Compound PPs are among the leading engineering plastics, significantly outperforming traditional resins. With a remarkable 30.96% market share in the global thermoplastics market, Compound PPs find extensive applications in various industries. This article provides a detailed overview of EuroPlas’ exceptional Compound PP ranges and their superior advantages.
1. What are Compound PPs?
Compound PPs are composites formed by combining PP (Polypropylene) resin with special reinforcing agents such as glass fibers, talc, conductive carbon black, or flame retardants. Unlike standard PP resins, Compound PPs are custom-engineered to meet specific requirements of individual applications and products, enhancing mechanical performance and special technical characteristics.
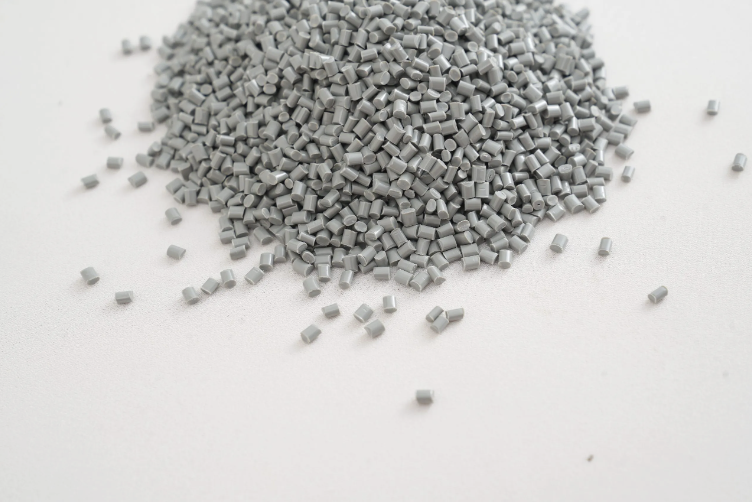
1.1 Technical Properties
Compound PPs exhibit numerous superior technical advantages, highlighted by the following key properties:
- High dimensional stability
- Excellent heat resistance
- Compliance with UL94 V0, V1, V2 standards
- High stiffness and impact resistance
- Conductivity (for carbon black filled grades)
- Scratch and abrasion resistance
- High temperature resistance and dimensional stabilit
With outstanding technical properties such as high dimensional stability, excellent heat resistance, compliance with stringent standards, and superior durability and flame retardancy, Compound PPs are the ideal material for industrial applications requiring high performance and safety.
1.2 Manufacturing Process
The production process of Compound PP granules involves a sequence of steps, strictly controlled in terms of technical parameters and operating conditions to ensure product quality. The main steps in the process include:
- Preparation of raw materials: Virgin PP granules, additives, fillers, colorants, stabilizers, etc.
- Quality inspection of raw materials: Moisture content, particle size, purity, etc.
- Dry blending of components according to the predetermined ratio for 10-15 minutes at room temperature.
- Melting and mixing the blend in a twin-screw extruder at a temperature of 180-250°C with a speed of 100-300 rpm for 2-5 minutes.
- Cool the product with water to 30-40°C for 1-2 minutes.
- Cutting the cooled resin into uniform granules of 2-4mm.
- Drying the granules at 80-100°C for 2-4 hours to achieve a moisture content below 0.1%.
- Inspection of physical and visual quality indicators of the product.
- Packaging the product in PE or PP bags and storing in conditions of 15-35°C and humidity below 70%.
The Compound PP granule production process is a closed-loop process, strictly controlled from raw material preparation to the final product. Each step in the process plays a vital role with specific technical parameters, contributing to the production of stable quality products that meet the requirements of use.
2. Outstanding Compound PPs of EuroPlas
Polypropylene (PP) is one of the most widely used materials in the plastics industry, renowned for its exceptional properties. However, to meet the specific requirements of different industries, PP needs to be blended with various additives to create Compound PPs with specialized features. Below are 6 common types of Compound PPs and their characteristics:
Glass fiber reinforced Compound PP is an engineering plastic composite made from PP resin, glass fibers, and suitable additives. This compound is specifically designed to enhance the stiffness and tensile strength of the final product. EuroPlas offers a variety of types with different glass fiber densities (ECP PP 10GF to 50GF), suitable for applications in the automotive, electrical equipment, and furniture industries.
Advantages:
- Increased stiffness, reduced shrinkage
- Improved impact resistance and heat resistance
- Enhanced strength of the final product
- Can be directly processed without the need for additional blending

Glass bead filled Compound PP is an engineering plastic composite made from PP resin, glass beads, and suitable additives. The main advantage of glass beads is their transparency, mechanical strength, and heat resistance. This product is widely used in automotive interiors and applications requiring high stability.
