Choosing between PE filler masterbatch and talc-based fillers is a critical decision for manufacturers looking to optimize plastic production. Both options provide distinct advantages, ranging from cost reduction to improved mechanical properties, but they serve different needs depending on the application.
While PE filler masterbatch enhances impact strength, flexibility, and thermal resistance, talc-based fillers improve stiffness, heat resistance, and dimensional stability. Understanding these differences is essential for manufacturers aiming to achieve the best balance of cost-effectiveness and performance in their products.
This guide provides an in-depth comparison of PE filler masterbatch vs. talc-based fillers, exploring their composition, advantages, and typical applications across various industries. By the end, you’ll have a clear understanding of which filler best suits your manufacturing needs.
1. Key Differences Between PE and Talc Fillers
PE filler masterbatch and talc-based fillers are widely used in plastic production, each offering unique advantages based on their composition and performance characteristics.
PE filler masterbatch, made from polyethylene (PE) resin, CaCO₃, and additives, enhances flexibility, impact resistance, and cost efficiency, making it an ideal choice for film blowing, injection molding, and extrusion applications.
On the other hand, talc-based fillers, composed mainly of talc mineral and polymer resin, improve stiffness, heat resistance, and dimensional stability, making them suitable for automotive parts, household appliances, and industrial applications.
Understanding the differences between these two materials helps manufacturers select the most suitable filler to optimize product quality, performance, and production costs.
1.1 Composition
PE Filler Masterbatch
PE filler masterbatch is a composite material made from polyethylene (PE) resin, calcium carbonate (CaCO₃), and specialized additives such as processing aids and dispersion agents. CaCO₃, a naturally abundant and cost-effective mineral, acts as the primary filler, helping to enhance mechanical properties while significantly reducing production costs.
The presence of additives in PE filler masterbatch optimizes dispersion, ensuring uniform material distribution and improving impact resistance, heat resistance, surface hardness, and ductility in the final plastic products. This makes PE filler masterbatch an excellent choice for manufacturers seeking to enhance performance while maintaining cost-efficiency.
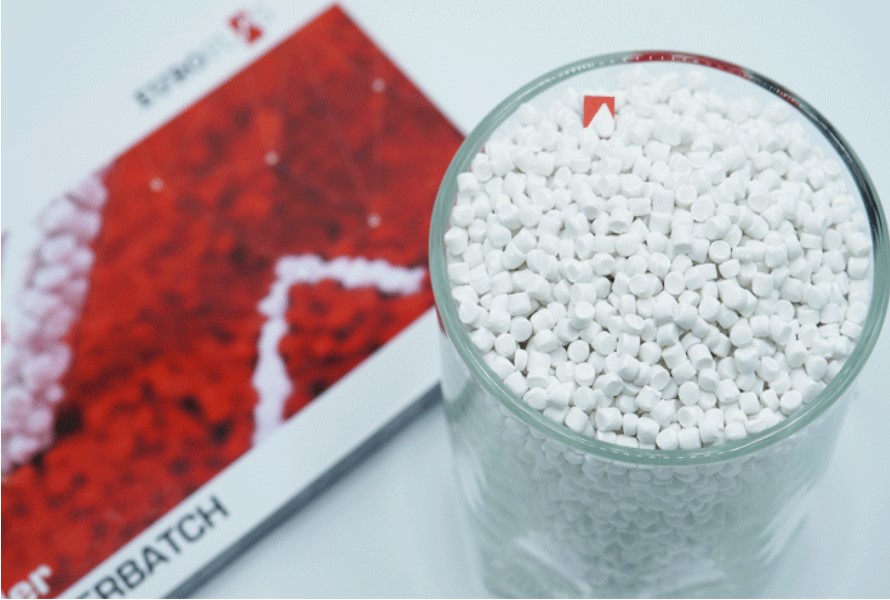
PE filler masterbatch is a composite material.
