Ductility is one of the important characteristics of plastics that greatly impacts the material's load-bearing capacity and durability of products. The ductility of materials is not only demonstrated in their ability to bend and stretch but also in their ability to withstand strong impacts, such as collisions and compressions, without breaking or cracking. Understanding the ductility of plastics helps manufacturers design high-quality products that meet market demands and minimize waste during production. This article will explore various aspects of ductility in plastics and its role in modern plastic product applications.
1. Definition of Ductility in Plastics
Ductility in plastics is defined as the ability to deform without being destroyed when subjected to force or temperature. Ductile materials often have the capacity to change shape when heated without breaking, allowing them to be widely used in producing a diverse range of products, from household items to industrial components. This ductility makes plastics an ideal material for design and manufacturing, providing flexibility and high resilience during use.
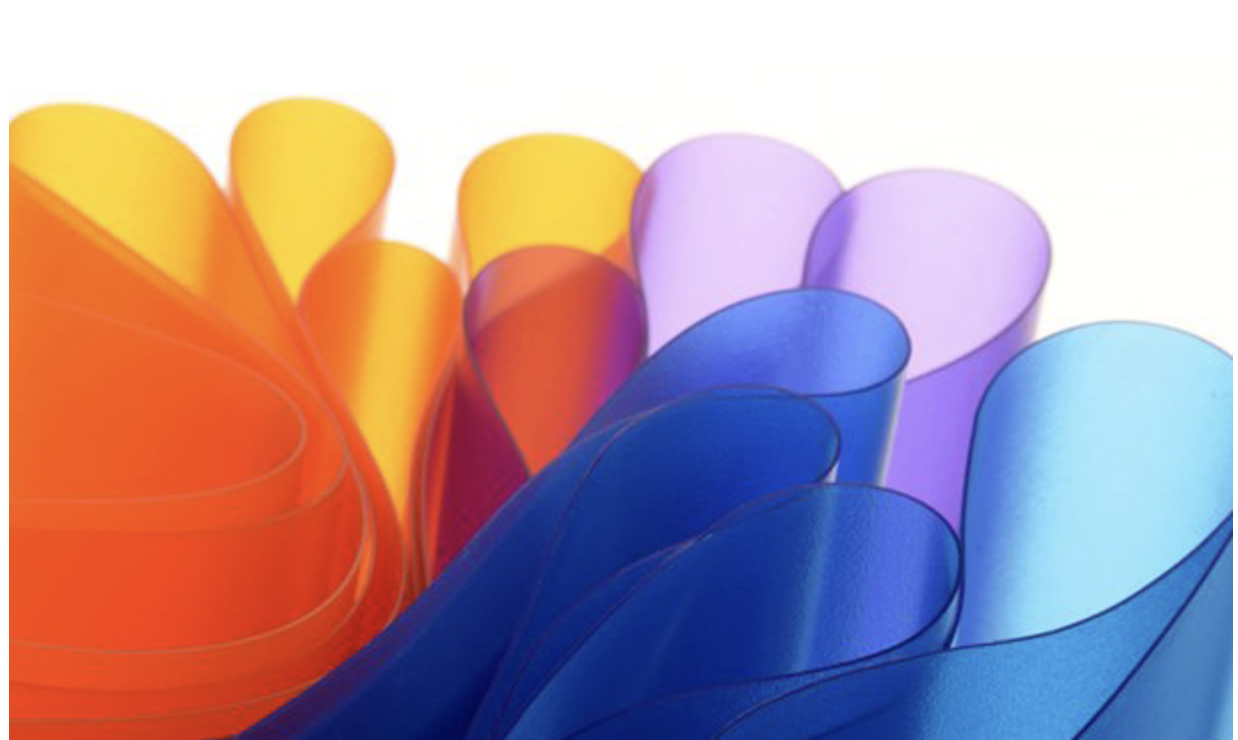
1.1. Characteristics of Ductility
Ductility in plastics is not only an important technical feature but also influences the application potential of plastics across various fields. By understanding ductility, we can optimize the use of plastics, improving product quality and contributing to environmental protection. Key features of ductility in plastics include:
- Strength: High ductility provides strength to plastic products, making them less likely to shatter or break under impact.
- Flexibility: Ductility allows bending without breaking or permanently deforming, enabling versatile product design.
- Customizability: Ductility permits changes in structure and shape of plastics to fit multiple applications, crucial for enhancing products to meet market needs.
1.2. Technical Characteristics of Ductility
Some technical characteristics of ductility in plastics include:
- Yield Point: The yield point is the moment when a material starts to experience permanent deformation, indicating how much pressure it can withstand without damage. The yield point of ductility in plastics may vary depending on their type and composition.
- Elastic Modulus: The elastic modulus is a measure of how stiff a plastic material is when stretched or compressed and changes depending on the type of plastic and its physical properties. A higher elastic modulus indicates material rigidity, while a lower modulus reflects material ductility and bending capability.
