With the goal of increasing the localization rate to 60%, new groups of materials have been continuously researched and developed to serve the automotive industry. In which, the most notable is compound engineering plastic. Let's discover the common applications of this material in the automotive industry in this article!
According to the Ministry of Industry and Trade, after more than 10 years of aiming to increase the localization rate of 9-seat cars to 60%, Vietnam's automotive industry has only reached 7-10% on average. Meanwhile, the localization rate of countries in the region is on average 65-70%, Thailand alone reaches 80%.
Related: Masterbatch - definition, applications, market trends and more
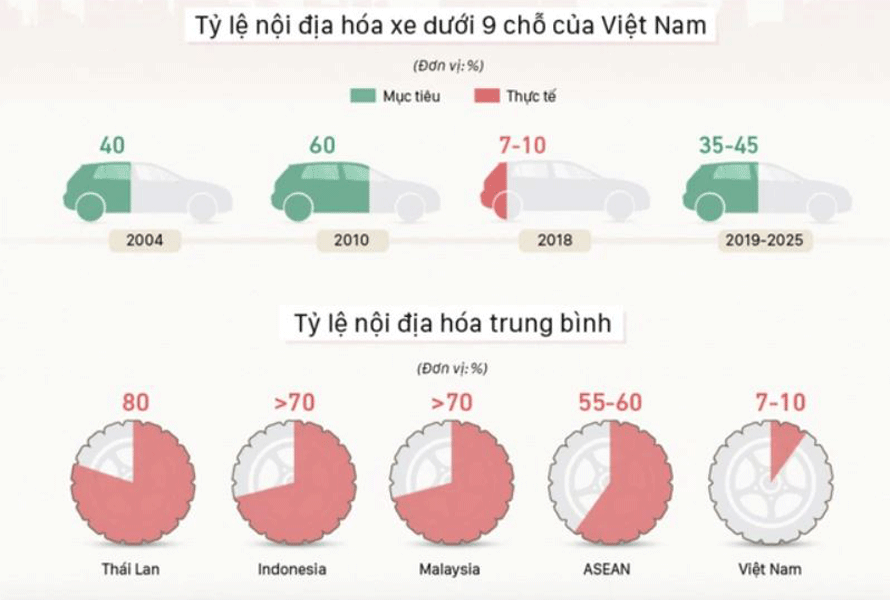
The localization rate of Vietnam automotive industry is only 7-10% on average
Accordingly, one of the main barriers that makes it difficult to assemble and manufacture cars in Vietnam is the limitation in input materials - most of which do not meet the manufacturer's technical standards, or their price is much higher than foreign competitors. This makes us dependent on imported raw materials, thereby limiting the development of supporting industries. To solve this, plastic engineering compound was born as a new material solution for the automotive industry.
Plastic engineering compound and its outstanding advantages
Compound engineering plastic is a combination of primary resin base, special reinforcing agents and appropriate additives. Some fossile resin commonly used in technical compounds are ABS, PP, PC, PA6, PA66, etc. Based on the characteristics of the end product, the plastic resin will be mixed with appropriate reinforcing agents, such as glass fibers/beads, conductive carbon, flame retardants, talcum powder, BaSO4 salts,... Processing aids and dispersion agents are two indispensable materials to increase the efficiency of the extrusion process. In some cases, special additives, such as transparency, brightness, UV resistance,... are also used to meet the technical requirements of the end-product.
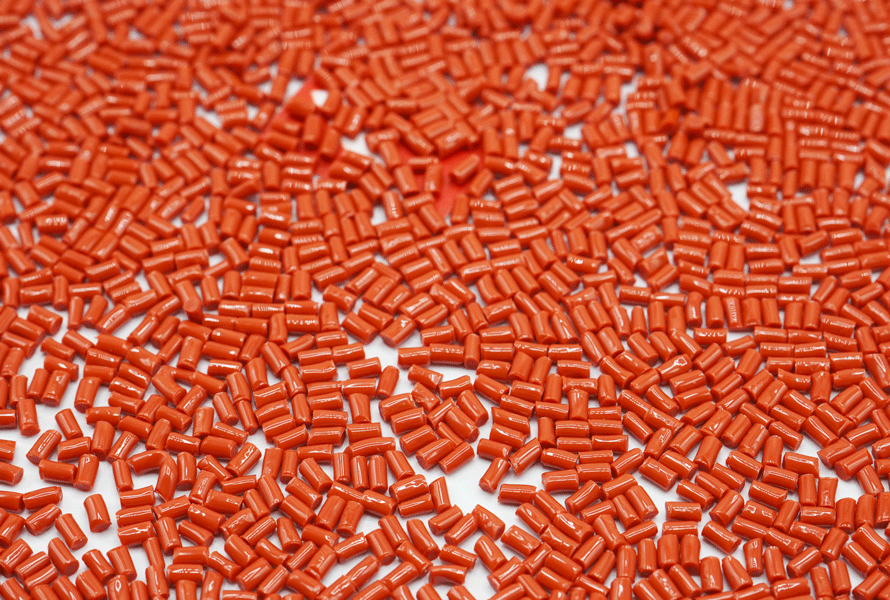
Compound engineering plastic is a combination of fossil resin, special reinforcements and appropriate additives
Customized solution for each end-product
The biggest difference between compound and traditional plastic material lies in the production method. Most of the traditional ingredients are mass-produced products. This means that whether it is a business that produces plastic pipes, plastic housings for household appliances or a business that manufactures plastic toys, it is possible to use the same input materials. Meanwhile, automotive manufacturing is a specific industry, requiring high processing level and absolute mechanical accuracy. Therefore, if only mass-produced materials are used, it is difficult to meet the manufacturer's requirements.
