In the plastics industry, plastic additives and filler masterbatches are crucial for enhancing properties and reducing costs. Additives are substances added in small amounts to improve material characteristics, while filler masterbatches are often used in larger quantities to lower costs or alter product physical properties. Many people confuse these two concepts. Understanding the difference is essential for both manufacturers and consumers to accurately assess product quality and features.
This article will provide detailed information on how to distinguish plastic additives from plastic fillers. This will help readers gain a deeper understanding of the production process and properties of everyday plastic products.
1. Overview of Plastic Additives and Filler Masterbatches
Plastic additives and filler masterbatches are both added to base plastics, contributing to the creation of diverse plastic products and suitable for many different applications in daily life. However, they have different characteristics and uses. Below is an overview of plastic additives and filler masterbatches:
1.1. Plastic Additives
Plastic additives are substances added to plastics in small amounts, typically less than 5% of the total weight. The main purpose of plastic additives is to improve specific properties of plastic materials, typically durability, flame retardancy, thermal stability, or UV resistance.

Plastic additives can be classified into several different groups, including:
- Stabilizers: Stabilizers prevent plastic degradation caused by heat, light, or oxygen. UV stabilizers specifically protect against ultraviolet rays, extending product life for outdoor use.
- Lubricants: Improve the flowability of plastics during processing, helping to increase production efficiency and product surface quality.
- Plasticizers: Improve the flexibility and processability of plastics, especially important in the production of soft plastic products such as food wraps.
- Colorants: Add color to plastic products, including pigments and dyes.
- Flame retardants: Help plastics resist burning or slow down the burning process, widely used in electronic and construction applications.
- Antioxidants: Protect plastics from oxidation during production and use, helping to maintain the mechanical properties and color of the product.
Plastic additives play an important role in customizing the properties of plastics to meet the specific requirements of each application. For example, in the production of food packaging, antioxidants and stabilizers are used to extend the shelf life of the product and protect the food inside.
1.2. Filler Masterbatches
Filler masterbatches are materials added to plastics in larger quantities, typically ranging from 10% to 50% or even more of the total weight of the mixture.
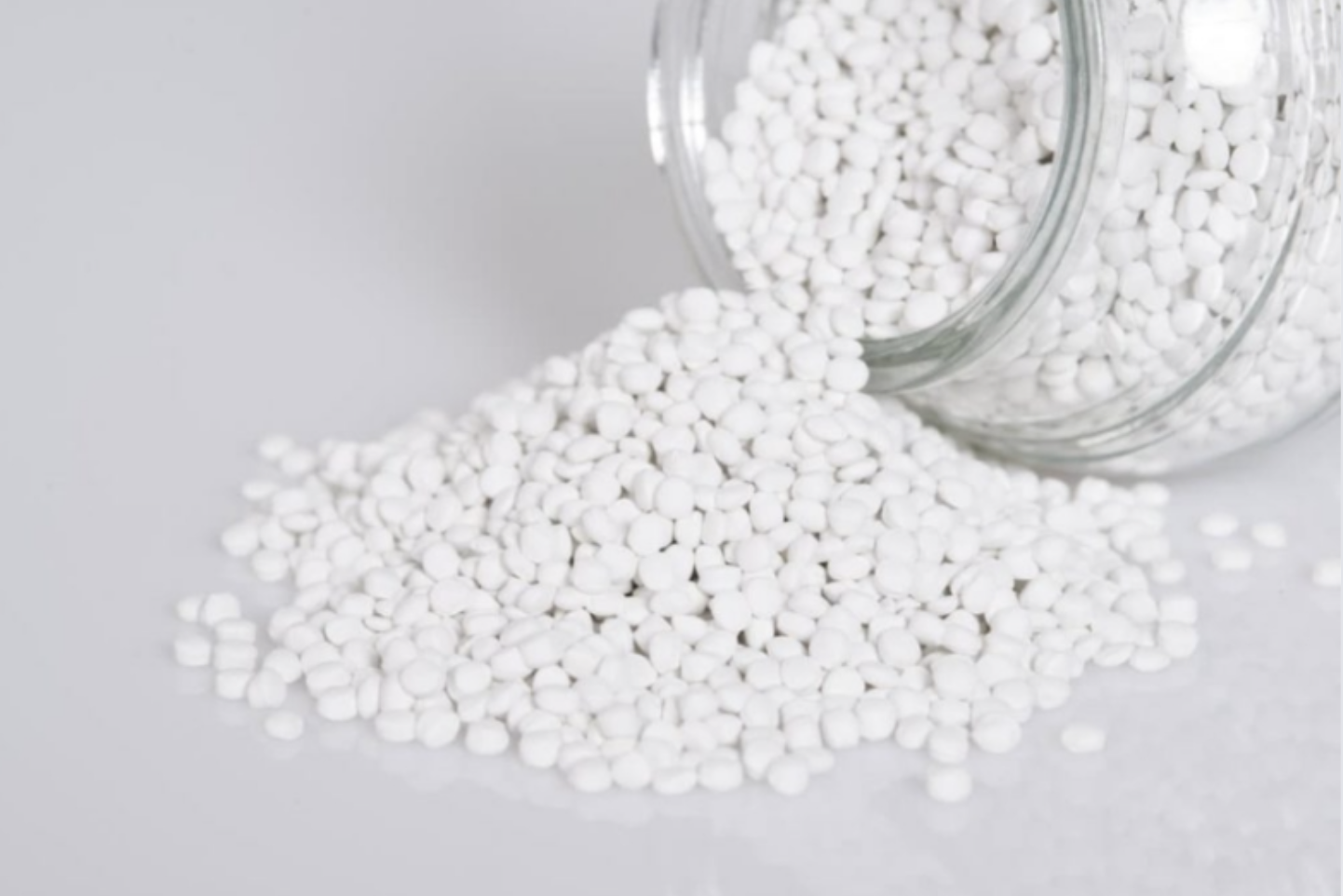
Filler masterbatches are used primarily to:
- Create special properties such as electrical conductivity of insulation.