- Tensile Strength and Elongation: Tensile strength and elongation are often used to determine a plastic's capacity to withstand forces without breaking. Here, tensile strength indicates the overall strength and deformability of the plastic when under load.
Below is a table summarizing the thermal limits and melting points of ductile plastics:
Type of Plastic
|
Thermal Limit (°C)
|
Melting Point (°C)
|
Polystyrene (PS) |
-20°C - 70°C
|
210°C - 240°C
|
Polyethylene (PE)
|
-50°C - 80°C
|
115°C - 135°C
|
Polypropylene (PP)
|
0°C - 120°C
|
130°C - 171°C
|
Polycarbonate (PC)
|
-135°C - 135°C
|
220°C - 230°C
|
Polyvinyl Chloride (PVC)
|
-10°C - 60°C
|
100°C - 260°C
|
Polyethylene Terephthalate (PET)
|
-40°C - 70°C
|
250°C - 260°C
|
Acrylonitrile Butadiene Styrene (ABS)
|
-20°C - 80°C
|
210°C - 270°C
|
1.3. Pros and Cons of Ductility
Advantages:
- Recyclability: Ductile plastics can be recycled to produce new products, helping minimize environmental damage.
- Flexibility and Variety: Ductile plastics can be manufactured into numerous shapes, meeting the needs of various industries.
Good Water Resistance: Ductile plastic often has effective waterproof capabilities, protecting products from moisture and external elements.
Disadvantages:
- Risk of Environmental Pollution: If not treated and recycled properly, ductile plastics can cause significant environmental pollution, affecting human health.
- Lower Strength Compared to Metals: In some applications requiring high durability, ductile plastics may not be suitable due to their lower mechanical strength compared to materials like metals.
1.4. Applications of Ductility
Ductile plastics play a significant role in determining their application capacity in various industries. Here are specific fields where ductile plastics are utilized, along with detailed applications:
Household Goods Production: Ductile plastics are widely used in producing household items owing to their flexibility and waterproof qualities. Notable applications include storage boxes, children's toys, etc.
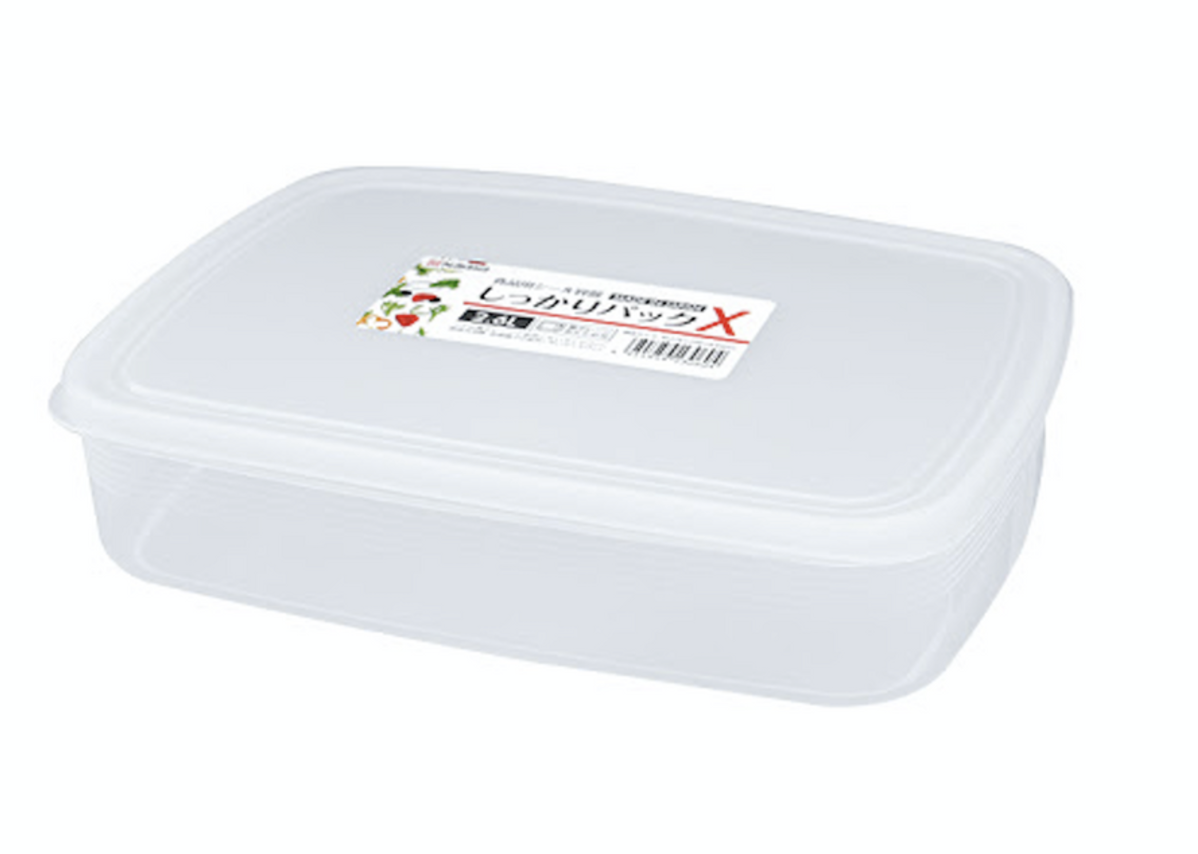
Packaging Industry: Packaging is one of the largest applications of ductile plastics. Ductile plastics are commonly used to produce various food packaging types, including food wrap, bags, and zipper bags.