On the other hand, plastic engineering compounds are designed to be "tailored" according to the characteristics of the end product. They're still fossil resin, reinforcement and additives, but for each finished product, these ingredients and proportions of ingredients will be adjusted to suit the technical requirements. This advantage makes engineering plastics specifically suitable for products requiring high technical level as the automotives.
Full functions in one single material
Another outstanding advantage of engineering plastics is that it brings all necessary functions for end-products in one material. Usually, to create a finished product (even the simplest), businesses need many different types of materials. The procurement, delivering and mixing of raw materials makes the production process complicated and inefficient, and also results in poor dispersion on the surface of the finished product.
However, the story for compound engineering plastics is much simpler. Due to the specific design based on the characteristics of the end product, engineering compounds carry all the features of the finished product. Enterprises can directly put it on the production line without having to go through the stage of mixing materials, thereby simplifying the production process, saving time and improving output.
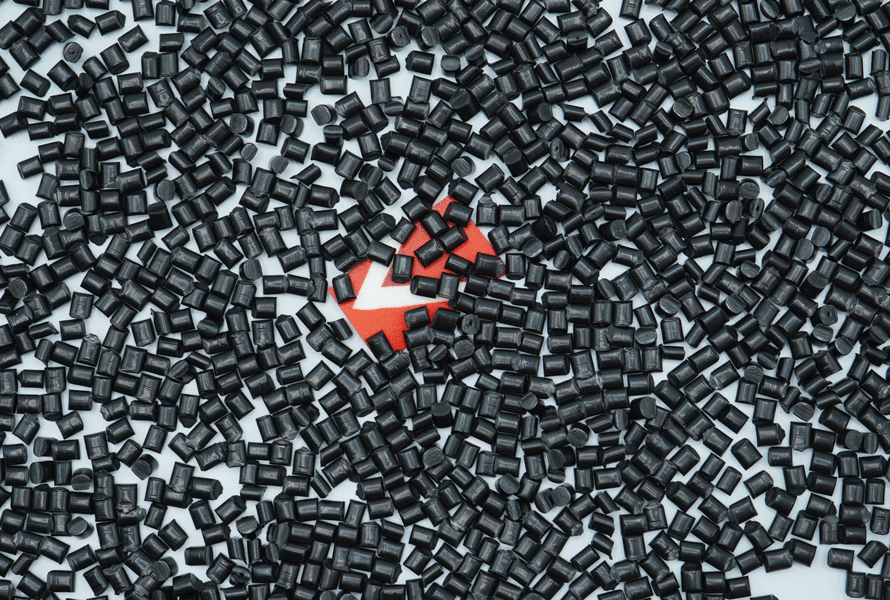
Plastic engineering compound has full functions of end-products in one single material
Benefits of engineering plastic compound in automotives
With special reinforcements, engineering plastic compounds help to increase the stiffness and impact strength of the finished product. Besides, through the improvement of the plastic structure, the compound makes the injection molding process easier and more efficient, limiting the formation of mold marks, stains, warping, uneven colors,... on the surface of finished products. At the same time, it increases the features of the end product, such as electrical conductivity, ease of painting,... thanks to special additives
Applications of plastic engineering compounds in the automotives
With outstanding advantages, compounds have been applied more and more widely in the automotive industry. According to Grand View Research, the automotives is the largest consumer of compounds in Southeast Asia with the revenue of US$821.4 million, accounting for 24.16% of the market share in 2018. This number is predicted reach 25.42% by 2026.
In Vietnam, although it is relatively young, the automotives still becomes the largest consumer of the compound with 59.9 million USD of revenue recorded in 2018. This number was estimated to reach 135.1 million by 2026, indicating the strong attraction of this material. Let's explore the outstanding applications of plastic engineering compound in the automotive industry below!