Advantages:
- Creates a uniform, transparent shape
- Good molding and heat stability
- Defines the shape of the finished product
- Custom design to meet specific requirements

PP-Talc compound is a blend of PP resin, talc, and additives. With 20% talc content, this compound is particularly suitable for manufacturing motorcycle and automobile parts, or products requiring high durability and heat resistance (120-130°C). The product can be directly processed without any additional steps.
Advantages:
- Good thermal conductivity, reduced shrinkage
- Increased stiffness and flexural modulus
- Custom design for specific applications
- Reduced tendency to warp at high temperatures

EuroPlas PP-BaSO4 compound is made from PP resin, barium sulfate, and suitable additives. This compound helps to reduce shrinkage and deformation at high temperatures, while enhancing dimensional stability, heat resistance, chemical resistance, and impact resistance.
Advantages:
- Improves molding
- Increases gloss and stiffness
- Custom design for specific products
- Reduces shrinkage and deformation at high temperatures
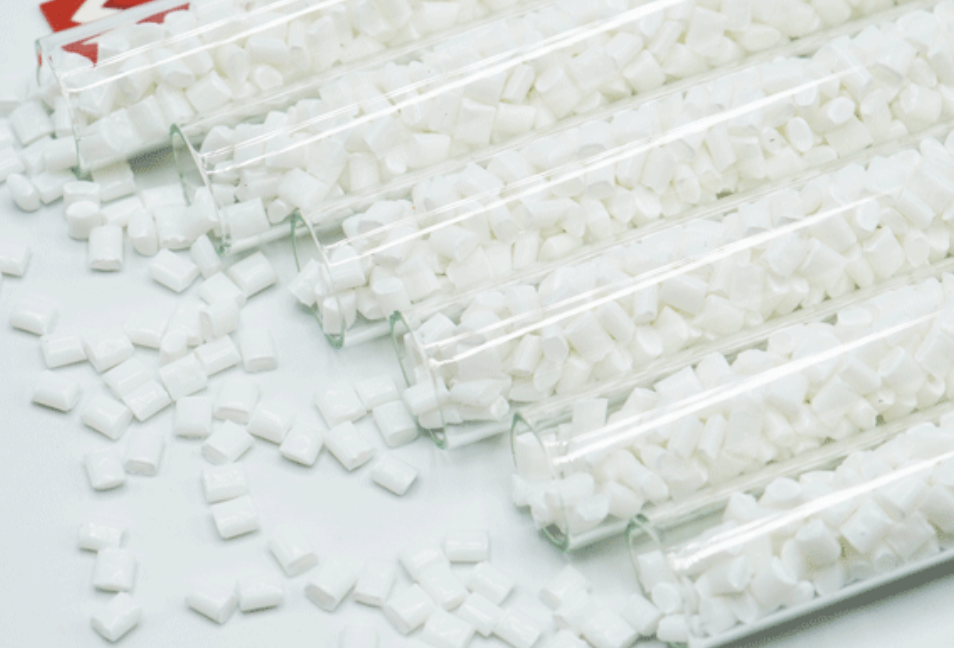
PP-Conductive is an engineering plastic composite made from PP resin and conductive carbon black as a reinforcing agent. This product is highly trusted by customers due to its high quality and cost-effectiveness.
Advantages:
- Custom design to meet specific requirements
- Improves conductivity of the final product
- Combines all features in a single raw material
- Higher stability compared to standard PP resin
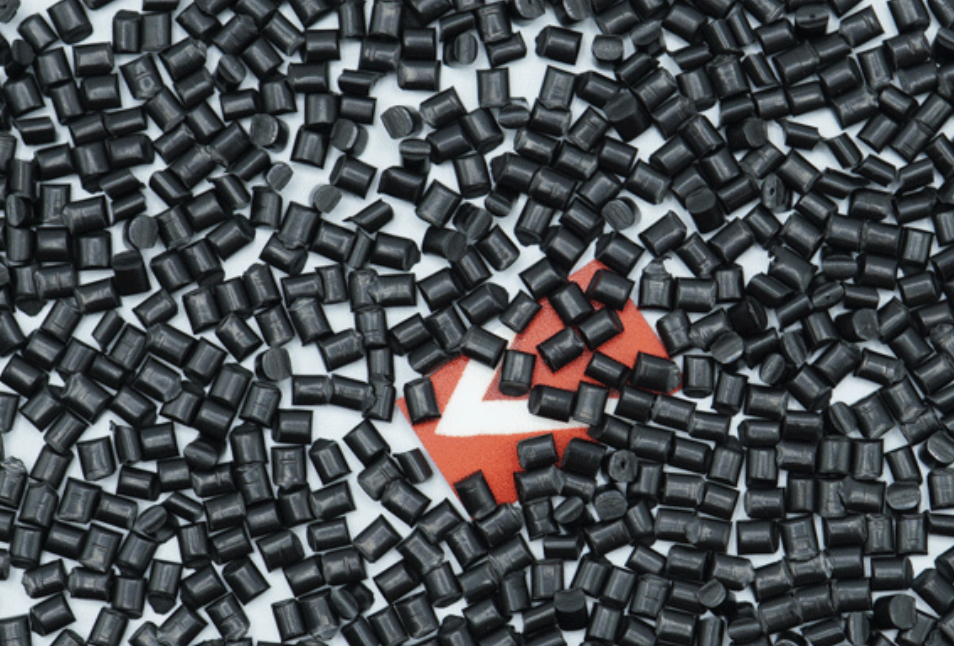
PP flame retardant compounds are blends of PP resin and halogenated/non-halogenated flame retardants. The products meet UL94: 5VA, 5VB, V0, V1, V2 flame retardancy standards and are widely used in the electrical, electronics, and construction industries.
