Want to improve your blown film production while cutting costs? CaCO₃ masterbatch is the secret ingredient! By integrating calcium carbonate into plastic formulations, manufacturers achieve stronger, more cost-effective films. Whether you're aiming for durability, smooth processing, or cost savings, this article will reveal how CaCO₃ masterbatch transforms the blown film industry, outlining its key benefits and essential tips to optimize your production process.
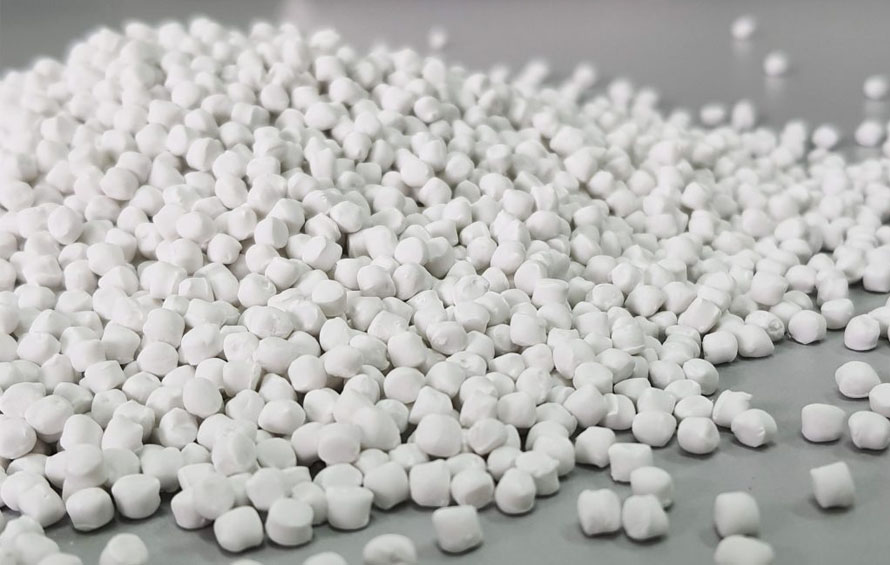
Boost blown film strength and cut costs with CaCO₃ masterbatch—enhancing durability and efficiency.
1. Importance of CaCO3 Masterbatch
1.1. What is CaCO₃ Filler Masterbatch?
CaCO₃ filler masterbatch is a concentrated mixture that made from calcium carbonate (CaCO₃), polymer resin and other additives. This masterbatch serves as a cost-effective solution to enhance the properties of plastic products by incorporating a high volume of filler material, primarily composed of finely ground calcium carbonate particles. The resulting masterbatch is then blended with the primary polymer during the production process, such as extrusion or injection molding, to create plastic products.
1.2. Role of CaCO₃ Masterbatch in the Plastic Industry
The primary function of CaCO₃ masterbatch is to reduce the overall cost of plastic products by replacing part of the polymer with inexpensive calcium carbonate. This helps reduce material costs while maintaining or even improving certain physical properties, such as rigidity, opacity, and dimensional stability. Additionally, the use of CaCO₃ in plastic products can enhance their surface finish, giving them a smoother appearance.
Calcium carbonate is naturally abundant, environmentally friendly, and provides several benefits when used in plastic applications, making it a popular choice for various industries, including packaging, automotive, and consumer goods. Furthermore, this filler masterbatch can improve the processing properties of the polymer, such as reducing melt viscosity, aiding in smoother flow during molding, and enhancing overall productivity.
CaCO₃ filler masterbatch is also used in applications where non-toxic and low environmental impact materials are required, such as food packaging and medical products.
1.3. Applications of CaCO₃ Filler Masterbatch in Blown Film
CaCO₃ filler masterbatch is extensively utilized in the blown film industry that span various sectors, each benefiting from its unique properties.
Packaging Films
In the production of packaging materials such as supermarket bags, garbage bags, and T-shirt bags, incorporating CaCO₃ masterbatch improves film stiffness and printability. This enhancement leads to better product quality and cost efficiency.
Agricultural Films
For agricultural applications, including mulch films and greenhouse covers, CaCO₃ filler masterbatch increases the mechanical strength of the films. This improvement results in more durable products that can withstand environmental stresses, thereby extending their functional lifespan.
Food Packaging
In food packaging, the use of CaCO₃ filler masterbatch enhances the stability of the manufacturing process and improves the physical properties of the final product. These benefits are crucial for maintaining the integrity and safety of packaged food items.
Medical industry
CaCO₃ filler masterbatch improves the mechanical strength, opacity, and barrier properties of plastic films used in medical packaging, such as IV bags, blister packs, and sterile wrap films. These enhancements help protect medical equipment and pharmaceutical products from contamination and external damage.
