Injection molding is a practical manufacturing technique when high volumes of identical parts are needed. To master it, nevertheless, calls for a high level of technical knowledge. Because there are so many distinct factors at play, even seemingly little errors made in the beginning stages of color mixing might later cause serious issues - and even compromise product integrity - down the line.
Related:
- How to effectively apply colorants in your plastic injection molding?
- Wholesale plastic color compounds: 4 reasons to choose a reliable supplier
- What is plastic? How to color plastic?
- Color masterbatch for housewares products
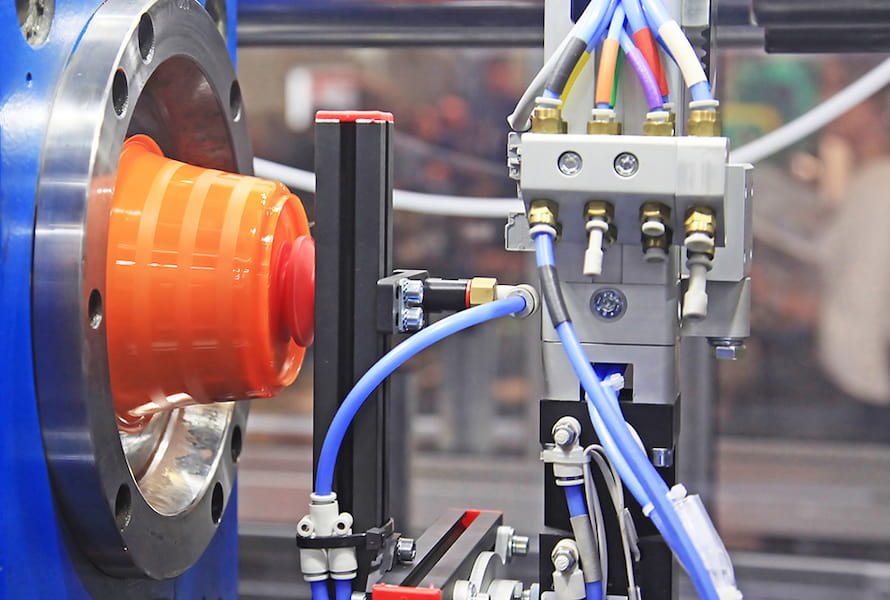
If defects go uncorrected, the entire color mixing process can become slower and more expensive, which could result in a bad aesthetic. As a result, in order to lower the possibility of probable injection molding color mixing problems, it is crucial to adopt a proactive approach to risk mitigation throughout the color mixing process. Here are some of the most frequent injection molding color mixing problems, along with advice for product teams on preventing them.
Read more: What is color masterbatch and how was masterbatch produced?
1. Injection molding color mixing problems from equipment
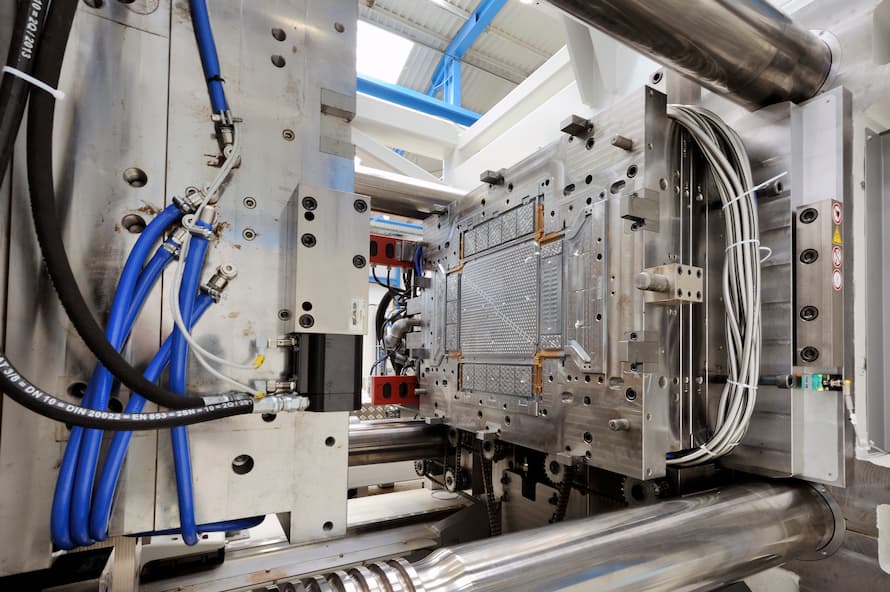
1.1. Screws/nonreturn valves
Depending on the letdown ratio, chromaticity, and base resin being used, a general-purpose screw will often function well with colorants. A rising number of injection molders are utilizing mixing screws to help with color dispersion even though it is often not essential. This kind of screw is often advantageous for processes that need difficult-to-color resins, and have high throughput, quick cycle durations, and big shot sizes.
