Black polypropylene has emerged as a game-changing material in automotive manufacturing, offering exceptional durability, cost-effectiveness, and environmental benefits that are transforming vehicle production across the industry.
1. Introduction to Black Polypropylene in Automotive Applications
The automotive industry constantly seeks innovative materials that can withstand demanding conditions while reducing vehicle weight and manufacturing costs. Black polypropylene has emerged as a standout solution, increasingly replacing traditional materials in various vehicle components. This versatile plastic has revolutionized how manufacturers approach vehicle design and production.
Black polypropylene, a thermoplastic polymer, offers a unique combination of properties that make it particularly valuable for automotive applications. Its popularity stems from exceptional durability, chemical resistance, and cost-effectiveness compared to alternative materials. As automakers face mounting pressure to improve fuel efficiency and reduce environmental impact, lightweight yet strong materials like black polypropylene have become essential components in modern vehicle manufacturing.
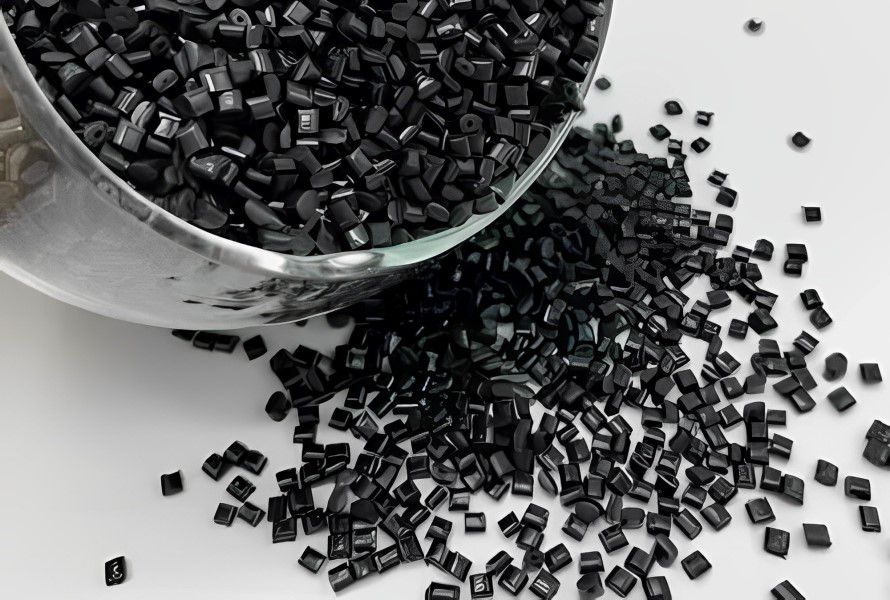
Black polypropylene, a thermoplastic polymer, offers a unique combination of properties that make it particularly valuable for automotive applications.
2. Physical Properties That Make Black Polypropylene Ideal for Vehicles
2.1. Weather and UV Resistance
One of the most significant advantages of black polypropylene in automotive applications is its excellent weather resistance. The carbon black additives that create its distinctive color also provide superior protection against ultraviolet (UV) radiation. This protection prevents degradation, cracking, and fading that can occur with prolonged exposure to sunlight, making it ideal for both exterior and interior components.
2.2. Temperature Stability and Impact Resistance
Black polypropylene maintains its structural integrity across a wide temperature range, from the freezing conditions of winter to the intense heat of summer. This temperature stability ensures that components don't become brittle in cold weather or deform in high temperatures. Additionally, when compared to standard polypropylene, the modified versions used in automotive applications offer enhanced impact resistance, which is crucial for parts that may experience mechanical stress or collision forces.
2.3. Lightweight Construction
Vehicle weight directly impacts fuel consumption and emissions. Black polypropylene's low density provides significant weight savings compared to metal alternatives without compromising structural integrity. This weight reduction contributes to improved fuel efficiency and reduced carbon emissions, aligning with increasingly stringent environmental regulations facing automakers worldwide.
3. Common Applications in Modern Vehicles
3.1. Interior Components
The versatility of black polypropylene makes it ideal for numerous interior applications. Dashboard components, door panels, center consoles, and trim pieces commonly utilize this material. Its ability to be molded into complex shapes while maintaining consistent color and texture has made it a preferred choice for interior designers. Also, black polypropylene offers superior durability for frequently touched or stressed components.
