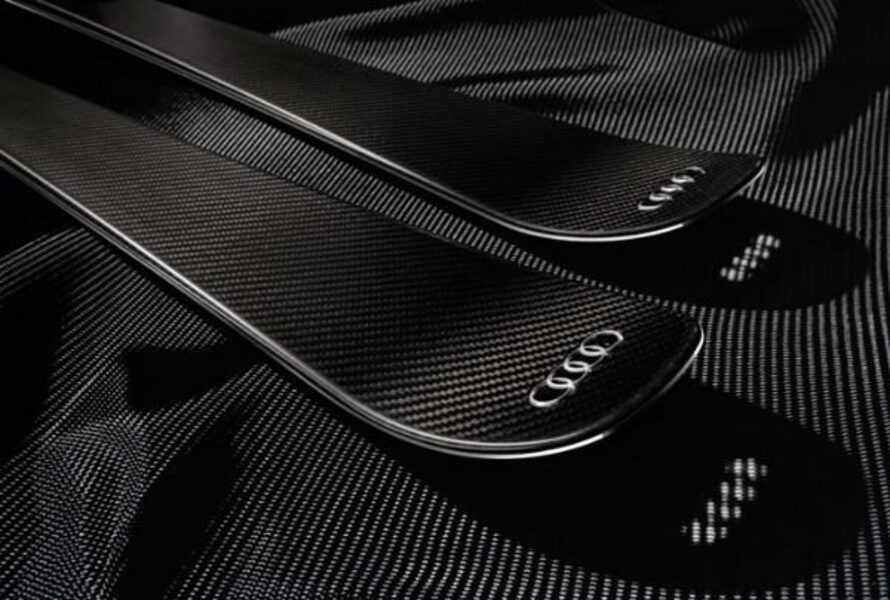
-
Carbon fiber has a fairly thin diameter, averaging only 5 - 10mm and is twisted together. Therefore, the weight of this type of fiber is quite light, allowing them to be flexibly applied in many fields such as sports, medicine, fashion and bringing comfort to consumers.
-
In addition, carbon fiber is also highly conductive, anti-corrosive and self-lubricating. In particular, carbon molecules are resistant to chemicals and help carbon fibers maintain their durability in harsh conditions.
1.2. Glass fiber
Glass is melted at temperatures above 100 degrees Celsius and stretched into thin fibers, which are glass fibers. In particular, if the carbon fiber has a diameter of only 5 - 10mm, the glass fiber is about 1/10 times thinner than natural hair. The main chemical composition of glass fiber includes inorganic groups such as: Cansilicate and Aluminum.
Therefore, the basic properties of glass fiber are extremely thin and light, but they also ensure very good durability and strength. Currently, glass fiber is divided into 4 basic types, named A, C, E and AE respectively. The classification of glass fiber depends on their characteristics and applications. For example: Type C glass fiber is resistant to chemicals and is used in the medical field. Type E glass fiber is a combination of C glass fiber and electrical insulation. Or AE glass fiber will be supplemented with alkali resistance suitable for heavy industries.
These characteristics and diversity help glass fiber increase its practicality and fully meet the criteria of many fields. For example:
-
Glass fiber has the property of being resistant to strong chemicals such as alkali, acid, ... so they can resist abrasion and prevent surface slippage. This is an advantage that is fully utilized in the chemical industry.
-
In addition, glass fiber is linked from thin fibers to create a durable structure, so the elastic modulus of glass fiber is in the range of 70 - 97 GPa. In particular, their tensile strength also shows impressive parameters from 1250 - 3600 MPa. They are used in the automotive & marine industry such as: manufacturing ship hulls, aircraft hulls, car frames.
-
Often used as optical conductors to support telephone transmission as well as television image transmission. The advantages of fiberglass are that it can transmit large capacities, is not affected by electromagnetic interference and is cheaper than using other metal materials.
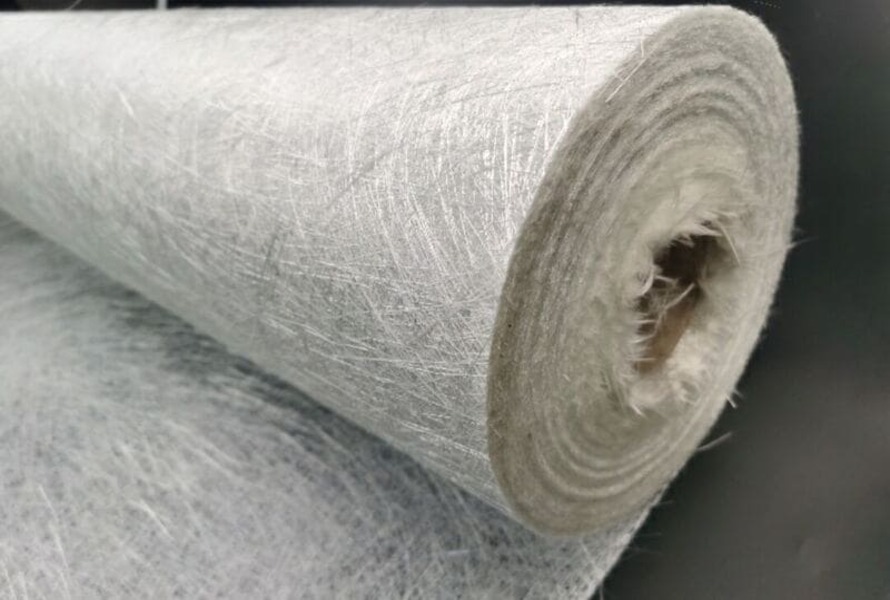
-
Fiberglass can withstand temperatures up to a maximum of 550 degrees Celsius. Therefore, they are also used in the construction materials industry. Fiberglass acts as a surface coating for wall paint as well as reinforcing concrete pieces to not only ensure cohesion but also ensure safety during use.
