Plastic is produced from different raw materials, going through many complex stages to form the final product. The plastic production process not only affects the quality of the product but also impacts the environment. This article will take you on an interesting journey, from raw materials to the final product, helping you better understand the plastic production process and the modern technologies applied in this industry.
1. Overview of the plastic production process
The plastic production process is a series of complex and sophisticated steps, requiring precision and strict control at each stage. When done properly and systematically, this process not only ensures product quality but also brings many important benefits to businesses and the environment.
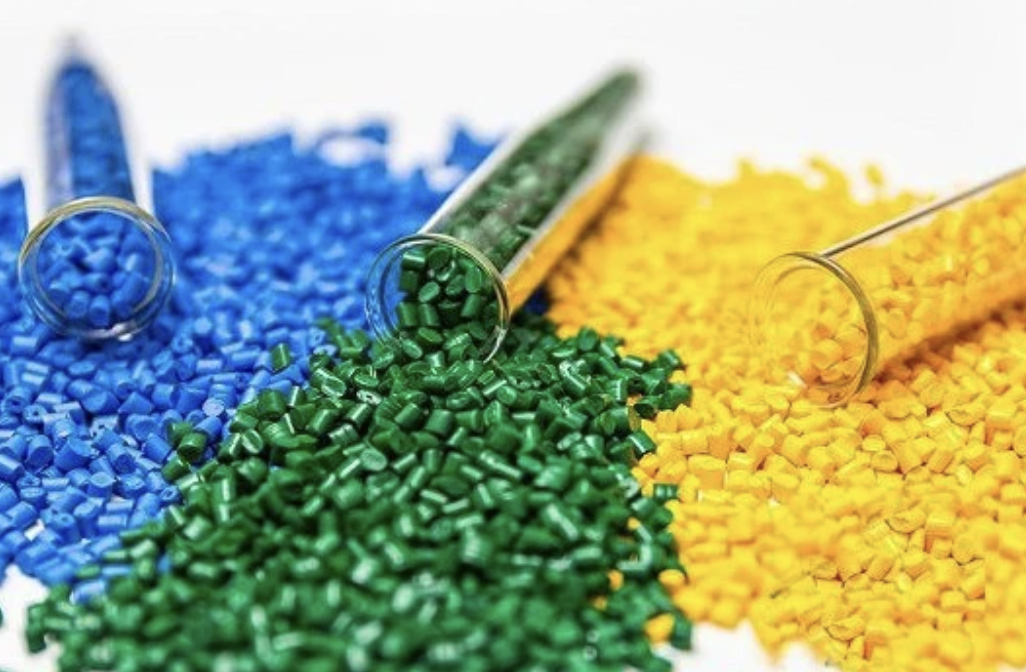
Properly and systematically implemented plastic manufacturing processes play an extremely important role in the plastic manufacturing process, specifically:
- Ensuring product quality:
A standardized process helps maintain product stability and reliability. This is especially important in minimizing problems related to new plastic odor, one of the major challenges of the plastics industry.
A well-organized process helps minimize waste of raw materials and energy, while increasing production productivity. This not only saves costs but also contributes to more efficient use of resources.
Adhering to strict processes helps to better control environmental factors during the production process, including temperature, pressure and time. This plays an important role in minimizing new plastic odor and volatile organic compounds (VOCs) generated during the production process.
A properly designed and implemented manufacturing process helps ensure worker safety, minimizing the risk of accidents and exposure to hazardous substances.
A well-organized process allows for easy tracking and tracing of products, from raw materials to finished products. This is important in addressing quality issues and meeting customer requirements.
- Enabling continuous improvement:
When processes are standardized and implemented consistently, it is easier to identify opportunities for improvement. This includes finding new, more effective ways to remove plastic odors.
A well-controlled manufacturing process makes it easier for businesses to comply with industry regulations and standards, including those related to odors and emissions.
- Enhance business reputation:
The ability to produce high-quality products that meet environmental and safety standards contributes to enhancing the reputation of the business in the market.
In short, a properly implemented and standardized plastic production process not only ensures product quality but also creates a solid foundation for the sustainable development of the business. In particular, in the context of increasing attention to environmental issues and consumer health, strict control of the production process, including the application of new effective ways to deodorize plastic, becomes a key factor determining success in the plastic industry.
See more: What is plastic? Everything you need to know about plastic.
2. How does the plastic production process take place?
The plastic production process is a series of complex steps, requiring precision and strict control. Here are the main steps in the plastic manufacturing process, along with the importance of performing this process correctly and systematically:
1. Raw material preparation: Select and mix virgin plastics and additives. Choosing the right raw materials and mixing ratios directly affects the quality of the product and the ability to remove the odor of new plastic.
2. Feeding: Bring the raw material mixture into the extruder or plastic injection molding machine. Proper feeding helps ensure product uniformity and minimize waste.
3. Heating and melting: The raw material is heated to the melting temperature. Strict temperature control helps avoid creating unwanted odor compounds.
4. Shaping: The molten plastic is fed into the mold or extruded through the mold head. Precise shaping will help minimize errors and optimize the use of raw materials.
5. Cooling: The product is cooled to stabilize the shape. Proper cooling helps minimize deformation and limit the odor of new plastic.
6. Finishing: Cutting, grinding, polishing, or decorating the product. This step determines the surface quality and aesthetics of the product.
7. Quality Control: Inspect the product for dimensions, durability, and other properties. Ensure that the product meets standards and detects quality issues early, including new plastic odor.
8. Packaging and Storage: The product is packaged and stored properly. Proper storage helps maintain product quality and limits the spread of new plastic odor.

In short, the plastic manufacturing process is a multi-stage process from raw materials to final products. The quality of plastic products depends largely on the production process. Strict control of the stages in the process will ensure that the final product meets the standards of quality, safety and environmental friendliness. At the same time, raising awareness of the importance of using plastics reasonably is also an important factor in protecting human health and the living environment.
However, to ensure sustainable development, we need to constantly improve the production process, minimize the impact on the environment and improve product quality. With the development of technology, bioplastics and recycling are opening up new promising directions.
3. Conclusion
The plastic production process is a series of complex steps, requiring precision and strict control from the raw material preparation stage to the final product. Strict adherence to this process not only ensures product quality but also optimizes production efficiency, minimizes environmental impact and enhances business reputation. In particular, in the context of the plastics industry facing challenges regarding the environment and consumer health, continuously improving the plastics production process, applying new technology and sustainable production practices become key factors determining the success and long-term development of businesses in the industry.
4. About EuroPlas
As the world's leading manufacturer of filler masterbatch, EuroPlas has affirmed its pioneering position in providing comprehensive solutions for the plastics industry. By constantly innovating and developing, EuroPlas focuses on meeting the increasingly diverse needs of the market.
EuroPlas is committed to providing customers with high-quality products and professional consulting services. For detailed advice, please contact EuroPlas via the form on the website. EuroPlas is committed to responding as soon as possible.