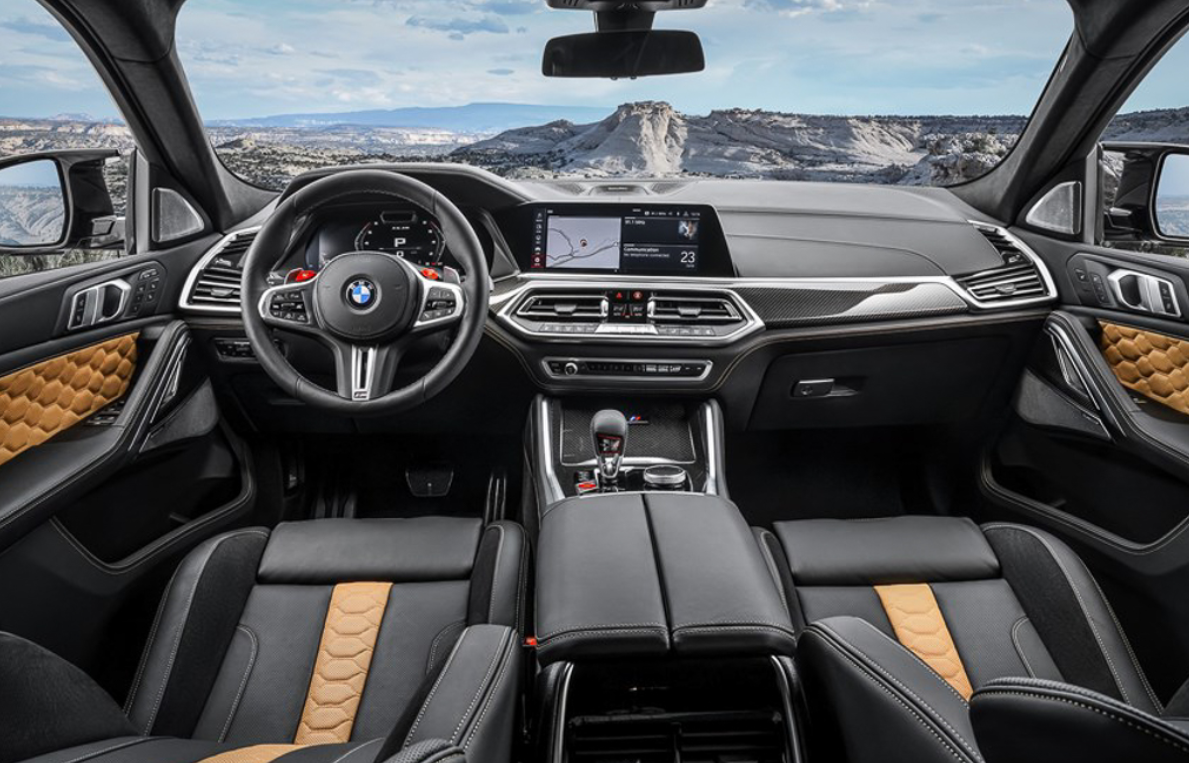
The versatility of black polypropylene makes it ideal for numerous interior applications.
3.2. Exterior Applications
Bumpers, wheel well liners, and exterior trim increasingly incorporate black polypropylene. Its resistance to road chemicals, salt, and environmental contaminants ensures these parts maintain their appearance and functionality throughout the vehicle's lifespan. The material's impact resistance also makes it suitable for components that may encounter road debris or minor collisions.
3.3. Under-Hood Components
The engine compartment presents particularly challenging conditions for materials, with extreme temperature fluctuations and exposure to various automotive fluids. Black polypropylene's chemical resistance and thermal stability make it appropriate for fluid reservoirs, air intake components, and battery cases.
