Is high-density polyethylene toxic? The question has mainly been raised because HDPE plastic is used in many food contacting products such as milk jugs or food storage containers.
The material is stronger, tougher, and can withstand higher temperatures compared to most other polymers. It's also applied in various industrial fields. However, some people may have doubts about its safety since they may not be familiar with HDPE or have bad experiences with other plastic usage. So, is HDPE toxic? Let's delve into the answer!
1. What Is HDPE Plastic?
High-density polyethylene is one among the 5 categories of the Polyethylene family, which is rated by their density. The higher the density, the stronger the material, meaning HDPE plastic is considered tough, strong, and durable.
The material is made from crude oil and has many outstanding properties. It has impressive yield strength and tensile strength and excellent chemical, temperature, and UV resistance. The plastic is stronger than standard polyethylene, acts as an effective barrier against moisture, and remains solid at room temperature. This type of polyethylene also resists insects and rot.
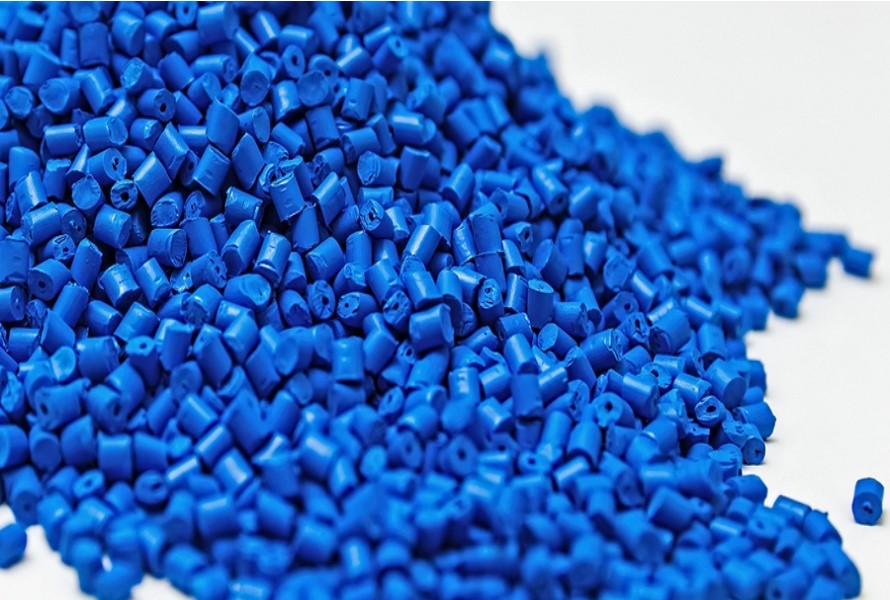
Thanks to its versatility, the material is widely used in manufacturing products, such as milk jugs, shampoo containers, and plastic chemical bottles. Besides its common application in the food industry, HDPE plastic is also present in construction materials, medical devices, toys, automotive parts, and clothing.
Read more: HDPE (High-density polyethylene) - What is it? Properties & common uses.
2. Is High-Density Polyethylene Toxic?
So, Is HDPE toxic? The answer is no. HDPE plastic is not dangerous since it creates no harmful emissions during its production or during its use by the consumer.
In general, the material is not poisonous in its final form, as HPDE is molded or manufactured into products that can be recycled after use. Not all but most of the HDPE plastic is FDA approved; thus, you can see it is often used for packing food. The material is considered safe and non-hazardous, and short-term and long-term inhalation does not negatively affect human health.
In addition, HDPE leaks no toxic chemicals into the air, soil, or water. Yet, manufacturers should pay attention to the manufacturing process. Without proper care, dust or resin of polyethylene can irritate the eyes when the vapor of the resin is heated. Safety gear is inevitable to avoid unintentional injury.
Is high-density polyethylene toxic? One more thing to keep in mind is that though the material is non-toxic, it's non-biodegradable. Therefore, recycling is a way to help create new, reusable, eco-friendly products and keep the landfills from overcrowding. One fun fact for your reference: Recycling plastic saves twice as much energy than incinerating it, and if you recycle 10 plastic bottles, you can save enough power to run a laptop for more than 1 day.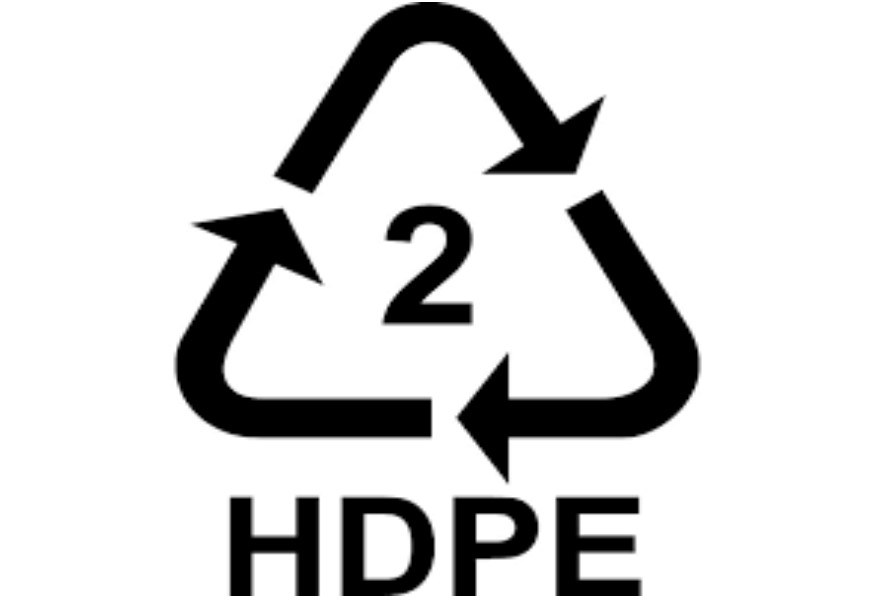
3. FAQs
3.1. What are the common applications of HDPE Plastic?
HDPE's toughness, durability, resistance to moisture, and chemical compatibility make it a suitable material for various applications, including package materials (such as bags, bottles, containers, etc.), construction and infrastructure, the automotive industry, and agriculture.