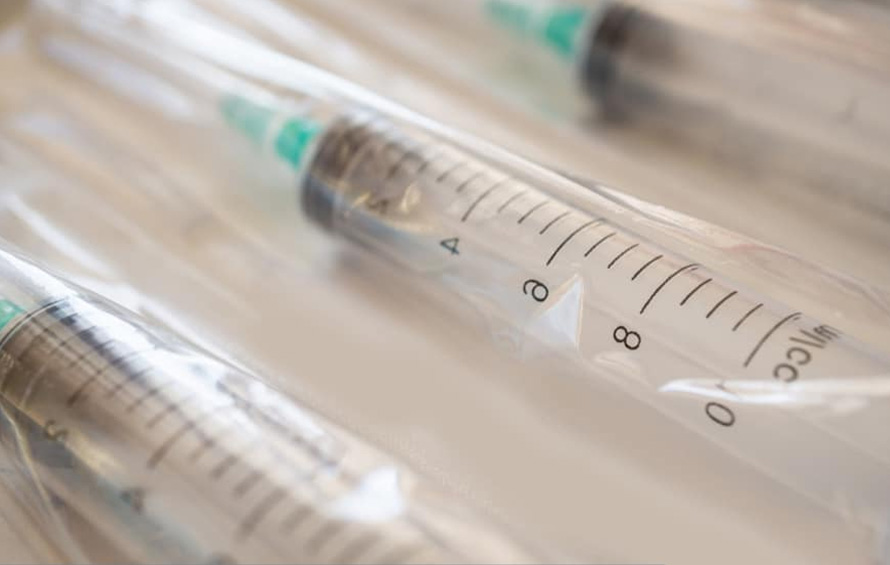
CaCO₃ filler masterbatch enhances the mechanical strength and barrier properties of plastic films used in medical packaging
By integrating CaCO₃ filler masterbatch into blown film production, manufacturers can achieve significant improvements in product quality and operational efficiency across these diverse applications.
2. Benefits of Using CaCO₃ Masterbatch in Blown Film
Incorporating CaCO₃ (calcium carbonate) masterbatch into blown film production offers several notable benefits:
- Cost Reduction: By substituting a portion of the primary polymer with CaCO₃ filler, manufacturers can significantly lower material expenses. This substitution not only reduces reliance on more costly virgin polymers but also enhances the overall economic efficiency of the production process.
- Enhanced Physical Properties: The addition of CaCO₃ masterbatch improves the mechanical characteristics of blown films. Notably, it increases stiffness, which is beneficial for products requiring enhanced rigidity. Additionally, CaCO₃ acts as an anti-block agent, facilitating better handling and processing of the films.
- Increased Productivity: CaCO₃'s superior thermal conductivity allows for faster heat transfer during the extrusion process, leading to increased volumetric output. This efficiency enables manufacturers to produce more film in less time, thereby boosting overall productivity.
- Energy Efficiency: The presence of CaCO₃ in the polymer matrix can lead to reduced energy consumption during processing. This reduction is attributed to the improved thermal properties of the compound, which facilitate easier processing and lower energy requirements.
- Improved Printability and Surface Finish: Films containing CaCO₃ masterbatch exhibit enhanced surface properties, resulting in better printability. This improvement is particularly advantageous for packaging applications where high-quality printing is essential.
By leveraging these benefits, manufacturers can optimize their blown film production processes, achieving cost savings, improved product quality, and increased operational efficiency.
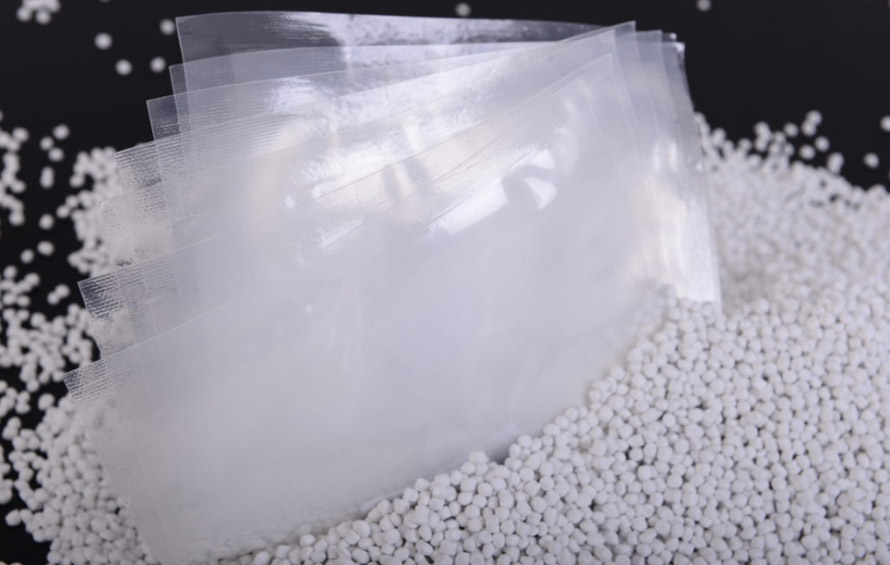
CaCO₃ masterbatch cuts costs, boosts strength, enhances processing, improves printability, and increases productivity for blown film production.