Talc-Based Fillers
Talc-based fillers are primarily composed of talc, a hydrated magnesium silicate, which is blended with polymer resins. Unlike CaCO₃, talc is a plate-like mineral that provides plastics with high stiffness, improved dimensional stability, and superior heat resistance. These characteristics make talc-based fillers particularly useful in engineering plastics, automotive components, and high-precision molded parts where rigidity and thermal performance are crucial.
However, because talc is generally denser and less flexible than CaCO₃, it may not be suitable for applications requiring high ductility and toughness. Additionally, the processing of talc requires fine grinding and surface treatment, which can increase production costs compared to CaCO₃-based fillers.
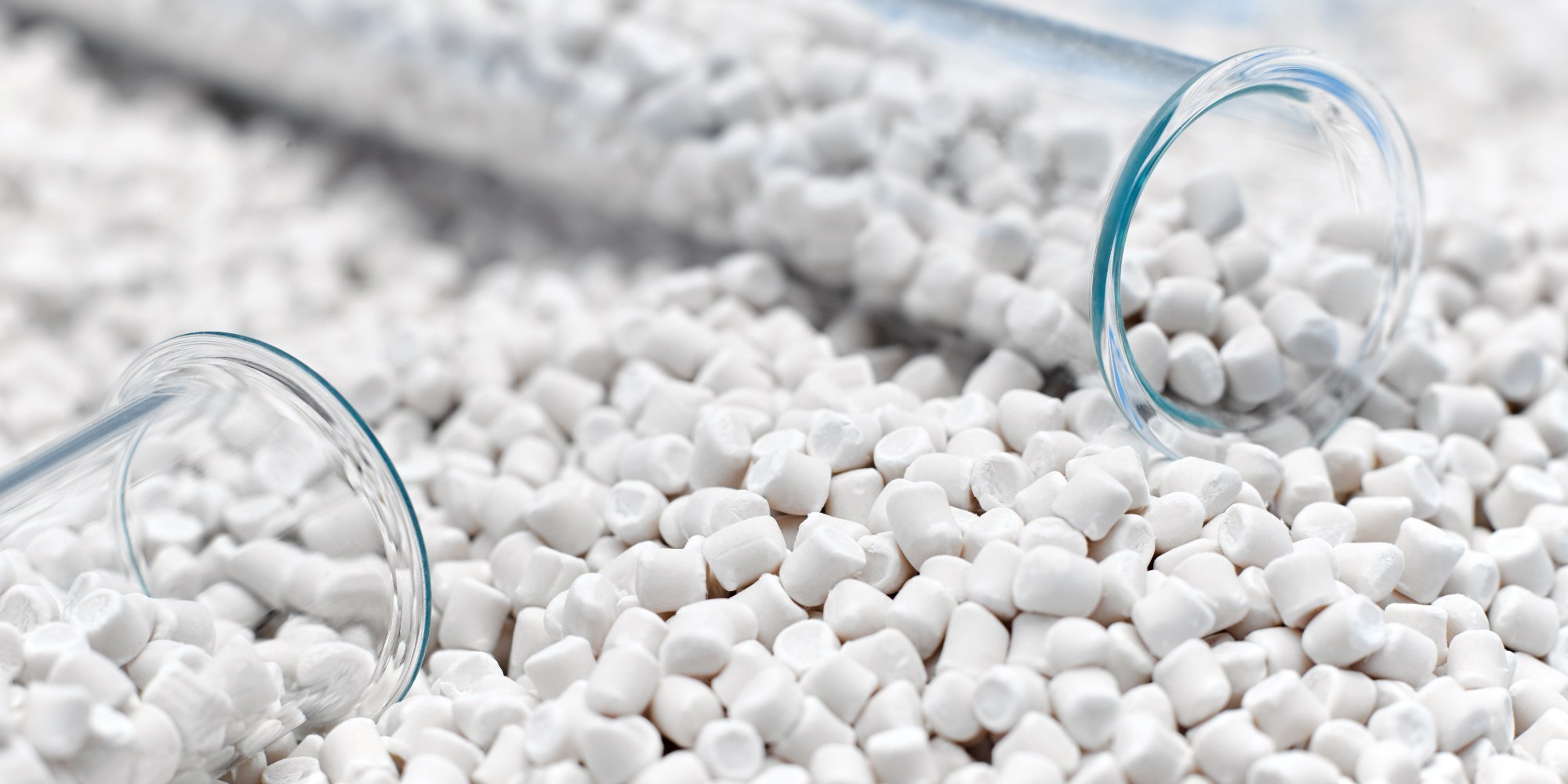
Talc-based fillers are primarily composed of talc.