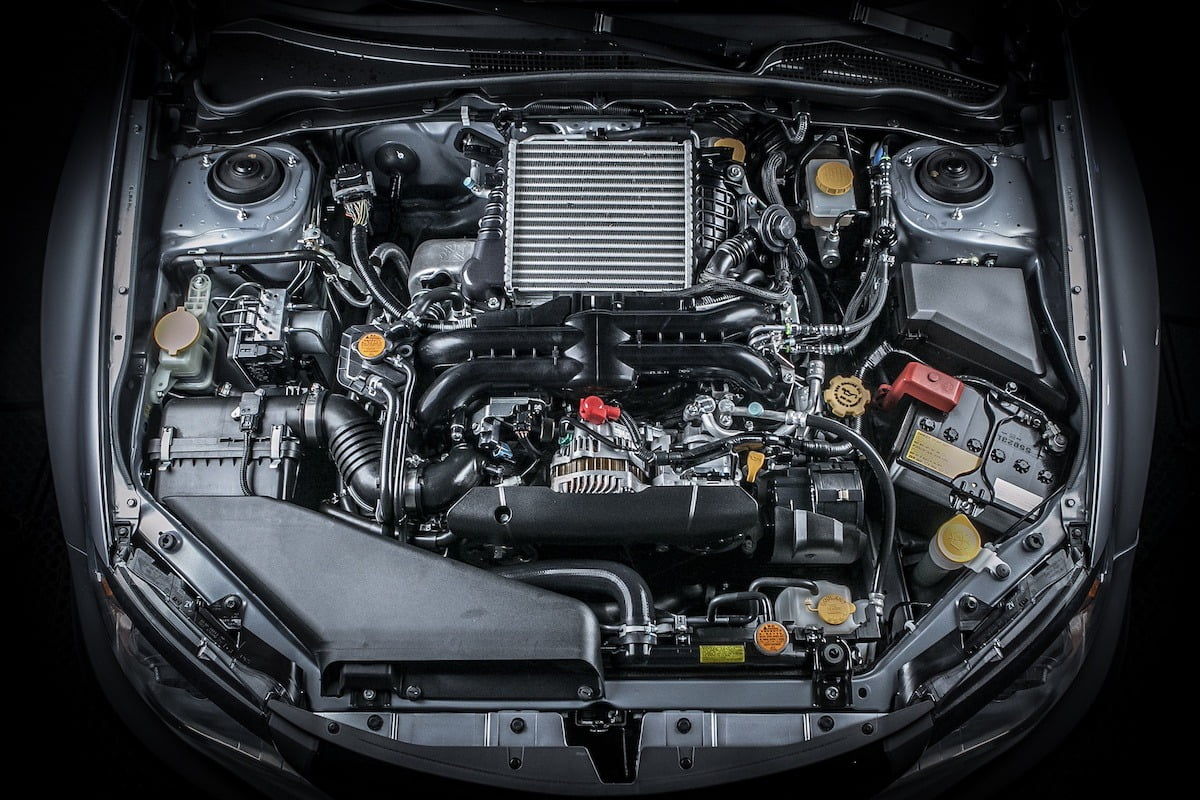
Black polypropylene's chemical resistance and thermal stability make it appropriate for under-hood components.
4. Manufacturing Advantages
4.1. Production Efficiency
Black polypropylene offers significant manufacturing advantages through its excellent flow properties during injection molding. This characteristic allows for faster production cycles and more consistent part quality compared to other materials. Additionally, the material requires lower processing temperatures than alternatives like high impact polystyrene, reducing energy consumption during manufacturing.
4.2. Design Flexibility
The material's moldability enables complex component designs that would be difficult or impossible to achieve with metal alternatives. This design flexibility allows engineers to consolidate multiple parts into single components, reducing assembly complexity and potential failure points. The material can also be easily textured during the molding process, eliminating the need for secondary finishing operations.
4.3. Cost Effectiveness
Black polypropylene delivers substantial cost savings throughout the manufacturing process. Its lower material cost compared to metals and some competing plastics provides immediate savings. The reduced energy requirements during processing and faster production cycles further enhance its economic advantages. Additionally, the elimination of painting or coating processes often required with high impact polystyrene components contributes to overall cost reduction.
.jpg)
Black polypropylene delivers substantial cost savings throughout the manufacturing process.
5. Environmental Benefits
5.1. Reduced Carbon Footprint
The lightweight nature of black polypropylene directly contributes to improved fuel efficiency and reduced vehicle emissions over its operational lifetime. Additionally, the manufacturing process typically requires less energy than producing metal components, further reducing the carbon footprint of vehicle production.
5.2. Recyclability Factors
Unlike some composite materials, black polypropylene can be recycled at the end of a vehicle's life. Modern recycling techniques can process this material for reuse in non-automotive applications, reducing waste and conserving resources. Typically, polypropylene maintains better mechanical properties through multiple recycling cycles.