-
Applications in the medical field: used as a plaster and used to make endoscopes to observe internal organs. Carbon fiber and fiberglass both have their own advantages. Therefore, these two lines of materials are often compared to each other. In the next section, Mega A Logistics will help customers distinguish the difference between fiberglass and carbon fiber. Check it out now!
2. Major differences between carbon fiber and fiberglass
2.1. Differences in the production process
Carbon fiber is produced at the molecular level. The fiber mixture of carbon atoms is liquid polyacrylonitrile that will be oxidized at 300 degrees Celsius to prevent the fibers from melting. To create the purest carbon atoms, the above mixture will be carbonized at temperatures up to 1000 degrees Celsius, helping to completely eliminate impurities and form quality carbon atoms. Carbon fibers will be surface treated to increase elasticity as well as adhesion of coatings.
Meanwhile, glass fibers are born through the process of melting silica to completely remove impurities. Liquid glass will be transferred through small holes on the hot metal plate to form fibers. Then, the glass fibers are cooled by water at a temperature of 1200 degrees Celsius and air. This will help them to be easily stretched and wound into rolls.
2.2. Differences in physical and chemical properties between carbon fibers and glass fibers
Although carbon fibers and glass have similar properties such as: corrosion resistance, high hardness, chemical resistance, moderate weight or heat resistance, the detailed parameters will have significant differences. Specifically as follows:
-
If the tensile strength of carbon fibers reaches 1000 MPa, glass fibers are only limited to 700 MPa.
-
In addition, the elastic modulus of carbon fiber is 651.5 GPa, which is higher than that of glass fiber (only 72.5GPA)
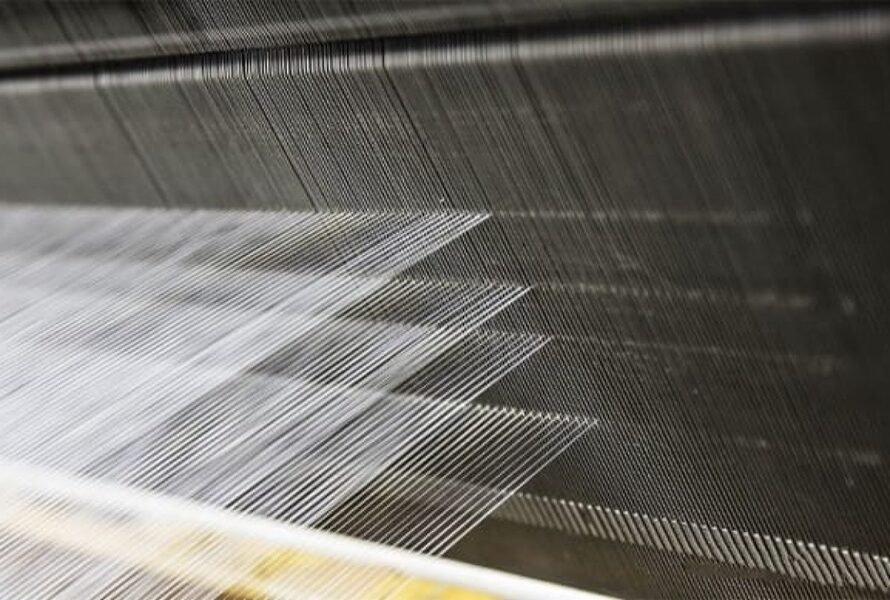
-
Glass fibers can be bent and increased in tension, but they will not break because the elastic modulus is lower than carbon fiber.
-
Normally, the main application of glass fiber will be suitable for products such as insulation materials, fashion, coatings or reinforcement for synthetic composites. Meanwhile, carbon fiber is mainly used in heavy industries such as aerospace, automobiles, sports equipment, and construction materials.
In general, the durability and quality of carbon fiber are rated higher than glass fiber. Currently, one of the very popular fields is 3D printing, which also has the presence of carbon fiber and glass fiber, so manufacturers are constantly balancing the quality and efficiency of both of these materials. The answer will be answered in detail by EuroPlas in the next section.
3. Fiberglass and carbon fiber: Which is better for 3D printing?
Fiberglass and carbon fiber are two popular materials in the 3D printing field because both types of fibers have the characteristics of hardness, toughness and good combination with other materials. Therefore, carbon fiber and glass fiber are applied in the 3D printing field to ensure that the product meets the following basic standards: Standard geometric dimensions, stable mass, long-term durability, high practicality and safety for consumers' health.