1.2 Mechanical Properties
PE Filler Masterbatch
One of the standout features of PE filler masterbatch is its ability to enhance the impact strength, ductility, and flexibility of plastic products. This makes it ideal for applications that require toughness and resilience, such as:
- Film blowing (e.g., shopping bags, T-shirt bags, and food packaging films)
- Injection molding (e.g., household items and plastic containers)
- Extrusion (e.g., pipes, sheets, and profiles)
By incorporating CaCO₃, PE filler masterbatch also helps in reducing shrinkage, improving opacity, and increasing surface smoothness, making it a versatile solution for a wide range of industries.
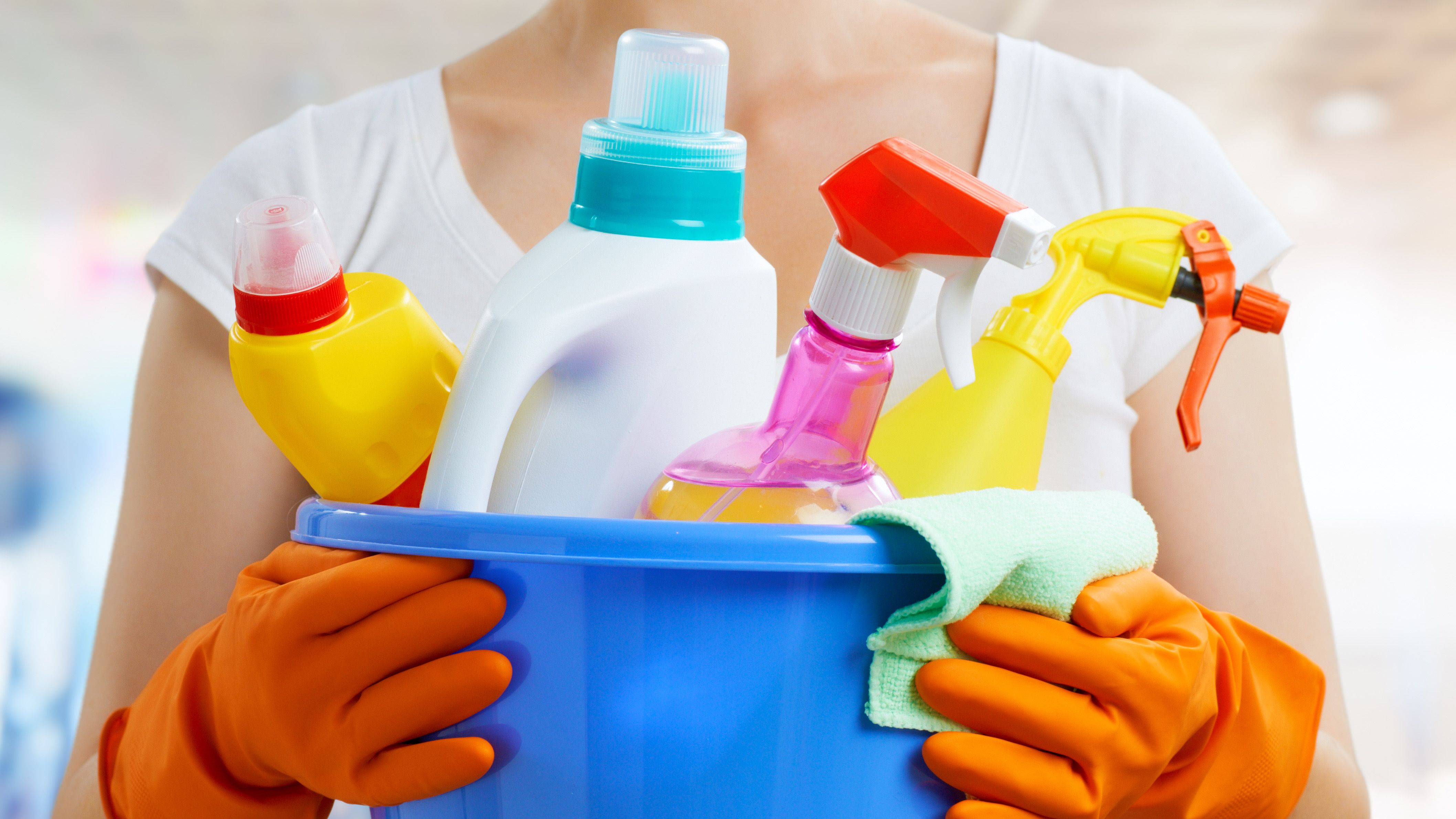
Household items and plastic containers.