3. Key Considerations When Using CaCO₃ Masterbatch
When incorporating calcium carbonate (CaCO₃) masterbatch into plastic production, it's essential to consider several factors to ensure optimal performance and product quality:
- Filler Ratio: Determining the appropriate proportion of CaCO₃ in the masterbatch is crucial. While higher filler content can reduce material costs, excessive amounts may adversely affect the mechanical properties of the final product, such as impact strength.
- Particle Size and Distribution: The particle size of CaCO₃ influences the surface finish and mechanical properties of the plastic. Fine particles can enhance the smoothness and gloss of the product, while uniform distribution ensures consistent quality.
- Compatibility with Polymers: Ensuring that the CaCO₃ masterbatch is compatible with the base polymer is vital. Incompatibility can lead to poor dispersion, affecting the appearance and structural integrity of the final product.
- Processing Conditions: Adjustments in processing parameters, such as temperature and screw speed, may be necessary when using CaCO₃ masterbatch. Proper calibration ensures optimal dispersion and prevents issues like die build-up during extrusion.
- End-Use Application: Consider the intended application of the plastic product. For instance, products requiring high impact resistance may need lower CaCO₃ content, while non-structural applications can accommodate higher filler levels.
- Regulatory Compliance: Ensure that the CaCO₃ masterbatch complies with industry standards and regulations, especially for applications involving food contact or medical devices.
By carefully evaluating these factors, manufacturers can effectively utilize CaCO₃ masterbatch to enhance product performance, reduce costs, and maintain high-quality standards.
4. Conclusion
In summary, the integration of CaCO₃ masterbatch into the blown film industry has proven to be a transformative advancement. By partially substituting virgin polymers with calcium carbonate, manufacturers can significantly reduce production costs while enhancing the mechanical properties of the films, such as increased stiffness and improved printability.
This approach not only promotes economic efficiency but also contributes to environmental sustainability by decreasing reliance on pure plastic resins. As the industry continues to evolve, the strategic application of CaCO₃ filler masterbatch stands out as a key factor in producing high-quality, cost-effective, and eco-friendly blown film products.
5. About EuroPlas’ Filler Masterbatch
EuroPlas, established in 2007, has rapidly ascended to become the world's leading manufacturer of filler masterbatch, offering innovative plastic material solutions to enhance production efficiency and product quality.
A flagship product of EuroPlas is the CaCO₃ filler masterbatch, a composite of calcium carbonate, plastic resin beads, and specific additives tailored to customer requirements. This masterbatch is extensively utilized in the blown film industry to improve film properties and reduce production costs.
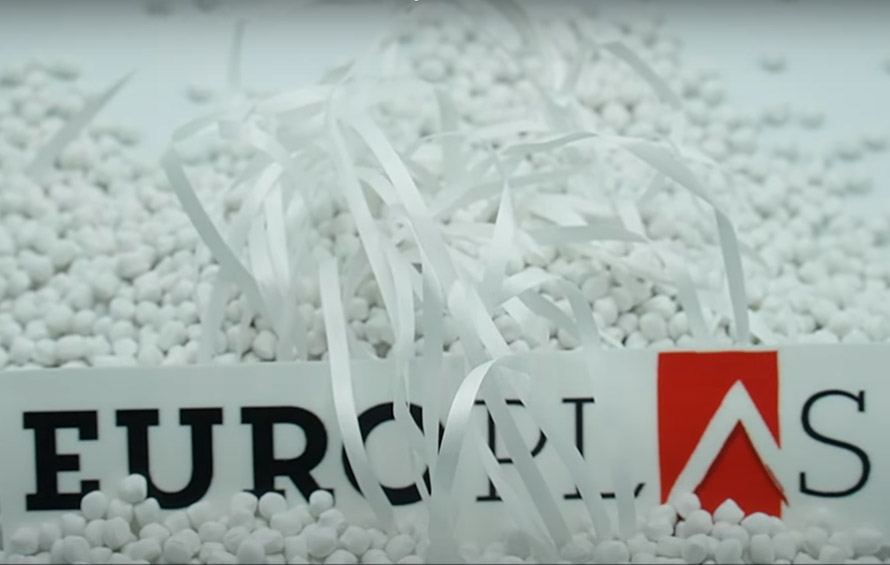
EuroPlas leads in CaCO₃ filler masterbatch, enhancing film quality, efficiency, and sustainability globally.
EuroPlas' commitment to quality and innovation ensures that our filler masterbatch not only meets industry standards but also provides customizable solutions to meet specific client needs. By integrating our masterbatch into blown film production, manufacturers can achieve superior product performance, cost savings, and environmental sustainability.
For more information or to discuss how EuroPlas' CaCO₃ masterbatch can benefit your production processes, please contact us at info@europlas.com.vn