The global composite market is predicted to reach USD 185.36 billion by 2032, with a 7.1% compound annual growth rate (CAGR) throughout the forecast period. The increasing demand for lightweight and robust materials in industries such as aerospace, automotive, and construction is driving this expansion.
The world of composite materials is a captivating tapestry of innovation, where plastic takes center stage as the versatile foundation for creating exceptional materials. Through the ingenious combination of plastic with other materials, composite materials have become the driving force behind technological advancements, shaping the future of industries as diverse as aerospace, automotive, and construction.
1. Mechanics of composite materials
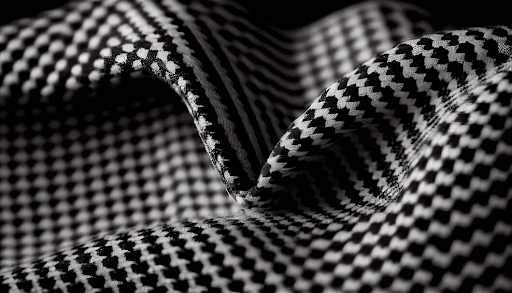
Carbon fiber composites deliver strength, stiffness, and lightweight
1.1. Overview of composite materials
Composite materials are a type of material that is made up of two or more different phases. One of the phases, known as the matrix, is often a polymer, such as plastic, that surrounds and secures the reinforcement. The reinforcement, which can be formed of fibers, particles, or whiskers, is responsible for the strength and stiffness of the composite material.
1.2. Evolution of composite materials
The concept of composite materials dates back to ancient civilizations, where natural composites such as mudbrick and timber were used in construction. The modern era of composite materials began in the early 20th century with the development of synthetic resins and fibers. The use of composites gained momentum during World War II, as they were used to replace traditional materials in aircraft construction.
1.3. Key characteristics and advantages
Composite materials offer a number of key advantages over traditional materials, including:
Enhanced strength and stiffness: Bioplastic compounds are often reinforced with strong fibers, such as glass fibers or carbon fibers, to enhance their strength and stiffness. This is because the reinforcement phase, such as fibers or particles, can be oriented in a specific direction to provide maximum strength and stiffness in that direction.
-
Lightweight: Biofillers can contribute to lighter composites, as they are lighter than traditional materials like wood flour or cellulose. This is because the matrix phase, typically a plastic, is lighter than the reinforcement phase.
-
Ductility and toughness: Composite materials can be ductile and tough, meaning that they can be deformed without breaking and can absorb energy before breaking. This is important for applications where materials need to withstand impact or fatigue.
-
Resistance to heat and corrosion: Engineering plastic compounds are often made from heat- and corrosion-resistant polymers, such as nylon or polypropylene.
-
Design flexibility: Composite materials can be designed to have a wide range of properties, making them versatile for a variety of applications.
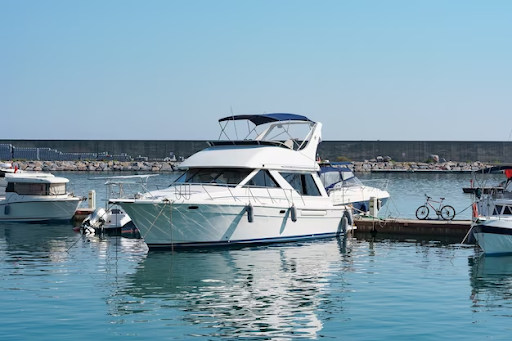
Fiberglass composites are the backbone of marine applications
2. Types of composite materials
2.1. Polymer matrix composites (PMCs)
Polymer matrix composites (PMCs), where ordinary plastic undergoes a remarkable metamorphosis, gaining newfound strength, stiffness, and resilience.
Plastic serves as the matrix, the foundation that binds together the reinforcing elements. These reinforcing elements, typically fibers or particles, introduce extraordinary properties to the plastic matrix, creating a composite material that far surpasses the limitations of plain plastic.
-
Glass-fiber reinforced PMCs: Glass fibers, woven into the plastic matrix, impart exceptional strength and stiffness, making PMCs ideal for applications where lightweight and robust materials are essential.
-
Carbon-fiber reinforced PMCs: Carbon fibers, renowned for their exceptional strength-to-weight ratio, transform plastic into a high-performance material, suitable for demanding applications where weight is a critical factor.
