In today's world, plastics play a significant role in our daily lives, from packaging materials to industrial applications. Two commonly used types of plastic are Low-density polyethylene (LDPE) and High-density polyethylene (HDPE). Both have their unique characteristics and applications, making them vital materials in various industries. This article explores the differences between LDPE and HDPE to help you understand which one might be better suited for your specific needs.
1. About LDPE (Low-density polyethylene)
LDPE is a versatile and widely used thermoplastic made from the monomer ethylene. It has a lower density and is more flexible compared to HDPE. LDPE is commonly used for its excellent resistance to moisture and chemicals, making it ideal for applications such as plastic bags, shrink wraps, and squeeze bottles. Its flexibility allows it to be easily molded into various shapes, making it popular for manufacturing products that require elasticity.
Read more:
What is LDPE (Low-density polyethylene)? Properties & applications
2. About HDPE (High-density polyethylene)
On the other hand, HDPE is a high-density thermoplastic made from petroleum. It has a higher density and is more rigid and durable than LDPE. HDPE is known for its excellent strength-to-density ratio, making it suitable for applications requiring sturdy and robust materials. It is commonly used in pipes, containers, and plastic lumber due to its resistance to chemicals, impact, and weather conditions.
Read more: HDPE (High-density polyethylene) - What is it? Properties & common uses
3. What’s the difference between LDPE and HDPE?
3.1. Differences between LDPE and HDPE in physical characteristics
Low-density polyethylene (LDPE) and High-Density Polyethylene (HDPE) are two types of polyethylene plastics with distinct physical characteristics. Here are the main differences between LDPE and HDPE in terms of their physical properties:
Density
LDPE has a lower density, typically ranging from 0.910 to 0.940 g/cm³. This low density gives LDPE a high degree of flexibility and makes it lightweight. Meanwhile, HDPE has a higher density, ranging from 0.941 to 0.965 g/cm³. Its higher density gives HDPE greater strength and rigidity compared to LDPE.
Melting point
LDPE has a lower melting point, typically around 105 to 115°C (221 to 239°F). This lower melting point allows LDPE to be easily processed and molded. HDPE has a higher melting point, typically around 120 to 160°C (248 to 320°F). Its higher melting point makes HDPE more resistant to heat deformation and suitable for applications involving higher temperatures.
Flexibility

Flexibility and duration of LDPE and HDPE
LDPE is highly flexible, even at low temperatures. It can be bent, stretched, and folded easily without breaking, making it ideal for applications requiring flexibility. HDPE is less flexible than LDPE. While it is still somewhat flexible, it is not as pliable as LDPE. HDPE maintains its shape and rigidity under stress.
Transparency
LDPE is not entirely transparent but has a slightly cloudy appearance, and allows some light to pass through. HDPE is opaque and does not allow light to pass through. It is solid and does not transmit light, providing better UV resistance.
Tensile strength
Tensile strength is a mechanical property of a material that measures the ability of a material to withstand tensile forces without breaking or stretching excessively. LDPE has a lower tensile strength compared to HDPE. It is not as strong under tension, making it more suitable for applications where flexibility is crucial. HDPE has a higher tensile strength, making it stronger and more resistant to stretching and tearing. It is ideal for applications where durability and strength are essential.
Impact resistance
LDPE has excellent impact resistance, meaning it can withstand sudden shocks or impacts without breaking or cracking. This property makes it suitable for packaging applications. HDPE also has good impact resistance and is generally stronger, and less prone to deformation than LDPE when subjected to impacts.
3.2. Differences between LDPE and HDPE in chemical resistance
LDPE has good resistance to acids and bases but is less resistant to solvents and organic chemicals. It is susceptible to swelling and softening when exposed to certain solvents, oils, and fuels.
HDPE exhibits excellent resistance to a wide range of chemicals, including acids, bases, and various organic solvents. It is highly resistant to most acids, alcohols, and alkalis. In addition, HDPE is also resistant to oil and grease, so it is suitable for products that come into contact with these substances.