Advantages:
- No need to add additional additives
- Limits the spread of flames
- Effective flame retardancy
- Custom design for specific products
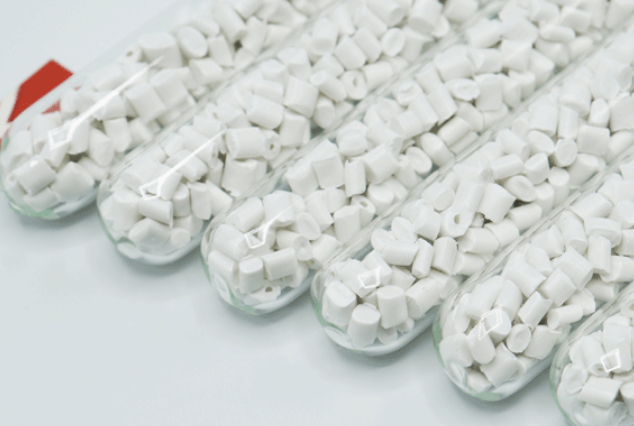
Overall, the above PP compounds are designed to meet the specific requirements of various industries. Each type has its own unique advantages, but they all share a common feature: they provide all the necessary properties of the final product in a single raw material, and can be directly processed without the need for additional blending.
Note: General specifications for all products:
- Storage: The product should be stored in a dry, cool place.
- Transportation: By road or sea, as agreed between the two parties.
3. Advantages of using EuroPlas' Compound PPs
EuroPlas' Compound PPs not only possess superior quality but also bring numerous benefits to your business, from cost savings to increased productivity. Specifically:
- Superior product quality: EuroPlas' Compound PPs are manufactured according to stringent international quality standards, ensuring high consistency and uniformity in each batch. With the ability to consistently reproduce high quality, the product fully meets the stringent technical requirements of customers, providing absolute trust for users.
- Professional services: EuroPlas' experienced technical team is always ready to provide dedicated advice and support to customers throughout the product usage process. With the ability to respond quickly and flexibly, we are committed to providing optimal solutions for all of our customers' specific requirements.
- Cost savings: Using EuroPlas' Compound PPs helps businesses save significantly on production costs by reducing the time and labor required for mixing additives. At the same time, the product also contributes to optimizing production processes and reducing the defect rate, thereby improving production efficiency.
- Stability and reliability: With many years of experience in the compound industry, EuroPlas has built a modern production system and a strict quality control process. This ensures high stability and reliability for the product, giving customers peace of mind about quality and performance.
- Comprehensive technical support: Customers will receive detailed advice from EuroPlas' technical team on selecting suitable materials, guiding processing parameters, and supporting troubleshooting during the production process. We are committed to accompanying customers throughout the product usage process.
4. Conclusion
Through this article, we have explored the outstanding Compound PPs offered by EuroPlas. With their consistent quality, diverse properties, and high customizability, EuroPlas' Compound PPs are increasingly gaining a strong foothold in the market. Let EuroPlas accompany you in creating high-quality and durable products.
5. About EuroPlas
With many years of experience in the industry, EuroPlas is proud to be a leading filler masterbatch manufacturer in Vietnam. The company possesses:
- Advanced production lines
- A team of experienced engineers
- A commitment to quality and competitive pricing
EuroPlas is always ready to accompany customers from consulting, design to production, helping to create superior quality products. Contact EuroPlas's experts today to receive detailed advice and find the most suitable solutions for your business.