Talc-Based Fillers
Talc-based fillers, on the other hand, are primarily used to increase stiffness, rigidity, and dimensional stability. This makes them well-suited for:
- Automotive components (e.g., dashboards, bumpers, and interior panels)
- Electrical and electronic housings
- High-performance industrial parts
Since talc has a high aspect ratio (plate-like structure), it enhances the material’s modulus of elasticity, making it less prone to deformation under stress. However, this increased stiffness comes at the expense of reduced impact resistance and flexibility, which may limit its use in applications that require high durability and shock absorption.
1.3 Processing and Energy Efficiency
PE Filler Masterbatch
PE filler masterbatch offers excellent thermal conductivity due to the presence of CaCO₃, which allows for efficient heat transfer during processing. As a result, manufacturers benefit from:
- Lower energy consumption during extrusion, molding, and film-blowing processes
- Faster cooling times, leading to shorter production cycles
- Reduced wear and tear on machinery, extending equipment lifespan
Additionally, the smooth dispersion of CaCO₃ particles in the polymer matrix prevents processing defects such as agglomeration and uneven distribution, ensuring higher product consistency.
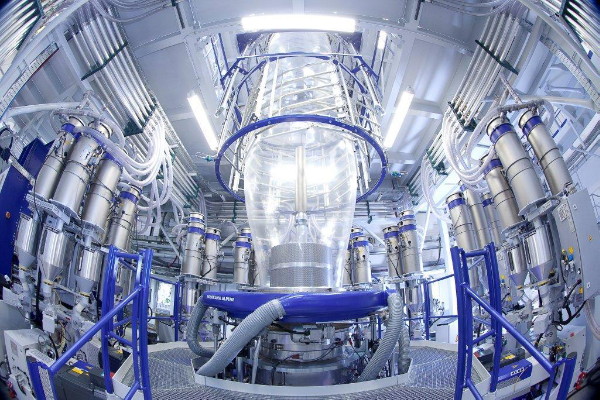
Film-blowing processes.
Talc-Based Fillers
While talc-based fillers also contribute to improved thermal resistance, they may require higher processing temperatures, especially in applications that demand precise melt flow control. This can lead to:
- Increased energy consumption during processing
- Longer cooling times, slowing down production speed
- Potential compatibility issues with certain polymer matrices
Moreover, because talc has a hydrophobic nature, additional surface treatments may be necessary to improve adhesion and dispersion within the polymer, further increasing processing complexity.
1.4 Cost Efficiency
PE Filler Masterbatch
One of the key advantages of PE filler masterbatch is its cost-effectiveness. CaCO₃ is widely available and low in cost, making it an economical solution for reducing plastic production expenses. Benefits of using PE filler masterbatch include:
- Significant raw material savings, as it partially replaces expensive virgin PE resin
- Lower energy costs due to CaCO₃’s thermal efficiency
- Improved production output by optimizing processing speed and stability
Because of these advantages, PE filler masterbatch is widely used in cost-sensitive industries, such as packaging, agriculture, and commodity plastics production.
