As the bioplastics market continues to grow, manufacturers and sustainability leaders are increasingly interested in understanding the specific characteristics of each bioplastic type. Among the most commonly used materials today are PLA (Polylactic Acid), PBAT (Polybutylene Adipate Terephthalate), and PHA (Polyhydroxyalkanoates). Each material offers unique properties that affect their usability, biodegradability, and environmental impact. This article analyzes how PHA bioplastic stands out compared to PLA and PBAT.
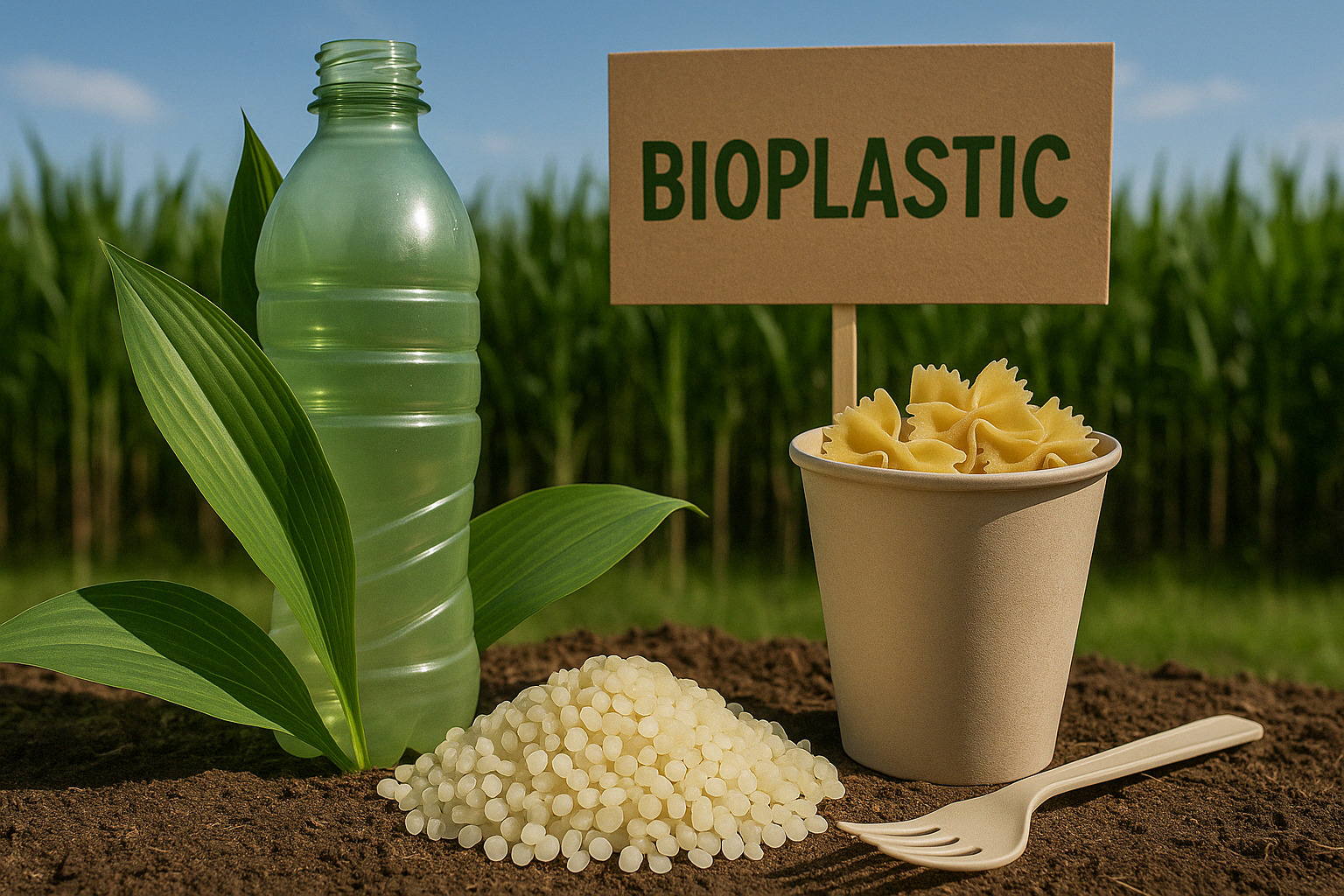
1. Origin and Raw Materials
PHA bioplastic is synthesized through microbial fermentation of sugars or lipids. Unlike PLA, which is produced by fermenting plant starches like corn or sugarcane, and PBAT—a petrochemical-derived co-polyester—PHA is entirely bio-based and produced directly by bacteria. This biological origin makes PHA closely resemble natural biopolymers found in living organisms.