The choice of non-return valves is often resin-specific, similar to screws. Ball check valves are more shear intensive and can help with color distribution, but this approach can be challenging when processing variables like screw speed, backpressure, and barrel temperatures are pushed to the base resin's limits, resulting in the degradation of both the colorant and the resin.
1.2. Screw and barrel wear
Regardless of the design, a worn screw or barrel will prevent mixing, resulting in a reduction in plasticizing quality and, therefore, in the distribution of color.
1.3. Barrel capacity
Using a GP screw with a barrel capacity of more than 60% is often regarded as stretching the processing limits for effective color integration. Of course, this depends on the cycle time. Another critical factor is the barrel's L/D ratio. In contrast, longer barrels (24:1) provide a longer mix environment but also a longer residency period. For instance, shorter barrels (18:1) are less suited to a good mix. It's critical to monitor material residence time since too much time in the barrel may produce distribution problems while too little time can cause problems with the base resin, colorant, or both.
1.4. Colorant handling and dispensing
Before the colorant and base resin reach the molding machine, they must be properly blended and distributed, which is one of the secrets to effective color processing. Production staff that utilizes blending equipment must be knowledgeable about correct operation, calibration, and maintenance. Any money saved by coloring the raw materials will be lost in wasted products if the equipment is not correctly tuned to the operation.
There are several various alternatives for solid colorants, including drum tumblers or auger mixers. Volumetric or gravimetric feeders are utilized to combine concentrates and powders at the machine. Because they feed colorants based on speed vs. time, volumetric feeders are less costly and may be less precise than gravimetric kinds. Each component of the mixture is weighed and combined using gravimetric feeders. Special volumetric pumps are often employed for liquid colorants to manage the color precisely and cleanly.
No matter how simple or difficult a molding project may be, all team members should be actively adhering to appropriate documentation methods. All along, processing parameters should be documented. This procedure not only enables molders to speed up the production of high-quality components while stabilizing their process, but it also establishes a baseline in case there are process drifts or other issues.
2. Injection molding color mixing problems from the tooling design
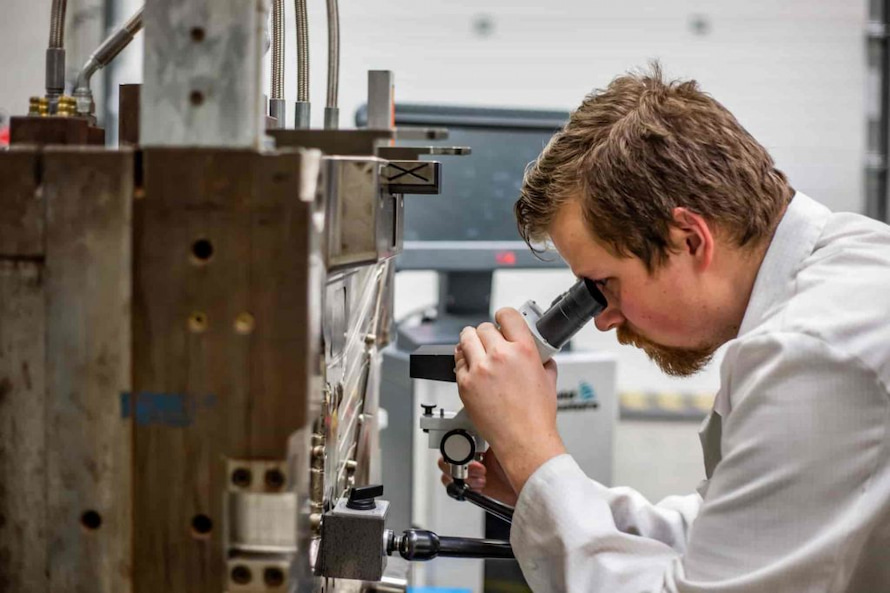
2.1. Gates and runner systems
At the design table, suitable gating and runner kinds should be taken into account. It's crucial to keep in mind that extra heat produced by a hot manifold or pin gate during injection fill might compromise the color's purity. A colorant provider may alter the formulation of the color package if it is known in advance that such tooling will be utilized.
2.2. Knit lines
It is crucial to consider color concerns early in the design process, particularly if knit lines are a problem. With certain resin families, color formulation adjustments may be made to make knit lines seem better when mold-filling data or experience suggest they are likely to occur. Naturally, this problem is simpler to overcome in the first phases of component and tooling design.