Talc-Based Fillers
Talc-based fillers, while offering excellent performance enhancements, tend to be more expensive due to:
- Higher raw material costs, as talc must undergo extensive refinement
- Additional processing steps, such as grinding, purification, and surface treatment
- More energy-intensive processing requirements
As a result, talc-based fillers are often reserved for high-end applications where stiffness, heat resistance, and durability outweigh cost considerations, such as automotive, electronics, and aerospace industries.
2. Applications and Industry Preferences
Different industries favor PE filler masterbatch or talc-based fillers based on their specific material requirements. While PE filler masterbatch is widely used in flexible plastic products, talc-based fillers are preferred in applications that require rigidity and high thermal resistance. The selection depends on factors such as cost, mechanical properties, and processing efficiency.
2.1 Injection Molding and Blown Film Applications
PE Filler Masterbatch
PE filler masterbatch is extensively used in injection molding and blown film applications due to its cost-effectiveness, flexibility, and impact resistance. Its ability to improve ductility, surface smoothness, and shrinkage control makes it an ideal choice for manufacturers in the packaging, consumer goods, and agriculture industries.
Key applications include:
- Shopping bags & T-shirt bags: The addition of PE filler masterbatch reduces production costs while maintaining the necessary flexibility and durability.
- Garbage bags: Offers good tear resistance and cost savings compared to pure PE resins.
- Food packaging films: Ensures transparency, softness, and cost-efficiency in thin plastic films.
- Agricultural films: Enhances UV stability, tear resistance, and flexibility, making it suitable for greenhouse covers and mulch films.
- Household items: Used in containers, plastic chairs, and kitchenware to enhance surface quality and durability.
The presence of CaCO₃ in PE filler masterbatch also contributes to faster cooling rates during processing, resulting in shorter production cycles and lower energy consumption.
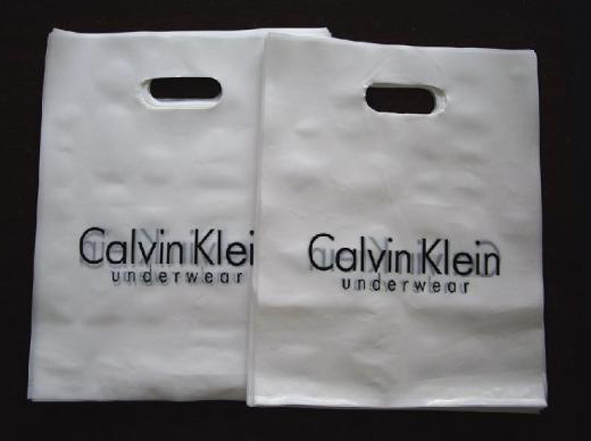
Shopping bags & T-shirt bags.
Talc-Based Fillers
Talc-based fillers are preferred in injection-molded products where stiffness, heat resistance, and dimensional stability are crucial. Unlike PE filler masterbatch, which improves flexibility, talc enhances the rigidity and mechanical strength of molded plastic parts.
Key applications include:
- Automotive parts: Used in dashboards, bumpers, and under-the-hood components due to its ability to withstand high temperatures and mechanical stress.
- Electrical appliances: Found in television casings, washing machine parts, and electronic housings for enhanced thermal resistance and fire retardancy.
- Consumer electronics: Used in laptop cases, mobile phone covers, and electronic connectors, ensuring dimensional accuracy and rigidity.
- High-performance industrial parts: Provides low shrinkage and high resistance to warping, making it ideal for engineering plastics used in industrial machinery.
Since talc-based fillers increase the material’s modulus of elasticity, they help in reducing part deformation under load, making them a go-to choice for industries demanding high-precision molded components.
2.2 Food Packaging Industry
PE Filler Masterbatch
In the food packaging sector, PE filler masterbatch is widely used as a cost-effective alternative to virgin PE resin. It enables manufacturers to maintain mechanical properties while significantly reducing raw material costs.