- Reduce manufacturing costs by replacing some of the expensive base resin.
- Improve certain mechanical properties such as hardness, impact resistance, or dimensional stability.
Some common uses for filler masterbatches include:
- Talc: Increases hardness and water resistance, used in many applications such as packaging and automotive components.
- Wood flour: Provides a natural look and improves certain mechanical properties, commonly used in the production of wood plastic composite (WPC) flooring.
- Limestone powder: Helps increase hardness and reduce costs, commonly used in the production of PVC pipes and building products.
- Glass Fiber: Improves strength and stiffness, widely used in the production of composite materials for the automotive and aerospace industries.
Filler masterbatches not only reduce manufacturing costs but can also significantly improve the properties of the final product. For example, adding glass fibers to the base resin can increase the strength and stiffness of the material, allowing it to be used in mechanically demanding applications.
See more: Here’s how EuroPlas produces CaCO3 filler plastic
The correct selection and use of plastic additives and filler masterbatches requires in-depth knowledge of polymer chemistry and materials engineering. Manufacturers must carefully consider the desired performance against potential impacts on the overall properties of the final product.
2. How to Distinguish between Plastic Additives and Filler Masterbatches
In recent years, the trend of sustainable development has led to increasing interest in environmentally friendly plastic additives and fillers. Researchers are focusing on developing bio-based plastic additives and filler masterbatches from renewable sources, aiming to minimize the environmental impact of the plastics industry. Understanding these two components is important not only for manufacturers but also for consumers, helping them accurately assess the quality and performance of plastic products.
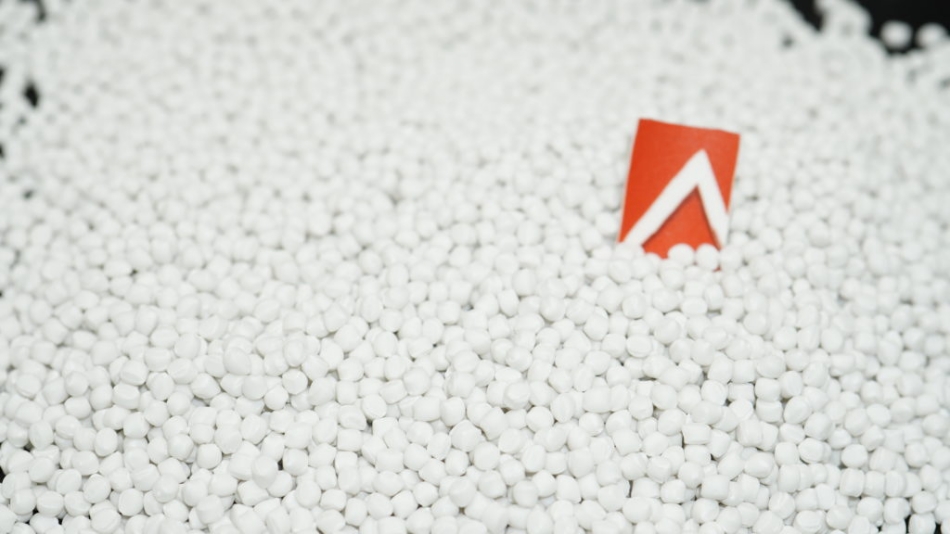
2.1. Similarities
We will now examine some similarities between plastic additives and plastic fillers with EuroPlas:
Diversity |
Plastic additives and filler masterbatches come in a variety of types, allowing the properties of the resin to be tailored to the specific requirements of each application. |
Manufacturing Process
|
Plastic additives and filler masterbatches are both added to the base resin during the manufacturing process, usually during the mixing or extrusion stages. |
Impact on Properties
|
Plastic additives and filler masterbatches have the potential to influence the mechanical, physical, and chemical properties of the final product. |
Expertise Required
|
The selection and use of plastic additives and filler masterbatches requires in-depth knowledge of polymer chemistry and materials engineering. |
2.2. Differences
In contrast to their similarities, plastic additives and filler masterbatches exhibit several key differences:
Characteristics |
Plastic Additives
|
Filler Masterbatches |
Particle Size |
Typically smaller, sometimes at the molecular or nano level.
