In the world of plastic manufacturing, material selection directly affects product performance, production efficiency, and long-term cost. Two widely used thermoplastics are HIPS vs PP — High Impact Polystyrene and Polypropylene. Each brings distinct characteristics suited for specific industries and applications. This article provides a detailed breakdown of HIPS vs PP, comparing mechanical properties, chemical resistance, environmental performance, processing advantages, and best-use cases to help you determine which is the better fit for your needs.
1. What is HIPS (High Impact Polystyrene)?
1.1. Definition and Structure
HIPS is a modified form of polystyrene that includes rubber or polybutadiene additives to increase impact strength. It’s a rigid, opaque plastic that offers an ideal surface for printing and thermoforming.
1.2. Physical and Mechanical Properties
- Moderate tensile strength (~2,000–3,000 psi)
- Good impact resistance
- Excellent surface finish and printability
- Easy to thermoform and machine
- Melting point: ~100°C (212°F)
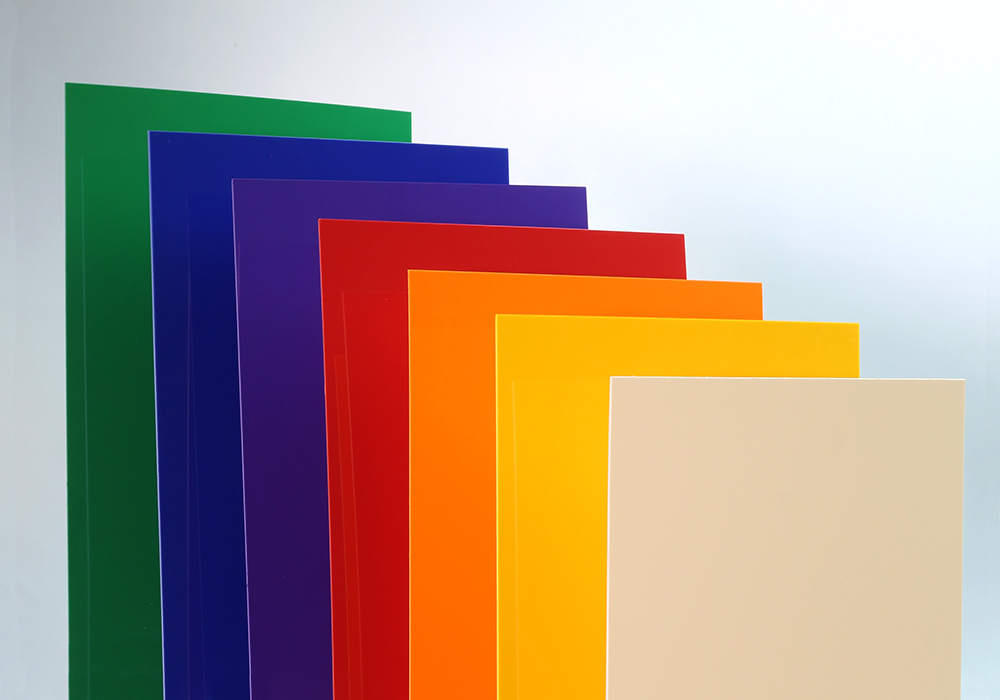
1.3. Application Areas
- Disposable food trays and cups
- Refrigerator interior liners
- Point-of-sale displays and signage
- Consumer electronics housings
HIPS is commonly chosen for consumer-facing products where visual appeal and short-term durability are required.
2. What is PP (Polypropylene)?
2.1. Definition and Composition
PP is a semi-crystalline thermoplastic derived from propylene monomer. Known for its high chemical resistance and fatigue endurance, PP is often used in applications that require durability under mechanical stress or exposure to harsh environments.