2.3. Mold texture
Mold texture is a crucial factor to take into account throughout the design process since it has an impact on how the eye perceives color. What might ordinarily be a perfect color match may seem quite different if the tool has gloss and/or texture. Given that certain materials inherently have greater glosses than others, gloss should be taken into account with respect to both the mold and the resin being treated.
3. Injection molding color mixing problems from the part design
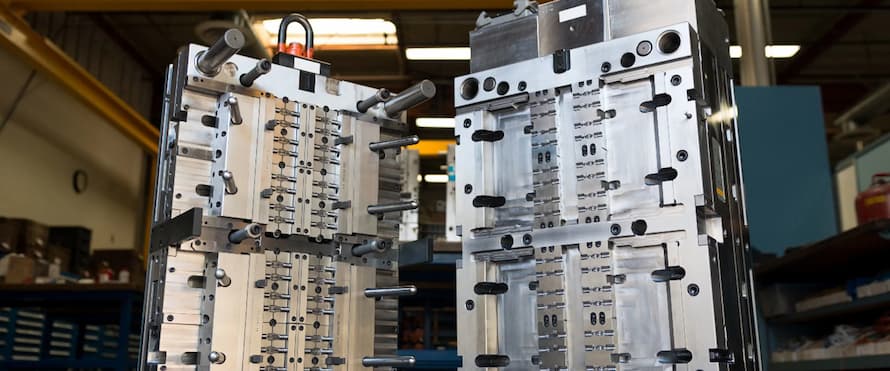
3.1. Color/special effects
Color package may highlight design or molding issues that are already present in a component, such as knit lines, small sinks, or stress-whitening markings close to the base of a snap-fit. This is both a blessing and a difficulty of molding color and/or special effects. In actuality, if the issue is a molding or design flaw, it is likely still there and simply less obvious after adding color back in and putting the item through the natural resin.
High-gloss designs and chromatic hues will highlight the issue. Small design changes may thus be able to address the issue if it is something that can otherwise be tolerated. On the other hand, certain issues, like stress-whitening markings, may often be covered up with the right color choices or even a formulation change.
When integrally colored, molded components of various materials are combined with other molded or painted components, their color, gloss, and texture must often match. To guarantee that the pieces will match as closely as possible when they are fresh and that they will fade at the same rate during the lifespan of the assembly, it is crucial to collaborate closely with the resin and color suppliers in this case.
3.2. Bosses/ribs/knit lines/parting lines
There is a high likelihood of sink marks, knit lines, and impaired mechanical integrity whenever there is a flow interruption in the part design, such as bosses, ribs, or even converging flow fronts on several gated components. This is because knit lines are always weaker than the surrounding resin. Many special-effects packages have aesthetic issues as a result of the shifting refractive index over this region of the component due to the shifting orientation of the material in these places. Therefore, these breaks should be included in the part's non-critical and invisible faces.
4. Injection molding color mixing problems from formulations and colorants
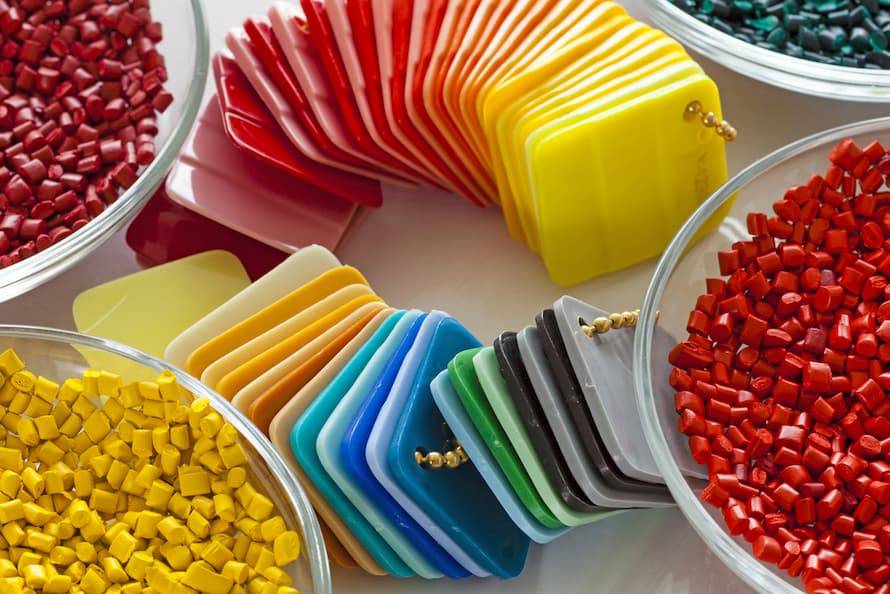
4.1. Resin and colorant compatibility
Early in the design process, the melt index connection between the base resin and color should be taken into account. Additionally, different colors have varying degrees of reaction with different resins.