|
Typically larger, sometimes visible to the naked eye.
|
Homogeneity |
Typically evenly dispersed throughout the resin matrix, creating a homogeneous mixture.
|
Can produce a heterogeneous mixture, with visible filler particles in some cases.
|
Primary Purpose |
Improves specific properties of the resin such as strength, flame retardancy, thermal stability, or UV resistance.
|
Reduces manufacturing costs by replacing part of the expensive resin matrix, and can improve some mechanical properties.
|
Recyclability
|
Typically does not significantly affect the recyclability of the resin. |
Can significantly affect recyclability, sometimes making recycling more difficult. |
Influence
|
Focuses on one or a few specific properties of the resin.
|
Affects many properties of the material simultaneously.
|
Affects Properties |
Usually does not significantly change the basic properties of the resin base, but only improves or adds specific properties.
|
Can significantly change the properties of the material, including hardness, impact strength, and dimensional stability.
|
Affects Appearance |
Usually does not significantly affect the appearance of the final product (except in the case of pigments).
|
Can significantly change the appearance of the product, creating effects such as marble or wood grain.
|
Affects Processing |
Usually does not significantly affect the processing process, and can even improve the machinability of the resin.
|
Can significantly affect the processing process, requiring adjustments to parameters such as temperature and pressure.
|
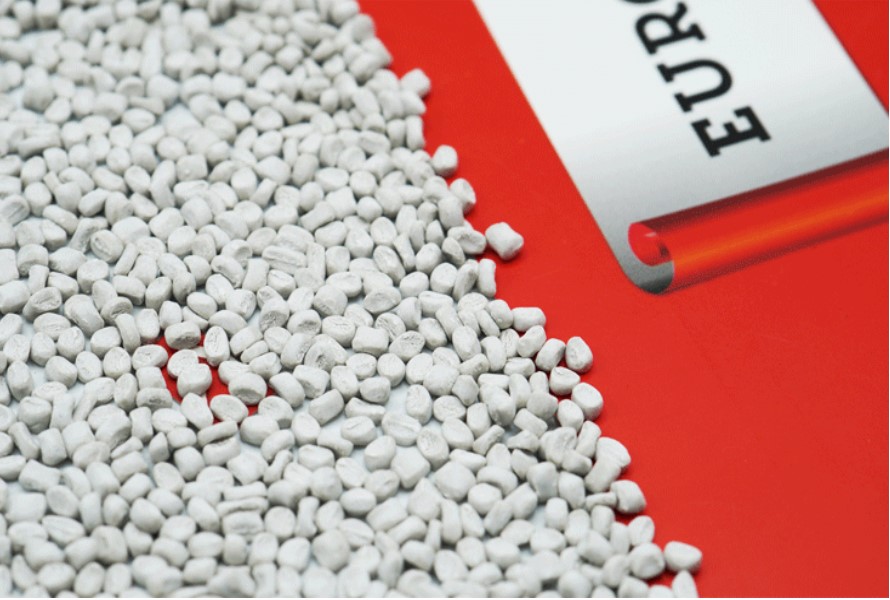
Above are the similarities and differences between plastic additives and filler masterbatches. The main difference between plastic additives and filler masterbatches lies in their quantity and primary purpose. Plastic additives are used in small quantities to improve specific properties, while plastic fillers are used in larger quantities to reduce costs or significantly change the properties of the material.
In practice, many plastic products use both plastic additives and filler masterbatches to achieve the optimal balance between performance, cost, and manufacturability. This combination requires a deep understanding of the interactions between the components and their effects on the overall properties of the material.
3. Conclusion
With the ever-growing plastics industry, the research and development of new additives and fillers, especially those that are environmentally friendly, is becoming urgent.
The ability to distinguish between plastic additives and filler masterbatches is essential for the plastics industry. Although both are added to the base resin to improve performance or reduce costs, they have distinctly different characteristics and uses. Understanding these similarities and differences helps manufacturers and material engineers to choose the right type of plastic additives or filler masterbatches for each specific application. This not only ensures that the desired properties of the final product are achieved, meeting the demand for high-quality plastic products, but also optimizes production costs and process performance.
4. About EuroPlas
As a leader in the field of filler masterbatch manufacturing, with a commitment to continuous innovation and improvement of its products, EuroPlas has built a solid reputation in the industry due to its ability to meet high standards of quality, safety, and environmental friendliness. With many years of experience in the industry, EuroPlas understands the importance of distinguishing and using the right plastic additives and fillers. EuroPlas not only provides high-quality products but also acts as a reliable partner, supporting customers in choosing and using the most suitable products for their specific needs.
In addition, EuroPlas also focuses on sustainability in its business operations by applying green production processes, minimizing the impact on the environment during operations. With a strong commitment to quality, innovation, and sustainability, EuroPlas has become a trusted partner for many businesses in the plastics industry. Do not hesitate to contact EuroPlas's consulting team via hotline and email or leave information via the form to receive the most accurate support.