2.2. Physical and Mechanical Properties
- Higher tensile strength (~4,000–5,000 psi)
- Excellent chemical resistance
- Exceptional fatigue resistance (ideal for hinges)
- Lightweight with low density (~0.90 g/cm³)
- Melting point: ~130°C (266°F)
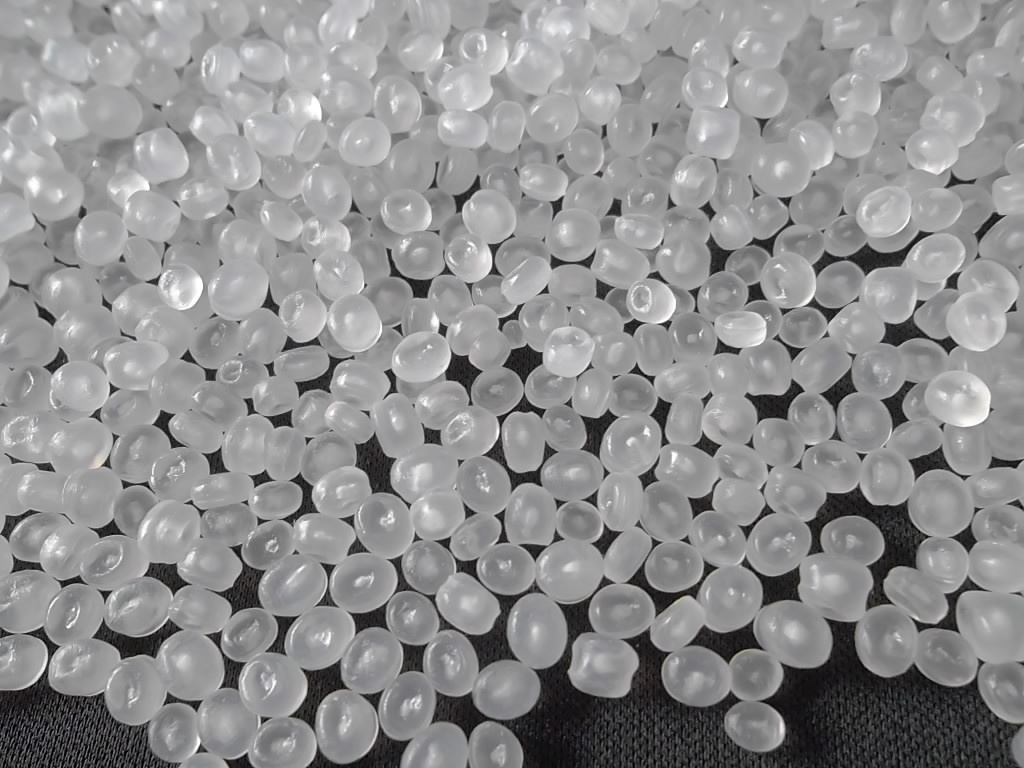
2.3. Common Applications
- Automotive components (bumpers, battery cases)
- Food storage containers
- Medical devices like syringes and IV connectors
- Pipes, fittings, and caps
PP is favored in applications requiring strength, longevity, and chemical inertness.
3. HIPS vs PP: In-Depth Comparison
Understanding the differences between HIPS vs PP requires looking at key performance metrics in real-world applications.
3.1. Mechanical Performance
- HIPS offers good impact resistance and is less likely to crack under single impacts, making it ideal for protective packaging.
- PP provides better long-term fatigue resistance, ideal for items like living hinges and flexing components.
3.2. Thermal Resistance
- PP withstands higher operating temperatures, up to 130°C, without deformation.
- HIPS performs well in moderate conditions but begins to deform around 100°C.
3.3. Chemical Resistance
- PP resists acids, bases, and most solvents, suitable for lab equipment and cleaning fluid containers.
- HIPS has limited resistance and can degrade under strong chemicals.
3.4. Moisture Resistance
- PP is nearly impervious to moisture absorption, which prevents microbial growth and deformation.
- HIPS can absorb small amounts of water over time, which may affect dimensional stability.
