The injection molding process is one of the most versatile and widely used manufacturing methods in the modern world. It has revolutionized the production of plastic components, enabling the creation of complex, high-quality parts at an impressive scale and cost efficiency. From the simplest household items to advanced industrial components, injection molding drives innovation in numerous industries.
In this guide, we will explore the injection molding process in detail, examining its fundamental principles, the profound influence it has on product outcomes, the factors that contribute to its success, and the role of global leaders like EuroPlas in advancing this essential technology.
1. Overview of the Injection Molding Process
Injection molding is a high-precision manufacturing technique used to create plastic parts by injecting molten plastic material into a pre-designed mold. The process comprises several crucial stages that collectively ensure accuracy and consistency:
The raw plastic material, usually in the form of granules or pellets, is fed into the injection molding machine’s hopper. From there, it enters a heated barrel where it is melted into a viscous fluid. Additives, such as colorants or filler compounds, can be mixed in at this stage to enhance specific properties of the material.
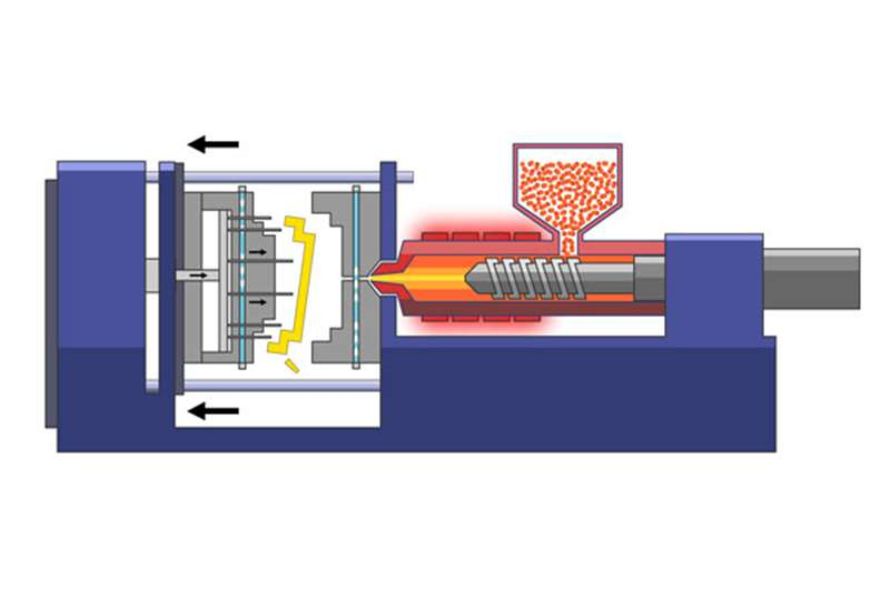
Injection Molding involves several steps to transform raw materials into finished products
Once melted, the plastic is injected into a custom-designed mold cavity under high pressure. The mold can have a single cavity or multiple cavities for mass production, depending on the requirements. The molten plastic cools and solidifies inside the mold. The cooling process must be carefully controlled to prevent warping, shrinkage, or surface imperfections.
After the plastic solidifies, the mold opens, and the final product is ejected using ejector pins. The product is then trimmed, inspected, and prepared for packaging or further processing. Excess material, such as sprues or runners, can often be recycled and reused in subsequent production cycles, minimizing waste and enhancing cost efficiency.
This method has become the backbone of industries such as automotive, electronics, healthcare, and consumer goods due to its ability to produce high-precision components in large quantities with consistent quality.
2. Influence of the Injection Molding Process on Products
The injection molding process plays a pivotal role in determining the performance, durability, aesthetics, and functionality of the products it creates. Here is a closer look at how this manufacturing method influences various product attributes:
2.1. Dimensional Precision
Injection molding ensures unparalleled dimensional accuracy, making it indispensable for applications that demand tight tolerances. For example:
Medical Devices: Components like syringes and surgical tools require micrometer-level precision to ensure safety and effectiveness.