-
Aramid-fiber reinforced PMCs: Aramid fibers, known for their exceptional strength, toughness, and heat resistance, infuse plastic with these remarkable properties, making PMCs suitable for applications where protection and durability are paramount.
PMCs represent a captivating fusion of plastic and reinforcing elements, opening up possibilities for lightweight, strong, and durable materials.
2.2. Metal matrix composites (MMCs)
Metal matrix composites (MMCs) stand out as a group of materials that bring together the strength and durability of metals with the versatility and lightweight nature of reinforcing materials.
They are remarkably strong and stiff, making them suitable for structural components that require high load-bearing capabilities. Additionally, their lightweight nature makes them attractive for applications where reducing weight is crucial, such as in the aerospace and automotive industries.
Here are a few notable examples of MMCs:
- Aluminum MMCs: These composites feature aluminum as the matrix material, known for its lightweight and corrosion-resistant properties. Aluminum MMCs are often reinforced with ceramic fibers, such as silicon carbide or alumina, to enhance their strength, stiffness, and wear resistance.
-
Magnesium MMCs: Magnesium MMCs utilize magnesium as their matrix material, valued for its exceptional lightness and high strength-to-weight ratio. Reinforcing materials like silicon carbide or boron nitride are commonly used to further improve their mechanical properties.
-
Titanium MMCs: Titanium MMCs leverage the outstanding strength, corrosion resistance, and high-temperature performance of titanium as the matrix material. Reinforcing fibers such as silicon carbide or carbon fibers are often incorporated to enhance their stiffness and wear resistance.
2.3. Ceramic matrix composites (CMCs)
CMCs are not just a mere blend of ceramics and polymers; they are a synergistic fusion of materials, where each component enhances the properties of the other. The ceramic matrix, often silicon carbide or alumina, provides exceptional strength, hardness, and resistance to heat and wear. The reinforcing fibers, typically carbon or silicon carbide, imbue the material with flexibility and toughness, enabling it to withstand stress and impact.
Some of the most common types of CMCs include:
-
Silicon Carbide CMCs (SiC CMCs): Renowned for their exceptional strength, high-temperature resistance, and wear resistance, SiC CMCs are widely used in aerospace and industrial applications.
-
Alumina CMCs (Al2O3 CMCs): Offering a combination of high strength, wear resistance, and electrical resistivity, Al2O3 CMCs find applications in various industries, including automotive, electronics, and biomedical.
-
Boron Nitride CMCs (BN CMCs): Boasting exceptional strength, high-temperature resistance, and chemical resistance, BN CMCs are used in applications that demand extreme performance and durability.
2.4. Carbon matrix composites (CAMCs)
Carbon matrix composites (CAMCs), crafted by intertwining carbon fibers with a carbon matrix, offer a remarkable blend of strength, stiffness, and temperature resistance that has captivated the attention of plastic manufacturers.
CAMCs are extremely remarkable in their capacity to resist severe temperatures. While most materials begin to degrade at high temperatures, CAMCs may retain their strength and integrity even in temperatures as high as 3,000 degrees Celsius, making them ideal for use in high-performance applications such as rocket engines and hypersonic vehicles.
There are two main types of CAMCs
-
Continuous fiber composites boast long, uninterrupted fibers that span the entire matrix, imbuing the material with unparalleled strength and stiffness.
-
Discontinuous fiber composites employ shorter fibers randomly dispersed throughout the matrix. This arrangement, while offering slightly reduced strength, facilitates easier manufacturing and allows for tailoring the material to specific needs.
CAMCs are a promising class of innovative materials with the potential to transform a wide range of industries. Because of their distinct qualities, they are suited for use in high-performance applications requiring great strength, stiffness, and temperature resistance.
3. Applications of composite materials
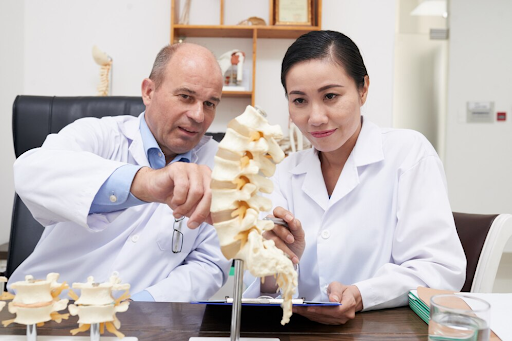
Biocompatible composite implants that promote healing and function
3.1. Automotive industry
The automotive industry is revving up with plastic composites, replacing heavy steel with lightweight plastic body panels, boosting fuel efficiency and reducing emissions. If composite materials in automotive applications may lower a car's weight by up to 10%, it equates to a 6-8% increase in fuel efficiency.