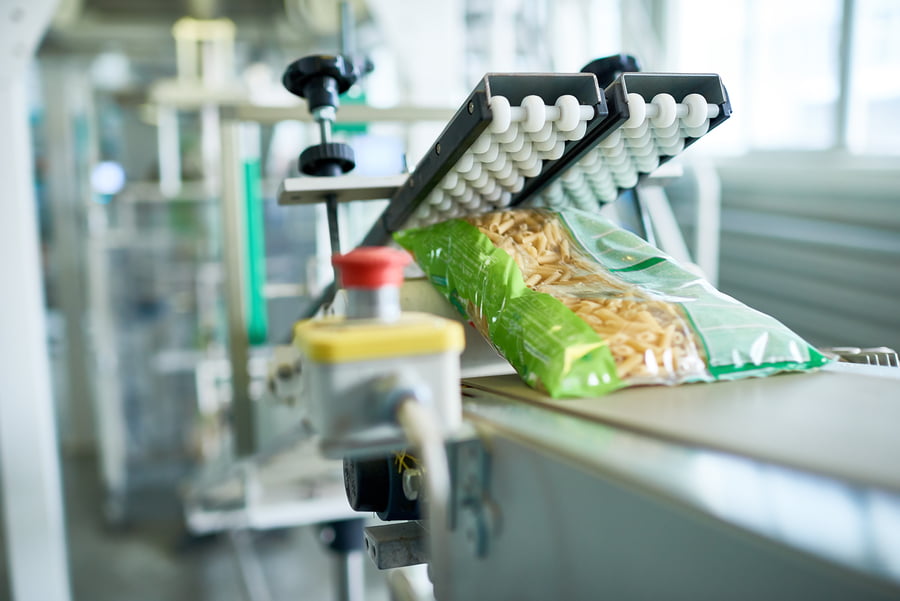
PE filler masterbatch is widely used as a cost-effective alternative to virgin PE resin.
Advantages in food packaging:
- Reduces production costs by replacing expensive PE resins while maintaining flexibility.
- Improves opacity and brightness, making packaging visually appealing.
- Enhances film strength to prevent tears and punctures.
- Compatible with food contact applications, ensuring safety and compliance with regulations.
Common applications include:
- Plastic grocery bags: Offers good tensile strength and elongation, allowing for efficient carrying of goods.
- Food wrapping films: Maintains clarity, flexibility, and barrier properties.
- Disposable containers & trays: Provides cost-effective solutions for food storage.
Talc-Based Fillers
Talc-based fillers, although less common in flexible food packaging, are used in rigid food packaging applications where barrier properties and dimensional stability are required.
Advantages in food packaging:
- Increases moisture resistance, preventing food spoilage.
- Enhances heat resistance, making it suitable for microwave-safe containers.
- Improves rigidity, ensuring stackability and durability of packaging.
Common applications include:
- High-barrier packaging films: Used in vacuum-sealed food storage bags to extend shelf life.
- Microwaveable food trays: Maintains shape and integrity under high temperatures.
- Yogurt cups and dairy containers: Enhances stiffness and form retention.
While PE filler masterbatch dominates in flexible food packaging, talc-based fillers are chosen for rigid food containers that require superior structural integrity.
2.3 Woven and Laminated Films
PE Filler Masterbatch
In the production of woven and laminated films, PE filler masterbatch provides a cost-saving alternative without compromising product performance. The addition of CaCO₃ enhances film stiffness, surface smoothness, and tear resistance, making it ideal for a variety of packaging applications.
Common applications include:
- PP woven bags: Used in agriculture, cement, and industrial packaging due to its strength and durability.
- Laminated films: Provides enhanced opacity, smooth surface texture, and heat resistance.
- Flexible packaging materials: Used in fertilizer sacks, rice bags, and industrial liners to enhance mechanical properties.
By incorporating PE filler masterbatch, manufacturers can reduce raw material costs, improve thermal stability, and maintain excellent printing quality on packaging surfaces.
Talc-Based Fillers
Talc-based fillers are less commonly used in flexible packaging due to their rigid nature, which can negatively affect film flexibility. However, they are sometimes incorporated into laminated structures where barrier properties and heat resistance are required.
Common applications include:
- Industrial sacks and bulk bags: Provides higher rigidity and load-bearing capacity.