Both carbon fiber and glass are capable of ensuring the standards of the manufacturer, but they also have differences depending on the raw materials and conditions during the 3D printing process. Some of the main differences are: Polymer base material (ABS, nylon, polycarbonate), base material blend type, mechanical quality of the 3D printer or percentage of filament mixed in.
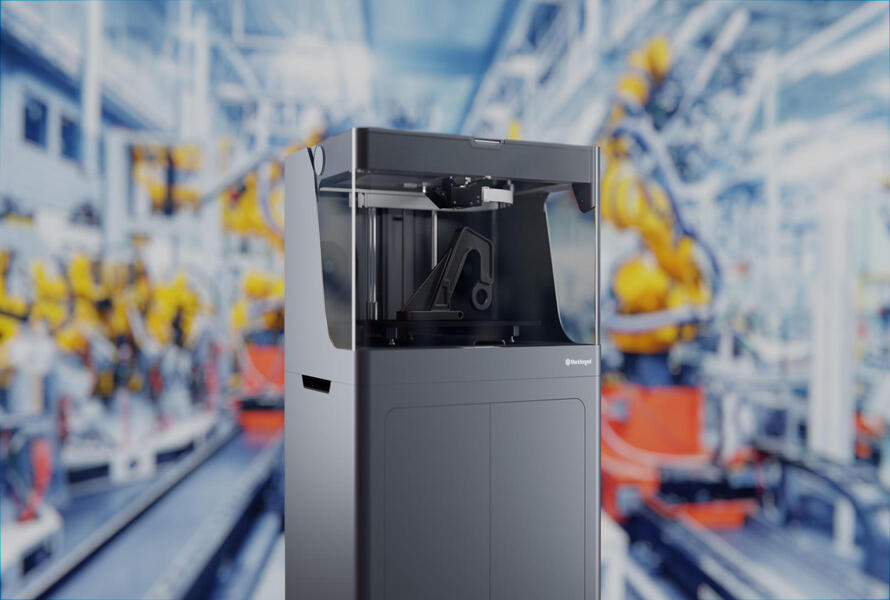
Depending on the requirements of each 3D printed product, the manufacturer will choose fiberglass or carbon fiber, EuroPlas will suggest to customers some criteria to consider between these two fiber materials!
-
Because the production process is complicated and requires high carbon molecules, the price of carbon fiber will be higher than that of glass fiber. Therefore, if the 3D printed product serves mid-range customers or in small markets, the manufacturer will prioritize using glass fiber.
-
In addition, 3D printed products require high stiffness and tensile strength, so carbon fiber will be the right choice. Because these indexes of glass fiber are much lower, they will be limited in withstanding impacts or strong forces from the outside.
-
On the contrary, the elastic modulus of glass fiber is lower than carbon, so this type of material is suitable for products that require high flexibility and durability. In addition, fiberglass is also easy to combine with multi-color substances or powders, which will produce more brilliant and precise colors than carbon fiber.
-
If we compare in terms of mass, carbon fiber will completely dominate. 3D printed products from carbon fiber will be lighter than products printed from glass fiber. At the same time, their fatigue strength will also be higher. In addition, carbon fiber is not only light but the products also possess stable anti-static properties.
-
In particular, carbon fiber is very difficult to contact with microwaves, which is extremely easy for products from glass fiber.
Those are the basic criteria and requirements in choosing carbon fiber or glass fiber for the 3D printing industry. In general, both material lines demonstrate good capabilities in terms of resistance to strong chemicals, UV resistance as well as high heat resistance. Whether carbon fiber or glass is more suitable for 3D printing is difficult to answer, the decision depends on the needs, financial conditions, equipment and the target customers that the manufacturer wants to target.
4. Introduction to EuroPlas
EuroPlas aims to become the world's leading enterprise in the field of supplying raw plastics. EuP owns modern equipment such as extruders, blowers, injection molding machines, etc., along with a system of standard measuring machines such as thermal deformation testers, impact resistance testers, tensile strength testers, etc. Thereby ensuring the highest quality products to customers.
With 7 factories of tens of hectares in 6 provinces: Ha Nam, Yen Bai, Hai Phong, Nghe An, Long An and Ho Chi Minh City, along with a modern production line system, EuP's annual capacity reaches approximately 0.8 million tons, ready to meet large orders from all over the world. Currently, EuroPlas provides 2 main fiberglass compound product lines: PA6 & PA66
PA66 & PA6 Compound fiberglass is a group of engineering plastics made from PA66 & PA6 plastic base with glass fiber reinforcement. PA66, PA6 fiberglass compound from EuroPlas has 30 - 50% glass fiber content. It is widely used in the production of gears, bearings, transmission belts, carburetor components, computer components or household electrical components.
5. Conclusion
The above article has summarized an overview of information about carbon fiber and fiberglass. In addition, EuroPlas has also pointed out the differences between fiberglass and carbon fiber. In particular, we have provided the answer to the question of fiberglass and carbon fiber: Which is better for 3D printing? Stay tuned to EuroPlas for the latest news on the plastic materials market!