3.5. Surface Appearance and Aesthetics
- HIPS features a smooth, matte surface that accepts ink and coatings easily, perfect for print applications.
- PP is more difficult to print on without surface treatment, though it can be dyed or blended.
3.6. Processability
- HIPS is easier to cut, shape, and thermoform, making it popular for custom packaging and signage.
- PP is better for injection and blow molding, especially in high-volume industrial settings.
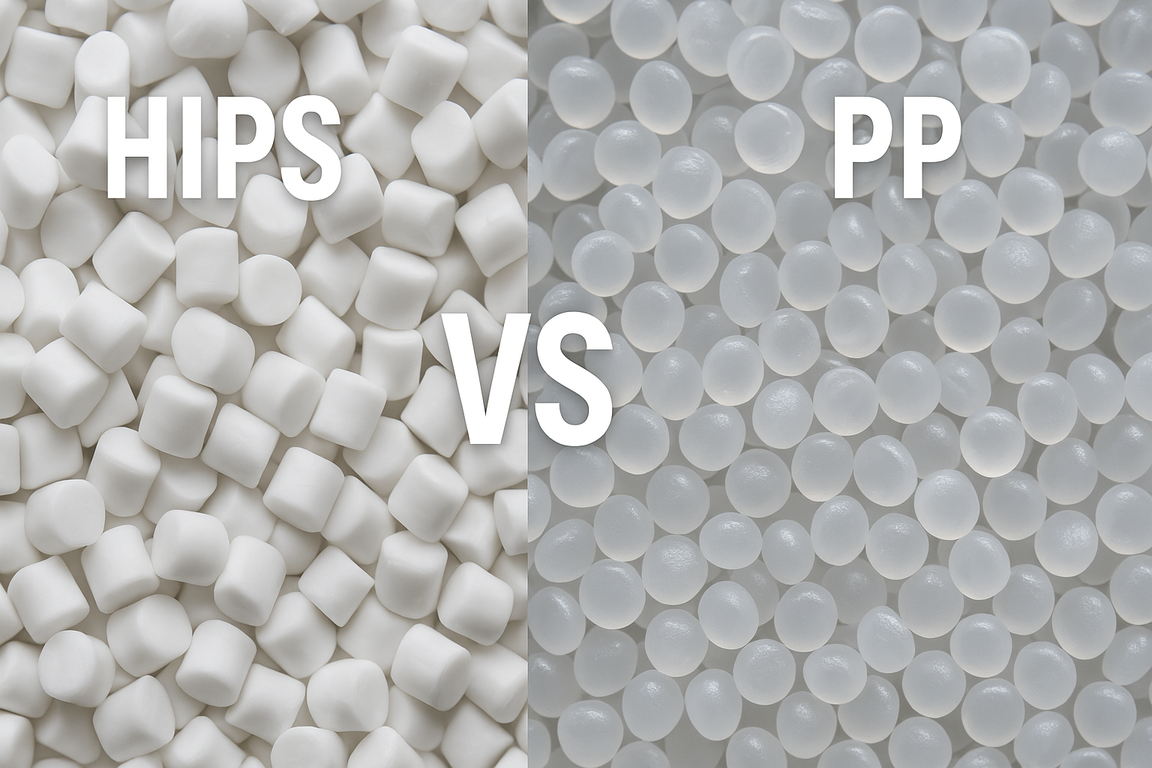
4. Environmental and Recycling Considerations
4.1. Recyclability
- PP is more widely accepted in recycling streams (resin identification code 5).
- HIPS recycling depends on local facilities and may be more limited (code 6).
4.2. Sustainability Trends
Both HIPS and PP are petroleum-based, but manufacturers are exploring bio-based alternatives and enhancing recyclability. PP has seen more commercial success in bio-derived forms.
5. Cost Efficiency in Manufacturing
When comparing HIPS vs PP on price:
- HIPS is generally lower in cost per kilogram and ideal for short-life products.