- Insulated food packaging: Enhances thermal resistance and moisture protection.
- Protective coatings for packaging films: Improves scratch resistance and dimensional stability.
While PE filler masterbatch remains the preferred choice for flexible films, talc-based fillers can be used in specific applications where stiffness and barrier properties are critical.
3. Conclusion
Both PE filler masterbatch and talc-based fillers play crucial roles in plastic manufacturing, offering distinct advantages based on specific application requirements.
- PE filler masterbatch is an excellent choice for manufacturers seeking cost-effective solutions, enhanced flexibility, and improved impact resistance. It is widely used in blown films, flexible packaging, and injection-molded products, providing a balance between performance and affordability. Additionally, its energy-efficient processing makes it an attractive option for industries aiming to optimize production costs.
- Talc-based fillers, on the other hand, excel in applications demanding high stiffness, dimensional stability, and heat resistance. They are preferred in automotive parts, rigid packaging, and electrical appliances, where mechanical strength and thermal durability are critical. Although talc-based fillers may increase material rigidity, they provide excellent structural integrity and long-term durability.
Choosing between the two depends on the desired properties, industry requirements, and budget considerations. By understanding their differences in mechanical properties, processing efficiency, and cost-effectiveness, manufacturers can make informed decisions to enhance product quality and optimize production performance.
4. About EuroPlas’ Filler Masterbatch
EuroPlas is a global leader in filler masterbatch production, offering high-quality PE filler masterbatch and talc-based fillers designed to meet the needs of various industries. With over 15 years of expertise, we specialize in providing cost-effective and performance-enhancing solutions for plastic manufacturers worldwide.
Our PE filler masterbatch is formulated to reduce production costs, enhance mechanical properties, and improve processing efficiency, making it an ideal choice for blown film, injection molding, and flexible packaging applications. Similarly, our talc-based fillers deliver exceptional stiffness, heat resistance, and dimensional stability, making them suitable for automotive, electrical, and rigid packaging industries.
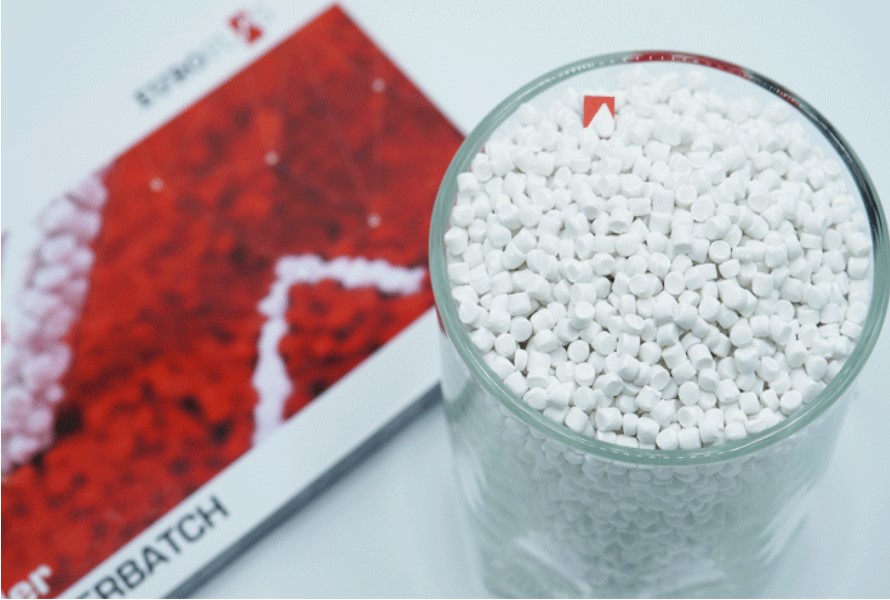
EuroPlas’s PE filler masterbatch.
At EuroPlas, we are committed to innovation, sustainability, and customer satisfaction, ensuring that our filler masterbatch solutions help manufacturers achieve higher efficiency and superior product performance.
For more information, contact EuroPlas today or visit our blog for expert insights into plastic compounding solutions!