3.2. Is HDPE Food-safe?
Yes, it is. The material is FDA-approved, meaning it is safe for food and beverage contact. Thanks to its inert nature, plastic can prevent any unwanted interactions or contamination while being used for food packaging and storage.
3.3. What are the Key Outstanding Features of HDPE Plastic?
The material has many excellent properties such as toughness, flexibility, translucency, weatherproof, chemical resistance, low cost, and easy to process by many methods.
4. EuroPlas - The World Leading Filler Masterbatch Manufacturer
As the world's No. 1 filler masterbatch manufacturer, EuroPlas proudly brings customers unique plastic raw material solutions to help their factories optimize production costs and improve their competitiveness in the market. Thousands of factories in over 85 countries have chosen EuroPlas products, proving our worldwide reputation and quality. With over 16 years of experience, we are confident that our products and services can satisfy your final products and other requirements. As one of the leading experts in the plastic materials market, we take advantage of unique natural resources, produce cost-effective material solutions, and offer tailor-made solutions for each customer.
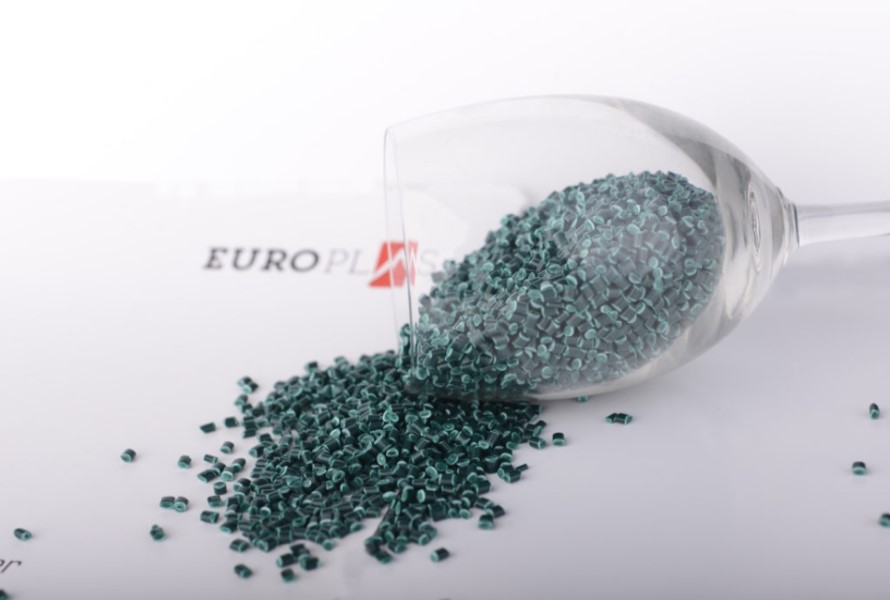
EuroPlas's remarkable products include:
4.1. Engineering plastic compound
Engineering plastic compound, consisting of primary resin, colorants, and reinforcements that help create finished products with desired technical properties, is a full-function-in-one-material solution for end-products. Our compound's base plastics include ABS, PC, PP, HIPS, etc. They all help improve end-products' mechanical properties: stiffness, impact resistance, etc., reduce shrinkage, and enhance thermal resistance ability.
4.2. Filler masterbatch
Filler masterbatch, a cost-effective material solution for plastic enterprises, is a combination of calcium carbonate (CaCO3), plastic resin beads, and plastic additives according to customer requirements. Thanks to CaCO3's great thermal transmission ability, our product helps save energy, thus shortening the production cycle. Besides, it improves several properties of end-products: stiffness, bend strength, and impact resistance, increases the stability in the manufacturing process, enhances printability, and saves production costs.
4.3. Color masterbatch
EuroPlas has a series of color masterbatches to meet the aesthetic requirements of the final products. Besides the ability to create exact colors as end-product requirements, our material has great dispersion, high color fastness, and good thermal resistance, and is environmentally friendly.
4.4. Plastic additives
EuroPlas supplies a list of plastic additives, including deodorizing/odor-removing additives, desiccant additives, flame retardant additives, anti-fog additives, anti-aging additives, processing aids, anti-static additives, Anti-UV additives, and additives to increase clarity and brightness. They help end products achieve the required mechanical, durability, longevity, and aesthetic properties, thus enhancing manufacturing efficiency.
4.5. Bioplastic compound
Our Bioplastic compound, under the name BiONext bioplastic, is a green material solution that enables end-products to be biodegradable within 12 months. They are made from renewable sources such as polylactic acid (PLA) and Polyhydroxyalkanoate (PHA), plants (corn, palm oil, potatoes), or fossil fuels such as aliphatic-aromatic co-polyester (PBAT). This biodegradable plastic compound with outstanding mechanical and aesthetic properties helps contribute to sustainable development and build a greener world.
4.6. Bio Filler
Bio Filler is a cost-effective material solution for bioplastic end-products. It can improve some properties of the finished product (increasing gloss, film hardness, etc.), save production costs, and enhance the competitiveness of finished products.