For instance, in styrene polymers, certain organic pigments have the propensity to disintegrate and vanish (or change hue). Similar to nylon polymers, which are weak reducing agents that essentially destroy the chromophore component of the dye that supplies the color, many dyes often change color or vanish in them. Additionally, because of their very low solubility and possibility for color migration, dyes are not advised for use in olefins, except in certain circumstances. Additionally, certain colors may function as a plasticizer, lowering the thermal characteristics of the material or even interacting with the resin itself to generate other effects.
Phthalocyanine (phthalo) pigments can be troublesome since they may operate as nucleators and cause often unmanageable shrinkage and warpage issues in crystalline resins. Fluorescent dyes may potentially be problematic in certain settings. They react chemically with nylon, lack temperature stability for use in many technical resins, and lack UV stability for use in the majority of outdoor applications.
Alloys and polymer mixes are often associated with a final group of issues. Phase barriers between these materials' different constituents may result in light scattering and subsequent milkiness. Therefore, getting chromatic hues may be expensive since so much colorant has to be added to offset the milkiness - often at the expense of important physical or mechanical qualities and economic considerations.
4.2. Carrier specifications
The exact color carrier and its flow characteristics relative to the base resin are crucial to the color dispersion and must be taken into account during the original design. To ensure that the pigment or dye in the mix is distributed evenly, the carrier has to melt in the late-feed or early-transition areas of the screw. The colorant won't be evenly distributed in the melt and, ultimately, in the molded object if the carrier has a melting point that is either too high or too low.
4.3. Other additives
Some color-related issues may be solved with special colorant package additions. However, these chemicals are often not used until processing attempts have failed, mainly because they add costs that may reduce the cost-effectiveness of the finished product.
4.4. Grade can make a difference
It is essential to keep in mind that not all resin families or even grades within the same family are interchangeable with a particular color package. This is true even when comparing various pigment or dye packages that belong to the same chemical family. In addition, since the majority of colorant suppliers tailor the formulation of their packages to a certain resin grade produced by a given manufacturer, the color package must be retested in the event that the resin supplier is changed after the package has already been formed.
The natural color of polypropylene, which may vary from a yellow-white to a gray-white hue depending on the quality and amount of filler that is used, is an excellent illustration of this phenomenon. The natural color of polypropylene can exhibit a pretty large range of variation.
5. Prevent injection molding color mixing problems
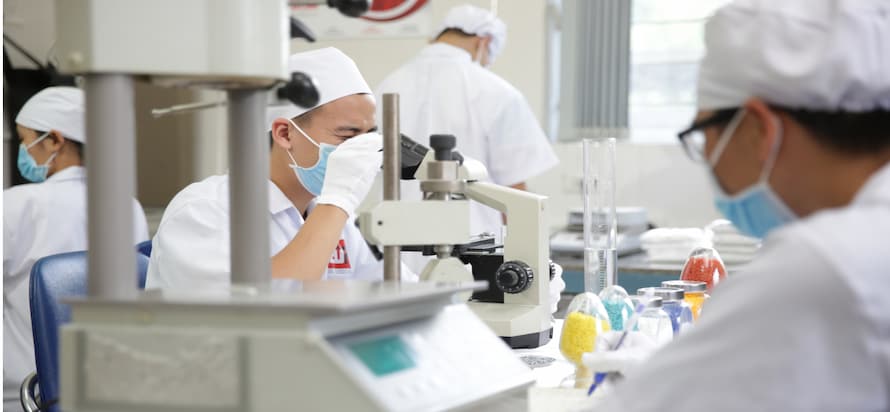
Plastic components may be produced via injection molding, which can be a very effective manufacturing technique. However, like with many other processes, generating high-quality end parts requires close attention to detail and a proactive approach to risk management. In order to guarantee that products meet the highest quality aesthetic standards and prevent these typical injection molding color mixing problems, everyone involved in the color mixing process, from the initial design and proof-of-concept stages all the way to fulfillment, needs to take the appropriate precautions.
Choosing a supply partner like Europlas, who is well-versed in common injection molding color mixing problems and their troubleshooting, can mean the difference between high-quality parts produced on time and within budget.
As the world's No. 1 filler masterbatch manufacturer, EuroPlas proudly brings customers unique plastic raw material solutions to help their factories optimize production costs and improve their competitiveness in the market. We are a skilled supply company, but we also provide design advice to make sure we can assist any team in producing beautiful, high-performance components as quickly as possible.
To learn more about our products, get in touch with us right now.