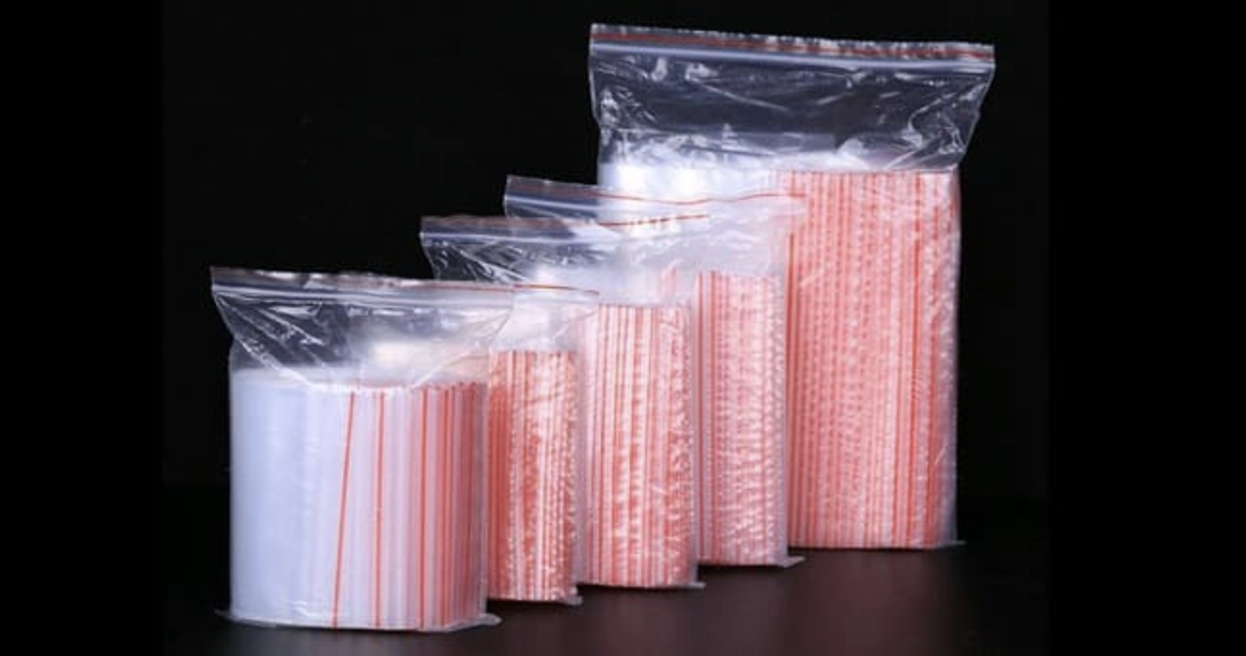
Electrical and Electronics: Ductile plastics are crucial in producing electronic components. Notable applications include cable sheathing, electronic device casings, etc.