Automotive Parts: Critical components such as dashboards, connectors, and housings depend on exact specifications to integrate seamlessly with larger systems.
This precision reduces the need for post-processing, minimizing production time and cost.
2.2. Material Versatility
The ability to use a wide variety of materials is a key strength of the injection molding process. Manufacturers can select materials based on:
Mechanical Strength: Materials like polycarbonate are used for high-stress applications.
Flexibility: Polypropylene is ideal for items like living hinges or containers.
Temperature Resistance: Nylon and PEEK are chosen for parts exposed to high temperatures.
This versatility enables manufacturers to meet diverse requirements across industries, including automotive, aerospace, consumer goods, and healthcare.
2.3. Surface Finish and Aesthetics
Injection molding molds can be crafted to impart specific surface textures or finishes to products, eliminating the need for secondary operations like polishing or painting. Examples include:
Glossy Finishes: Found in electronic device casings for aesthetic appeal.
Matte Textures: Preferred in automotive interiors to reduce glare.
Detailed Patterns: Logos, text, or intricate designs can be incorporated directly into the mold.
The ability to customize the surface finish ensures products are both functional and visually appealing.
2.4. Structural Integrity and Durability
The injection molding process ensures uniform material distribution, which significantly enhances the structural integrity of the product. Key benefits include:
Resistance to Stress: Optimized cooling processes prevent weak spots or residual stresses in the part.
Durability: Proper material choice and molding conditions result in products that withstand wear, impacts, and environmental factors.
2.5. Cost-Efficiency in Mass Production
While the upfront cost of mold creation can be high, injection molding proves economical for large-scale production runs. Examples include:
Consumer Goods: Millions of identical items, such as water bottle caps, can be produced efficiently.
Industrial Components: Uniform parts for machinery, reducing variability and ensuring consistency in assembly.
The scalability of injection molding supports the production of both high-volume and complex multi-component assemblies.
2.6. Environmental Impact
With advancements in sustainable materials, such as bioplastics, and efficient processes, injection molding is increasingly environmentally friendly. Recyclable waste like sprues and runners further reduces the ecological footprint.
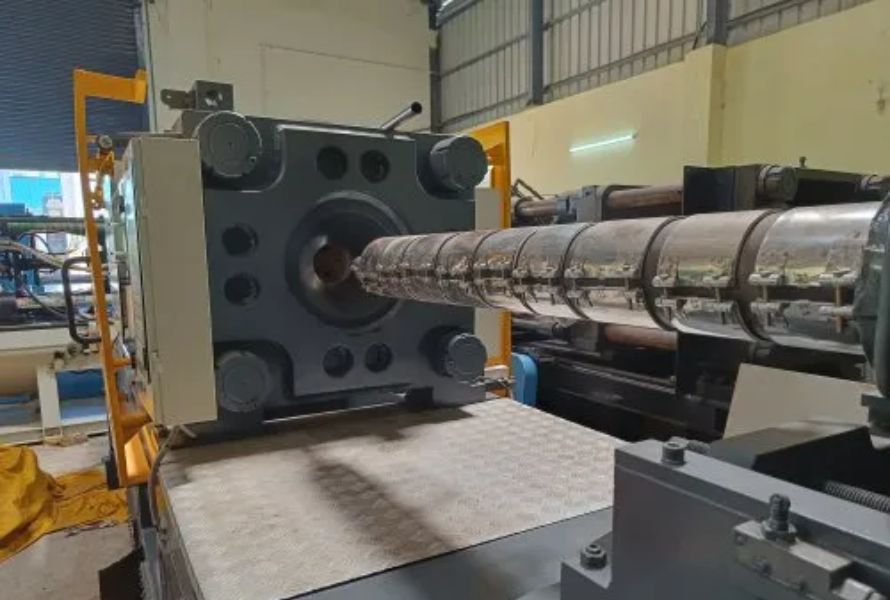
Each component in the injection molding process plays a critical role
3. What Are Factors Influencing Injection Molding Processes?
Several factors determine the success of the injection molding process. Understanding and managing these factors ensures the production of high-quality parts with minimal defects.