Car interiors
Lighter, and therefore more energy efficient, the engineering compound is widely used in automotive interiors: seat belts made of ultra-durable polyester, airbags made of polyamide, child safety seats children, bus seats made of pp compound,... In which, PP compound with good rigidity, impact resistance and ease of processing has accounted for nearly half of the proportion of compound materials used in the automotive industry. .
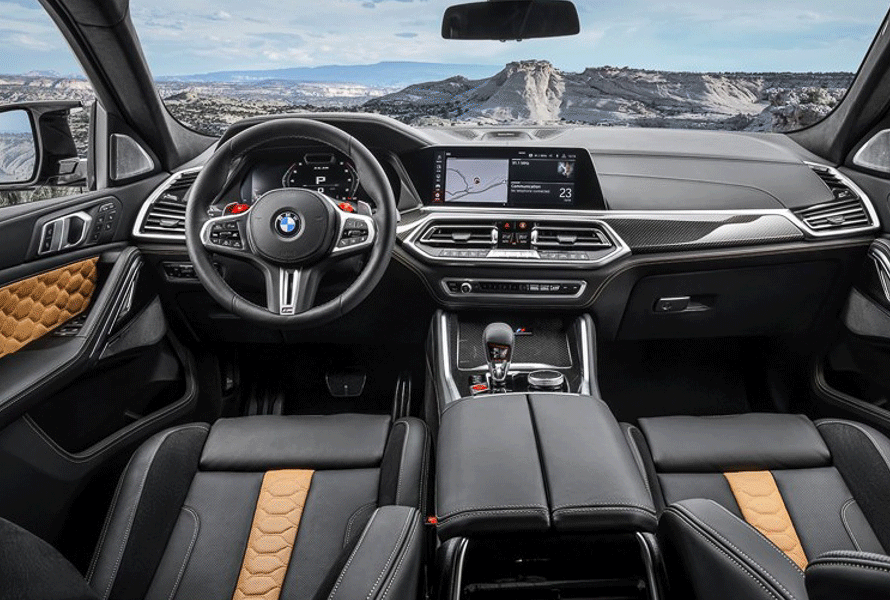
PP compound accounts for nearly half of the amount of compound consumed in the automotives
Car exteriors
Not only interiors, the exterior parts (such as the front bumper, grille, panels, door panels, fuel tank cap,...) also use engineering plastics compound (Polycarbonate (PC), polypropylene (PP), Acrylonitrile Butadiene Styrene (ABS), polyamide (PA)) thanks to its ideal hardness and weather resistance. By mixing with appropriate pigments and special effects additives, the compound can well meet the technical and aesthetic requirements of the finished product.
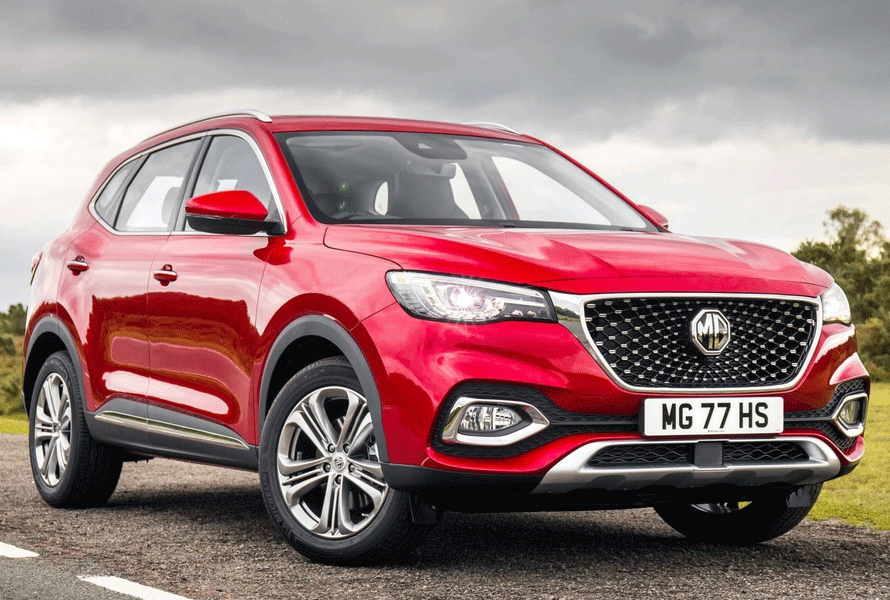
External parts, such as bumper, grille, panels, car door, fuel tank cap,... also use engineering plastic compound
EuroPlas plastic engineering compound
Nearly 14 years of construction and development, EuroPlas is proud to bring customers quality compound products, which meet all technical requirements of finished products. EuP currently provides a variety of technical plastic compound lines such as compound PP, compound ABS, compound PC, compound PA66, etc. with its own formula according to the requirements of the finished product. The product is now well embraced by many large enterprises in several industries, such as electronics industry, household electrical appliances, automotives,...
Contact us for advice and samples HERE!