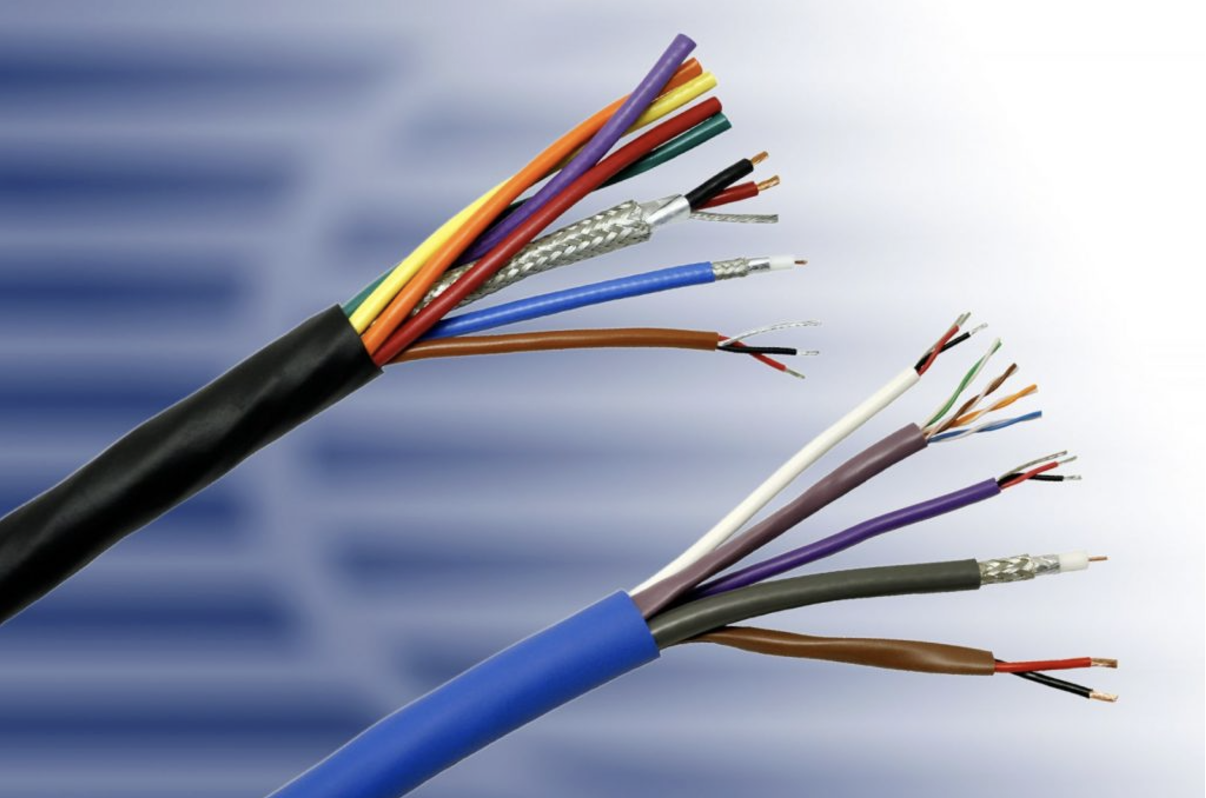
Construction Industry: Ductile plastics are often used for many applications to protect and improve the performance of structures. Notable applications include waterproof membranes, water conduits, drainage pipes, etc.
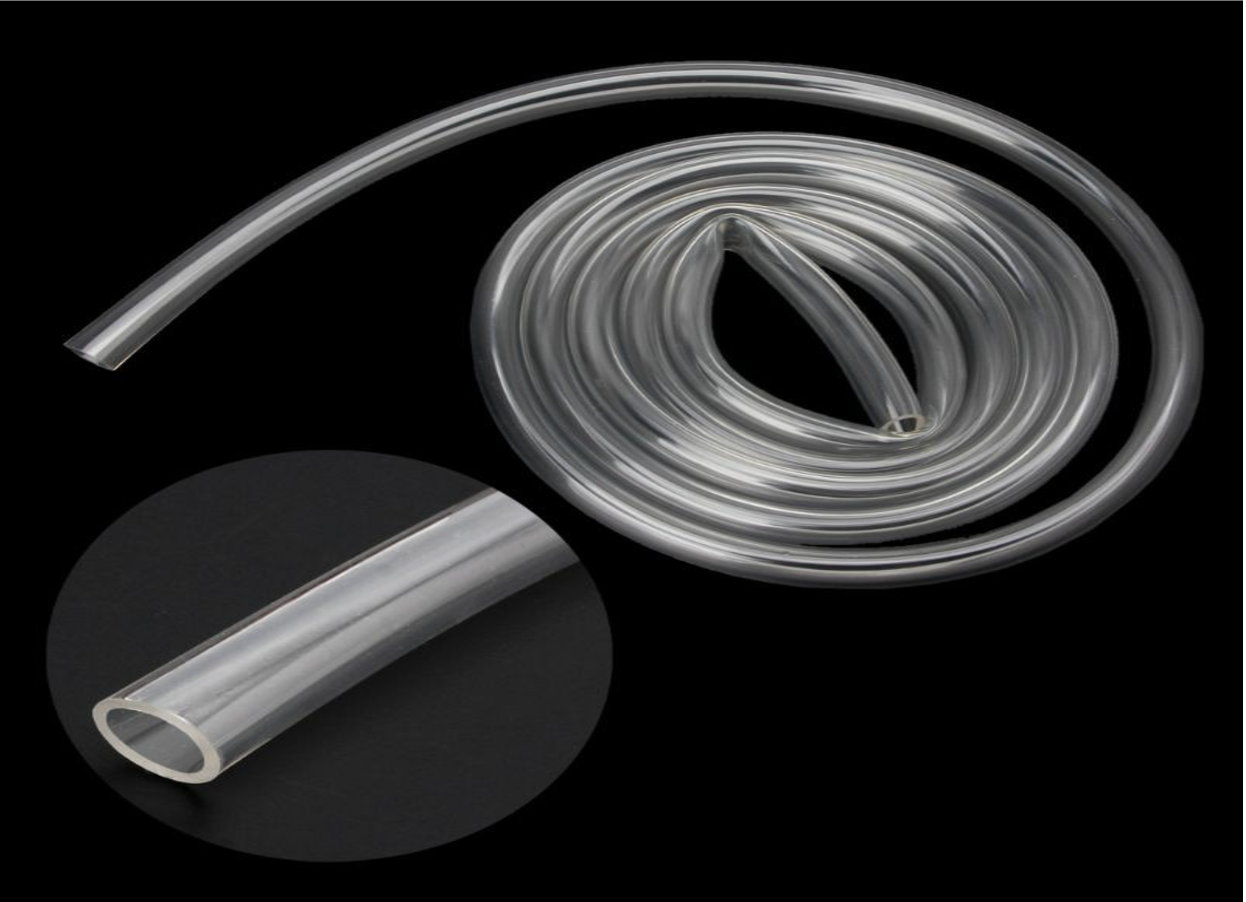
Textiles Industry: Ductile plastics improve the durability and flexibility of clothing products. Notable applications include synthetic fibers (nylon, polyester, etc.), non-woven fabrics (masks, diapers, shoe lining materials, etc.).