3.1. Material Selection
The choice of material directly impacts product quality and process efficiency. Critical considerations include:
Melt Flow Index (MFI): Higher MFI materials flow easily into intricate molds but may compromise strength.
Additives: Reinforcements like glass fibers enhance strength, while UV stabilizers improve outdoor durability.
Application Requirements: For example, food-grade plastics like HDPE are necessary for packaging, while flame-retardant plastics are essential in electronics.
3.2. Mold Design
An effective mold design is foundational to the process. Key aspects include:
Gate Placement: Proper gate locations ensure uniform filling and prevent defects like sink marks or voids.
Venting: Air trapped during injection must be expelled to avoid incomplete fills or burn marks.
Shrinkage Allowance: Mold dimensions must account for material shrinkage during cooling to maintain precision.
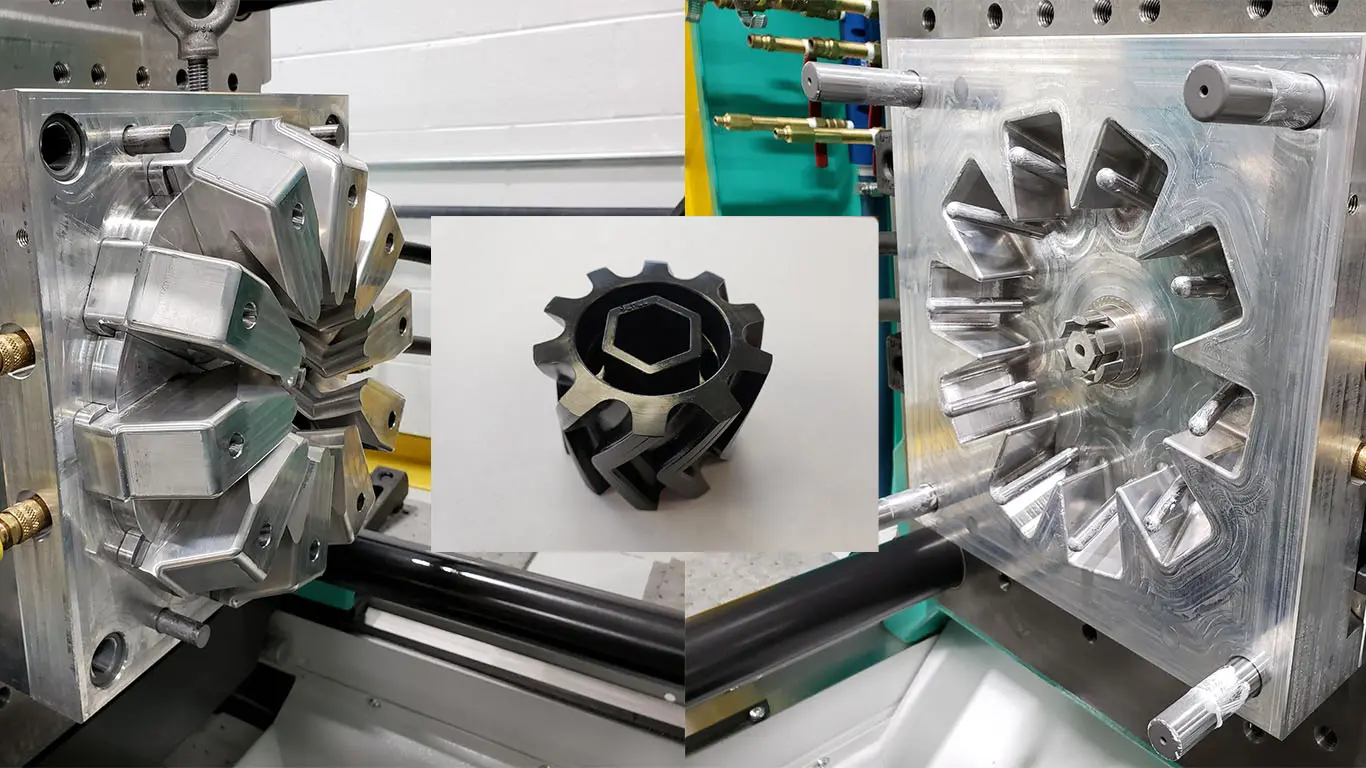
Mold design for injection molding process
3.3. Machine Settings and Processing Parameters
Injection molding machines must be carefully calibrated to optimize performance. Essential parameters include:
Injection Pressure: Sufficient pressure ensures the material fills the mold cavity completely, avoiding short shots.