3.3. Differences between LDPE and HDPE in recyclability
Recycling codes
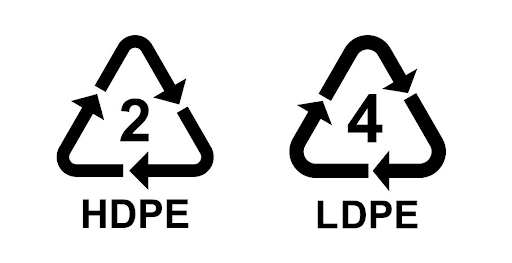
Recycling codes of LDPE and HDPE
LDPE is assigned the recycling code "4." Products made from LDPE, such as plastic bags and some packaging materials, are labeled with this code. LDPE is commonly recycled into new plastic bags, composite lumber, and plastic film products.
HDPE is assigned the recycling code "2." Products made from HDPE, including bottles, containers, and pipes, are labeled with this code. HDPE is widely recycled into various products, such as bottles, detergent containers, plastic lumber, and drainage pipes.
Recycling process
LDPE recycling involves processes like collection, sorting, cleaning, and reprocessing. However, LDPE has a lower recycling rate compared to HDPE due to its lower density, which makes it less economically viable to recycle. Recycling LDPE often requires more energy and effort.
HDPE has a higher recycling rate due to its high density and ease of processing. It is commonly recycled through a process that includes collection, cleaning, shredding, melting, and reforming into new products. HDPE recycling is more cost-effective and energy-efficient compared to LDPE recycling.
Environmental impact
Although LDPE can be recycled, recycling rates are lower and require greater energy resources, so in general, recycling LDPE is less environmentally friendly than HDPE. Recycling HDPE has the potential to be more sustainable as it is easier to process and requires less energy. The recycling of HDPE plastic contributes to reducing plastic waste and conserving the earth's resources.
3.4. Differences between LDPE and HDPE in production methods
Polymerization process
Polymerization is the process of combining many same or similar small molecules (monomers) into very large molecules (polymers). LDPE is produced through a process called free-radical polymerization. In this method, ethylene gas (a hydrocarbon) is converted into single polymer macromolecules. This process takes place under the influence of an initiator, usually a peroxide compound. This compound helps generate free radicals during the polymerization process, stimulating the combination of ethylene molecules. High pressure and temperature cause the ethylene molecules to form a branched, low-density polymer structure, eventually yielding LDPE.
High-density polyethylene (HDPE) is synthesized through two main methods: Ziegler-Natta polymerization and coordination polymerization.
- Ziegler-Natta polymerization: This method uses a specific catalyst called Ziegler-Natta, usually made from metal compounds such as titanium and aluminum. This catalyst facilitates the generation of free radicals during the polymerization process, helping ethylene molecules link into long polymer chains, forming HDPE.
- Coordination polymerization: This is a form of polymerization that uses catalysts such as salts or transition metals. In this process, ion transfer catalysts (also known as coordination catalysts) create complex interactions with monomers, promoting the polymerization process, and forming HDPE.
Molecular structure
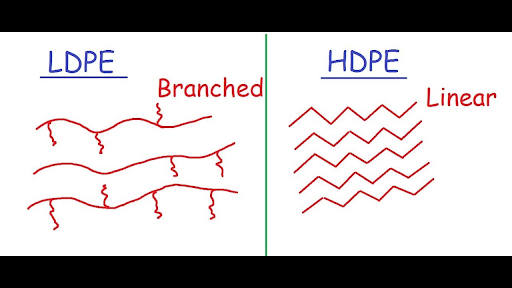
Molecular structure of LDPE and HDPE
LDPE has a highly branched and low-density molecular structure. The branching occurs due to the reaction conditions during the polymerization process, leading to numerous side branches and a less orderly arrangement of polymer chains.
HDPE has a more linear and densely packed molecular structure with fewer side branches. The absence of branching allows HDPE molecules to pack closely together, creating a higher density and increased crystallinity.
Processing conditions
LDPE is processed at lower temperatures and pressures due to its low density and highly branched structure. It has a lower melting point, making it easier to mold and shape.
HDPE is processed at higher temperatures and pressures because of its higher density and more crystalline structure. It has a higher melting point, which contributes to its ability to withstand processing temperatures and provides better mechanical strength.