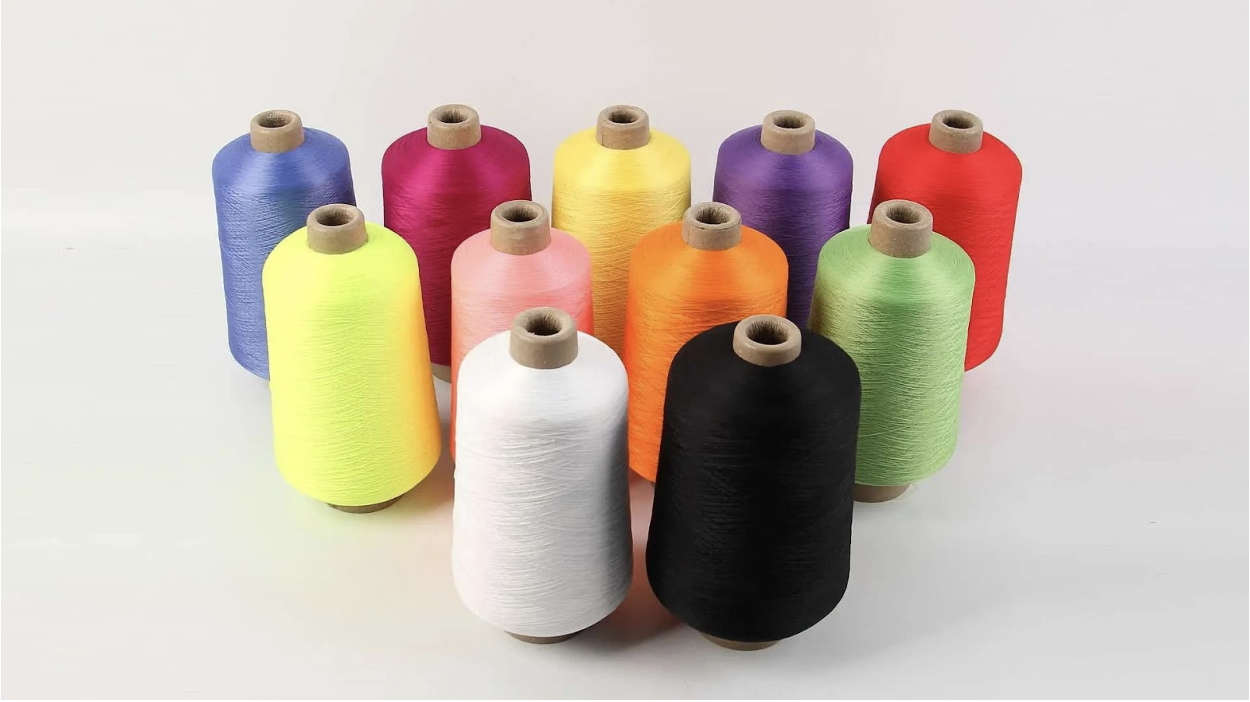
Healthcare: The ductility of plastics is vital in healthcare, where materials must ensure safety and sterility. Notable applications include intravenous tubes, blood bags, etc.