Melt Temperature: Proper temperature prevents material degradation and ensures smooth flow. Overheating, however, may cause discoloration or structural weakness.
Cooling Time: Adequate cooling prevents warping but should not be excessive to avoid increasing cycle times unnecessarily.
3.4. Mold and Machine Maintenance
Regular maintenance is essential to avoid downtime and defects. Maintenance activities include:
Cleaning: Residual material or buildup in molds can cause imperfections or dimensional inaccuracies.
Lubrication: Ensures moving parts operate smoothly and reduces wear.
Inspection: Identifying wear or damage in molds and machines prevents production delays.
.png)
Mold maintenance for injection molding process
3.5. External Environmental Factors
Production conditions such as temperature, humidity, and cleanliness can subtly impact the process:
Temperature: Fluctuations can affect the cooling rate, leading to inconsistent shrinkage.
Dust and Contaminants: These can interfere with mold surfaces, leading to defects or variations in surface quality.
3.6. Cycle Time Optimization
Reducing the cycle time without compromising quality is a critical goal in injection molding. Efficient cycle times involve:
Faster Cooling Rates: Achieved through optimized cooling channel designs and advanced mold materials.
Automation: Robotic systems can accelerate part removal and secondary operations like trimming.
3.7. Technological Innovations
Advanced injection molding machines and techniques further enhance efficiency and precision. These include:
Multi-Material Injection Molding: Allows the combination of different materials in a single product, such as hard plastic with soft-touch rubber grips.
Gas-Assisted Injection Molding: Reduces material usage and weight while maintaining strength.
Real-Time Monitoring Systems: Ensure consistent quality by detecting and correcting errors during the molding process.
By understanding and controlling these factors, manufacturers can fully utilize the capabilities of the injection molding process to produce superior products efficiently.
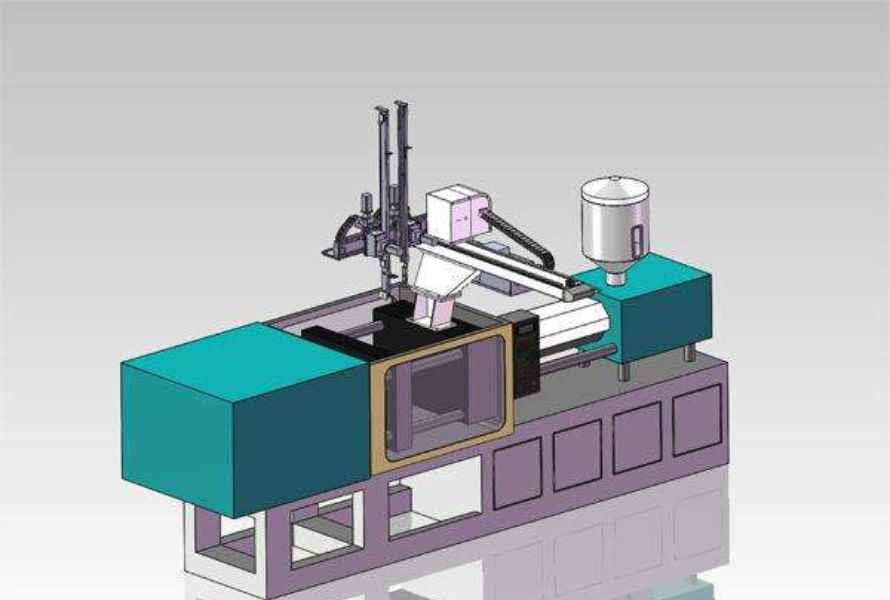
Several key factors can significantly influence the success of the injection molding process
4. Conclusion
The injection molding process has cemented its place as an indispensable technology for modern manufacturing. By understanding the nuances of the process, businesses can leverage its capabilities to achieve unmatched precision, scalability, and cost-effectiveness. Whether producing everyday items or critical industrial components, injection molding continues to drive innovation and elevate product quality in an increasingly competitive market.