What makes PHA bioplastic particularly appealing is its flexibility in raw material sourcing. It can be produced from non-food sources such as agricultural by-products, used cooking oil, and even waste streams. This provides PHA with a significant advantage in discussions about food security and sustainable resource sourcing.
2. Biodegradability
All three materials—PHA, PLA, and PBAT—are classified as biodegradable, but they differ significantly in terms of the environments and timeframes required for degradation.
PHA bioplastic is renowned for its excellent biodegradability under various conditions. Studies indicate that the average rate of PHA biodegradation in marine environments ranges from 0.04 to 0.09 mg·day⁻¹·cm⁻², depending on environmental conditions. This gives PHA a significant environmental advantage, especially in reducing microplastic accumulation in oceans.
PLA, while also biodegradable, typically requires industrial composting conditions to degrade effectively. The EN 13432 standard mandates that PLA must achieve at least 90% biodegradation within six months under industrial composting conditions. It is less suitable for natural environments or home composting systems.
PBAT is designed to biodegrade in industrial environments and is often blended with PLA to enhance flexibility and degradation rates. Products like BASF's ecoflex® have been certified for industrial compostability under international standards such as EN 13432 and ASTM D6400.
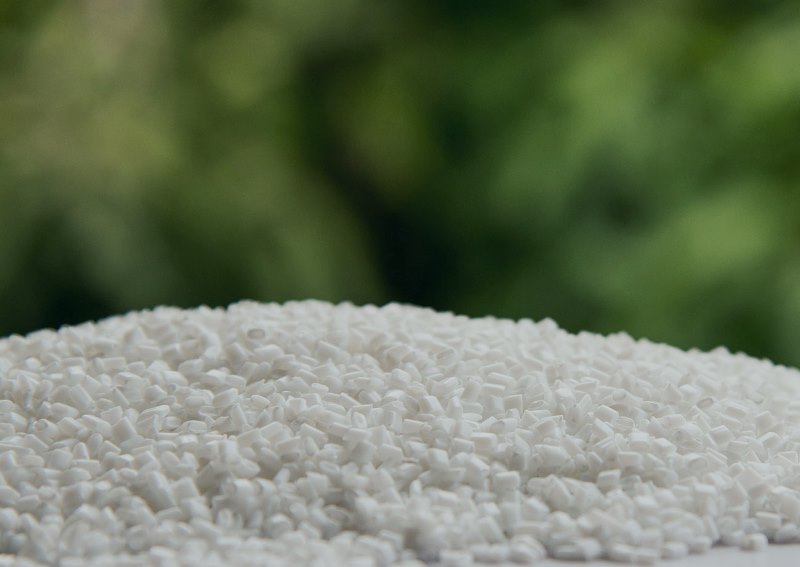
PHA bioplastic is renowned for its excellent biodegradability under various conditions.
3. Performance and Processability
In terms of mechanical properties, PHA bioplastic exhibits characteristics similar to polypropylene, including flexibility and UV resistance. However, its brittleness and slow crystallization rate can be drawbacks in certain applications, necessitating blending or further modification.
PLA is notable for its high stiffness and transparency, making it ideal for packaging, 3D printing, and disposable products. However, it tends to be brittle and has poor heat resistance. PBAT offers high flexibility and processability akin to LDPE, making it suitable for film products, bags, and packaging requiring elasticity.
While PLA and PBAT can be processed relatively easily using existing plastic processing equipment, PHA requires specialized equipment due to its sensitivity to thermal degradation.
4. Environmental Impact and Certifications
Environmentally, PHA bioplastic offers significant benefits. It is produced from renewable resources, can degrade in natural environments, and helps address ocean plastic pollution. Many PHA variants have been certified for home and marine biodegradability.
PLA is also bio-based and emits fewer greenhouse gases during production compared to fossil-based plastics. However, its end-of-life processing limitations reduce its overall sustainability potential.
PBAT, derived from petroleum, is not considered bio-based, though it is certified for industrial compostability under standards like EN 13432 and ASTM D6400.
5. Market Applications
PHA bioplastic is increasingly being considered for applications where uncontrolled environmental degradation is a concern—such as agricultural films, fishing gear, and disposable products prone to environmental leakage. It is also gaining traction in medical fields for items like sutures and bio-implants due to its biocompatibility.
PLA dominates in packaging, disposable cutlery, and 3D printing applications. It is often blended with PBAT to enhance flexibility in film and bag products. PBAT is favored for products requiring elasticity and softness, such as biodegradable garbage bags and food wraps.