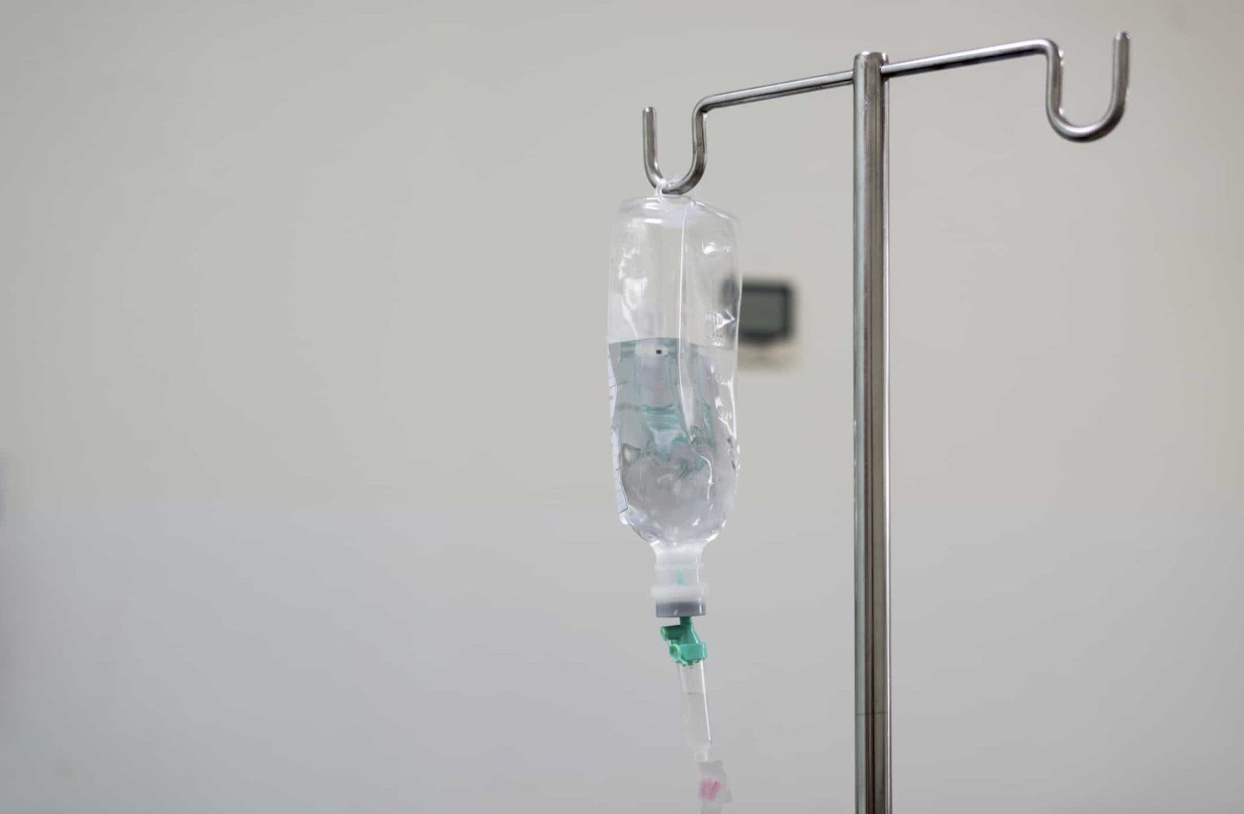
2. Mechanism of Plastic Ductile Deformation
Ductile deformation in plastics is the ability to change shape when subjected to force without returning to the original shape after the force is removed. This mechanism depends on the chemical structure and physical properties of the plastics. When stressed, the molecular structure of plastics undergoes a transformation process, leading to the temporary breaking of bonds in the polymer network. This allows polymer chains to move more freely, resulting in ductile deformation.
The process of ductile deformation in plastics is typically divided into two main stages:
- Elastic Stage: In this stage, plastics return to their original shape when the force is no longer applied. This stage depends on the polymer network structure, temperature, and loading rate.
- Ductile Stage: When the stress exceeds a certain threshold (yield point), permanent deformation occurs. In this stage, stress allows the material to be ductile without breaking apart or losing structure.
3. Classification of Plastics by Ductility
Plastics can be classified into various categories based on their ductility, with two main groups being thermoplastic and thermosetting plastics.
Group 1: Thermoplastic: This type of plastic can soften when heated and harden as it cools without undergoing chemical change. These properties allow thermoplastics to be recycled multiple times without losing their beneficial characteristics. Common thermoplastics include polyethylene (PE), polypropylene (PP), and polyvinyl chloride (PVC).