5. About EuroPlas
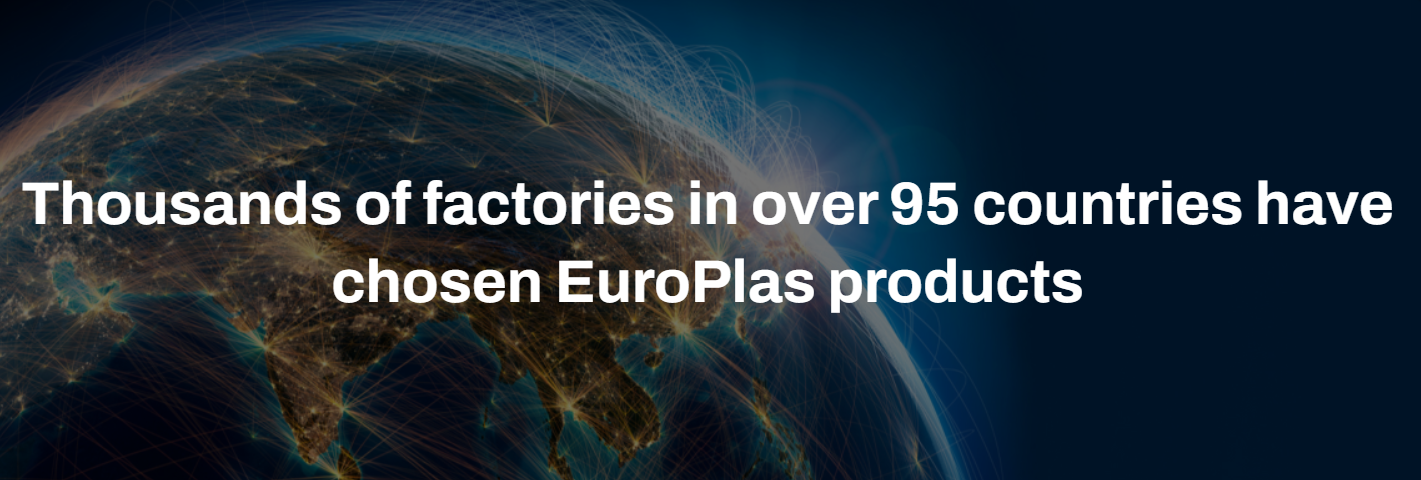
EuroPlas - No. 1 3D printing material manufacturer
EuroPlas (EuP) is the world’s leading filler masterbatch manufacturer, committed to providing innovative and high-quality plastic solutions to elevate the competitiveness of businesses worldwide. With a strong focus on ABS compounds and other essential 3D printing materials, EuroPlas is a trusted partner for industries looking to improve efficiency and sustainability.
EuP operates seven factories across Vietnam, spanning dozens of hectares, and produces up to 0.8 million tons annually. This extensive manufacturing capacity enables EuP to fulfill large-scale orders for clients in over 95 countries. With state-of-the-art equipment, such as extruders and injection molding machines, EuP guarantees products that meet the highest standards of quality and consistency.
What’s the wait? Visit our Contact Us page to learn how EuroPlas can help your business thrive.