6. Conclusion
While PLA, PBAT, and PHA each play vital roles in transitioning to a more sustainable plastic economy, PHA bioplastic stands out for its natural origin, superior biodegradability, and potential to address plastic pollution in both marine and terrestrial environments. As technology advances and production costs decrease, PHA is expected to become an increasingly important material in the global bioplastics portfolio.
Businesses aiming for high environmental performance and compliance with emerging waste reduction policies should seriously consider integrating PHA bioplastic into their material strategies.
7. About EuroPlas
EuroPlas is a global leader in masterbatch and bioplastic compound manufacturing. With seven factories located in Vietnam and Egypt, and a production capacity of up to 800,000 tons annually, EuroPlas exports to over 95 countries worldwide.
The company’s BiONext product line includes high-performance bioplastic compounds based on PLA, PHA, and PBAT. These materials are engineered for packaging, agriculture, and consumer applications where both performance and sustainability are critical.
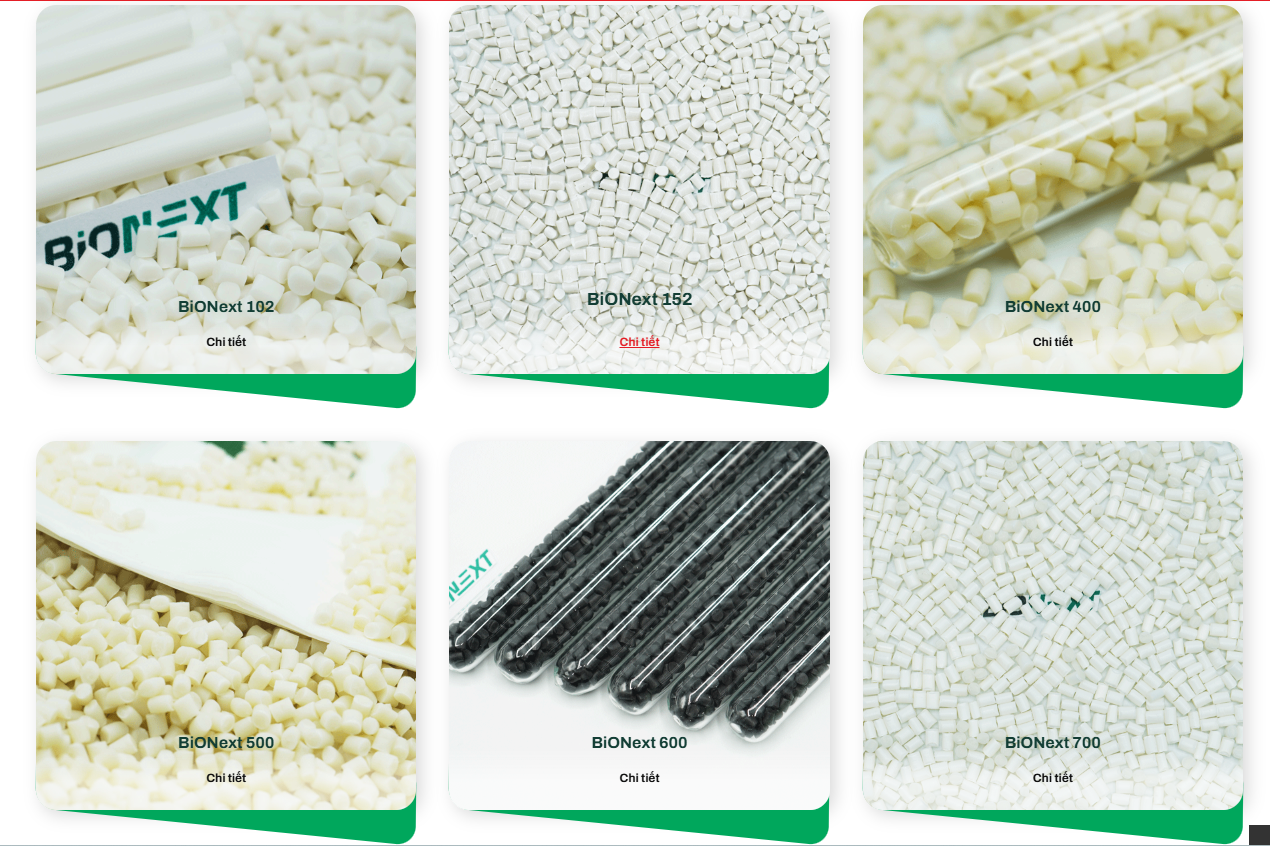
By combining innovation with a strong environmental vision, EuroPlas supports its customers in reducing their carbon footprint while maintaining product functionality.
Learn more at the EuroPlas Blog or connect via our Contact Page.