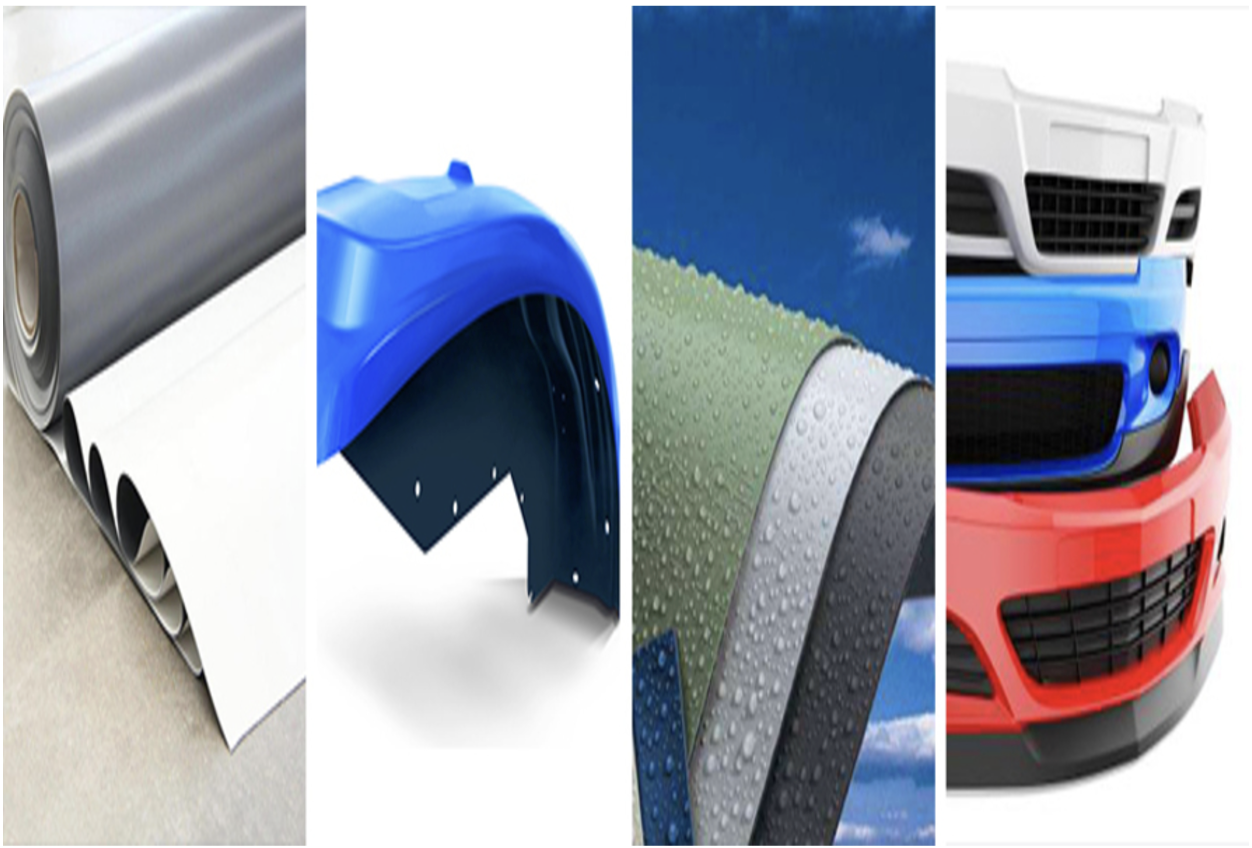
Group 2: Thermosetting: In contrast to thermoplastics, thermosetting plastics cannot revert after they are formed and cooled. Once a thermosetting plastic is shaped, any attempt to reheat it will not make it soft but will usually lead to burning or damage. This type of plastic is mainly used in applications requiring high durability and temperature resistance, such as epoxy and phenolic plastics.
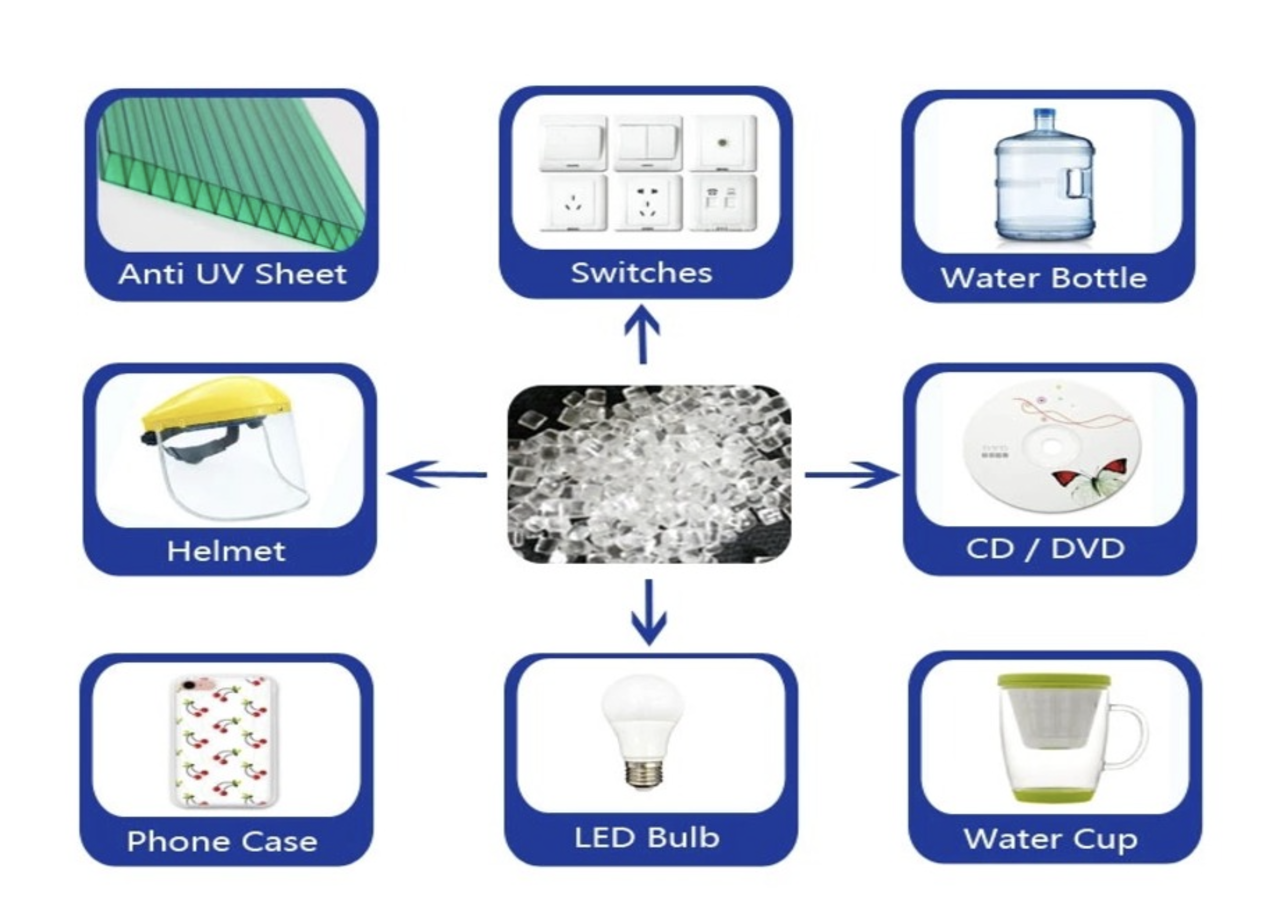
Below is a detailed comparison table outlining the properties and applications of thermoplastics and thermosetting plastics, facilitating easier differentiation and selection for specific uses.
Criteria
|
Thermoplastic |
Thermosetting
|
Production Process
|
Formed through heating and melting
|
Formed through chemical reaction and cannot be recycled
|
Molecular Structure
|
Comprises non-cross linked monomer chains, easily change shape
|
Has a stable network structure that does not break down upon heating
|
Recyclability |
Can be recycled multiple times while maintaining chemical properties
|
Cannot be recycled, does not revert to original state after hardening
|
Melting Point
|
Low melting point, generally temperature resistant from 105°C to 175°C
|
High melting point, ranging from 150°C to 300°C, depending on the type
|
Flexibility
|
Highly flexible, can be remolded upon heating
|
Rigid and brittle, cannot change shape after hardening
|
Applications |
Commonly used in packaging, household items, consumer products
|
Used in electrical, automotive, construction, and electronic component production
|
Production Cost
|
Lower cost, easy to produce and handle
|
Higher cost due to more complex production processes |
Durability
|
May not be as durable as thermosetting plastics, susceptible to high temperatures. |
Higher durability, good resistance to force and chemicals.
|
4. Importance of Ductility in the Plastic Industry
Ductility plays a crucial role in the plastic industry, directly impacting the production capabilities and applications of plastic products. Some notable reasons are:
- Processability: Ductility allows plastics to be easily processed and shaped. Manufacturing processes such as blowing, molding, and injection molding require plastics to be ductile to be shaped into various designs. This contributes to product design flexibility and optimizes production processes.