End-use applications
LDPE is often used for applications requiring flexibility, such as plastic bags, films, and coatings. Its highly branched structure gives it excellent flexibility and impact resistance.
HDPE is used in applications requiring strength, rigidity, and chemical resistance, such as bottles, pipes, and containers. Its linear structure 9the molecules or units in a material are arranged in a simple, straight shape, without branches or curves) provides superior tensile strength and durability.
4. LDPE vs HDPE, which one is better? Choosing the right material
The question of whether Low-Density Polyethylene (LDPE) or High-Density Polyethylene (HDPE) is better depends entirely on the specific requirements of your project. Each material has its own unique set of properties and applications.
Choose LDPE if you need a flexible, moisture-resistant material for products like plastic bags, wraps, or squeeze bottles. LDPE is also an excellent choice for applications where elasticity is essential.
Choose HDPE if you require a sturdy, durable material with excellent chemical resistance. HDPE is suitable for applications such as pipes, containers, and industrial equipment that demand strength, and the ability to operate stably and with few errors for a long time.
5. Conclusion
In the LDPE vs HDPE debate, there is no one-size-fits-all answer. The choice between these two plastics depends on the unique needs of your project. Consider the properties of each material carefully and evaluate your requirements before making a decision. Whether you prioritize flexibility or durability, LDPE and HDPE both offer exceptional qualities that can cater to a wide range of applications. By understanding the differences between these plastics, you can make an informed choice and ensure the success of your project.
6. Plastic products at EuroPlas
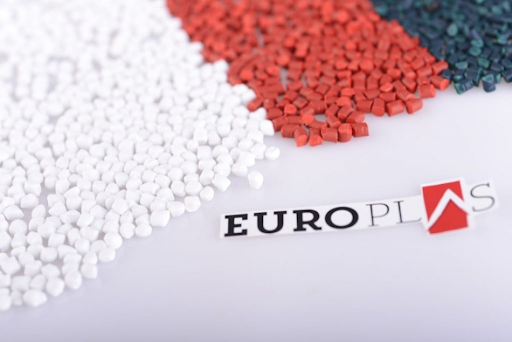
EuroPlas with outstanding advantages in plastic products for your company
If you are looking for a supplier of specialized plastics to help plastic businesses save costs and increase competitive advantage, EuroPlas is a suitable choice. Currently, EuroPlas provides 6 popular plastic products with outstanding advantages such as:
- Bioplastic compound: This is considered a green solution and a premise for sustainable development with the special feature of being able to differentiate cancellation within 12 months. EuroPlas' BiONext bioplastic possesses outstanding mechanical properties such as high hardness, excellent impact resistance, and good stretchability, not only that but also has a glossy, beautiful surface and is easy to process. This material is suitable to meet both functional and aesthetic requirements for the finished product.
- Color masterbatch: The outstanding advantage of EuroPlas color masterbatch is the ability to disperse evenly on the product surface, ensuring stable color and high heat resistance. Currently, we offer a variety of colored beads including white, black, red, gray, purple, blue, brown, orange, and yellow. In addition, there are specialized types of colored plastic resins, suitable for your specific needs.
- Plastic additives: EuroPlas specializes in providing a variety of plastic additives, including deodorizing additives, desiccant additives, flame retardant additives, anti-fog additives, anti-aging additives, and processing aid additives, antistatic additives, anti-ultraviolet rays additives, and clarity and brightness enhancing additives.
- Engineering plastic compound: EuroPlas provides the optimal solution with compound engineering plastic products that are flexible and high quality, meeting many functions. Some products include PBT GF-FR compound, blend PA6, PA66, PC fireproof compound, ABS fiberglass compound, and ABS antistatic compound...
- Filler masterbatch: Currently, EuroPlas is the world's largest supplier of filler masterbatch. With more than 16 years of experience in manufacturing and exporting filler masterbatch, we have conquered the markets of Asia, the Middle East, Africa, and Europe... with a wide range of filler masterbatches to help reduce costs and increase performance. plastic production and quality.
- Bio filler: BiOMates is the perfect choice for the production of environmentally friendly products. This is a solution to help your business save costs during the processing of bioplastic products.