- PP may offer greater long-term value due to its superior durability and resistance.
Production cost also depends on:
- Processing method (thermoforming vs injection molding)
- Material additives (UV stabilizers, colorants)
- Volume of production
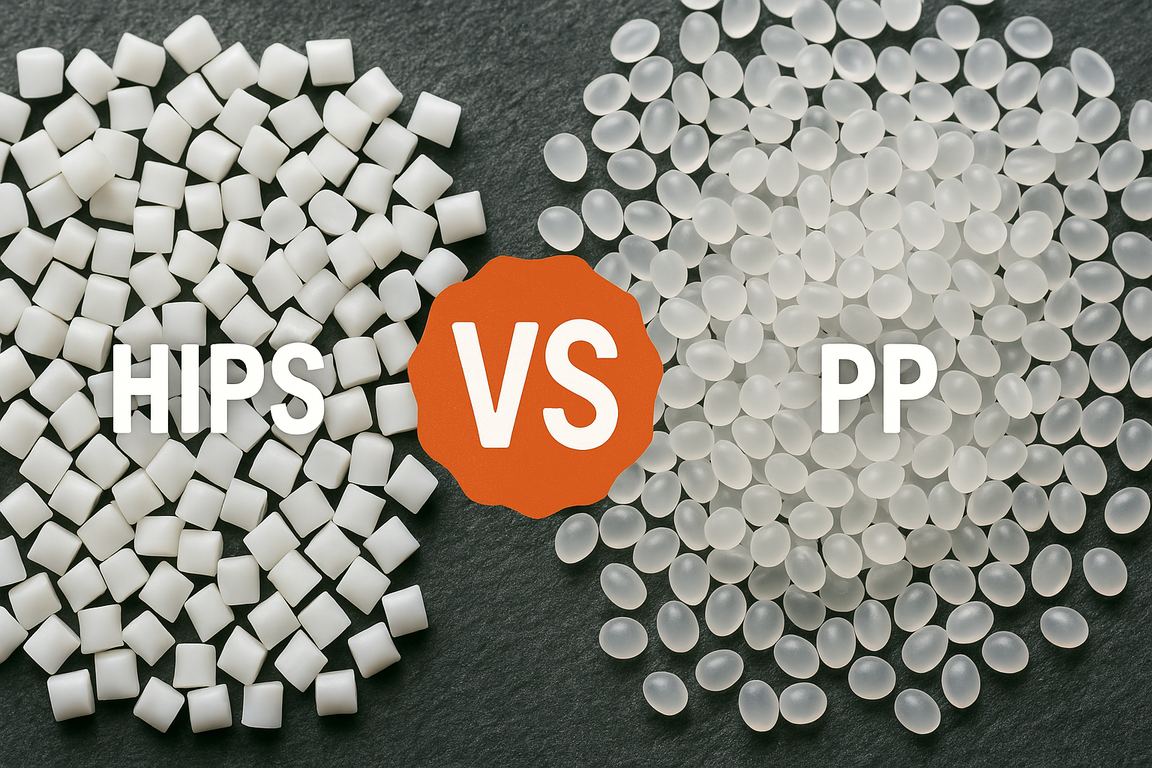
6. Choosing Between HIPS vs PP: Key Considerations
6.1. Choose HIPS If:
- Your product requires high-quality print finishes
- You’re making lightweight, short-term consumer goods
- Thermoforming or vacuum forming is your primary process
6.2. Choose PP If:
- Your product must resist chemical exposure or heat
- It will undergo repetitive motion or flexing
- Long-term strength and reliability are critical
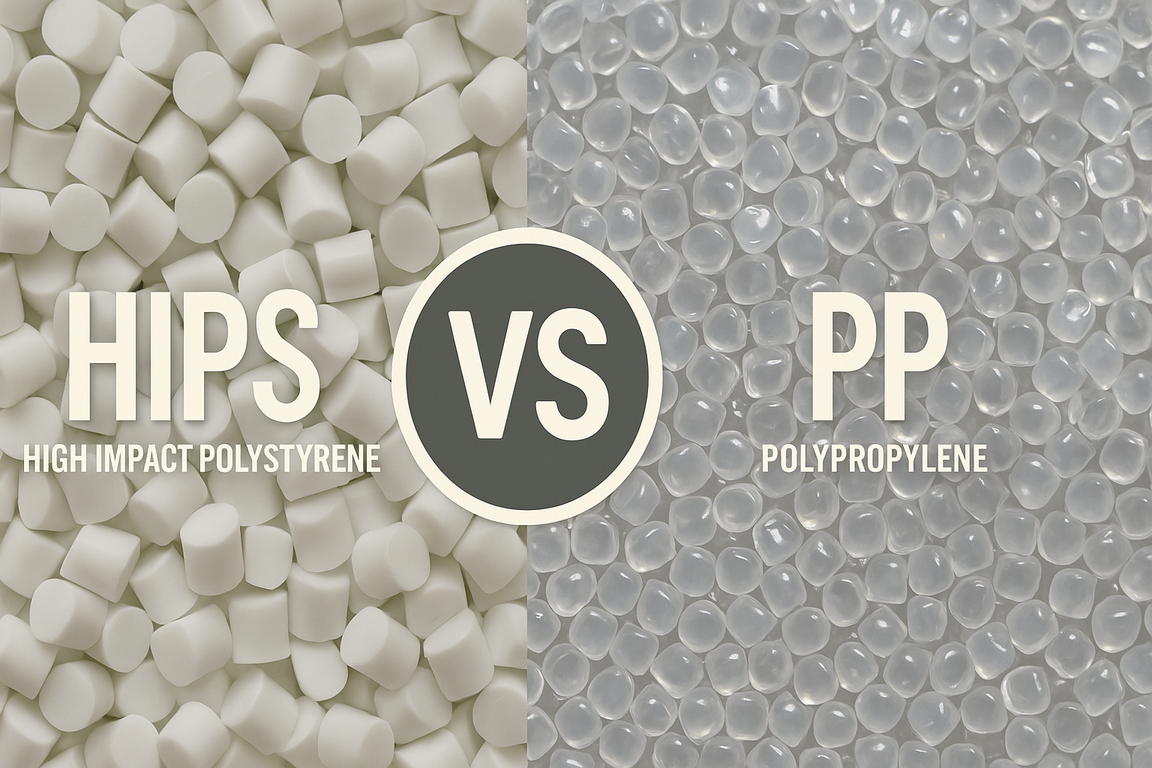
7. Conclusion
The comparison of HIPS vs PP reveals two materials with distinct profiles. HIPS is better suited for short-term, aesthetically focused, and easily formable applications. PP excels in chemical resistance, long-term fatigue performance, and environmental exposure.
Ultimately, your choice between HIPS vs PP should align with end-use requirements, processing methods, and lifecycle goals. By understanding their differences, manufacturers can make cost-effective and performance-driven decisions for every application.
8. About EuroPlas
EuroPlas is a global leader in the production of plastic filler masterbatch, serving over 95 countries worldwide. Backed by advanced R&D and modern production facilities, EuroPlas offers tailor-made solutions that optimize both performance and cost-efficiency.
For businesses working with HIPS, EuroPlas provides a high-quality HIPS filler masterbatch that improves stiffness, printability, and dimensional stability while reducing production costs. It is ideal for thermoforming and vacuum-forming processes used in packaging and appliance industries.
For those focused on PP applications, the company’s PP filler masterbatch enhances mechanical strength, thermal resistance, and overall material efficiency in extrusion and injection molding.
With a strong reputation for innovation, quality, and customer satisfaction, EuroPlas remains a trusted partner for manufacturers seeking to improve their plastic products using HIPS and PP materials.