- Production of Load-bearing Materials: High ductility in plastics allows them to absorb impact forces well, preventing breakage. Plastic products like packaging, household items, and electronic components are often designed with high ductility to ensure long-term usability in various working conditions.
- Recycling and Environmental Protection: As mentioned earlier, the ductility of thermoplastic allows for easy recycling. The use of ductile plastics minimizes plastic waste, contributing to sustainable development and environmental protection. Furthermore, the industry is increasingly focusing on developing recyclable plastics to address contemporary environmental issues.
5. Conclusion
Ductility in plastics is not just a physical property but also a decisive factor affecting the application capabilities and production of plastics in everyday life. From the mechanism of shape transformation to classification and their significance, ductility demonstrates an indispensable role in the plastic industry. Ductility in plastics not only aids in producing diverse and multifunctional products but also greatly contributes to sustainable development in industry. To optimize these benefits, researching and developing new, sustainable, and environmentally friendly ductile plastics is essential. Understanding ductility will help businesses make informed choices and enhance product quality while providing economic value and ensuring consumer safety.
6. About EuroPlas
EuroPlas is one of the leading companies in the plastic industry, particularly known for its high-quality filler masterbatch products. EuroPlas not only provides plastic products that meet European quality standards but also continually seeks innovative solutions to enhance production efficiency for customers.
With a commitment to delivering sustainable value and customer satisfaction, EuroPlas is strongly developing and asserting its position in the international plastic industry. If you are looking to learn more about high-quality plastic products or have any questions regarding their applications in production, please contact EuroPlas today for dedicated and professional consultation. EuroPlas is always ready to support and accompany you in finding optimal solutions for your plastic production needs!