Picture engine components made from plastic composites, revving up performance while shedding excess weight. And envision those stylish and durable automotive interiors, a testament to the versatility of plastic composites.
3.2. Construction industry
The building industry is embracing the strength and sustainability of plastic composites, substituting lightweight and strong plastic alternatives for traditional materials. Durable and lightweight structural components can help to lighten our planet's load. Consider structures made of plastic composites that are both energy efficient and environmentally beneficial. Consider bridges, roads, and other infrastructure that has been reinforced with plastic composites that can withstand the test of time.
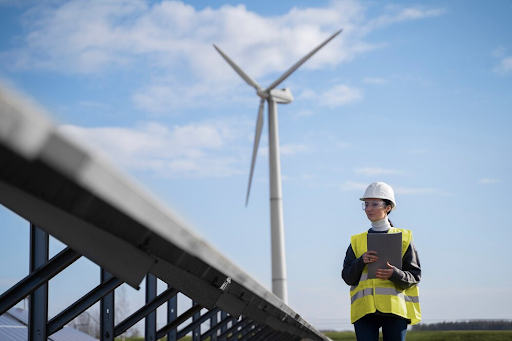
Composite blades is powering wind energy's future
3.3. Sporting goods
Plastic composites enable athletes to achieve new heights. Thanks to plastic composites, golfers are swinging with enhanced clubhead speed and precision. Tennis players are benefiting from improved racquet performance and control thanks to plastic composites. And riders are riding on lightweight, robust, and responsive plastic composite-powered bicycles.
3.4. Biomedical applications
Plastic composites are sparking a paradigm change in healthcare, giving patients fresh hope and altering medical treatments. Bone implants made of biocompatible and durable plastic composites are restoring mobility and enhancing people's lives. Dental fillings are changing dental treatment thanks to the strength, longevity, and cosmetic appeal of plastic composites. And, with the introduction of plastic composites in medical equipment, we are on the verge of new healthcare innovations.
4. Future of composite materials
The world of composite materials is poised for an exciting future, where plastic plays a pivotal role in shaping the materials of tomorrow.
4.1. Ongoing research and development
Researchers and scientists are relentlessly pushing the boundaries of composite materials, venturing into uncharted territory by experimenting with novel combinations of plastic matrices and reinforcing fibers to create materials with extraordinary properties.
Plastic composites that are stronger than steel, lighter than aluminum, and more heat resistant than ceramics are just a few of the possibilities.
4.2. Emerging applications of composite materials
The potential applications of composite materials are truly limitless, extending far beyond the industries we typically associate them with. As these materials continue to evolve, we can expect to see them transform everything from infrastructure to medical devices, transportation to renewable energy.
4.3. Impact of composite materials on various industries and societies
Composite materials will have a significant impact on numerous sectors and civilizations. Composite materials in the construction sector can result in lighter, stronger, and more energy-efficient buildings. They can help fuel-efficient automobiles and cut pollutants in the automotive industry. Composite materials can also pave the way for new prosthetics and implants that improve patient outcomes in the medical profession.
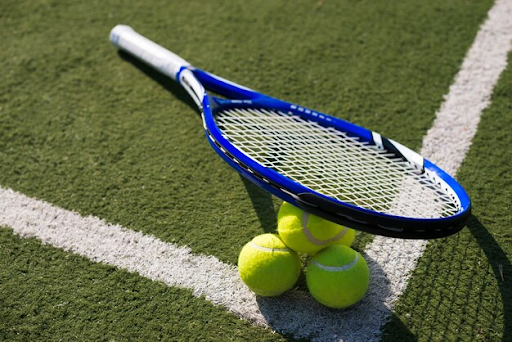
Composite tennis racquets empower players with a winning blend of power, control, and agility
5. Conclusion
Composite materials are a type of material created by fusing two or more distinct materials into a single substance. This results in a material with qualities that outperform the separate materials.
They are helping us to address global challenges such as climate change, resource scarcity, and economic growth.
If you want to learn more about composite materials or innovative plastic solutions and technologies, be sure to check on the EuroPlas library.