5.3. Sustainable Manufacturing Practices
The automotive industry's shift toward more sustainable manufacturing aligns perfectly with black polypropylene's attributes. Its production generates fewer harmful emissions compared to some alternative materials, and its durability ensures longer component lifespans, reducing the frequency of replacements and subsequent resource consumption.
6. Comparison with Traditional Materials
6.1. Advantages Over Metal Components
When compared to traditional metal components, black polypropylene offers significant weight reduction, superior corrosion resistance, and greater design flexibility. While metals may provide greater strength in some applications, engineered grades of polypropylene deliver sufficient performance for many automotive components at a fraction of the weight and cost.
6.2. Benefits Compared to Other Plastics
Black polypropylene outperforms many other automotive plastics in several key areas. Its superior chemical resistance, temperature stability, and weather durability make it more suitable for demanding automotive applications than alternatives like ABS or standard polystyrene. The carbon black additives also provide intrinsic UV protection that many other plastics lack without additional stabilizers.
7. Future Trends and Innovations
The future of black polypropylene in automotive applications looks promising as manufacturers continue to develop enhanced formulations with improved mechanical properties. Research into nano-reinforced variants shows potential for even greater strength-to-weight ratios. Additionally, bio-based polypropylene formulations derived from renewable resources represent an emerging trend that could further reduce the environmental impact of vehicle production.
As electric vehicles gain market share, the demand for lightweight, durable materials like black polypropylene will likely increase. The material's excellent electrical insulation properties and resistance to battery chemicals make it particularly valuable in EV applications. Innovations in polypropylene blends may also create new hybrid materials that combine the best properties of both for specialized automotive applications.
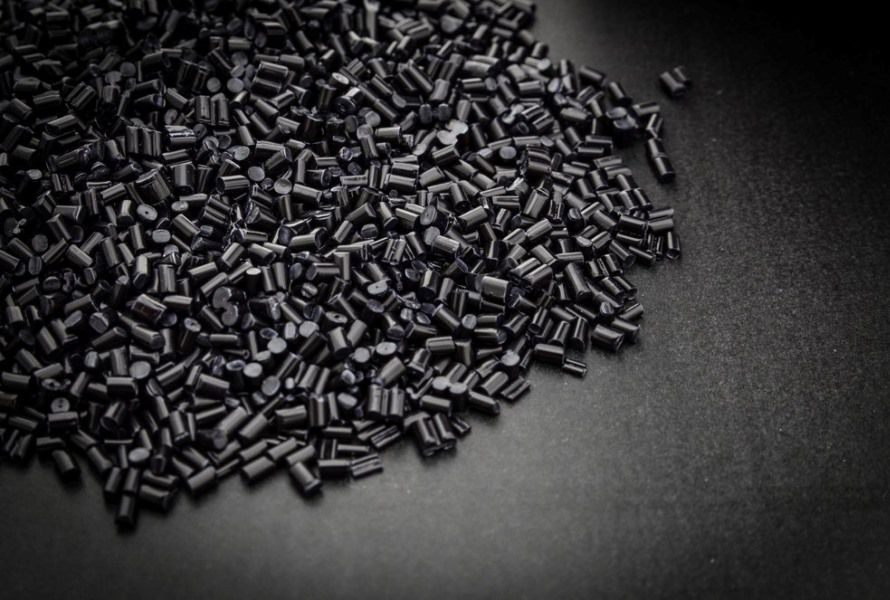
The future of black polypropylene in automotive applications looks promising.
8. Conclusion
Black polypropylene has established itself as an essential material in modern automotive manufacturing. Its unique combination of physical properties, manufacturing advantages, and environmental benefits continues to drive its adoption across numerous vehicle systems. As the automotive industry evolves to meet new challenges in sustainability, performance, and cost-effectiveness, black polypropylene will undoubtedly remain a key material in vehicle design and production strategies.
9. About EuroPlas
European Plastic Company is currently the world's largest supplier of filler masterbatch with a capacity of 800,000 tons/year, and has been present in over 95 countries. Especially, PP products of EuroPlas are the solution to optimize costs and improve product features for enterprises producing plastic-finished products. During 18 years of development, we are always confident in our commitment to the quality of our products and services.
For more information, please fill out the form or contact us directly via email/phone number.